Take The Quiz On This Post
Read the post, then take the quiz—test your knowledge and see what you’ve learned!
Introduction
Insulation is one of the most important elements in building a comfortable and energy-efficient home. It plays a major role in reducing heating and cooling costs by acting as a barrier to heat flow—keeping your home warm during the winter and cool during the summer.
A well-insulated home not only saves energy but also contributes significantly to reducing greenhouse gas emissions, making it an essential aspect of sustainable living.
For many Australian homeowners, understanding insulation can be challenging, especially when it comes to choosing the right materials and ensuring proper installation. With a variety of insulation types available and different climate considerations to factor in, selecting the best solution for your home can feel overwhelming.
This guide will cover everything you need to know about insulation, including the different types of materials available, how insulation is rated, and how to ensure it's installed correctly.
We will also discuss the importance of design considerations like thermal bridging and provide a quality checklist to help you verify that your insulation meets Australian standards. Whether you are building a new home or retrofitting insulation in an existing one, this comprehensive guide aims to help you make informed decisions that will improve your home's comfort and efficiency for years to come.
What Is Insulation and Why Is It Important?
Definition and Function
Insulation is a material that acts as a barrier to heat flow, helping to maintain a comfortable indoor temperature regardless of the weather outside. During the winter months, insulation keeps heat inside your home, reducing the need for excessive heating.
In the summer, it prevents heat from entering, keeping your home cool without relying heavily on air conditioning.
There are different types of insulation that can serve multiple purposes. Apart from controlling temperature, insulation can also help with acoustic performance by reducing noise transfer between rooms, and it can manage moisture, preventing problems like condensation and mould.
It underscores the importance of conducting mould risk assessments for every new home. Simply relying on "the way we’ve always done it" no longer meets the health, safety, and livability standards required for modern dwellings.
And yes, I do rant about this—because no one else seems to be talking about it, despite the fact that it’s costing the country billions in health expenses!
Climate Considerations
The effectiveness of insulation largely depends on the climate and how the material is used in your home. For example, homes in tropical areas might need reflective insulation to resist radiant heat, while those in colder regions benefit more from bulk insulation that traps air and minimises heat loss. Understanding your local climate is the first step towards determining the most suitable type of insulation for your home.
Additionally, insulation works best when combined with other passive design elements, such as appropriate shading, natural ventilation, and the strategic placement of windows and doors. Improper design can lead to unintended issues—like the "oven effect"—where the insulation traps heat inside the home, making it uncomfortably hot during the summer.
A well-balanced design considers both the insulation material and the architectural elements to ensure your home remains comfortable year-round. If your interested in this topic, check out our other post on control layers (link below).
Why Insulation is Important
A well-insulated home provides year-round comfort, significantly reducing energy bills for heating and cooling, which is particularly valuable in a country like Australia, where temperatures can vary dramatically. By cutting down on energy consumption, insulation also plays a vital role in reducing greenhouse gas emissions, making it an environmentally friendly choice for home owners.
Studies have shown that homes without proper insulation experience up to 25-35% heat loss through walls, ceilings, and floors. Adding insulation to these key areas can drastically reduce these losses, leading to significant energy savings and a more comfortable indoor environment. Furthermore, a properly insulated home ensures that the heating and cooling systems do not have to work as hard, which can extend the lifespan of these systems and reduce maintenance costs over time.
Make sure the batt thickness suits your wall frame thickness! i.e. 70mm wall frame uses less than 70mm thick batts or your wall linings can pop off!
Understanding R-Values: Performance and Application
What Is an R-Value?
An R-value is a measure of how well an insulation material resists heat flow. The higher the R-value, the better the material is at insulating your home. Essentially, R-values indicate the thermal resistance of the insulation product—meaning its ability to prevent heat from passing through it. The right R-value for your home will depend on several factors, including your local climate, the type of construction, and whether additional heating or cooling systems are installed.
It is important for home owners to understand that R-values are important when assessing the efficiency of an insulation product. However, it's not just about choosing a product with a high R-value; the effectiveness of insulation also depends on proper installation, the location of the material, and other building factors that can impact performance.
