Introduction
In Australia’s slowly evolving housing market, one of the most pressing challenges is meeting the growing demand for quality homes. With a national target to construct 1.2 million new homes in the next five years, traditional construction methods alone may not work. This is where prefabricated and modular construction is stepping up, offering a faster, more efficient, and cost-effective way to build homes.
But what exactly are prefabricated and modular construction methods? And how can they benefit prospective homeowners?
In this post, we’ll look into these modern methods of construction (MMC), guided by insights from the Australian Building Codes Board’s Prefabricated, Modular, and Offsite Construction Handbook.
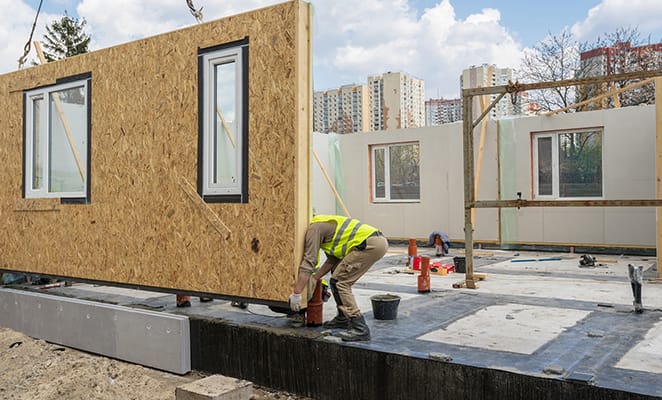
What is Prefabricated and Modular Construction?
Prefabricated and modular construction are modern approaches that challenge the traditional way of building homes. They leverage advanced manufacturing techniques and offsite production to deliver high-quality, efficient building solutions. But what do these terms mean in practice?
Prefabricated Construction Prefabrication refers to the process of manufacturing building components in a controlled factory environment before transporting them to the construction site for assembly. Think of it as building with giant LEGO blocks—pieces like walls, floors, and roofs are prepared in advance, ensuring precision and consistency.
Modular Construction Modular construction takes prefabrication a step further. Here, entire sections—or modules—of a building are manufactured offsite. These modules are fully constructed with interior finishes, plumbing, and electrical systems in place. Once transported to the site, they are joined together to create a complete structure, ready for immediate use.
How It Differs from Traditional Construction In traditional construction, all processes happen onsite, from laying the foundation to putting up walls and roofing. This method often involves delays caused by weather, supply chain issues, or workforce availability. Prefabrication and modular methods minimise these risks by shifting much of the work to an indoor, controlled environment, making the process more predictable and efficient.
Examples of Modern Methods of Construction (MMC) Some popular applications of prefabrication and modular construction include:
- Volumetric Construction: Fully built sections, such as entire rooms or apartments, are transported to the site and assembled like building blocks.
- Precast Concrete Components: Structural elements like beams, panels, or columns are pre-made and used in various building types.
- Structural Insulated Panels (SIPs): Panels with a foam core sandwiched between durable outer layers, offering excellent insulation and structural support.
- Bathroom Pods: Pre-assembled bathrooms that arrive onsite fully equipped and ready for connection.
Why Prefabrication Matters in Australia
Australia faces a housing challenge of unprecedented scale. With a national target of building 1.2 million homes over the next five years, the construction industry is under immense pressure to deliver quickly, efficiently, and sustainably. Prefabrication and modular construction methods offer a promising solution to meet this demand while addressing key issues in the current residential construction landscape.
Tackling the Housing Supply Shortfall
The Australian Building Codes Board (ABCB) and government ministers have identified prefabricated and modular construction as pivotal in addressing the country's housing needs. By manufacturing components offsite, these methods can dramatically reduce construction timelines, enabling builders to complete projects faster. In an environment of high demand and skilled labour shortages, speed is critical to getting homes on the market.
Improved Cost Efficiency
Traditional construction often suffers from inefficiencies, including material waste, weather-related delays, and supply chain disruptions. Prefabrication reduces these issues by creating components in a controlled factory environment, where precision is prioritised, and waste is minimised. As a result, homeowners and builders can benefit from significant cost savings without sacrificing quality.
