Introduction
In the construction industry, managing costs effectively is not just a goal; it's a necessity. With projects ranging from small-scale home builds to large commercial developments, the ability to control and reduce construction costs can significantly impact the bottom line. This importance is magnified when you consider the various factors involved in a construction project – from the initial planning and design phase to the final touches of a completed structure.
Construction costs encompass a wide range of expenses, including but not limited to, the cost of materials, labour costs, and other overheads. For construction business owners, general contractors, and home builders, understanding how to navigate these costs without compromising on quality standards or project scope is essential. In this article, we delve into ten proven strategies that can help in reducing these costs. These strategies are not just theoretical but are practical, tried and tested methods that have yielded results in real-time scenarios.
Throughout this article, we will explore different ways to minimise unnecessary expenses, lower costs, and maximise profit margins without sacrificing the integrity and quality of the construction project. From leveraging modern technology to optimising the use of building materials, each strategy offers a unique approach to cost management. Whether you're building your own house, managing a construction site, or overseeing a large-scale construction firm, these tips will provide valuable insights into achieving cost savings in the long run.
As we dive into these strategies, remember that reducing construction costs is not about cutting corners. It's about smart planning, efficient execution, and open communication among all team members involved. So, let's embark on this journey to discover the most effective ways to keep your construction project costs within budget while maintaining high-quality standards.
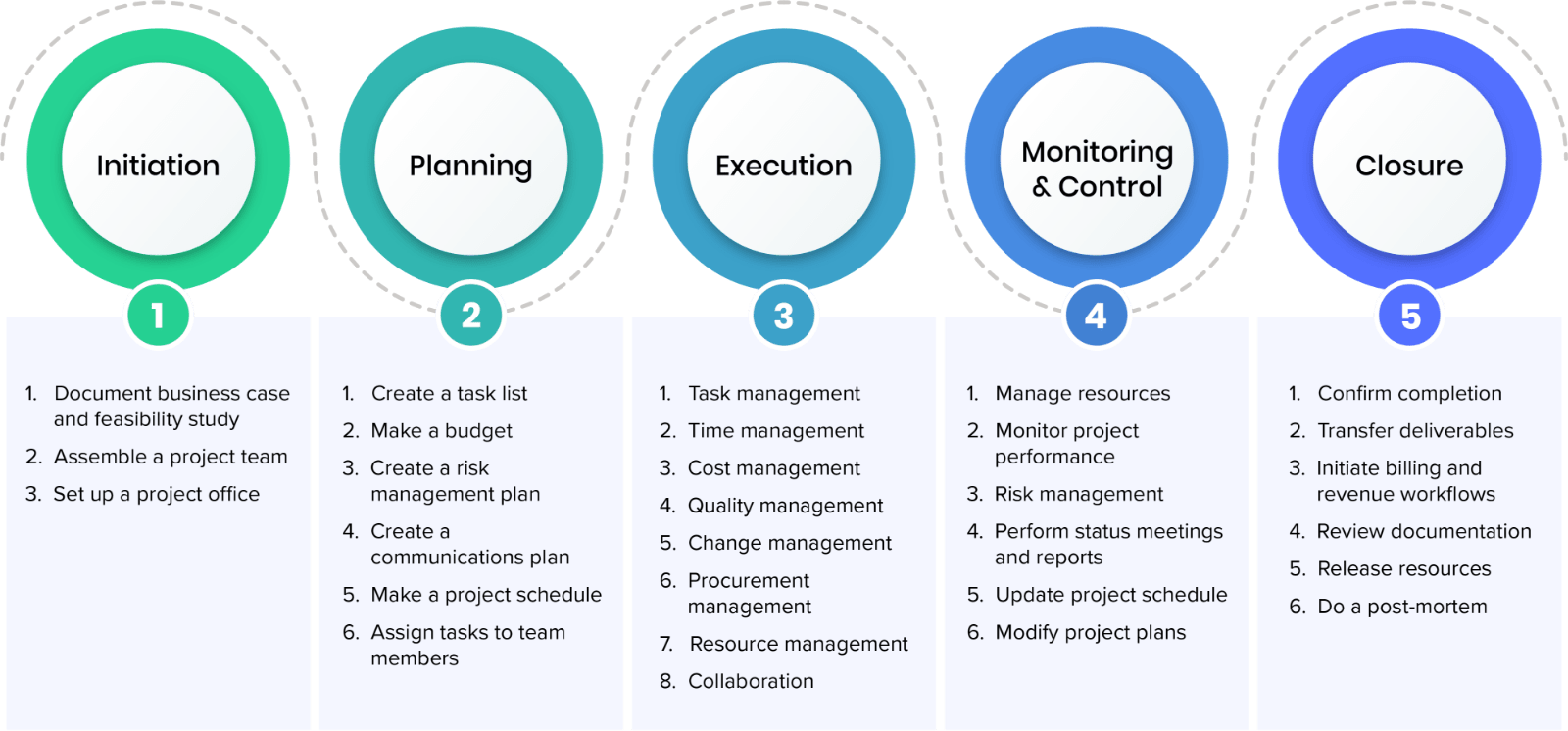
Effective Planning and Design Phase
The foundation of any successful construction project lies in its planning and design phase. This stage is crucial not just for setting the project's vision but also for outlining a roadmap that can significantly influence the total cost. Effective planning involves a deep understanding of the project scope, ensuring that every aspect of the construction process is thoughtfully considered and accounted for.
In-depth Planning: At the heart of cost-effective construction is thorough research and planning. Before breaking ground, it's imperative to have a comprehensive plan that addresses every detail of the project. This includes understanding the building process, from site work to the finishing touches. A well-defined plan helps in avoiding costly mistakes that often result from last-minute changes or oversights.
Design Efficiency: The design stage plays a pivotal role in determining the efficiency and cost-effectiveness of the entire project. Here, architects and designers must work closely with construction companies to create a design that not only meets aesthetic and functional requirements but also considers the cost implications. For instance, opting for a smaller house or a design with less square footage can lead to significant cost savings in materials and labour.