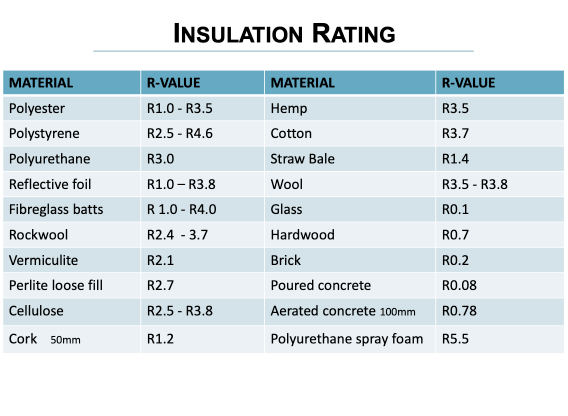
Material vs. Total R-Value
There are two main types of R-values to consider: material R-value and total R-value. The material R-value refers to the insulating capacity of the product alone. This value tells you how well a particular type of insulation—such as fibreglass batts, polystyrene, or reflective foil—will resist heat flow. The National Construction Code (NCC) and BASIX in New South Wales set out the minimum material R-values for the insulation products used in residential buildings. However, it is generally recommended to exceed these minimum requirements for increased comfort and greater energy savings over the lifespan of your home.
The total R-value refers to the combined insulating effect of all the components that make up a part of your home's structure—such as the walls, floors, or ceilings. This includes the insulation, as well as the building materials used for the framing, plasterboard, roof sheeting, and any reflective barriers. The total R-value is a more accurate measure of how effective your insulation will be once installed within your home's building envelope, as it considers all elements that contribute to thermal resistance.
The direction of heat flow also affects the R-value, especially in roof and ceiling insulation. Total R-values can be expressed as "up" R-values or "down" R-values:
- "Up" R-values describe resistance to heat flow upwards, which is important in cold climates where heat rises out of the home (also called “winter” R-values).
- "Down" R-values describe resistance to heat flow downwards, essential in hot climates to prevent heat from entering the home (also called “summer” R-values).
How to Choose the Right R-Value
The appropriate R-value for your home will depend on the following factors:
- Climate: Different Australian regions have different temperature ranges and seasonal variations. For example, homes in tropical areas may prioritise reducing heat gain, while those in colder climates focus on minimising heat loss.
- Building Type: The type of construction used for your home—such as lightweight timber frame, brick veneer, or double brick—can influence the insulation's performance. For example, brick walls provide more thermal mass, which can enhance insulation performance when combined with appropriate materials.
- Building Regulations: The NCC provides guidelines for the minimum R-values required for residential buildings in different regions. However, exceeding these minimum standards can significantly improve comfort and reduce energy costs.
It is also important to remember that several factors can reduce the effectiveness of the R-value over time, including thermal bridging, compression of insulation, and dust buildup on reflective surfaces. Therefore, ensuring proper installation and addressing potential issues such as air gaps or thermal bridges is essential for maintaining the intended performance of the insulation.
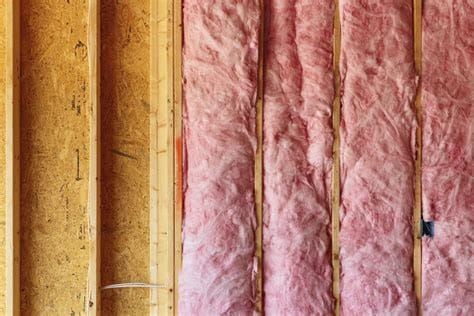
Types of Insulation Materials
Selecting the right insulation material for your home is important to achieve maximum comfort and energy efficiency. Insulation products can be broadly categorised into bulk insulation, reflective insulation, and composite insulation. Each type has distinct properties and is suitable for different applications, depending on your climate and the area of the home being insulated.
Bulk Insulation
Bulk insulation works by trapping pockets of air within its structure, which helps resist the transfer of conducted and convected heat. Bulk insulation is commonly used in Australian homes for walls, ceilings, and floors, as it provides consistent thermal resistance regardless of the direction of heat flow.
- Common Materials:
- Fibreglass Batts and Rolls: Made from spun glass fibres, fibreglass is a popular choice due to its cost-effectiveness, ease of installation, and fire resistance. Many fibreglass products also contain recycled glass, making them environmentally friendly.
- Wool Batts and Loose Fill: Wool insulation, often made from sheep's wool, offers excellent thermal and acoustic properties. It is a natural, sustainable option and provides good moisture management.