Consistency and Quality Control
In traditional construction, onsite variability can lead to inconsistencies in workmanship and quality. Prefabricated and modular methods offer a higher level of quality control since components are manufactured under strict factory conditions. This ensures that every element meets rigorous standards before it ever reaches the construction site.
Sustainability Benefits
Prefabricated and modular construction aligns with Australia’s growing focus on sustainability. These methods produce less waste and can utilise energy-efficient materials and designs, resulting in homes that are not only quicker and cheaper to build but also more environmentally friendly.
Adapting to Australia's Unique Conditions
Australia's diverse climate and geographical challenges make prefabrication particularly advantageous. Modular components can be tailored to meet specific requirements, such as bushfire resilience or energy efficiency, ensuring that homes are built to withstand local conditions while complying with the National Construction Code (NCC).
Prefabrication is more than just an alternative to traditional construction—in the current marketplace conditions, it’s an approach that can reshape the housing market.
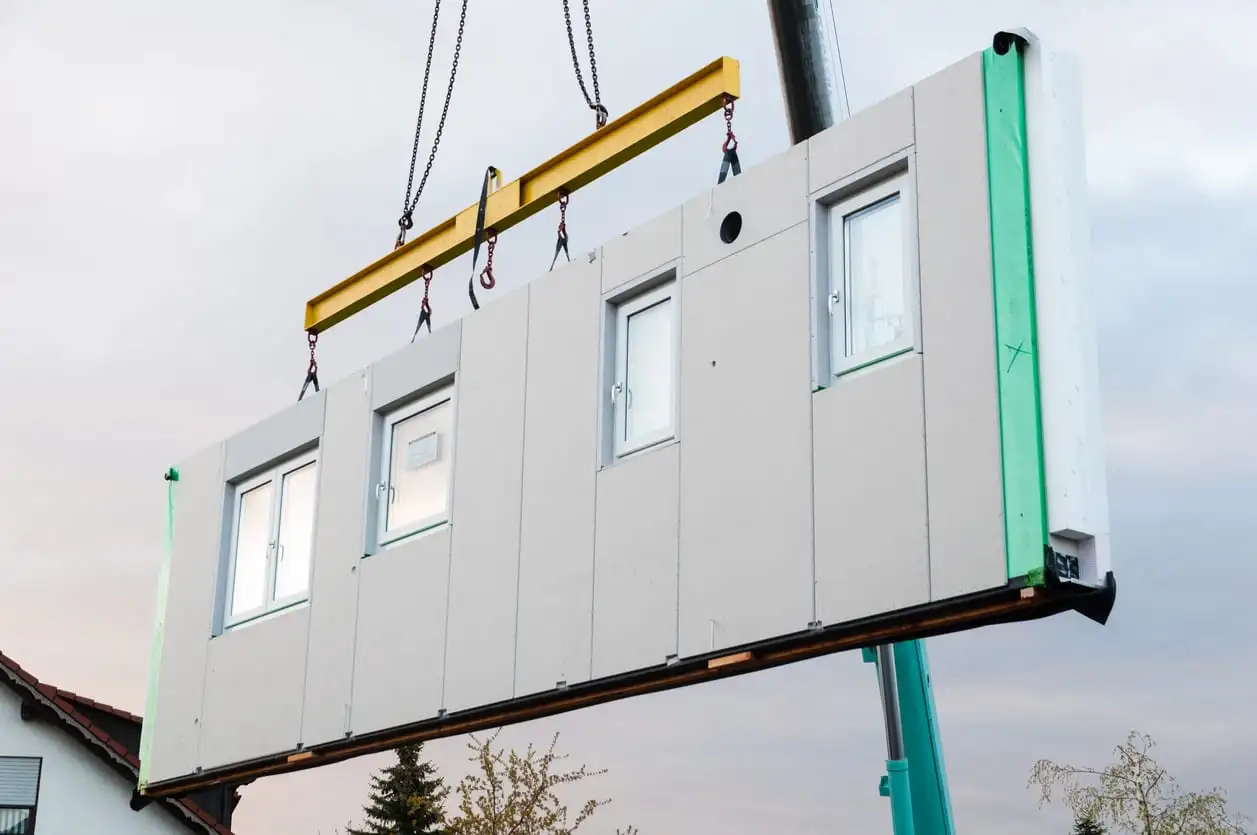
The Role of the NCC and Compliance
Building a home in Australia is not just about laying bricks and mortar—it’s about adhering to stringent regulations that ensure the safety, quality, and durability of every structure. For prefabricated and modular construction, the National Construction Code (NCC) plays a vital role in maintaining these standards.