Cost-Efficient Choices: During the design process, it’s beneficial to explore different materials and design alternatives. Choosing the right materials can have a substantial impact on the cost of construction materials. It’s about finding the balance between quality and affordability. For example, using pre-fabricated components or sustainable materials like solar panels can offer long-term cost savings.
Prevent Overruns with Accurate Estimates: An accurate estimate in the design phase is the first step in preventing cost overruns. This involves a detailed analysis of every element of the construction, including labour costs, material prices, and other expenditures. Utilising project management software can aid in providing real-time data and accurate cost estimates, ensuring that the project stays within budget.
In conclusion, the design phase is not just about drawing up plans; it’s about laying the groundwork for a cost-efficient construction project. By focusing on detailed planning, efficient design, and smart material choices, significant cost savings can be achieved even before the construction begins.
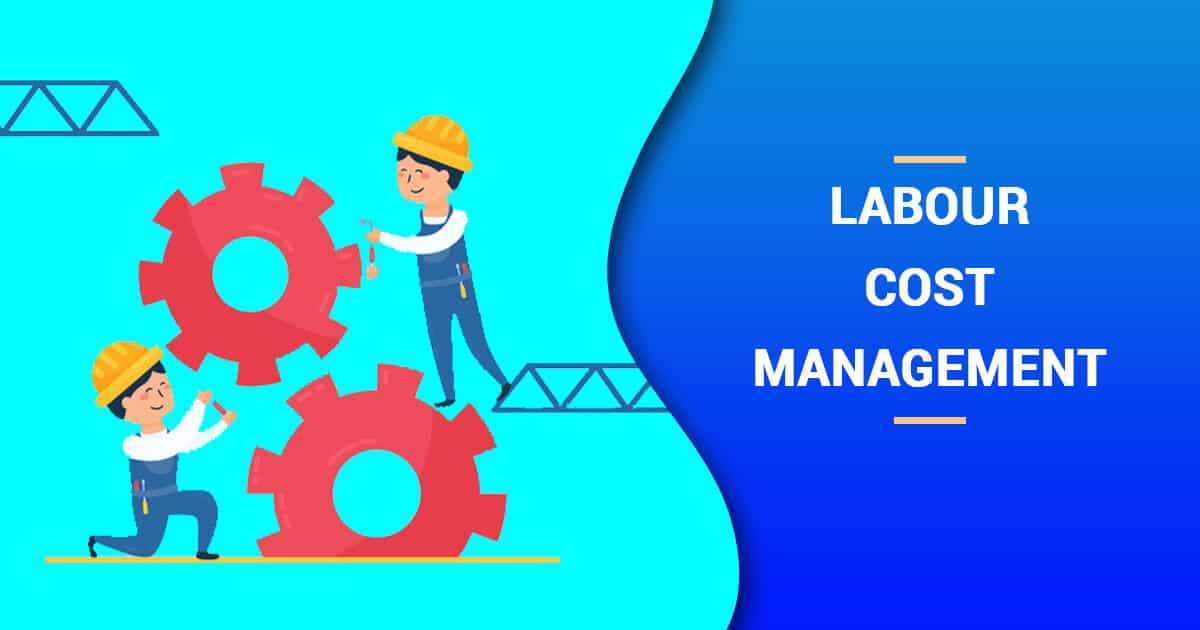
Streamlining Labour Costs
Labor costs often constitute a significant portion of the total cost in the construction industry. However, there are several strategies that can be employed to streamline these costs, ensuring efficiency without compromising on quality standards.
Efficient Workforce Management: One of the first things to consider is the efficient management of team members. This involves ensuring that the right number of skilled workers is employed for each stage of the building process. Overstaffing can lead to unnecessary expenses, while understaffing might cause delays and lower quality of work. Implementing a well-organised scheduling system can help in achieving the right balance.
Training and Skill Development: Investing in the training and development of workers can lead to more efficient and faster completion of tasks. Skilled labourers are less likely to make costly mistakes and can contribute to a smoother construction process. This not only helps in reducing labour costs in the long run but also enhances the overall quality of the construction project.
Use of Technology: Modern technology, such as project management software, can significantly aid in labour cost management. Software tools can offer real-time data on labour performance and help in tracking productivity. This allows project managers to make informed decisions about labour allocation and utilisation, leading to more efficient use of resources.
Incentivising Productivity: Implementing incentive programs for workers can boost productivity and reduce labour costs. Rewarding teams for completing projects on or ahead of schedule can encourage efficient work practices. This approach not only helps in lowering costs but also promotes a positive and motivated work environment.
In summary, effectively managing labour costs involves a combination of strategic planning, workforce optimisation, and the integration of technology. By focusing on these areas, construction companies and general contractors can ensure that labour expenses are kept in check while maintaining high standards of workmanship.
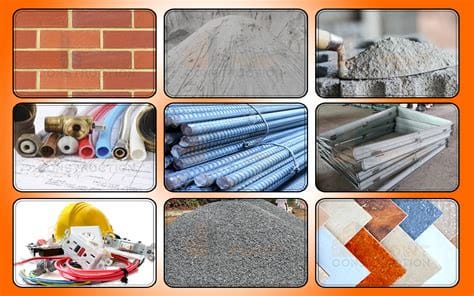
Optimising the Use of Building Materials
A critical aspect of reducing construction costs lies in the strategic selection and utilisation of building materials. Making informed decisions in this area can lead to substantial cost savings without compromising the project's integrity.
Finding the Best Deals: One of the easiest ways to reduce the cost of materials is by securing the best deals. This requires construction business owners and project managers to conduct thorough research on different suppliers. Comparing prices, negotiating with suppliers, and buying in bulk are great ways to lower prices. However, it's crucial to ensure that lower costs do not lead to a compromise in quality.
