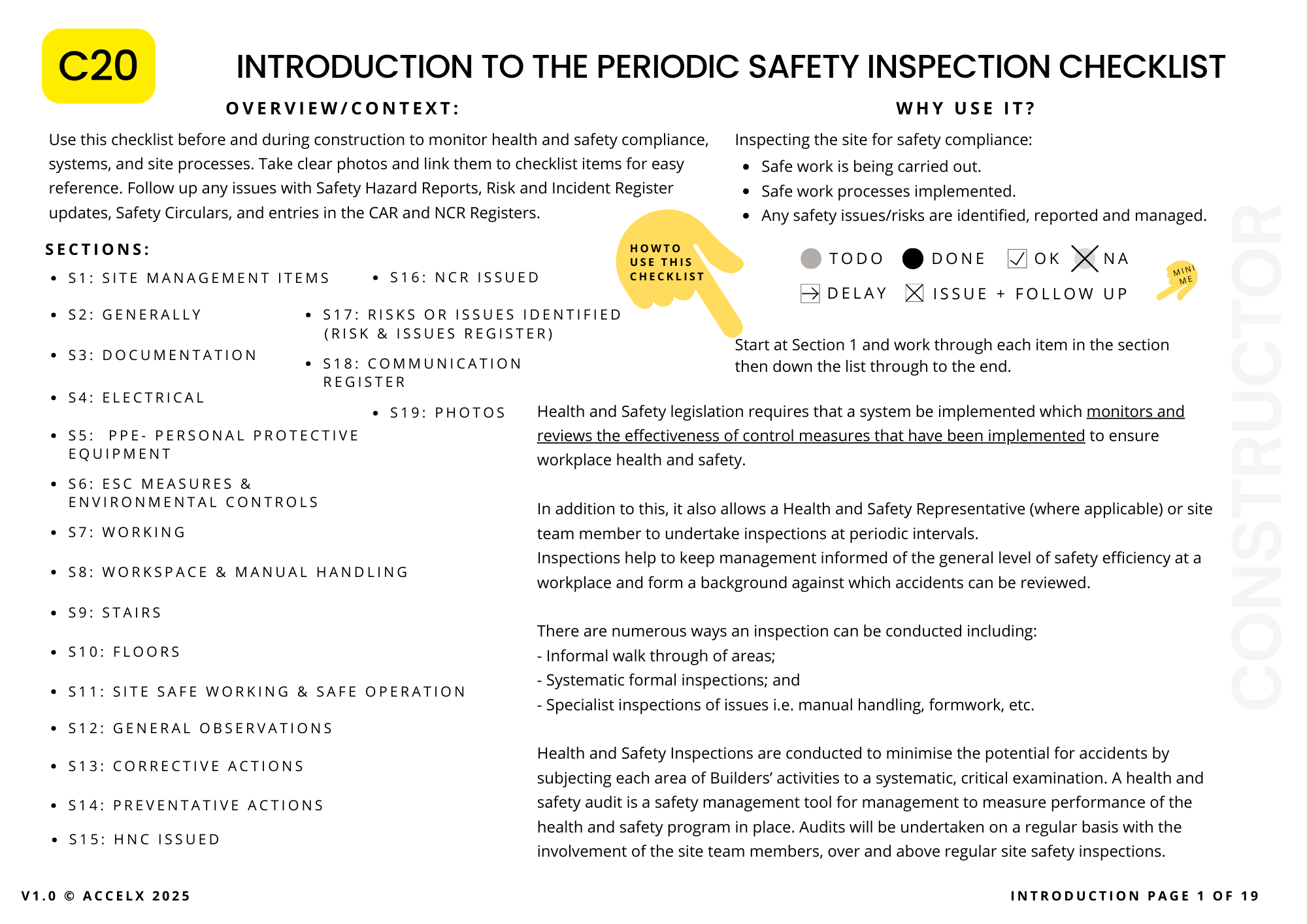
Introduction
Building Your Dream Home? Safety Starts with a System.
Constructing your first home should be thrilling—not stressful. But without a structured approach to safety and compliance, that excitement can quickly turn into anxiety.
Take Sarah and Mark, first-time builders in Sydney. They trusted their contractor’s promises of “frequent safety checks”—until a near-miss with untested electrical equipment revealed gaps in their site’s safety management plan.