What is the NCC?
The NCC is Australia’s primary technical standard for the design and construction of buildings. It sets out the minimum performance requirements that all structures must meet, covering areas such as safety, health, accessibility, energy efficiency, and sustainability. Prefabricated and modular construction must meet these same requirements, whether components are built onsite or offsite.
Key Compliance Pathways
The NCC provides three pathways to demonstrate compliance:
- Deemed-to-Satisfy (DTS) Solutions: These are prescriptive requirements that, when followed, automatically ensure compliance. For instance, a prefabricated wall that meets specific NCC standards for fire resistance and insulation qualifies under DTS provisions.
- Performance Solutions: These allow for innovative designs or materials that deviate from DTS requirements but still meet the NCC’s performance criteria. For example, a modular home using advanced insulation materials could use a Performance Solution to demonstrate compliance with energy efficiency standards.
- Combination of DTS and Performance Solutions: Many projects use a mix of both pathways, where certain elements follow prescriptive rules, while others rely on performance-based assessments.
The 4-Step Compliance Framework
Prefabricated and modular construction often requires careful documentation to prove compliance. The NCC outlines a 4-step approach to ensure that components and systems are fit for purpose:
- Identify Relevant Requirements: Determine the specific NCC provisions applicable to the prefabricated component or system, such as fire resistance or structural integrity.
- Provide Evidence of Suitability: Submit certificates, test reports, or engineering calculations to demonstrate that the product meets the relevant NCC standards.
- Assess Risk and Documentation Needs: For complex systems, more rigorous documentation (e.g., CodeMark certificates) may be required to address higher risks.
- Ensure Proper Construction and Installation: Verify that all components are installed according to manufacturer guidelines and comply with the NCC.
Prefabrication’s Unique Compliance Challenges
Prefabricated and modular construction introduces distinct challenges, such as:
- Transport and Handling Risks: Ensuring components are not damaged in transit and remain compliant upon delivery.
- Interface Management: Seamlessly connecting modular components with onsite elements while maintaining compliance with structural and safety standards.
- Site-Specific Factors: Accounting for variations in soil type, bushfire risk, and climate zone when assembling modular homes.
How the NCC Supports Innovation
One of the NCC’s strengths is its flexibility. It encourages innovation by allowing builders to use Performance Solutions to adopt modern methods of construction (MMC) while maintaining compliance. For example, volumetric modules or advanced materials like structural insulated panels (SIPs) can be incorporated into projects with proper documentation and oversight.
By understanding and navigating the NCC, homeowners and builders can ensure that prefabricated and modular homes meet Australia’s high standards for safety, quality, and performance. In the next section, we’ll break down technical terms into plain English, making this topic more accessible for everyone.
Technical Terms Explained in Plain English
The world of prefabricated and modular construction is filled with technical jargon that can feel overwhelming to homeowners unfamiliar with the industry. Let’s break down some of the key terms from the Prefabricated, Modular, and Offsite Construction Handbook into simple, easy-to-understand language.
Prefabrication
This is the process of building components in a factory instead of onsite. For example, a wall or floor section is made in a controlled environment, ensuring quality and precision, before being transported to the construction site.
Modular Construction
This refers to creating entire sections—or modules—of a building in a factory. These modules are fully finished, with walls, floors, plumbing, and electrical systems in place. They’re then transported and assembled onsite, forming a complete structure.
