The views expressed here are based on our personal observations and interpretations.
Readers should treat this as our subjective viewpoint and not rely on it as professional advice.
Introduction
In the aftermath of a startling event overseas—where a healthcare CEO was reportedly killed in retaliation for denying a claim—there’s a sobering lesson to consider here in Australia: when companies hold the power to impact human well-being, be it in healthcare or home construction, ethical and moral responsibilities come to the fore.
While we condemn any act of violence outright, this tragic scenario underscores the profound influence corporate decisions can have on people’s lives.
Just as health insurers influence patient care and outcomes, so too do residential builders shape the health and comfort of homeowners.
Think of your home as a kind of “healthcare provider” for your family’s well-being. After all, you rely on it for warmth, safety, and a healthy environment—just as you rely on a healthcare system to maintain your physical health. When builders cut corners, opt for barely compliant methods, or ignore well-established construction science, they risk creating unhealthy living conditions.
We’ve covered mould crises, condensation issues, and poor moisture management in previous articles (see further reading section below). These aren’t small cosmetic faults; they’re factors that affect indoor air quality, thermal comfort, and long-term health.
Yet, the typical homeowner has been taught to trust that if a house “meets code,” it must be good enough. Unfortunately, this often is not the case.
Current State of the Australian Residential Construction Industry
In Australia, construction standards and building codes exist to ensure a baseline of safety and structural integrity. But the bare minimum isn’t a synonym for quality.
The industry, dominated by large project builders and constrained by a culture of “meeting compliance,” frequently fails to place occupant health at the centre of its priorities.
Many homeowners are dazzled by modern kitchens, shiny fixtures, and marketing promises, diverting attention from what truly matters: whether the home’s design, methods, and materials promote a healthy, energy-efficient, and durable living space.
This post isn’t just another cautionary tale. It’s a demand for greater accountability.
If we scrutinise healthcare executives for decisions that impact patient health, why do we not hold construction company directors and owners—who have a similar impact on homeowner well-being—to the same standard?
With property prices rising and quality controls seemingly lagging, it’s time to insist on more than superficial finishes. Builders must step up, embrace continuous improvement, and move beyond minimum compliance.
Homeowners, regulators, and the industry as a whole must push for systemic changes, ensuring that design and building practices deliver truly healthy, comfortable, and resilient homes.
Why Accountability Matters in Home Construction
Health and Amenity at Stake
Accountability in the construction industry goes well beyond adherence to a checkbox of standards. The homes we live in directly impact our physical health and psychological well-being. Poorly designed and constructed dwellings can trap moisture, foster mould growth, and fail to maintain comfortable indoor temperatures.
Exposure to mould spores, condensation issues, and poor ventilation can lead to respiratory problems, allergies, and chronic health conditions, especially for children, the elderly, and those with pre-existing conditions. Beyond physical health, a poorly built home can lead to stress, frustration, and a sense of helplessness when repairs and modifications become part of daily life.
We’ve previously explored how mould is a silent but pervasive issue in many Australian new builds. Mould thrives in poorly ventilated spaces and in homes that haven’t been designed with moisture management in mind. While a mould-affected home may meet the bare minimum compliance standards, it’s hardly a model of healthy living.
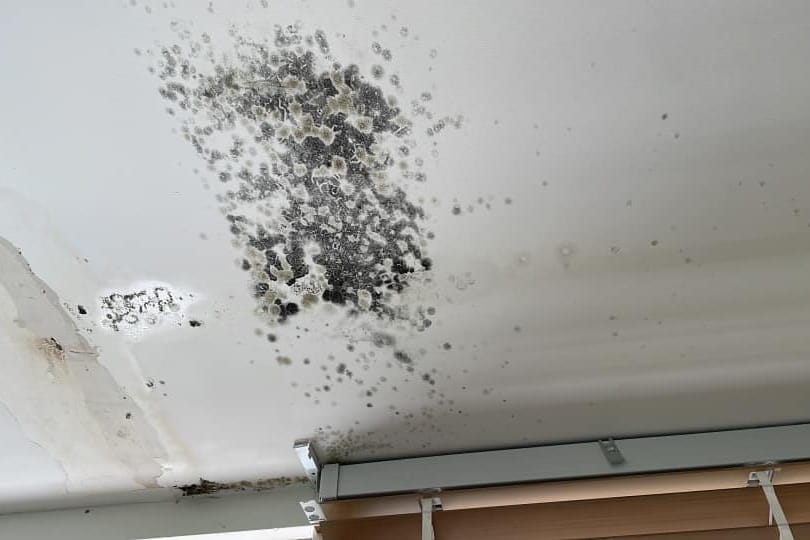
Good construction practices—like effective moisture barriers, rainscreens, and proper insulation—can prevent these issues. Yet many builders either do not prioritise these measures or treat them as expensive owner requested “extras” rather than essential components of a well-built home.