A 2023 SafeWork NSW report found that many site accidents can be prevetnted through better awareness and reducing unsafe practices - LINK. One homeowner in Melbourne faced $22K in fines after sediment runoff (S6 violation) contaminated a neighbouring property—a risk the C20 checklist flags early.
This is why we created the C20 Periodic Safety Inspection Checklist. More than just a formality, this tool:
- Demystifies compliance (no jargon, just clear checks).
- Prevents costly mistakes (like council fines for sediment runoff).
- Puts you in control (even if you’re not a construction expert).
In this post, you’ll learn how to use the C20 checklist to:
✅ Spot hazards before they become accidents.
✅ Avoid delays and budget blowouts.
✅ Build with confidence—not crossed fingers.
Our C20 Periodic Safety Inspection Checklist is here to clear away your confusion, smooth out the stress lines, keep your site safe, a smile back on your dial and ensure your project stays productive.
2. Why Use A Periodic Safety Inspections
1. Legal Compliance Isn’t Optional
Under the Work Health and Safety (WHS) Act 2011, builders and homeowners share accountability for site safety. The C20 checklist helps you:
- Meet Duty of Care obligations (Section 19).
- Document due diligence (Section 27) – critical if disputes arise.
Real consequence: A Perth builder faced $75K in penalties after failing to prove regular inspections (SafeWork WA, 2023).
2. Stop Problems Before They Start
Construction sites evolve daily. The C20 checklist catches risks like:
- Untested electrical gear (S4) – #1 cause of preventable incidents (AS/NZS 3760).
- Missing edge protection (S7) – 58% of falls linked to unchecked temporary structures (SafeWork Australia).
3. Protect Your Budget and Timeline
A single oversight can derail projects:
- Example: S6 (Environmental Controls) neglect led to 3-week delays for a Queensland family after sediment runoff triggered council intervention.
4. Build Trust with Trades
Contractors respect sites that prioritise safety and cleanliness:
- Clear checklists reduce arguments—everyone knows exactly what’s expected.
- Everyone goes to work and wants to get home safely at the end of the day.
Why are these inspections so important?
Firstly, they help you identify and rectify safety hazards early. Construction sites are busy places with multiple activities happening simultaneously, increasing the risk of accidents or injuries. Regular inspections ensure these risks are minimised.
Secondly, inspections help maintain quality standards. By systematically reviewing each area, from site management to electrical safety and environmental controls, you're able to spot issues that might affect the health and safety of site workers. Safe workers are more productivity workers.
Have you ever tried to do anything when clutter and rubbish is around you? It slows you down. It's no different to a building site, cleanliness and organisation correlates to productivity/output.
1. Safety Directly Impacts Output
Systematic inspections do more than tick compliance boxes—they remove the hidden drags on productivity. Consider:
- Clutter = Slowdown: A site littered with debris (S2.08) forces workers to navigate obstacles, adding unnecessary time to tasks.
- Hazards = Distractions: Untagged electrical gear (S4.02) or missing edge protection (S7.05) divert mental energy from work to risk avoidance.
2. The Clean Site Advantage
Data shows organized sites finish 12% faster (SafeWork NSW, 2023) because:
- Workers spend less time searching for tools/materials (S8.04).
- Fewer tripping hazards (S10.04) mean fewer work stoppages.
3. The Human Factor
Safe, orderly sites:
- Reduce fatigue (no wasted effort circumventing risks).
- Improve morale (workers feel valued when PPE/SWMS are enforced (S5, S3)).
Finally, periodic safety inspections safeguard your investment. By catching issues early, you prevent small problems from becoming big, costly ones that lead to delays and budget overruns.
Ultimately, these inspections help your project run smoother and finish on time.
In short, adopting a regular inspection routine with a structured checklist is one of the smartest decisions you can make to protect your home-building project.
The C20 Checklist isn’t just a compliance formality—it’s your proactive system to measure, manage, and prove safety and quality standards. Because in construction, what gets tracked gets improved.
3. Key Checklist Sections Explained
1. Site Management (S1)
Important Checks:
- Sediment controls: Functional fences, straw wattles for drainage (S1.01, S1.06)
- Builder signage: Visible from street (S1.02)
- Neighbour protection: No damage to adjoining properties (S1.04)
- Sanitary facilities: Toilet within pegged boundaries (S1.08)
- Stormwater systems: Unblocked grates, proper drainage (S1.11, S1.13)
Why It Matters:
- Prevents council fines (e.g., $10K+ for sediment runoff under Environmental Protection Act)
- Ensures basic site setup meets contractual requirements
🔧 Action Step: Photograph sediment controls weekly—councils accept timestamped images as evidence of due diligence.