- Polyester Batts and Rolls: Polyester insulation is made from recycled plastic, such as PET bottles. It is non-irritant and easy to handle, making it a popular choice for DIY installation.
- Cellulose Fibre Loose Fill: Made from recycled paper, cellulose is treated for fire resistance and provides good thermal performance. It is typically used for ceilings and is blown into place to ensure coverage without gaps.
- Polystyrene (EPS and XPS) Rigid Boards: Expanded polystyrene (EPS) and extruded polystyrene (XPS) are used for insulating walls and floors. XPS has a higher R-value and better moisture resistance compared to EPS, making it suitable for damp areas.
- Polyisocyanurate (PIR) and Polyurethane (PUR) Rigid Boards: These foam boards offer high R-values for their thickness and are commonly used in roofs, walls, and floors where space is limited.
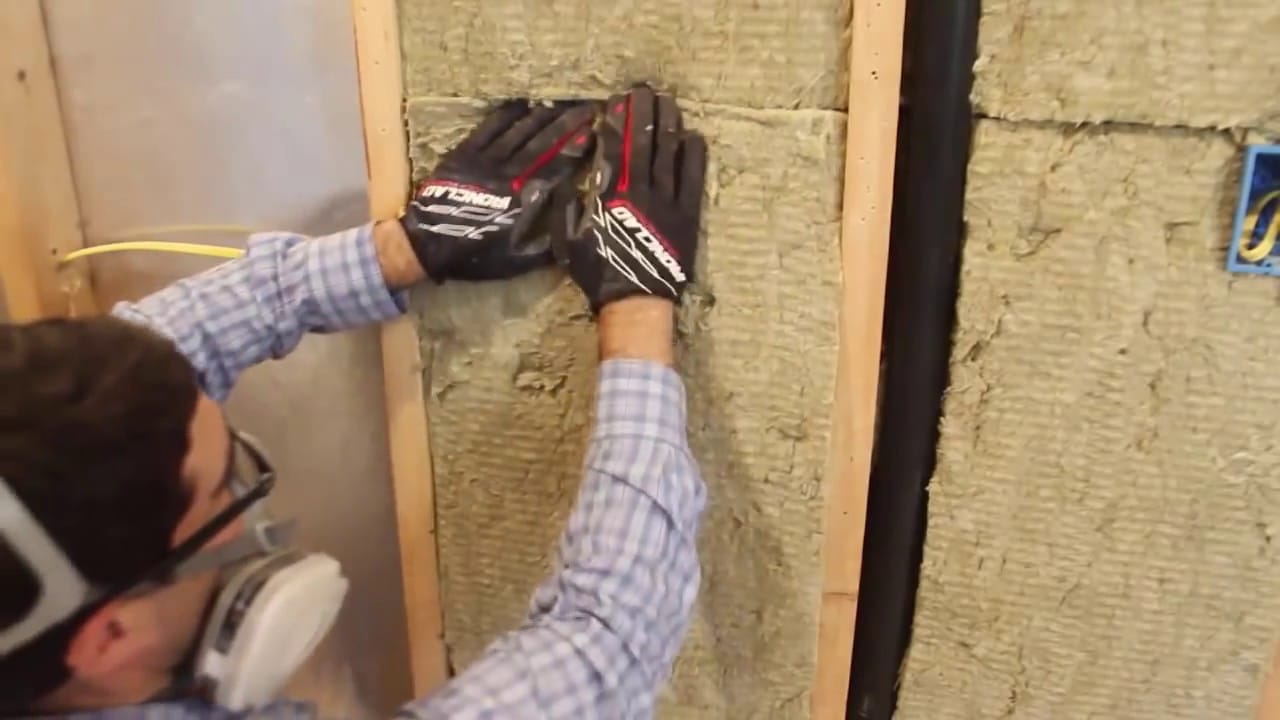
Reflective Insulation
Reflective insulation resists radiant heat by reflecting it away from the surface. It is usually made from shiny aluminium foil laminated onto paper or plastic and works best when installed with an adjacent air layer of at least 25mm. Reflective insulation is particularly effective in hot climates, where it helps to reduce heat gain from the sun.