I fail to understand how building professionals do not educate owners of the options available when building, rather, they do the minimum viable sales shuffle to get them over the line and a new customer onto the books.
The Moral and Ethical Imperative
In healthcare, when a patient’s well-being is compromised by institutional neglect, we recognise a moral failing. Similarly, when a home’s design and construction make inhabitants sick or force them into stressful living conditions, it signifies an ethical lapse.
Construction companies, like healthcare providers, have a duty of care. This duty extends from the executive boardroom down to the tradespeople onsite. Owners and directors who push production deadlines while ignoring best practices place profit ahead of people.
The industry’s repeated failure to fully integrate building science, quality management systems, and continuous improvement into standard practice represents not just a technical oversight but a moral one.
Home building isn’t merely an engineering exercise; it’s the creation of environments where families grow, children sleep, and the elderly seek comfort.
If an executive disregards known design methodologies—such as performing a condensation risk analysis—this is akin to a doctor ignoring a known treatment protocol.
In both cases, the result is the same: long-term harm to the very people who rely on their supposed expertise and trust their judgement. Executive ignorance isn’t merely an oversight—it’s contributory negligence. Individuals without actual building experience have no place running construction companies. Lacking the necessary know-how, they reduce every decision to cost and speed alone, ignoring the short-, medium-, and long-term consequences for quality.
People rise to the highest level of incompetence when they're promoted beyond their abilities, leaving them in roles where they can do the most damage—or at least the least good.
You can’t fix stupid, but many building directors sure do act like they’ve graduated top of the class at the Business School of Dumb with a major in Bootlicking.
The recent government bailout of a large private building company is a textbook example of everything wrong with the system. Bloated management, razor-thin margins (?), and the "too big to fail" excuse meant the government decided the blow back from letting them collapse was worse than the cost of bailing them out.
But wait—it gets better. After the bailout, the same company was handed a contract for around 480 houses, only to turn around and sell its majority stake to a foreign investor. Seems like a deal was done to cement the sale and incentivise the investment.
You couldn’t script this if you tried. And yet, somehow, the company has the audacity to spin this spectacular failure as a roaring success. Clap slower, please 👏 👏 👏
Beyond the Legal Minimum
Building codes and standards set the legal floor for construction quality, not the ceiling. Meeting these baseline requirements is not the same as delivering homes that are truly fit for purpose, especially in a country with varied climates like Australia’s.
A house that just clears legal hurdles may not be energy efficient, moisture-resistant, or comfortable to live in year-round.
While some builders claim “compliance” as a badge of quality, real accountability means striving for best practices that go beyond the minimum.
For instance, understanding and applying advanced moisture management principles isn’t simply an extra cost; it’s a protective measure that saves homeowners from future health risks and maintenance expenses.
Accountability in the building industry means recognising that consumers often do not have the technical know-how to demand such measures. Instead, it is the builder’s responsibility to offer them as standard practice. Anything less is a dereliction of their ethical obligations to the people who will ultimately live in these structures.
Setting a Positive Precedent
If builders, directors, and CEOs commit themselves to a culture of accountability, the ripple effects will improve the entire industry.
It would motivate more widespread use of proper insulation systems, thoughtful ventilation strategies, third-party quality audits, and continuous staff training. Over time, a higher standard of care would become the norm, not the exception.
By linking executive performance and compensation to genuine quality outcomes—like independent moisture tests, occupant health feedback, and long-term durability—companies can foster a more transparent, consumer-focused ecosystem.
Accountability must be woven into the fabric of the construction process, from design to handover.
When accountability matters, everyone—homeowners, builders, and the broader community—wins.
The Illusion of Compliance
Limited Regulatory Checks
The Australian residential construction process tends to instil a false sense of security in homeowners. On the surface, it looks robust: engineers must design and inspect foundations before pouring concrete, building certifiers verify that the frame is adequately braced and tied down, and at the completion of construction, a certificate of occupancy is issued to confirm that the home “meets code.”
But what does “meeting code” really mean for everyday living quality?
Unfortunately, these mandated checks often focus on structural integrity and meeting bare-minimum standards, not on whether the home will remain healthy, comfortable, and durable over its lifespan.
Unlike other industries that have thorough, multi-stage quality audits, the residential building sector often relies on a handful of snapshot inspections. The result is that the lion’s share of quality decisions—like how moisture is managed, how insulation is installed, or how airflow is maintained—remain at the builder’s discretion.