Material Alternatives: Exploring different materials can offer both cost savings and innovation in construction methods. For example, using sustainable materials or cheaper alternatives for certain components without affecting the overall quality can be a cost-effective approach. Construction companies should always be on the lookout for new, cost-efficient materials entering the market.
Efficient Use of Materials: Minimising waste is another efficient way to manage construction material costs. Proper planning and accurate measurements can reduce the amount of extra materials ordered and wasted. Additionally, reusing or recycling materials from the construction site can also contribute to cost savings.
Collaboration in the Design Process: Involving suppliers and contractors in the design process can provide insights into more cost-effective construction methods and material choices. Open communication between all parties can lead to innovative solutions that align with the budget without compromising the design intent.
In essence, the strategic selection and efficient utilisation of building materials are pivotal in reducing house construction costs. By focusing on getting the best deals, exploring material alternatives, reducing waste, and collaborating during the design stage, significant cost savings can be achieved in the construction process.
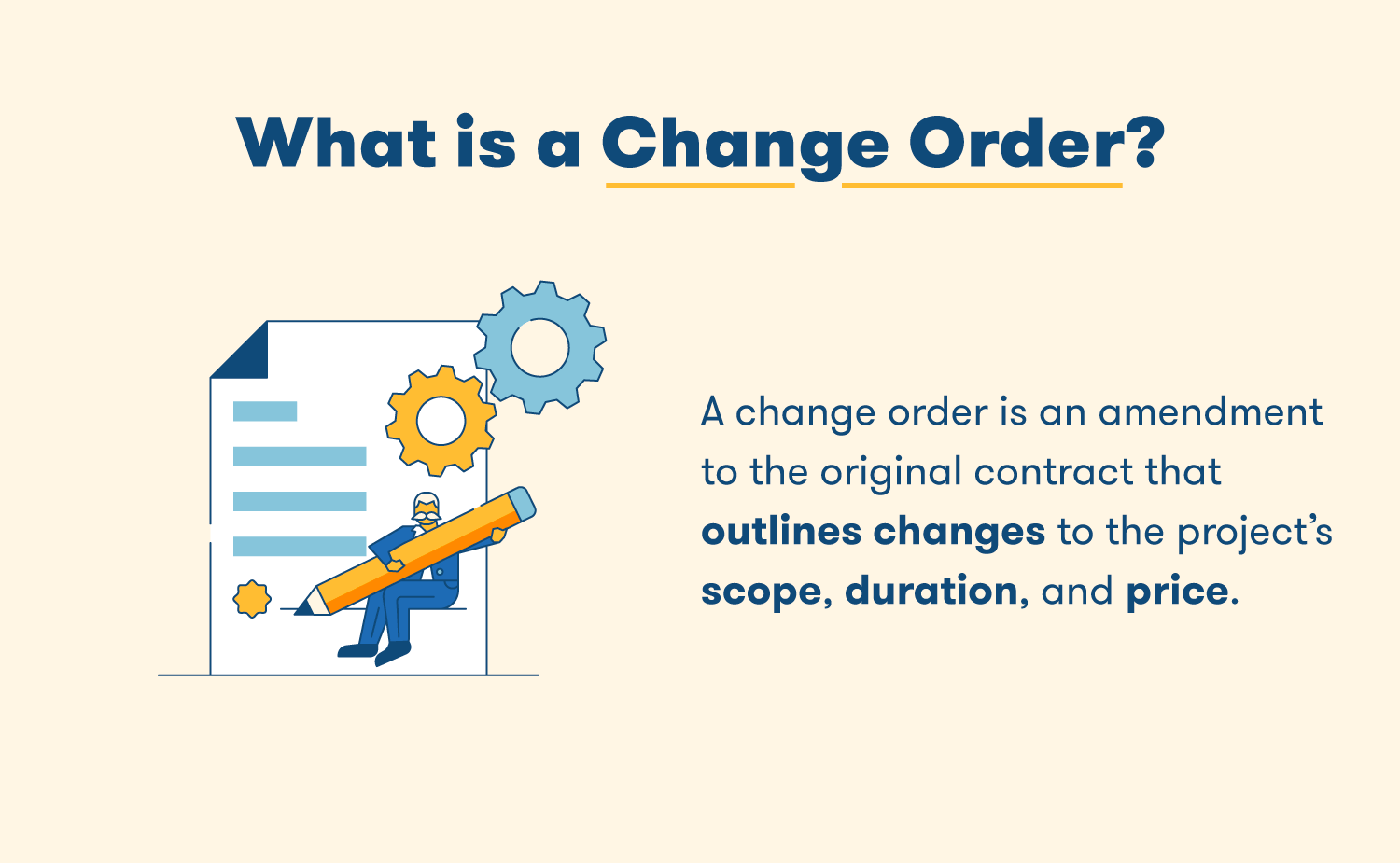
Minimising Change Orders (Variations)
Change orders in the construction process can significantly escalate total costs and lead to budget overruns. Minimising these change orders is crucial for maintaining control over the construction budget.
Detailed Initial Planning: The first step in minimising change orders is through detailed and thorough initial planning. This includes a comprehensive understanding of the project scope and clear communication of expectations. The more detailed the planning phase, the less likely it is that unforeseen changes will be required later on.
Establishing Clear Communication: Effective communication between all parties involved – including architects, contractors, and clients – is essential. This ensures that everyone is on the same page regarding the project's goals and requirements. Open communication can help in quickly identifying and addressing issues before they necessitate a change order.
Flexible yet Firm Design Stage: While flexibility is important, it's equally crucial to be firm in the design stage decisions. Frequent design changes can lead to multiple change orders, adding to the additional costs. Establishing a solid design plan and sticking to it as closely as possible can significantly reduce the need for changes during the construction phase.
Real-Time Monitoring and Management: Utilising project management software to monitor the construction process in real time can help in identifying potential issues that might lead to change orders. This proactive approach allows for adjustments to be made before they escalate into costly changes.
Educating Clients about the Impacts: Clients should be made aware of the cost implications of change orders. Educating them about how changes can affect the overall budget and timeline can encourage them to make more considered decisions.