- Common Forms:
- Reflective Foil Laminates (RFL): Available as sheets or concertina-type batts, reflective foil laminates are often installed under roofs or in walls to minimise heat transfer. They are especially useful in combination with bulk insulation to improve overall performance.
- Sarking: This type of reflective insulation is commonly used under metal or tiled roofs to reduce radiant heat and act as a moisture barrier. It also provides an additional layer of weatherproofing for the roof.
Reflective insulation can significantly reduce heat gain, but it requires careful installation. The shiny surface must be kept free from dust, and an air gap must be maintained to prevent the reflective properties from being compromised.
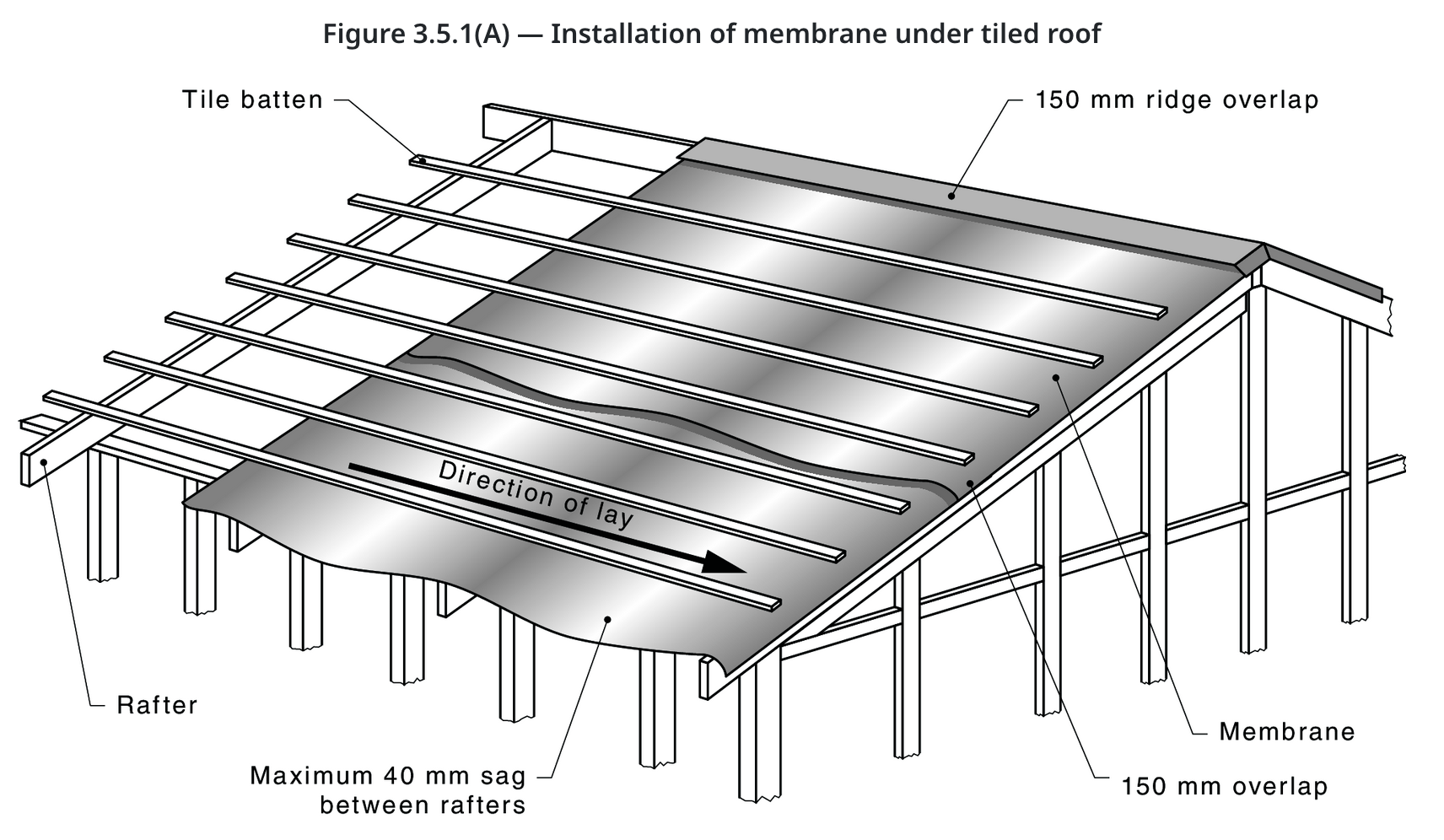
Composite Insulation
Composite insulation combines the properties of both bulk and reflective insulation to enhance performance. It is designed to provide the benefits of both types—thermal resistance from bulk insulation and radiant heat reflection from reflective surfaces.