Volumetric Construction
A subset of modular construction, volumetric construction involves manufacturing three-dimensional modules, such as entire rooms or apartments. These are delivered to the site as near-complete units, ready for assembly.
Deemed-to-Satisfy (DTS) Solutions
This compliance pathway means following specific rules outlined in the National Construction Code (NCC). For example, using materials with pre-approved fire resistance ratings is a DTS Solution.
Performance Solutions
When innovative designs or materials don’t fit neatly into the NCC’s prescriptive rules, they can be assessed on their ability to meet the performance standards required. This allows for greater flexibility and creativity in construction.
Structural Insulated Panels (SIPs)
SIPs are sandwich-like panels with a core of insulating material (like foam) between two layers of durable material. They’re lightweight, strong, and provide excellent thermal insulation, making them ideal for energy-efficient homes.
Evidence of Suitability
This refers to the documentation needed to prove that a material, product, or construction method complies with the NCC. It can include certificates, engineering calculations, and test reports.
Bushfire Construction Requirements
If your home is in a bushfire-prone area, it must meet specific standards for fire resistance, including materials and designs that reduce the risk of ignition. For example, metal roof sheets and ember guards are common features.
Composite Wall Panels
These are prefabricated panels that combine multiple layers, such as structural elements, insulation, and cladding. They’re used to build walls more efficiently while meeting energy efficiency and safety standards.
Additive Manufacturing
Also known as 3D printing, this method involves building components layer by layer using materials like plastics or cement. It’s a modern, innovative approach to creating custom parts for homes.
CodeMark Certificate
This is a government-backed certification that proves a product or system meets Australian standards, including the NCC. It’s often used for complex prefabricated systems like modular bathrooms or wall panels.
Benefits of Prefabricated and Modular Construction
Prefabricated and modular construction isn’t just about new technology—it’s about transforming how homes are built to be faster, more efficient, and higher in quality. For Australian homeowners, these methods offer numerous advantages that make them an appealing option for residential construction.
1. Faster Construction Timelines
One of the standout benefits of prefabrication is speed. By manufacturing components in a factory, the time spent building onsite is significantly reduced. For example:
- Modules can be produced simultaneously while site preparation is underway.
- Weather delays are minimised since most work happens in controlled environments. This means your new home can be move-in ready much sooner compared to traditional methods.
2. Cost Savings Through Efficiency
Prefabricated construction eliminates many inefficiencies commonly associated with traditional building. Here’s how:
- Reduced Waste: Factory settings allow for precise material usage, minimising excess.
- Streamlined Labour: Workers specialise in specific tasks, increasing productivity and reducing labour costs.
- Predictable Budgets: Standardised production reduces unexpected expenses caused by delays or material shortages.
3. Consistent Quality Control
In traditional construction, quality can vary due to weather conditions, skill levels, and onsite management. Prefabrication addresses this by:
- Building components under strict factory controls.
- Using advanced machinery to ensure precision.
- Conducting quality checks before components leave the factory.
For homeowners, this means fewer defects, reduced maintenance, and a better-built home.
4. Improved Sustainability
Sustainability is increasingly important in residential construction, and prefabrication delivers on this front. Key environmental benefits include:
- Lower Carbon Footprint: Factories are often more energy-efficient than onsite construction.
- Recyclable Materials: Many modular components are designed for reuse or recycling.
- Energy-Efficient Homes: Prefabricated materials often incorporate advanced insulation and sustainable design elements, reducing energy costs for homeowners.
5. Design Flexibility and Customisation
Gone are the days when prefabricated homes meant cookie-cutter designs. Modern methods allow for:
- Custom floor plans tailored to individual preferences.
- A variety of materials, finishes, and features to suit different aesthetics.
- Integration of energy-efficient technologies like solar panels and double-glazed windows.
6. Adaptability to Australian Conditions
Prefabricated and modular construction is well-suited to Australia’s unique environment:
- Homes can be designed to withstand bushfire risks, cyclonic conditions, or coastal corrosion.
- Energy efficiency standards are easier to meet with modern prefabricated materials.
- Modular systems can be tailored to specific climate zones, ensuring comfortable living year-round.