If a design element is technically permissible under the code but fails to account for moisture buildup or future maintenance issues, the homeowner pays the price. Compliance in this sense is closer to a legal loophole than a guarantee of long-term performance.
The Conflict of Interest in Certification
One of the systemic flaws lies in who hires and pays the certifier. Typically, it’s the builder, not the homeowner. While many certifiers maintain professional integrity, the reality is that their ongoing work often depends on the builder’s continued business.
This arrangement can create subtle pressures to “go easy” on enforcement. After all, pushing too hard for improvements or calling out borderline practices can be seen as adversarial, risking a loss of future contracts.
The result? A process that, while officially independent, is structurally inclined to favour the builder’s interests over the homeowner’s long-term well-being.
We’ve touched on this issue in previous articles discussing why builders should conduct condensation risk analyses or install rain screens. The problem is that these proactive measures are not mandated, and if not rigorously demanded by certifiers—or more importantly, driven by builders themselves—they’re often skipped to save time and money.
From Bare Minimum to Lost Opportunities
Meeting compliance means little if it leaves families living in uncomfortably hot rooms during summers, damp bedrooms in winters, or spaces prone to mould. “Good enough” construction might satisfy the law but does nothing to ensure energy efficiency, proper ventilation, or durability.
To illustrate: a home may pass a basic structural frame check yet fail spectacularly at managing internal moisture.
This deficiency may not be immediately obvious at handover, but over months and years, problems like mould growth, poor indoor air quality, and even compromised structural components can emerge.
If comprehensive checks at each stage were mandated and performed with genuine independence, builders would have a much harder time justifying shortcuts. They would need to incorporate proven building methods—like vapour-permeable membranes, continuous insulation, and proper drainage gaps—into their standard workflows, rather than treating them as expensive afterthoughts.
The Need for Independent Oversight
True accountability requires impartial, third-party verification that isn’t beholden to the builder’s paycheck. Independent auditing could help identify future mould-prone areas, poorly installed insulation, or gaps in design that cause excessive indoor heat.
Such oversight ensures that compliance becomes more than a superficial tick-box exercise. It pushes the industry toward continuous improvement and nudges builders to adopt better practices across the board.
Until we establish such mechanisms, homeowners are left in a vulnerable position. They rely on trust—trust that the builder and the certifier will ensure the best possible outcome. Yet, as we’ve seen, that trust often goes untested and unrewarded.
By acknowledging the illusion of compliance and demanding more rigorous, genuinely independent checks, consumers can help shift the industry from focusing on what’s minimally acceptable toward what’s genuinely beneficial.
We detailed our thoughts on the need for independent oversight in our blog post linked below.
The Gap Between Marketing and Reality
Consumer Manipulation Through ‘Features’
It’s easy to be swayed by "more for less marketing", shimmering countertops, eye-catching light fixtures, and a kitchen that looks straight out of a magazine. Project builders often highlight these aesthetic features—offering flashy upgrades like fancy range hoods or designer tapware—to entice consumers. But there is always a cost to be paid so where are you paying for it?
While such additions might make the initial purchase more appealing, they rarely address the underlying quality issues in the building envelope itself.
Essentially, homeowners are being sold sizzle instead of steak: the surface appearances may impress, but the structural and environmental health aspects remain neglected.
When we previously explored the widespread mould crisis and condensation problems in Australian new homes, we saw that these issues are almost never mentioned in sales pitches. A prospective home buyer might hear about “energy-efficient appliances” but not about how well the home’s walls manage moisture or whether the design reduces thermal bridging.
This imbalance in presentation leads consumers to prioritise superficial amenities and décor, inadvertently encouraging builders to spend their time and resources on cosmetic upgrades rather than robust construction methods.
Value Engineering vs. Long-Term Quality
The term “value engineering” often appears benign, even positive. Who wouldn’t want to optimise resources and reduce costs? However, in the building context, “value engineering” can be a euphemism for cost-cutting that compromises long-term livability and resilience.
For instance, substituting cheaper materials, reducing insulation thickness, or simplifying moisture management strategies might save the builder money in the short term. These changes may not violate the building code, but they set the stage for comfort and maintenance headaches down the road.
From the homeowner’s perspective, what looks like a great deal at signing can turn into a long-term liability. Without proper moisture control, indoor air quality suffers. Without adequate insulation and ventilation, energy bills soar. And while the builder pockets higher margins thanks to these “economies,” the occupant pays in the form of reduced health, comfort, and property value.
This distortion of “value” highlights a systemic problem: the market currently rewards superficial features and nominal compliance rather than durable, health-focused construction.