- Examples of Composite Insulation:
- Foil-Faced Boards: These boards combine a bulk insulation core (such as PIR or EPS) with a reflective foil facing. The orientation of the foil needs careful consideration to ensure maximum efficiency and minimise condensation risks.
- Foil-Faced Blankets: Typically used in roof spaces, foil-faced blankets consist of a fibreglass or polyester core wrapped in reflective foil. They are effective at reducing both conducted and radiant heat transfer, making them ideal for use in a variety of climates.
- Foil-Backed Batts: These products combine traditional bulk insulation batts with a foil backing to increase their thermal performance. They are suitable for use in walls and ceilings, where both heat flow resistance and radiant heat reflection are beneficial.
When installing composite insulation, it is important to consider the orientation of the reflective layer. In cooler climates, the reflective foil should face inwards, while in hot, humid climates, it is better to have the foil facing outwards. This ensures that the insulation performs optimally and does not contribute to condensation issues.
Choosing the Right Insulation for Your Home
Choosing the right insulation for your home can make a significant difference in comfort, energy efficiency, and overall livability. To make the best choice, it is essential to consider your local climate, the type of construction used for your home, and any specific environmental factors that may impact performance. Below, we explore the key considerations that will help you choose the most suitable insulation.
Climate and Construction Considerations
The local climate is the most important factor when deciding on the type and level of insulation for your home. Australia's diverse climate zones mean that the insulation requirements for a home in Darwin are vastly different from those for a home in Melbourne.
- Hot and Humid Climates (e.g., Northern Australia): In these areas, reflective insulation is often the preferred choice because it effectively reduces heat gain by reflecting radiant heat. Bulk insulation can also be used to slow down the transfer of heat from the outside into the home.
- Cool and Temperate Climates (e.g., Southern Australia): Bulk insulation with high R-values is ideal for cooler climates, as it helps retain heat during winter. In these regions, a combination of bulk insulation in walls, floors, and ceilings, as well as reflective insulation in the roof, can provide the best performance.
- Mixed Climates (e.g., Sydney): In climates that experience both hot summers and cold winters, a combination of bulk and reflective insulation is recommended. This dual approach helps keep the home comfortable throughout the year by providing both heat resistance and radiant heat reflection.
The construction type of your home also affects the choice of insulation. For instance:
- Brick Veneer and Cavity Brick Homes: These homes have a cavity between the exterior brick wall and the interior framing, which can be filled with bulk insulation or rigid foam boards to enhance thermal performance.
- Weatherboard Homes: These typically require insulation batts in the wall cavity to provide sufficient resistance to heat flow, as the weatherboard alone has a low R-value.
- Timber Frame Homes: Insulation can be installed between the studs to provide effective thermal resistance. Additionally, installing insulation on the outside of the timber frame can reduce thermal bridging and improve overall performance.
Environmental Considerations
The environmental impact of insulation products is becoming an increasingly important factor for many home owners. When selecting insulation, consider both the environmental benefits during its use and its environmental footprint over its entire lifecycle.
- Recycled Content: Many insulation products, such as glass wool, polyester, and cellulose fibre, are made from a high percentage of recycled materials. For example, some brands of glass wool insulation contain up to 80% recycled glass, while polyester insulation is often made from recycled PET bottles.
- Recyclability: It is also important to consider how easily the insulation can be recycled at the end of its life. Materials like polyester and glass wool are more readily recyclable compared to other types, making them more environmentally friendly choices.
- Ecolabel Certifications: When comparing insulation products, look for ecolabel certifications such as Ecospecifier Global, Global GreenTag, Good Environmental Choice Australia (GECA), and the Australian National Life Cycle Inventory Database. These certifications provide information about the environmental performance of building products, helping you make an informed decision.
Maximising Insulation Effectiveness
Choosing the right insulation is only half the equation—ensuring it is installed correctly is just as important for maximising its effectiveness.