In summary, minimising change orders is a key factor in controlling construction project costs. Through detailed planning, clear communication, a firm yet adaptable design approach, real-time monitoring, and client education, the number and impact of change orders can be significantly reduced.
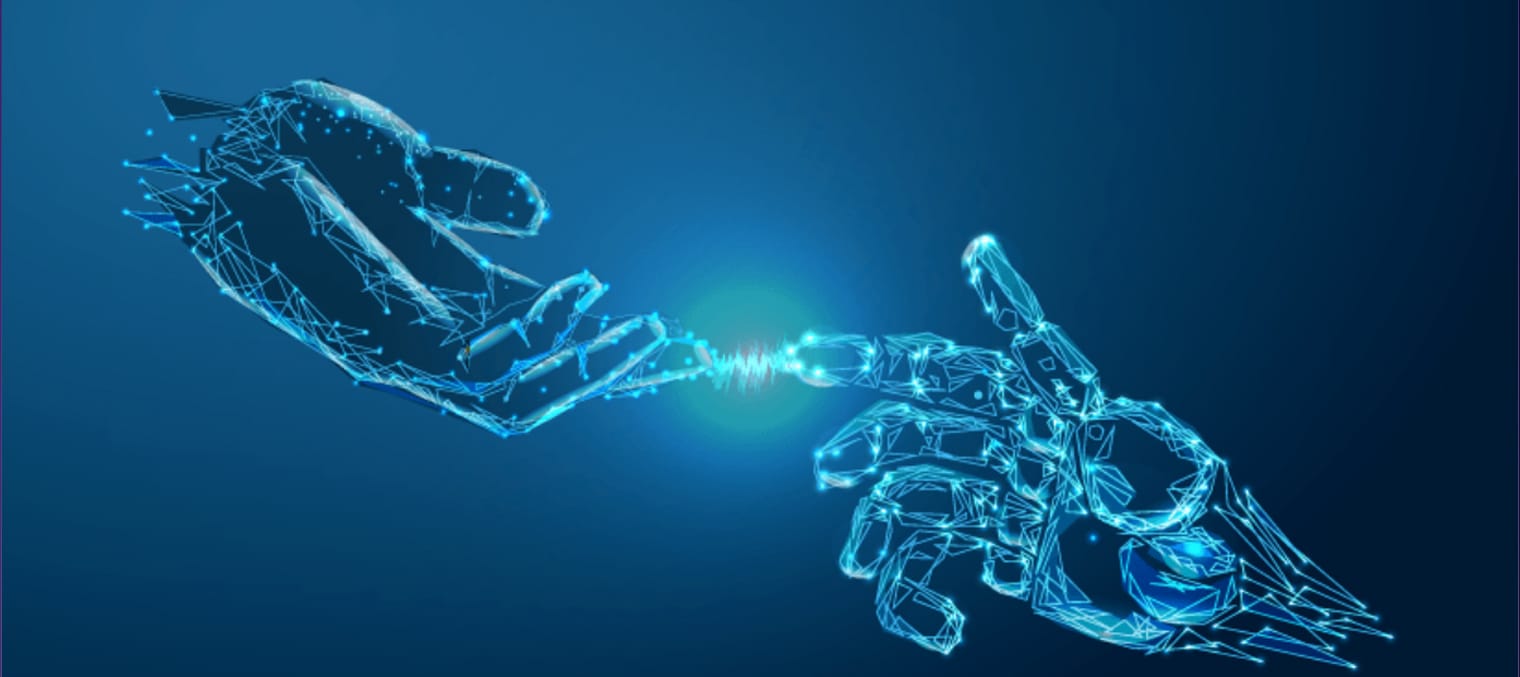
Leveraging Modern Technology
In today's construction industry, embracing modern technology is one of the most effective ways to reduce costs. Technology can streamline various aspects of the construction process, making it more efficient and cost-effective.
Project Management Software: One of the first things to consider is the adoption of project management software. This type of software allows for real-time tracking of the construction process, ensuring that everything stays on schedule and within budget. It can provide accurate estimates, track labour costs, and even monitor material usage, all of which are crucial for cost control.
Building Information Modeling (BIM): BIM is a transformative tool in the construction industry. It allows for the creation of digital representations of physical and functional characteristics of a project. BIM aids in making more informed decisions during the construction process, reducing the likelihood of costly errors and reworks.
Use of Drones and AI: Drones can be used for site surveys and inspections, significantly reducing the time and labour costs associated with these tasks. Similarly, artificial intelligence (AI) can analyze data to predict project delays or budget overruns, allowing for proactive measures to mitigate these risks.
Automation and Prefabrication: Automating certain construction tasks can lead to significant labour cost savings. Prefabrication of components off-site can also reduce waste and increase efficiency, leading to lower overall construction costs.
Incorporating modern technology not only aids in reducing immediate costs but also ensures a more streamlined, efficient, and ultimately more profitable construction process. This adoption of technology is a clear indicator of the construction industry's evolution, one that savvy construction businesses and home builders are quickly embracing.
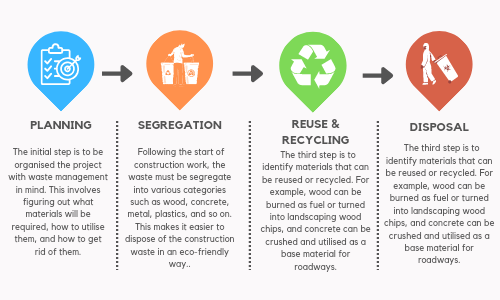
Effective Waste Management
Effective management of construction waste is not only an environmental concern but also a significant factor in reducing overall construction costs. Implementing strategies for minimising waste can lead to direct cost savings.
Planning for Waste Reduction: The planning phase should include strategies for waste reduction. This involves accurate material estimation to avoid over ordering and efficient material usage to minimise offcuts and leftovers. A well-thought-out plan can significantly reduce the amount of construction waste generated.