2. General Site Conditions (S2)
Important Checks:
- Emergency preparedness: Clear muster points (S2.02, S2.03)
- Site cleanliness: Orderly work areas, unobstructed access (S2.08, S2.09)
- Amenities: Clean WC, drinking water available (S2.06, S2.07)
- Traffic/deliveries: Adherence to Traffic Management Plan (S2.10, S2.12)
Why It Matters:
- Reduces slip/trip hazards (most common injuries on sites)
- Complies with WHS Regulations 2011 for emergency protocols
3. Documentation Compliance (S3)
Important Checks:
- SWMS/JSA: Available for high-risk tasks (S3.03, S3.04)
- Worker credentials: Valid White Cards (S3.09)
- Chemical safety: MSDS up-to-date (S3.11)
- Emergency contacts: Posted onsite (S3.08)
⚠️ Red Flag: "Missing SWMS (S3.12) is the #1 reason sites fail WHS audits."
4. Electrical Safety (S4)
Important Checks:
- Leads & tools: Tested/tagged, no frayed cords (S4.02, S4.03)
- RCDs: Functional and tested (S4.05)
- Greenboy/power lines: Undamaged, safe distances (S4.04, S4.07)
Why It Matters:
- Aligns with AS/NZS 3000 standards
- Prevents electrocution (15% of construction accidents)
5. PPE (S5)
Important Checks:
- Basic PPE: Helmets, boots, high-vis worn (S5.01)
- Task-specific gear: Hearing protection, masks (S5.02)
🔧 Action Step:
"Cross-check PPE against JSA/SWMS for each task (S5.03)."
6. Environmental Controls (S6)
Important Checks:
- Stockpiles: Tarped/bunded (S6.02)
- Dust suppression: Sprinklers, barriers (S6.04)
- Tree protection: No damage (S6.07)
Why It Matters:
- Avoids council stop-work orders for ESC violations
7. High-Risk Activities (S7–S11)
Key Focus Areas:
- Working at heights: Guardrails, void protection (S7.05, S9.05)
- Manual handling: Mechanical aids, training (S8.05)
- Trenching/excavation: Barricades, shoring (S11.03)
- Concrete/crane ops: Safe setup (S11.08, S11.10)
⚠️ Red Flag: Unprotected edges (S7.05) account for 58% of falls.
8. Records & Follow-Up (S12–S19)
Important Processes:
- Corrective actions: Track fixes in CAR/NCR registers (S13–S16)
- Communication logs: Document contractor convos (S18)
- Photo evidence: Timestamped, referenced to items (S19)
🔧 Action Step: Use S19 photos to create a visual audit trail for disputes.
4. Conducting Your Inspections: A Proactive Approach
Using the C20 checklist isn’t difficult, but a little structure goes a long way. Here’s how to approach each inspection to get the most out of it—and actually improve safety, quality, and communication onsite.
How to Implement the C20 Checklist for Maximum Impact
Step 1: Pre-Inspection Planning
What to Do:
- Schedule inspections periodically during construction, at least at three phases:
- Early works (post-slab pour, before major construction)
- Mid-construction (after framing/roof on (around the frame inspection stage), before internal fit-out)
- Pre-handover (final review before practical completion)
- Assign roles: Designate a Site Manager (for S1–S3, S12–S19) and trade specialists (e.g., electrician for S4).
Why It Matters:
- Aligns with WHS Regulation 299 (requiring regular inspections).
- Prevents "catch-up" audits that miss evolving risks.
Step 2: Onsite Execution
Follow This Process:
- Physical Walkthrough:
- Start at S1 (Site Management) and proceed sequentially to S19 (Photos).
- Use the checklist’s TODO/DONE/ISSUE flags for real-time tracking.
- Document Everything:
- Photos: Capture each item (e.g., "S4.02 – Frayed cord at northwest corner").
- Notes: Record conversations (e.g., "S5.01 – Subcontractor advised to replace cracked helmet by EOD").
⚠️ Important Tip: "Never skip S3 (Documentation). A missing SWMS (S3.12) can stop work instantly during audits.