- Avoid Thermal Bridging: Thermal bridges are areas where heat can pass through more easily due to less insulation or conductive materials. Common thermal bridges include the building frame, window frames, and areas where insulation is compressed or missing. To reduce the effects of thermal bridging, consider adding rigid foam boards over framing elements or using thermal breaks in metal-framed homes.
- Proper Installation: Insulation must be installed according to the manufacturer’s specifications to achieve its intended R-value. Common installation mistakes, such as leaving gaps, compressing batts, or failing to maintain air gaps for reflective insulation, can significantly reduce performance. Hiring a professional installer ensures that your insulation meets Australian standards and performs as expected.
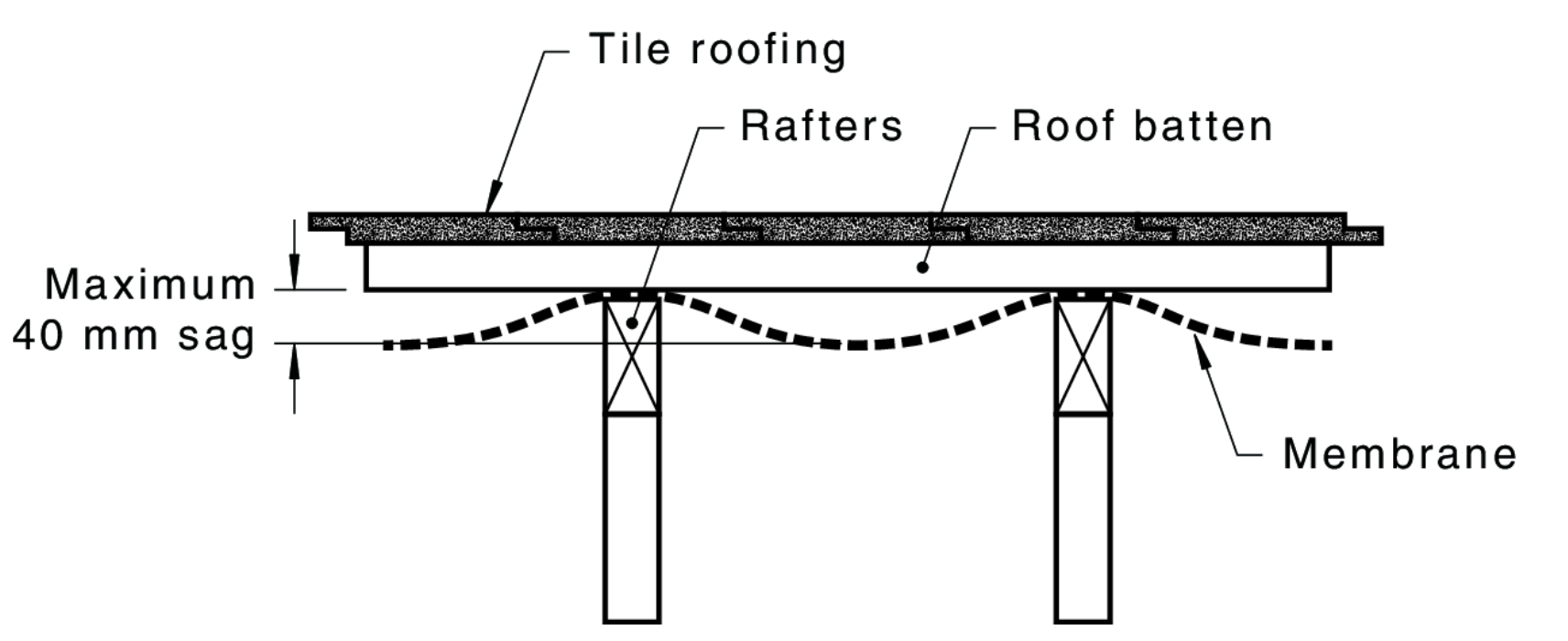
Exceeding Minimum Requirements
The National Construction Code (NCC) and BASIX set the minimum requirements for insulation in residential construction, depending on the climate zone. While meeting these minimum standards is mandatory, it is often advisable to exceed them for enhanced comfort and energy efficiency.