Recycling and Reusing Materials: Whenever possible, recycling and reusing materials on the construction site can lead to substantial cost savings. This approach not only reduces the need for new materials but also cuts down on waste disposal costs. For example, using leftover materials for other parts of the project or recycling materials like metal and concrete can be both cost-effective and environmentally friendly.
Proper Waste Segregation: Segregating waste on the construction site can enhance the efficiency of recycling and reusing materials. This involves setting up different disposal bins for various types of waste, making it easier to manage and recycle them effectively.
Collaboration with Waste Management Services: Partnering with specialised waste management services can be a cost-effective solution. These services often have the expertise and resources to handle construction waste efficiently, ensuring that it is disposed of or recycled in the most economical way possible.
Effective waste management in the construction process is not just about reducing environmental impact; it’s also a practical approach to reducing costs. By focusing on waste reduction, recycling, proper segregation, and collaboration with waste management services, construction companies can achieve significant cost savings.
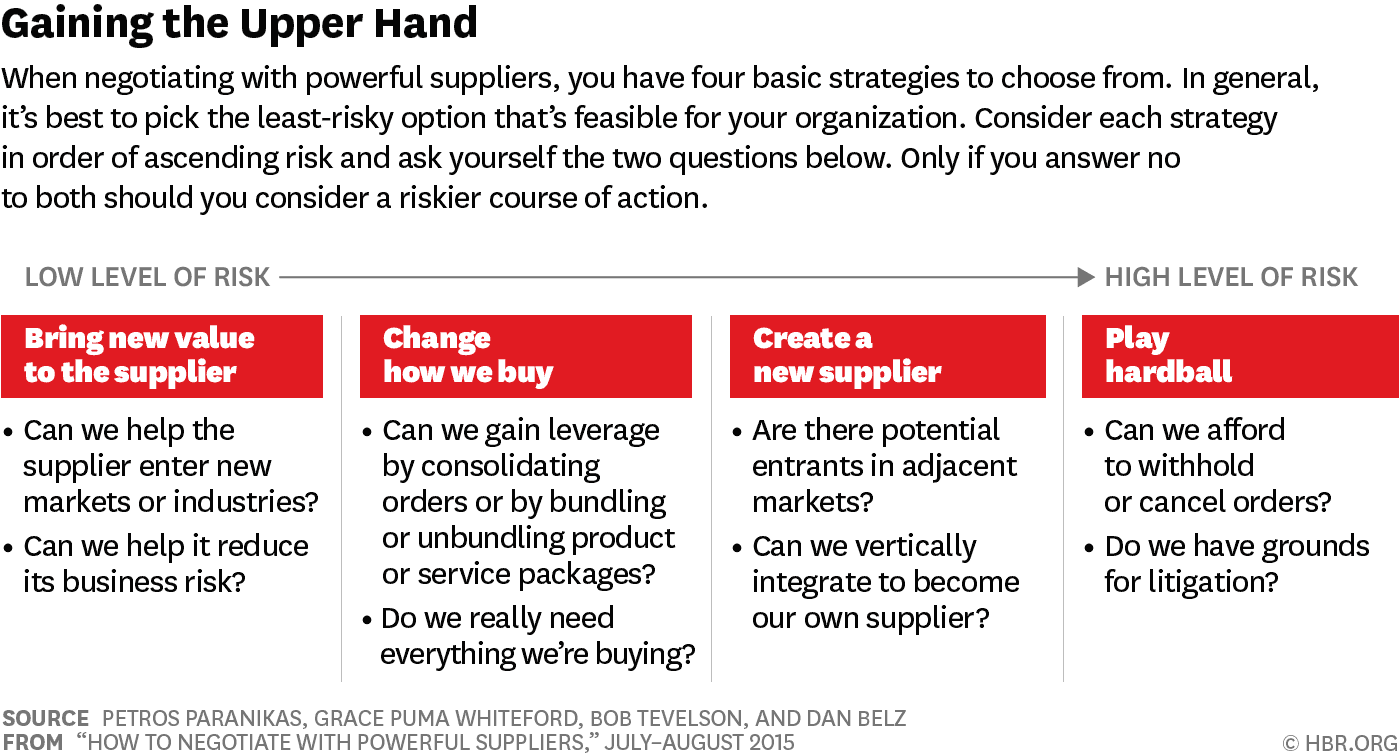
Negotiating with Suppliers and Contractors
Effective negotiation with suppliers and contractors is key to obtaining the best prices and terms, which can have a significant impact on reducing construction costs.
Research and Comparison: Before entering into negotiations, it's important to do thorough research and compare different suppliers and contractors. This not only gives you a better understanding of the market rates but also provides leverage during negotiations.
Volume Discounts: One of the easiest ways to lower costs is by negotiating volume discounts. Buying in bulk or committing to long-term contracts with suppliers can lead to lower prices for materials. This approach is particularly effective for small-volume builders and general contractors who can combine their buying power.
Long-term Relationships: Building long-term relationships with suppliers and contractors can lead to better deals and discounts. Suppliers are more likely to offer favorable terms and prices to loyal customers. Additionally, long-term partnerships can ensure more reliable and consistent service.
Negotiating Payment Terms: Apart from negotiating the price, payment terms can also be a significant area for negotiation. Longer payment terms or staggered payments can improve cash flow for the construction project, which can be beneficial, especially for larger projects.
Open Communication: Clear and open communication is crucial during negotiations. Understanding the needs and constraints of both parties can lead to mutually beneficial agreements. It's not just about getting the lowest price, but about finding value that benefits both sides.
By effectively negotiating with suppliers and contractors, construction companies and builders can secure the best deals, reducing the overall cost of materials and services. This requires not just good negotiation skills but also a strategic approach to building and maintaining relationships in the industry.