7. Reduced Construction Noise and Disruption
For projects in established neighbourhoods, prefabrication offers a quieter and less disruptive alternative. With much of the construction happening offsite, neighbours experience less noise, dust, and disturbance during the building process.
8. Long-Term Durability
Prefabricated components are engineered to meet more precise standards, often exceeding those of traditional construction. This results in homes that are built to last, giving homeowners peace of mind about the durability of their investment.
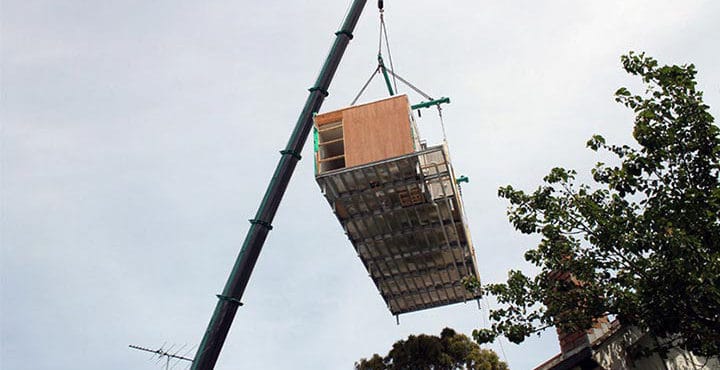
Potential Challenges and How to Address Them
While prefabricated and modular construction offers numerous benefits, it’s not without challenges. However, understanding these potential obstacles and planning for them can ensure a smooth building process and a high-quality outcome.
1. Transport and Handling Risks
Prefabricated components are often large and require careful transportation to the construction site. Challenges include:
- Damage During Transit: Modules may be exposed to vibrations, moisture, or physical impacts.
- Complex Logistics: Transporting oversized loads may require special permits and planning.
How to Address It:
- Ensure components are securely packaged and protected against environmental factors.
- Work with experienced transporters familiar with moving modular structures.
- Inspect all modules upon arrival for damage before installation.
2. Site Preparation and Compatibility
Proper site preparation is critical to ensure prefabricated components fit seamlessly. Common issues include:
- Dimensional Incompatibilities: Prefabricated elements may not align perfectly with onsite foundations or existing structures.
- Environmental Factors: Soil conditions, uneven terrain, or adverse weather can complicate installation.
How to Address It:
- Engage an engineer to assess site conditions and prepare detailed foundation plans.
- Use adjustable systems or temporary supports to align prefabricated components accurately.
- Plan for on-the-ground modifications if needed, while ensuring compliance with the NCC.
3. Interface and Connection Challenges
Prefabricated systems must connect seamlessly with onsite elements, such as plumbing, electrical systems, and other modules. Issues can arise at these interfaces, leading to:
- Misalignment: Gaps between components can affect structural integrity or insulation.
- System Failures: Poorly connected utilities may cause functionality issues.
How to Address It:
- Use detailed design coordination to anticipate interface requirements.
- Conduct rigorous quality checks at connection points during installation.
- Collaborate with licensed tradespeople to ensure plumbing and electrical connections meet Australian standards.
4. Regulatory and Compliance Complexities
Navigating the NCC and other regulations can be daunting, especially for innovative methods like modular construction. Builders must ensure:
- Appropriate Certification: Products and methods comply with NCC provisions.
- Site-Specific Adjustments: Local conditions, such as bushfire zones or flood risks, may require additional compliance measures.
How to Address It:
- Engage NCC consultants early in the project to identify all applicable requirements.
- Use CodeMark-certified products to simplify the compliance process.
- Maintain detailed documentation to demonstrate evidence of suitability.
5. Workforce Familiarity
Prefabrication and modular construction often require different skills and workflows compared to traditional methods. Challenges include:
- Learning Curve: Tradespeople and site supervisors may need training to handle modular components.
- Coordination Issues: Seamlessly integrating factory-built components with onsite work can be tricky.
How to Address It:
- Provide training for workers on handling and assembling prefabricated systems.