For instance, increasing the R-value of ceiling insulation beyond the minimum can significantly reduce summer heat gain, while higher R-values for wall insulation help maintain consistent indoor temperatures during winter. Investing in higher-quality insulation may have a higher upfront cost but can lead to considerable savings on energy bills and increased comfort throughout the life of your home.
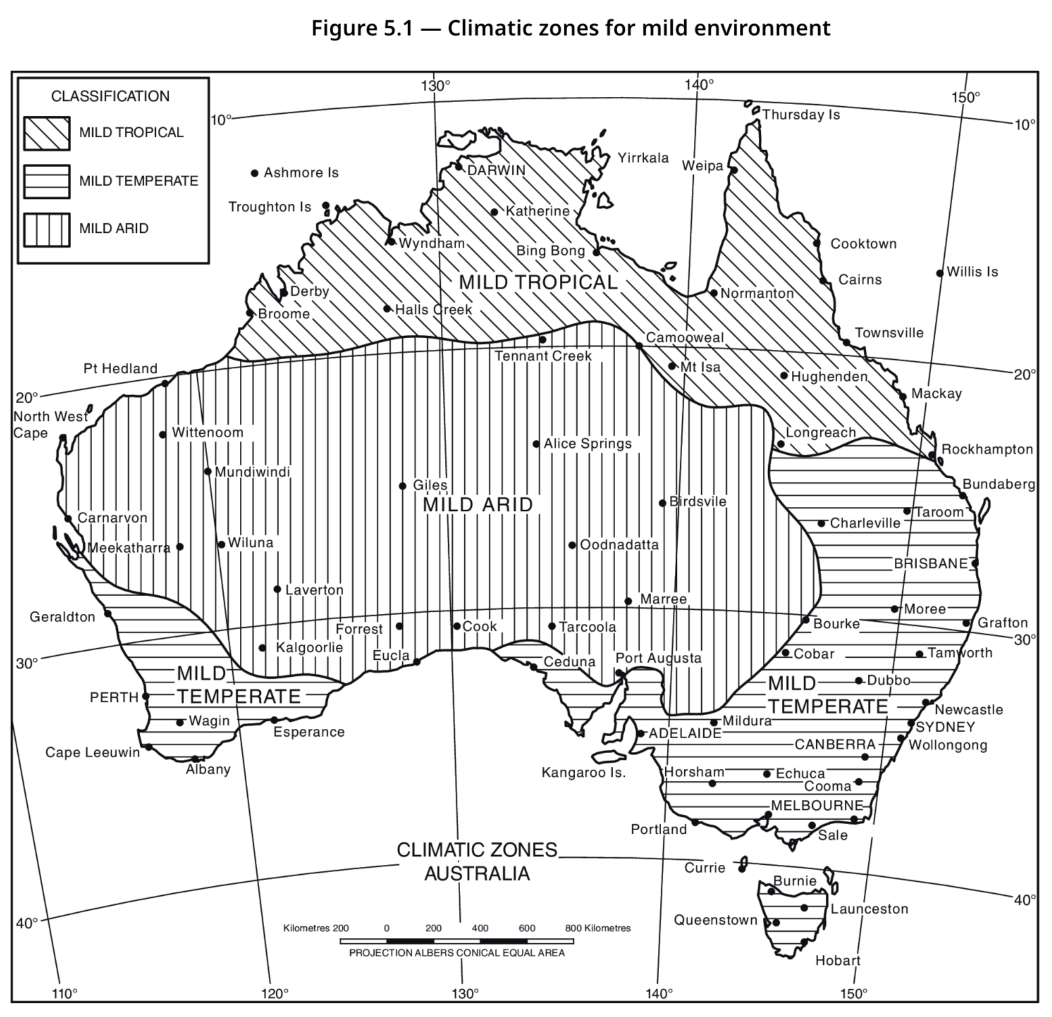
Key Design Considerations for Effective Insulation
Effective insulation goes beyond simply choosing the right materials. Proper design and installation techniques are essential to maximise the benefits of insulation in your home. This section covers the key design considerations that home owners should be aware of to ensure insulation performs effectively and efficiently.
Thermal Bridging
Thermal bridges are areas in a building where heat can bypass the insulation, leading to increased heat loss in winter and heat gain in summer. Common thermal bridges occur through metal framing, un-insulated areas, and junctions between different building elements.