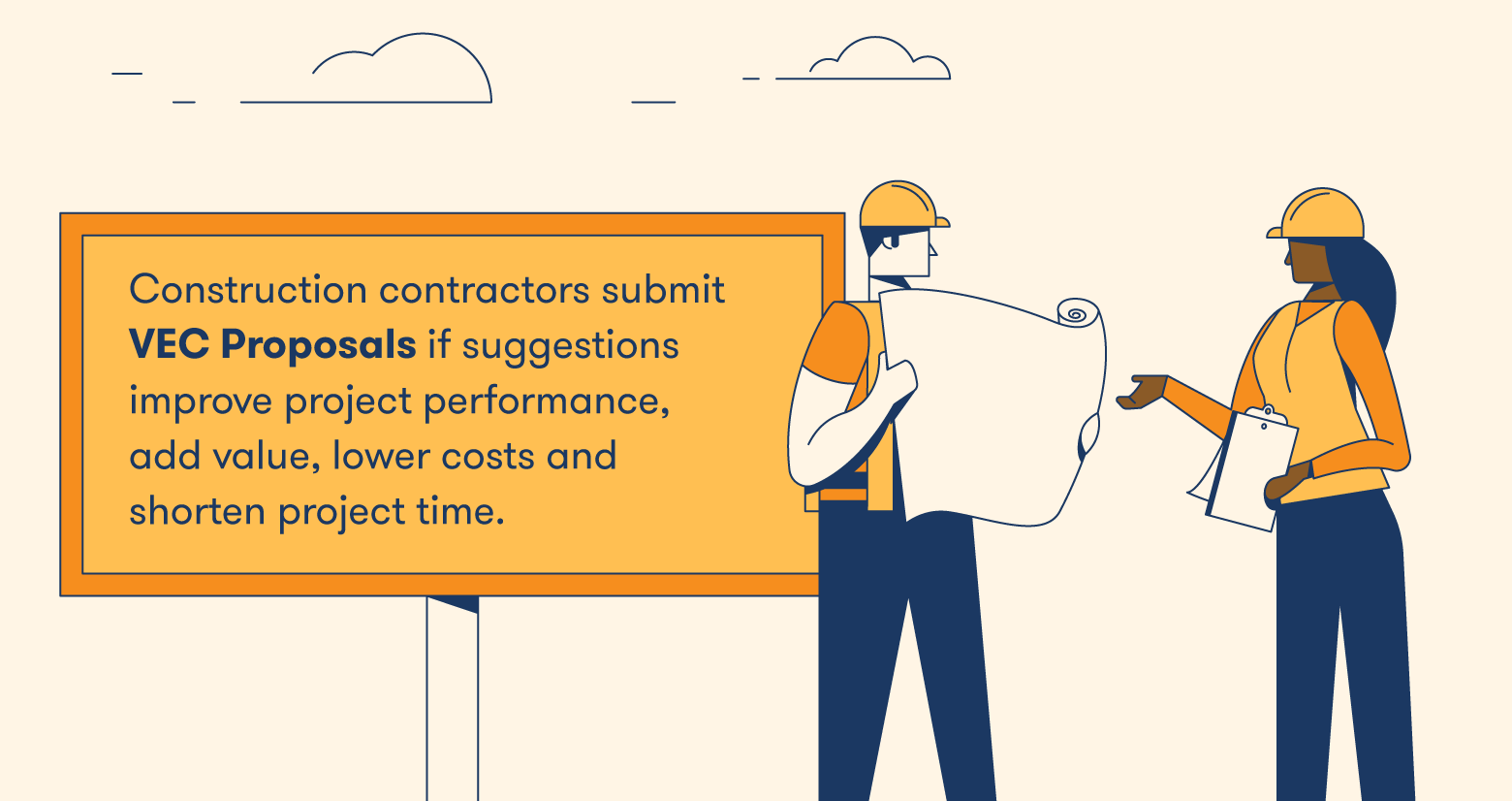
Utilising Value Engineering
Value engineering is a systematic and organised approach to providing the necessary functions of a project at the lowest cost. It plays a crucial role in cost reduction in the construction industry.
Functionality and Cost Efficiency: The core principle of value engineering is to maximise the functionality of a project while minimising costs. This involves re-evaluating the building materials, design methods, and construction techniques to find alternatives that offer the same functionality and quality at a lower cost.
Collaborative Approach: Value engineering is most effective when it’s a collaborative effort involving architects, engineers, contractors, and clients. This collaboration allows for a pooling of expertise and ideas, leading to innovative solutions that can reduce costs without compromising the integrity of the project.
Analysing Life Cycle Costs: Value engineering goes beyond just the initial construction costs. It also takes into account the life cycle costs of a project, including maintenance, operation, and even demolition. By considering these long-term costs, more sustainable and cost-effective choices can be made.
Focus on Key Areas: In value engineering, the focus is often on the areas of the project that consume the largest part of the budget. For instance, structural elements, HVAC systems, and exterior walls can be targeted for cost reductions.
Value Engineering Workshops: Hosting value engineering workshops at the design stage can be a significant way to identify cost-saving opportunities. These workshops are a platform for all stakeholders to suggest ways to improve value and reduce costs.
Implementing value engineering in the construction process can lead to significant cost savings and efficiency improvements. It’s a strategy that doesn’t just look at cutting costs but focuses on enhancing value, ensuring that the project meets or exceeds its intended function at the lowest possible cost.