- Use experienced supervisors to oversee the interface between offsite and onsite construction.
- Implement a clear communication plan to keep all teams aligned.
6. Public Perception
Some homeowners may perceive prefabricated homes as lower quality compared to traditionally built houses. This misconception can affect market acceptance.
How to Address It:
- Highlight the consistent quality control and innovative designs achievable through prefabrication.
- Showcase examples of high-quality, custom modular homes.
- Educate buyers about the sustainability and efficiency benefits of these methods.
7. Cost of Initial Investment
Although prefabrication saves costs in the long term, the upfront investment in specialised factory facilities, transport, and modular designs can be higher.
How to Address It:
- Focus on lifecycle savings, such as reduced waste, faster timelines, and lower energy costs.
- Explore government incentives or grants for sustainable building methods.
- Work with builders who can optimise the design to balance cost and efficiency.
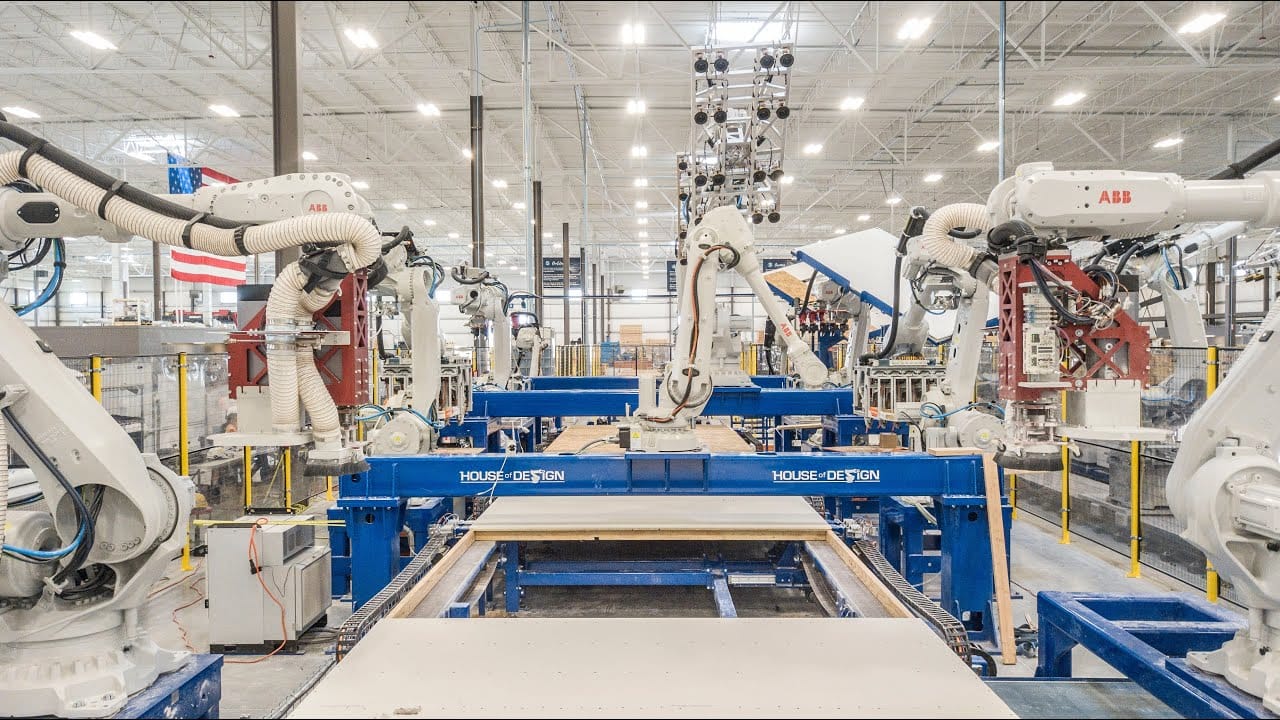
Prefabrication’s Impact on Time, Cost, and Quality
Prefabricated and modular construction isn’t just about new methods—it’s about redefining what’s possible in residential building. These techniques significantly influence the three key pillars of construction: time, cost, and quality, offering a compelling alternative to traditional methods.