Deceptive Perceptions of Quality
The industry’s marketing tactics often lead consumers to believe that a prominent builder’s brand or a glossy brochure equates to reliable quality. In reality, many large builders share the same subcontractor pools, source similar materials, and follow the same minimal standards.
A builder’s reputation might rest on a handful of landmark projects or alluring display homes that only represent their best work, not the median build.
Without proper oversight, what you see in the showroom or marketing materials may not reflect what you’ll actually live with for decades.
Consumers rarely ask to see quality management plans, third-party inspection results, or proof of genuine building science integration.
Builders capitalise on this knowledge gap, focusing their sales process on upgrades and cosmetic differentiation rather than on the invisible, yet important, aspects of building performance.
Education as a Tool for Empowerment
To bridge the gap between marketing and reality, homeowners must be better informed. Prospective buyers can demand more transparency by asking to review the builder’s construction management plans, moisture management strategies, or any independent auditing done before handover.
Doing so flips the script: rather than being dazzled by a shiny bathroom fixture, you start evaluating whether your future living environment is set up for health, comfort, and durability.
Educated consumers create a market incentive for change. If buyers prioritise real quality over superficial features, builders will have to adapt to meet that demand.
Over time, this collective shift in consumer priorities encourages an industry-wide improvement, making sincere quality and accountability the new marketing hook.
Industry Associations and the Illusion of Quality
The Role of Industry Associations
Industry organisations/lobby groups present themselves as guardians of craft and quality within the residential construction sector. They market their membership as a hallmark of professionalism and expertise, implying that builders who display their logos operate under elevated standards.
At face value, this association membership reassures consumers, suggesting that any builder bearing these credentials must be competent, well-trained, and committed to excellence.
Membership Without Meaningful Standards
However, when we look closer at the criteria for membership, a very different picture emerges. While these associations hold significant influence and boast widespread industry representation, their membership requirements often amount to little more than paying annual fees.
There is no robust, ongoing requirement to demonstrate proven quality management processes, adherence to advanced building science principles, or consistent delivery of healthier, more durable homes.
In practice, anyone—even a builder with a history of poor workmanship, or one who has declared bankruptcy only to “phoenix” into a new company—can join simply by paying annual dues. This lack of enforced quality criteria reduces the association’s badge to a mere marketing tool rather than a genuine credential.
A Missed Opportunity for True Standards
If industry associations truly aimed to elevate the industry, they could establish and enforce rigorous membership standards, mandating continuous education, independent quality audits, and transparent performance metrics.
Instead, the absence of stringent requirements means the organisations function more like lobby groups and industry aggregators than quality gatekeepers.
Their primary value lies in securing a seat at regulatory and policy discussions, leveraging a large membership base to influence outcomes. Unfortunately, none of this translates into guaranteed excellence for the consumer.
Window Dressing for the Industry
Without minimum quality benchmarks, membership logos become little more than window dressing—pretty signs suggesting mastery where none may exist. This gap between image and reality misleads consumers, who reasonably assume that such memberships indicate professionalism and skill. In fact, what they often get is a builder no better than one without such affiliations, just one who has paid for an industry “seal of approval” that does not reflect genuine scrutiny or accountability.
Demanding More From Industry Bodies
To restore public trust and ensure these organisations offer tangible benefits, consumers and policymakers must push for reforms within these industry associations.
Mandating quality management demonstrations, requiring ongoing professional development, and conducting regular, independent assessments of members’ building standards would transform these groups into meaningful arbiters of quality.
Until that occurs, the brand recognition these associations confer remains largely symbolic, failing to protect homeowners or encourage builders to truly excel.
Oh, that’s right—you need to pay just to see these elusive “standards.”
Because ensuring builders meet proper quality guidelines should obviously be a pay-per-view event, right? Makes perfect sense..