Step 3: Issue Resolution
For Non-Compliances:
- Minor Issues (e.g., S8.06 – Poor lighting):
- Address verbally with contractors; note in S18 (Communication Register).
- Major Risks (e.g., S4.05 – Faulty RCD):
- Issue a HNC (S15) or NCR (S16) with:
- Clear description (reference checklist item).
- Deadline for resolution (e.g., "S11.03 – Trench shoring required within 24hrs").
- Issue a HNC (S15) or NCR (S16) with:
🔧 Pro Move:
"Attach photos to HNC/NCR reports. Visual evidence speeds up fixes."
Step 4: Follow-Up & Closure
Close the Loop:
- Re-inspect flagged items within 48 hours (use S13 Corrective Actions).
- Update registers:
- S17 (Risk Register): For recurring issues.
- S19 (Photos): Add "after" images of resolved items.
- File records: Store completed checklists digitally for 7+ years (per WHS Act).
Step 5: File and Review
Keep copies of every inspection (digitally or in a project folder). These become part of your site safety record that you should review monthly safety meeting.
Are you seeing the same problems again and again? That’s a sign you may need to adjust your processes or have a broader conversation with your builder or site team.
Periodic inspections aren’t just about checking boxes—they’re a simple but powerful way to stay informed, keep people accountable, and steer your build in the right direction.
Common Mistakes to Avoid During Inspections
Even with the best intentions, it's easy to overlook important aspects during construction inspections. Being aware of common pitfalls can help ensure that inspections are thorough and effective.
1. Treating Photos (S19) as Optional
The Risk:
- Without timestamped images linked to checklist items (e.g., "S1.03 – Sediment on kerb"), you lose evidence for disputes or audits.
The Fix:
- Assign a "Photo Manager" to:
- Label images with checklist codes (e.g., S4.05-RCD-test-14May24.jpg).
- Upload to shared drives with inspection dates.
Regulatory Basis:
- WHS Act Section 274 requires records proving due diligence.
2. Skipping Documentation Reviews (S3)
The Risk:
- Expired SWMS (S3.12) or missing White Cards (S3.09) trigger immediate work stoppages during audits.
The Fix:
- Implement a "Docs Expiry Tracker" with:
- Monthly reminders for SWMS renewals.
- Onsite digital folders for instant access.
Real Impact:
- A Melbourne site faced $8K fines for outdated MSDS (S3.11).
3. Rushing High-Risk Areas (S4, S7, S11)
The Risk:
- Superficial checks of electrical systems (S4) or scaffolding (S11.10) miss latent hazards.
The Fix:
- Use the "3-Point Verification" method:
- Visual check (e.g., S4.02 – no frayed cords).
- Functional test (e.g., S4.05 – RCD test button).
- Trade sign-off (electrician initials for S4).
4. Ignoring Recurring Issues (S17 Risk Register)
The Risk:
- If S5 PPE violations keep appearing, your systems—not just workers—may be flawed.
The Fix:
- Quarterly "Pattern Reviews" to:
- Identify top 3 recurring items (e.g., S6.05 – kerb sediment).
- Update training or procurement (e.g., buy better silt fences).
Data Point:
- Sites analyzing S17 data reduce repeat issues by 40%.
5. Poor Communication with Contractors
Not effectively communicating inspection findings can lead to repeated mistakes and unresolved issues. Better communication by:
- Discussing findings with contractors immediately after inspections. or at pre-defined stage gate meetings (weekly, fortnightly).
- Providing written reports outlining issues and recommended actions.
- Setting clear expectations for issue resolution timelines.
Example: Poor Follow-Up (S13-S16)
The Risk:
- Unclosed corrective actions (S13) erode contractor accountability.
The Fix:
- The "24/48 Rule":
- Minor fixes: Verify within 24 hours.
- Major risks: Escalate to NCR (S16) with 48-hour deadlines.
Identifying issues without ensuring they're resolved undermines the inspection process. Ensure accountability by:
- Scheduling follow-up inspections to verify that corrective actions (CAR) have been taken.
- Documenting the resolution of previously identified issues.
Conclusion
Let’s be honest—constructing a home isn’t just stacking materials. It’s a precision process where documentation, trades, and timelines intersect. And like any complex process, consistency is key.
The C20 Periodic Safety Inspection Checklist is your systematic safeguard:
- Eliminates guesswork with clear, repeatable checks (from S1 sediment fences to S19 photo logs).