1. Faster Construction Timelines
The time savings offered by prefabrication are unmatched in the industry. By manufacturing components offsite in a controlled environment, builders can overlap production and onsite preparation tasks, reducing the overall project timeline. For instance:
- Foundations can be prepared while modules are being built in the factory.
- Weather delays, a common issue in traditional construction, are largely eliminated.
- Assembly onsite takes days or weeks instead of months, making the process much faster.
Example: A modular home that might take nine months to build using traditional methods could be completed in as little as four months with prefabrication.
2. Cost Efficiency
While prefabrication might involve higher upfront costs, the long-term savings can be substantial. Key cost benefits include:
- Reduced Material Waste: Factories use precise measurements, minimising leftover materials.
- Lower Labour Costs: Factory environments optimise labour efficiency, reducing the need for large onsite teams.
- Fewer Delays: Predictable timelines eliminate unexpected expenses caused by delays or rework.
Additionally, predictable costs offer homeowners greater peace of mind, as they are less likely to encounter budget overruns.
3. Superior Quality Control
Prefabricated components are manufactured in a controlled environment, which significantly reduces the likelihood of defects. Features that enhance quality include:
- Advanced machinery ensuring precision in every component.
- Rigorous inspections at multiple stages of the production process.
- Consistent compliance with the National Construction Code (NCC).
For homeowners, this translates to fewer defects, reduced maintenance costs, and improved long-term performance.
5. Sustainability Advantages
Prefabrication also impacts sustainability, a growing concern for Australian homeowners. These methods produce homes that:
- Consume less energy during construction.
- Incorporate energy-efficient materials and systems, reducing energy costs.
- Align with Australia’s sustainability goals, particularly in reducing construction-related carbon footprints.
6. Long-Term Durability
Homes built using prefabrication are often more durable than those constructed using traditional methods. Factory-built components are designed to withstand transportation and installation stresses, ensuring they perform well over time. This leads to:
- Fewer repairs and replacements.
- Increased property value due to superior build quality.
Balancing the Pillars
While prefabrication excels in all three areas—time, cost, and quality—it’s important to strike a balance that meets the homeowner’s specific needs. For instance:
- A tight timeline might prioritise speed over extensive customisation.
- A focus on cost savings could influence the choice of materials or finishes.
- Premium quality and durability may involve a slightly higher initial investment.
Conclusion
We believe that prefabricated and modular construction represents a sound approach to meeting the needs of affordable and social housing in Australia. By addressing housing demand with faster timelines, cost-effective solutions, and high-quality builds, these methods are paving the way for a sustainable, efficient future in residential construction.
The challenge is for this methods to be embraced and funded!
FAQs
To wrap up, here are answers to some of the most common questions about prefabricated and modular construction. These insights aim to provide clarity and address any lingering concerns.
1. What is prefabricated construction?
Prefabricated construction involves manufacturing building components, like walls or roofs, in a controlled factory environment before transporting them to the site for assembly. This method ensures precision, consistency, and reduced construction timelines.
2. How does modular construction differ from traditional methods?
Modular construction is a subset of prefabrication where entire sections (or modules) of a building, such as rooms or floors, are built offsite. These modules are then transported and assembled onsite, drastically reducing the time and labour required compared to traditional methods.
3. What are the main benefits of prefabricated construction for homeowners?
Key benefits include:
- Faster construction times.
- Cost savings through reduced waste and improved efficiency.
- High-quality builds with fewer defects.
- Sustainability through energy-efficient designs and reduced material use.
4. Are modular homes more affordable than traditional homes?
While upfront costs may be comparable or slightly higher, modular homes save money in the long run through lower labour costs, less material waste, and energy efficiency. Additionally, faster construction reduces financing costs.
5. Can prefabricated homes be customised?
Yes! Modern prefabrication methods offer significant design flexibility. Homeowners can choose custom layouts, materials, finishes, and features to create a home that suits their lifestyle and preferences.