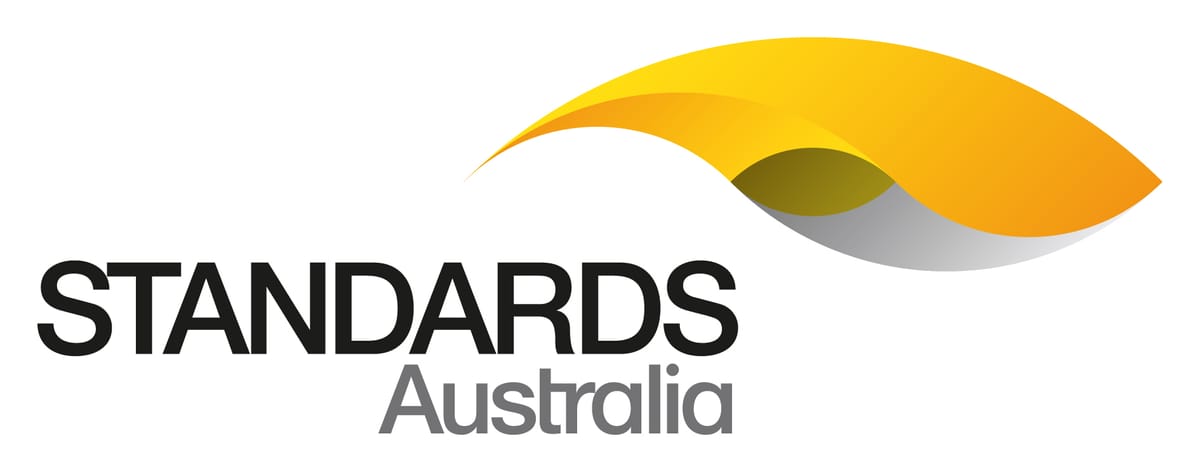
Unmasking the Decision-Makers
Who Are the Directors and CEOs of Building Companies?
When it comes to residential construction, we often picture skilled tradespeople, architects, and engineers working toward a common goal: a safe, healthy, and comfortable home. Yet, as the industry evolves, decision-making power frequently resides in the hands of directors, CEOs, and board members who may have little to no practical building experience or formal building education only marketing, accounting or even hospitality industry backgrounds.
Many are adept at running a business—maximising margins, optimising supply chains, and scaling operations—but lack a deep understanding of building methods, materials or building science.
This disconnect between executive leadership and practical know-how poses a serious challenge. How can someone who has never truly engaged in hands-on building, studied moisture management systems, or analysed thermal bridging detail influence the creation of quality, livable homes?
Without a grounding in these fundamentals, strategic decisions can lean heavily toward profit maximisation and brand perception rather than occupant health and comfort.
In essence, we have non-experts steering the quality and sustainability of an entire industry, relying on the bare minimum compliance structure to validate their choices.
Profit vs. Quality Incentives
By and large, executive compensation packages in the construction industry hinge on meeting sales targets, achieving certain profit margins, and maintaining shareholder returns. These incentives rarely, if ever, factor in the post-occupancy health of homeowners or the long-term performance of the structures themselves.
A CEO might be rewarded for cutting construction times, securing cheaper materials, or signing off on “value-engineered” designs that reduce overhead—without any regard for the hidden cost in occupant well being and increased maintenance down the road.
This structure effectively places quality, continuous improvement, and occupant health as secondary considerations, if they register at all. Instead of asking, “How can we build a home that stays mould-free and energy-efficient for decades?” decision-makers might be asking, “How can we cut $5,000 off the build cost to offer a promotional deal?”
The immediate financial gains overshadow the ethical responsibility to deliver homes that won’t compromise residents’ respiratory health or comfort.
When professional qualifications or building science expertise are not prerequisites for leadership roles, it’s no surprise that homes can end up as products of cost-led decision-making rather than well-considered design.
If bonuses were tied to independent quality audits, occupant satisfaction surveys, or long-term durability assessments, directors and CEOs would have a compelling reason to push for industry-leading construction practices. Instead, the current system tacitly encourages them to do the bare minimum.
A Call for Greater Transparency and Qualification
To address this imbalance, homeowners, regulators, and advocacy groups must demand more transparency around who is calling the shots at building companies.
Are these individuals qualified builders, or at least extensively educated in building science and sustainability?
Can they articulate why their construction methods differ from their competitors in ways that promote better indoor air quality or superior moisture management?
Shining a light on executive decision-making means asking tough questions.
It involves probing the credentials and motives of those at the top and challenging them to demonstrate a genuine commitment to delivering healthier homes.
If consumers begin to ask, “What experience do your directors have in building science? How do they ensure your company’s designs meet long-term health and environmental goals?” we may see a paradigm shift. Business leaders will be forced to incorporate meaningful quality metrics and accountability measures into their operational models.
Aligning Incentives with Quality and Accountability
Imagine a scenario in which government bodies, industry associations, and consumer advocacy groups collaborate to benchmark quality, health outcomes, and environmental performance as standard metrics.
Directors and CEOs would then have their reputations, and possibly their compensation, tied to delivering these results.
This shift could spark a change in thoughtful design, robust project management, and genuine quality control measures, lifting the entire industry and restoring consumer trust.