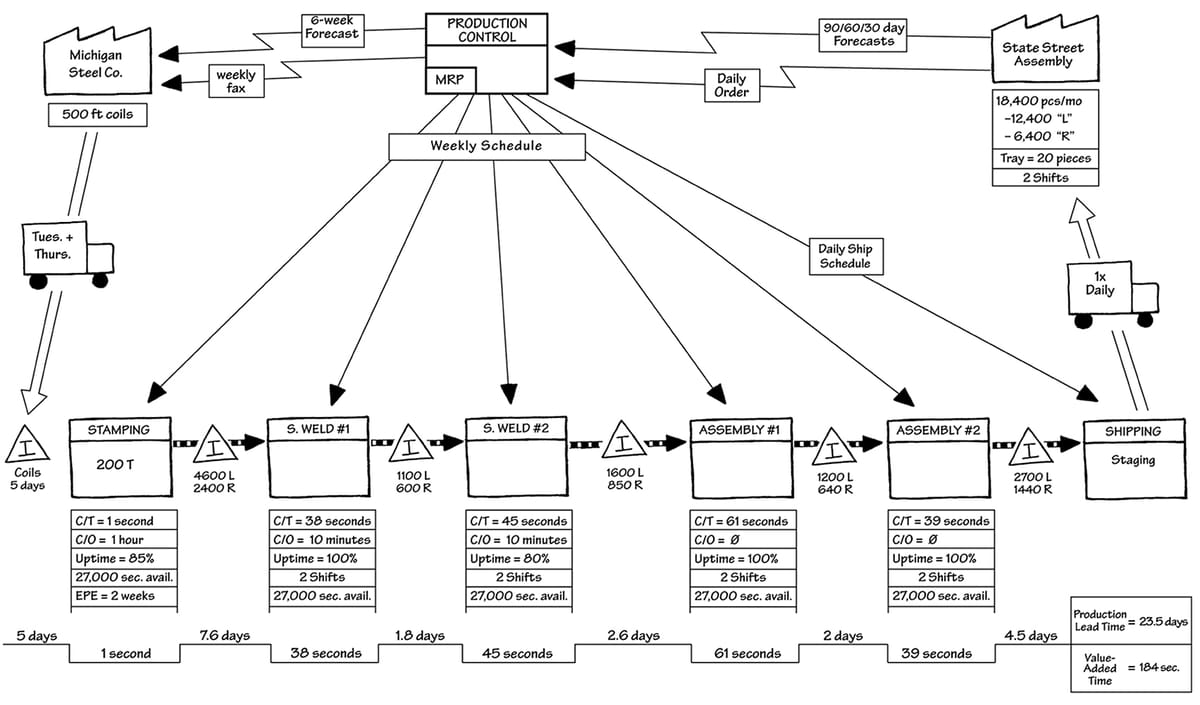
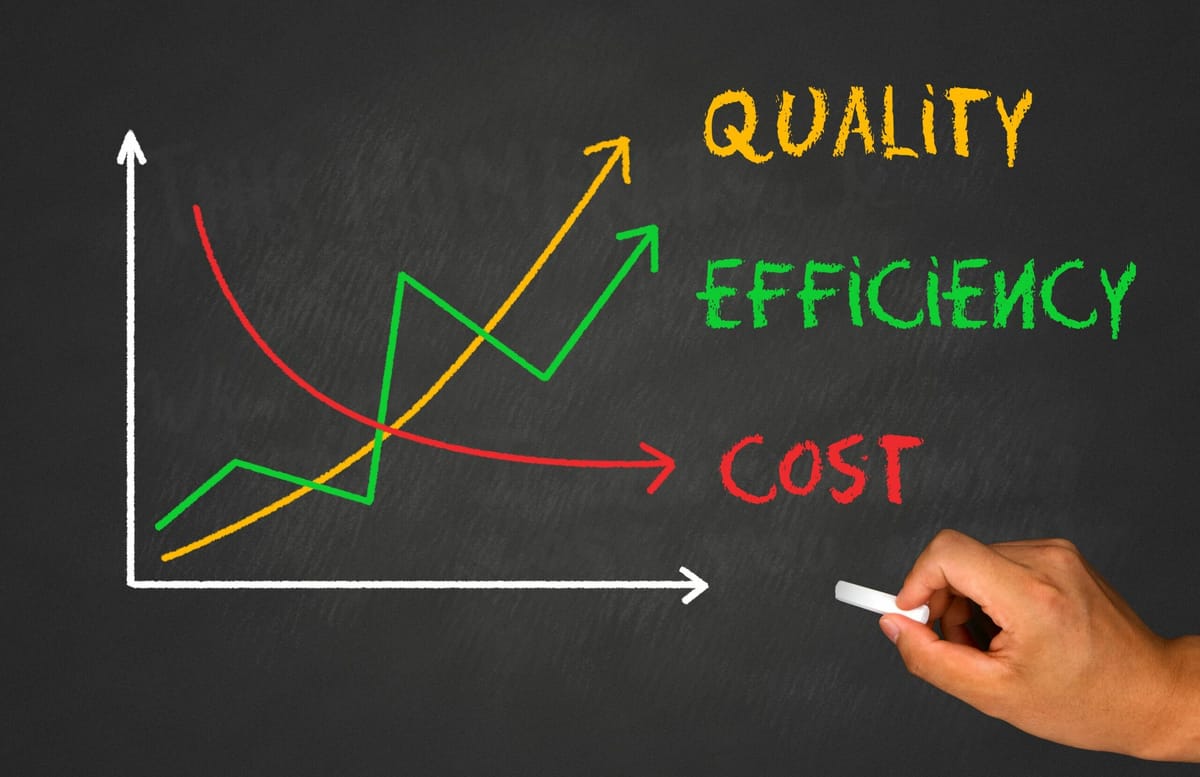
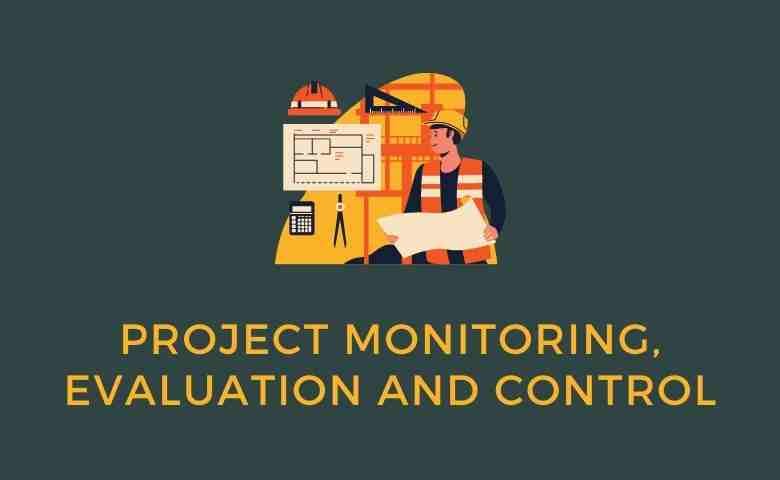
Regular Monitoring and Review
Regular monitoring and review are essential for keeping construction projects within budget. This practice ensures that any cost overruns are identified and addressed promptly.