- Protects your priorities—investment, timeline, and worker safety—without micromanaging builders.
- Turns compliance into confidence (because "hope" isn’t a WHS-approved strategy).
Here’s Your Power Move:
- Download the C20 Checklist and annotate it for your project’s risks.
- Schedule inspections at 3 important phases (early/mid/handover).
- Lead with questions, not assumptions. (Even simple checks like S5 PPE or S3 SWMS prevent 80% of common issues.)
A final note: the soundtrack of Safety
Here’s one song you don’t want stuck in your head:
FAQs
- How often should I conduct a periodic safety inspection during construction?
- A minimum of three inspections is recommended during the project duration. Longer duration projects require more inspections.
- Who should perform these inspections?
- Ideally, your construction supervisor or an accredited WHS Officer.
- What should I do if I identify issues during an inspection?
- Immediately notify your contractor, either verbally or formally documented.
- Are these inspections mandatory by law in Australia?
- Yes, Australian WH&S laws require effective monitoring and inspections for construction projects.
- Can inspections prevent all accidents?
- No inspection can eliminate all risks, but consistent checks greatly reduce likelihood and severity.
- What is a SWMS and why is it important?
- Safe Work Method Statements (SWMS) detail risks and safety practices for high-risk tasks and are legally required.
- What should I do if my builder refuses to conduct inspections?
- Consider this a major red flag. Engage an independent inspector immediately.
- Why do I need photos during inspections?
- Photos provide clear evidence for records, reporting, and future reference.
- What is PPE and who provides it?
- Personal Protective Equipment; typically provided by employers/contractors for worker safety.
- How long should I keep inspection records?
- Australian regulations typically require retaining records for at least 7 years.
- My concretor refuses to put boots on what should I do?
- Start by asking them for their Safe Work Method Statement (SWMS) or Job Safety Analysis (JSA). If they’ve genuinely assessed the risks and decided that thongs are the best choice for power floating a slab (yes, seriously), and it’s documented in their risk assessment, then that’s them taking responsibility for their work environment and method of work. But—if they don’t have an SWMS or JSA on file, then you’ve got a problem. Raise it as a risk or safety issue, and issue a Corrective Action Request (CAR) to the trade. That puts them formally on notice to fix the situation. Personally, I like my toes where they are—they help me balance. Just saying.
Further Reading
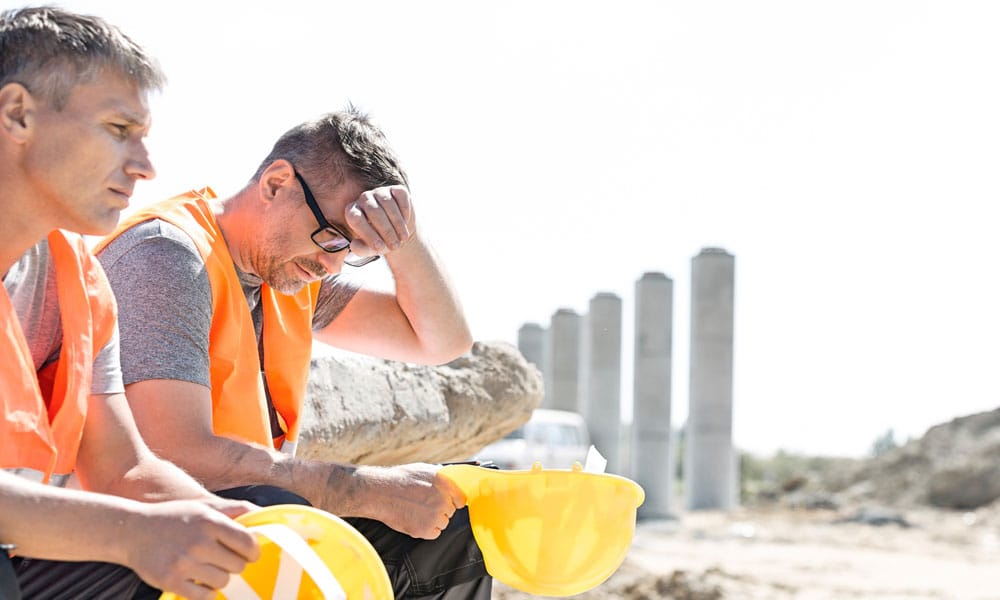