By unmasking who makes the decisions and understanding the incentive structures that guide them, we can begin to hold these leaders to account. In doing so, we help ensure that the people at the helm recognise the profound responsibility they carry—no less significant than that of a healthcare executive determining the fate of patients.
After all, homes are more than commodities; they are environments that shape the health, comfort, and happiness of those who live inside them.
Owner-Building as an Alternative to Project Builders?
Empowering Homeowners
In a market where large project builders often wield significant influence over prices, timelines, and material choices, the idea of becoming an owner-builder can seem daunting—but it’s also increasingly appealing. Taking charge of your own construction project allows you to set the standards, select materials, and engage tradespeople based on merit rather than who the builder chooses.
While not everyone has the time, resources, or inclination to go this route, it does offer a radical form of consumer empowerment. Instead of relying on a project builder’s opaque decision-making process, an owner-builder can impose their own quality requirements from the start.
Not a Silver Bullet
Owner-building isn’t a perfect solution for everyone. It requires a commitment of time, money, and patience, as well as a willingness to learn about construction methods and regulatory frameworks.
Mistakes made through inexperience can be costly, both financially and in terms of delayed occupancy. Additionally, banks and lenders may be more cautious financing owner-builder projects, and insurance requirements can be more complex.
However, for those with the determination and resources, owner-building provides a pathway to achieving a higher standard of quality on your own terms. By establishing strict specifications, commissioning independent inspections at each stage, carrying out your own thorough stage based quality management inspections and refusing to cut corners, the owner-builder can deliver a healthier, more durable home.
Influencing the Broader Market
An increase in owner-building or even the possibility of it sends a strong message to the industry. If enough consumers bypass project builders, these companies must adapt to stay competitive.
They’ll need to improve their transparency, adopt better construction methods, and elevate their quality control measures to lure customers back from the owner-builder market. In other words, the growth of owner-building as an alternative pathway can, in itself, push large builders toward accountability and quality improvements.
It’s important to acknowledge that owner-building isn’t the only answer, and not everyone wants—or is able—to take it on. The ideal scenario is one where you don’t have to become a builder yourself just to ensure a decent outcome.
Still, just the existence of this option provides leverage. As consumers become savvier and realise that they can, if necessary, bypass the conventional model, they gain influence.
Builders who continue offering substandard homes will find themselves increasingly out of step with a more informed and empowered homeowner base.
In a fair marketplace, buyers wouldn’t need to build their own homes to secure quality and accountability. Yet, until the industry adjusts its priorities and incentive structures, owner-building stands as an empowering alternative—a way for homeowners to reclaim control and demand the excellence that should have been standard practice all along.
A Call to Action
Pressure on Directors and CEOs
It’s time to shift our focus from isolated incidents and questionable design choices to the executives and directors at the helm of building companies.
If we believe in holding healthcare leaders accountable for the well-being of patients, it’s only fair to hold building company directors to a similar standard for the environments they create. These decision-makers must feel pressure from consumers, advocacy groups, and regulators to prioritise long-term health, comfort, and quality over short-term margins.
Consumers can write letters, submit reviews, and share their experiences on social media. Regulators and industry bodies can enact policies mandating more rigorous oversight. When directors realise that cutting corners risks not just reputational damage but tangible financial and legal consequences, the incentive structure begins to change.
The Need for Structural Change
Real change often requires more than consumer education and moral appeals; it may need structural reforms. For example, implementing independent, third-party inspections at critical project stages or tying executive compensation to long-term quality metrics can realign priorities.
Facilitating industry-wide training programs that emphasise building science & technical literacy and constant improvement in compliance with Australian Standards, training and education in Project & Construction Management could help ensure everyone from top-tier executives to on-site trades understands why certain practices matter.
Government incentives for builders who demonstrate superior health and efficiency standards could further encourage a market shift. Linking rebates, grants, or reduced insurance premiums to proven quality and durability measures would reward forward-looking builders.
Over time, these systemic changes cultivate an environment where the “bare minimum” no longer suffices, and builders who deliver truly outstanding results gain a competitive advantage.
Conclusion
For too long, the conversation around residential construction in Australia has fixated on cosmetic features and baseline compliance checks. The recent tragedy overseas—though not directly related—serves as a reminder to all that companies wield immense power over our health and comfort.
When builders, their directors, and executives make decisions that prioritise profit over occupant well-being, they fail in their moral duty as surely as any healthcare provider who neglects a patient’s needs.
As Australia’s housing market evolves, the industry must step beyond the bare minimum and embrace accountability, transparency, and genuine quality.
It’s no longer acceptable to hide behind glossy sales pitches or minimally compliant finishes. Continuous improvement—adopting best practices in design, moisture control, insulation, ventilation, and overall construction management—should be seen as non-negotiable, not optional.