6. Are prefabricated homes durable?
Prefabricated homes are built to stringent standards and often exceed the quality of traditional homes. Factory production ensures precision, and components are designed to withstand transportation and installation stresses, making them highly durable.
7. How does prefabrication contribute to sustainability?
Prefabricated construction produces less waste, uses energy-efficient materials, and often includes designs that lower energy consumption. This aligns with Australia’s sustainability goals and reduces the carbon footprint of building homes.
8. What should I know about site preparation for modular homes?
Proper site preparation is crucial for modular homes. Foundations must align with the prefabricated components, and factors like soil conditions, site access, and local compliance requirements should be considered. Working with experienced professionals ensures a smooth process.
9. Are there any challenges with modular construction?
Potential challenges include transport logistics, site compatibility, and compliance with regulations. However, these can be addressed with careful planning, quality control, and collaboration with experienced builders.
10. How do prefabricated homes comply with the National Construction Code (NCC)?
Prefabricated homes must meet the same NCC standards as traditional builds. Compliance can be demonstrated through Deemed-to-Satisfy (DTS) solutions or Performance Solutions, with documentation to prove suitability.
Further Reading
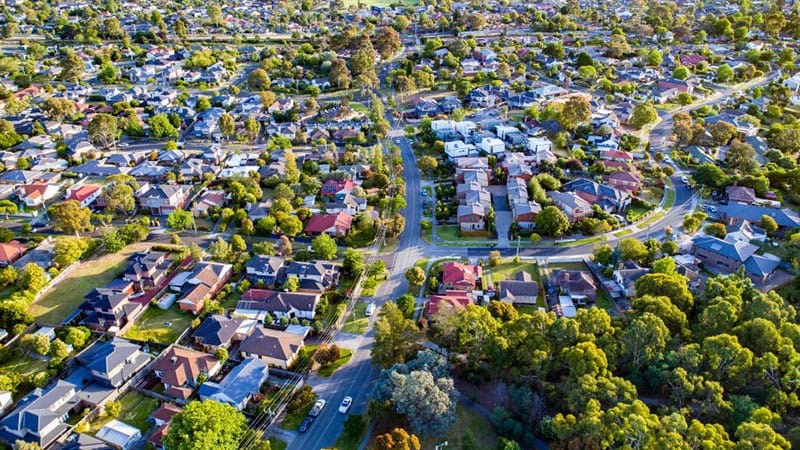
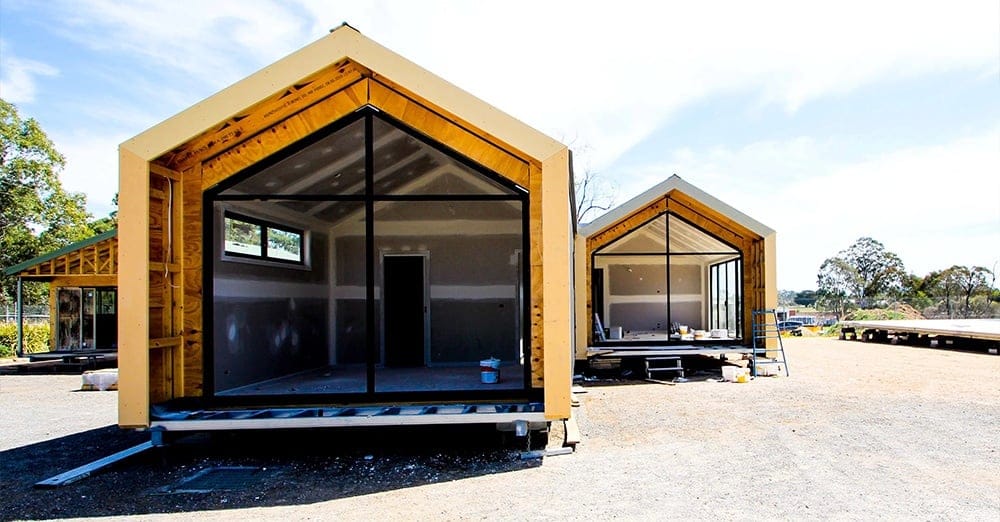