Implementing Real-Time Tracking: Utilising technology for real-time tracking of expenses is crucial. Project management software can provide up-to-date information on all aspects of the project, allowing for quick identification of any deviations from the budget.
Scheduled Reviews: Setting regular intervals for reviewing the project’s financial status is a good idea. These reviews should involve all key team members, including the project manager, contractors, and stakeholders. During these meetings, the project's progress is compared against the budget, and necessary adjustments are made.
Identifying Cost Overruns Early: The earlier a potential cost overrun is identified, the easier it is to mitigate. Regular monitoring allows for quick action, preventing small issues from turning into larger, more costly problems.
Adjustments and Course Corrections: Regular review meetings provide an opportunity to make adjustments to the project plan. This might involve reallocating resources, adjusting timelines, or even re-negotiating with suppliers and contractors.
Documenting and Learning from Mistakes: Keeping detailed records of any issues and how they were resolved is valuable for future projects. This documentation can serve as a learning tool, helping to avoid similar mistakes in future projects.
Consistent monitoring and review are not just about maintaining control over the budget; they are also about ensuring the overall success of the project. This proactive approach to project management can lead to more accurate cost estimates, better resource allocation, and ultimately, a more efficient construction process.
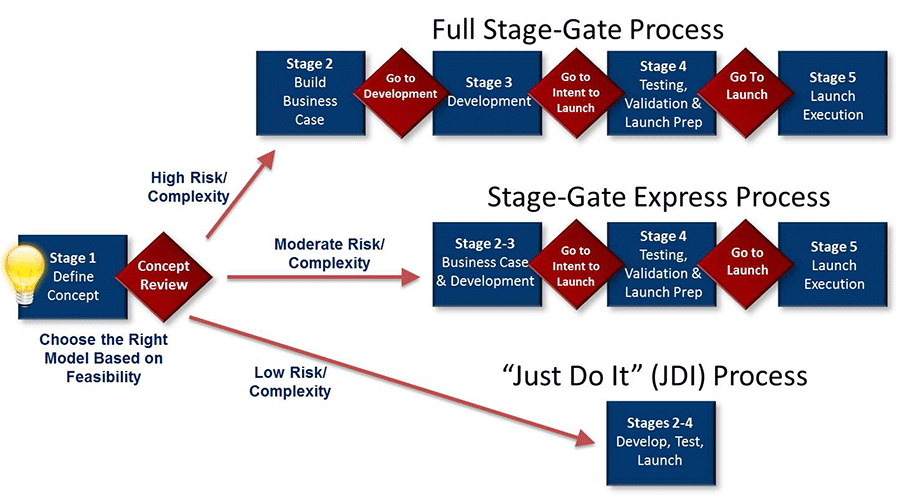
Conclusion
In the construction industry, controlling and reducing costs is an ongoing challenge. However, as we have explored throughout this article, there are multiple strategies that can be employed to effectively manage and reduce these costs. From the early stages of planning and design to the final stages of construction, each step offers opportunities for cost savings.
Effective planning and design are the cornerstones of cost-efficient construction. Streamlining labour costs, optimising the use of building materials, and minimising change orders are crucial steps in keeping a project within budget. Leveraging modern technology, such as project management software and Building Information Modeling, can significantly enhance efficiency and cost control. Additionally, effective waste management not only saves money but also contributes to environmental sustainability.
Negotiating with suppliers and contractors, utilising value engineering, and regular monitoring and review are also key elements in cost management. These strategies are not just about cutting expenses but are about adding value and efficiency to the construction process.
Ultimately, reducing construction costs is about making informed decisions, staying adaptable, and maintaining open communication among all stakeholders involved. By employing these proven strategies, construction business owners, general contractors, and home builders can achieve their goal of delivering high-quality projects while maintaining control over their budgets.
In conclusion, while managing construction costs can be complex, a strategic approach incorporating these ten proven methods can lead to successful and cost-effective construction projects.
Frequently Asked Questions
Q1: How can small construction firms reduce their material costs?
A1: Small construction firms can reduce material costs by negotiating bulk purchase discounts, exploring cost-effective material alternatives, and establishing long-term relationships with suppliers for better deals. Additionally, efficiently managing inventory to minimise waste can also help in reducing costs.
Q2: Is it possible to reduce labour costs without compromising quality?
A2: Yes, labour costs can be reduced without compromising quality by improving workforce efficiency through training, adopting modern construction methods and technologies, and optimising labour scheduling. Incentive programs for timely and quality work can also increase productivity, reducing overall labour costs.
Q3: Can technology really help in cutting down construction costs?
A3: Absolutely. Technology, such as project management software and Building Information Modeling (BIM), can significantly cut down costs by improving project planning, enabling real-time tracking, and reducing errors and reworks. Drones and AI can also streamline site surveys and predict potential delays or cost overruns.
Q4: What are the risks of using cheaper materials in construction?
A4: While using cheaper materials can reduce initial costs, it can sometimes lead to higher long-term expenses due to maintenance, repair, or replacement if the materials are of lower quality. It's important to balance cost with quality and ensure that the materials meet the necessary standards and requirements.
Q5: How can effective project management reduce construction costs?
A5: Effective project management contributes to cost reduction by ensuring efficient use of resources, timely completion of projects, and minimising delays and errors. Regular monitoring, accurate budgeting, and effective communication among all stakeholders are key aspects of successful project management.