There are consequences for the decisions made and not made by directors including those shadow directors who hide behind their public faced puppets. This is a wake up call for all who prioritise personal or shareholder returns over the consumers they extol to work for.
It’s time to demand more from those who shape the environments we inhabit. The call to action is clear: Hold builders accountable by asking tougher questions, supporting stronger regulations, and considering alternatives like owner-building if the status quo refuses to change.
By illuminating the responsibilities of directors and executives, encouraging independent oversight, and insisting on better building science education, we can transform the Australian construction landscape. In doing so, we ensure that homes serve their ultimate purpose: providing a healthy, comfortable, and secure place to live and thrive.
Frequently Asked Questions (FAQ)
- Why should I worry about the builder’s accountability if my home meets basic compliance?
Basic compliance only ensures the home is not dangerously unsafe. It doesn’t guarantee that it’s well-insulated, moisture-resistant, energy-efficient, or free from potential health hazards like mould. Accountability pushes builders to go beyond the minimum, delivering a healthier, more comfortable living space. - Aren’t certifiers independent and responsible for ensuring quality?
While certifiers play an important role, they’re often hired by the builder and focus mainly on structural and code requirements. They typically don’t look deeply into building performance issues like moisture management, long-term durability, or indoor air quality. - How does mould or condensation affect my family’s health?
Prolonged exposure to mould can cause respiratory issues, allergies, and worsen conditions like asthma. Condensation leads to damp environments that encourage mould growth and degrade indoor air quality, affecting everyone’s comfort and well being. - Why can’t I just trust a well-known builder’s reputation?
Many large builders share the same trade pools and often prioritise cost savings over long-term health and efficiency. A strong brand doesn’t always mean the builder invests in superior construction practices or thorough quality management. - What documents or evidence should I ask my builder to provide?
Request their quality management plan, independent inspection reports, and evidence of design considerations like condensation risk analyses, proper insulation strategies, and moisture control details. This information offers a clearer picture of their commitment to quality. - Is owner-building a viable solution to ensure a healthier home?
Owner-building can give you full control over materials, methods, and inspections. However, it’s not for everyone. It requires time, research, and strong project management skills. Still, it can be a pathway to achieving higher-quality standards if you’re willing to learn. - How can consumer pressure influence builder practices?
When buyers demand transparency, ask tougher questions, and are willing to look elsewhere, builders have to adapt. Informed consumers can collectively push the industry toward better standards, making it harder for builders to ignore critical aspects of home quality. - Are there any reforms in progress to improve building quality standards?
Regulatory bodies and industry groups occasionally review and update standards. Consumer advocacy and media attention on issues like mould and poor-quality builds have begun to prompt greater scrutiny. However, true reform often requires sustained pressure from consumers, industry professionals, and policymakers. - How does improving building quality benefit the environment?
Better insulation, moisture control, and thoughtful design translate into higher energy efficiency, reduced greenhouse gas emissions, and less resource waste over the home’s lifespan. Sustainable homes are better for both occupants and the planet. - Is it possible to hold directors personally accountable for poor construction practices?
Legal frameworks vary, but directors can face consequences if negligence or disregard for health and safety standards is proven. As public awareness grows, so does the push for more stringent accountability measures and oversight that could lead to enforceable consequences.
Further Reading
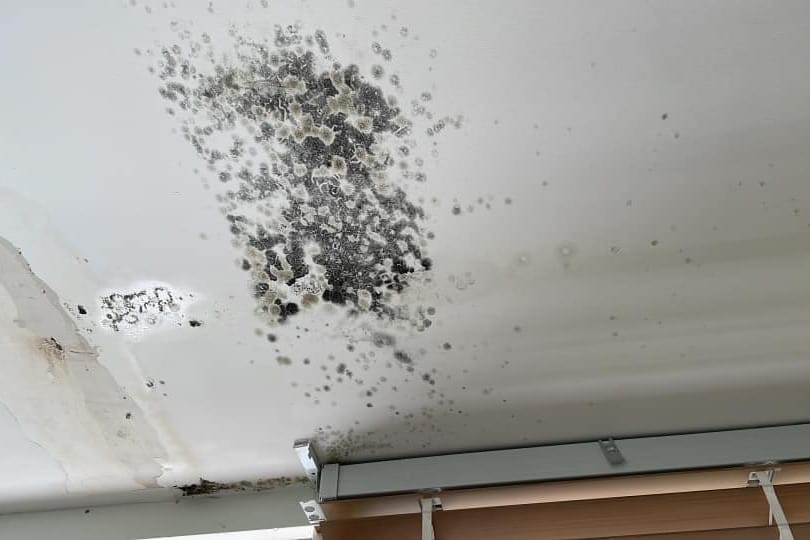
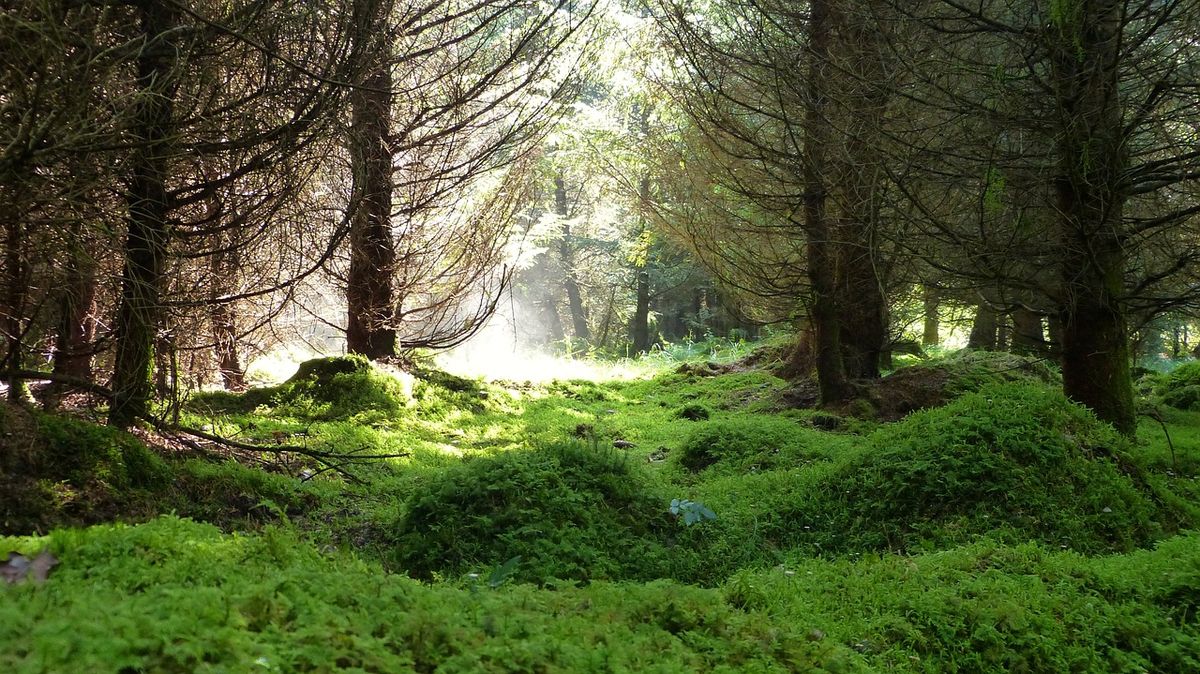
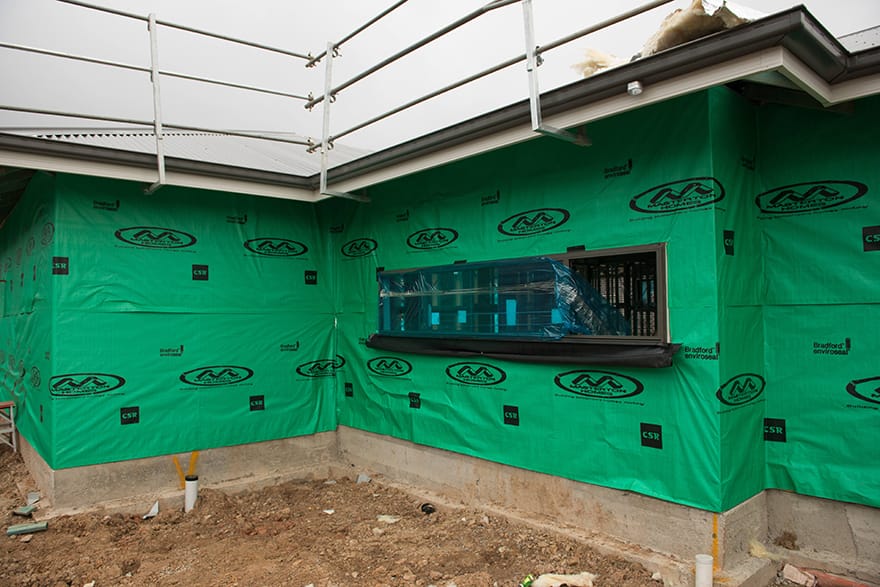