- Identifying Thermal Bridges: The building frame, particularly steel or metal frames, can act as thermal bridges due to their high conductivity. Window and door frames, especially those made from non-thermally broken aluminium, are also prone to thermal bridging.
- Minimising Thermal Bridges: To minimise heat transfer through thermal bridges, consider the following strategies:
- Install thermal breaks between metal frames and cladding materials to reduce conductivity.
- Use rigid foam boards over framing elements to create an additional insulating layer.
- Select glazing that suits your climate, such as double-glazed windows with low-E coatings to reduce heat transfer.
Minimising thermal bridging is required for improving insulation performance and preventing condensation issues, especially in colder climates where condensation can lead to mould and mildew.
Installation Quality and Techniques
The quality of insulation installation has a significant impact on its performance. Even the best insulation materials can perform poorly if they are not installed correctly. To achieve optimal thermal performance, it is essential to follow best practices during installation.
- Avoid Gaps and Compression: Gaps or compression in insulation can drastically reduce its effectiveness. Insulation should be cut and fitted snugly between wall studs, roof trusses, and floor joists to avoid leaving any gaps. Additionally, bulk insulation should not be compressed, as this reduces its ability to trap air and lowers its R-value.
- Air Gaps for Reflective Insulation: Reflective insulation relies on the presence of an air gap next to the reflective surface to function properly. Maintaining an air gap of at least 25mm is important to prevent the reflective properties from being compromised. Dust accumulation on the reflective surface can also reduce its effectiveness, so reflective insulation should be installed with the shiny surface facing downwards or kept vertical.
Ventilation and Moisture Control
Proper ventilation and moisture control are key to ensuring insulation remains effective over the long term. Condensation is a common issue in well-insulated homes, particularly in areas like the roof and walls. Without adequate ventilation, condensation can accumulate and lead to mold growth, which not only reduces insulation performance but also poses health risks.
- Ventilated Roof Spaces: Roof spaces should be adequately ventilated to allow any moisture to escape. This is particularly important in cooler climates, where condensation can form when warm, moist air comes into contact with cold surfaces. Installing ridge vents, eave vents, or roof vents helps maintain airflow and reduces the risk of condensation.
- Vapour-Permeable Moisture Barriers: In areas prone to condensation, such as under roofing materials or behind wall cladding, it is advisable to use a vapour-permeable moisture barrier (sarking). These barriers allow moisture to escape while preventing water ingress, helping to keep insulation dry and effective.
I'm a massive fan of fixed roof vents, not whirly birds. In my opinion having moving parts is a point of failure. Hot air rises (as we all know) so as long as there is the means to escape, a fixed roof vent does the job without the risk of failure.
Combining Insulation Types for Maximum Efficiency
For the best results, it is often beneficial to combine different types of insulation to address both radiant and conducted heat transfer. For example:
- Reflective Insulation and Bulk Insulation: Combining reflective insulation (to reflect radiant heat) with bulk insulation (to resist conducted heat) provides a comprehensive solution for both hot and cold climates.
- Composite Insulation: Composite insulation products, such as foil-faced boards or foil-backed blankets, offer the benefits of both bulk and reflective properties in one product, making them ideal for maximizing efficiency in limited space.
When combining insulation types, it is important to consider the orientation of the reflective surface and the placement of bulk insulation to avoid unintended issues such as condensation.
Proper Insulation for Different Parts of the Home
Different parts of your home require specific insulation solutions to achieve optimal performance:
- Walls: Wall insulation should be installed between the studs, with rigid foam or bulk batts, and an appropriate vapour barrier. For better results, external wall insulation can be applied to reduce thermal bridging.
- Roof and Ceiling: Roofs and ceilings can be insulated with bulk batts or reflective insulation. For pitched roofs, reflective insulation should be installed beneath the roofing material to minimise radiant heat gain. In cooler climates, consider using composite insulation to maximise heat retention.
- Floors: Suspended timber floors benefit from bulk insulation installed between the joists, while slab-on-ground floors can be insulated around the slab edge to prevent heat loss. In some cases, using foam boards under the floor can help reduce heat transfer and improve thermal performance.
Room-Specific Insulation Guidance
The insulation needs of different parts of your home vary depending on the type of construction and the function of the space. Understanding the specific requirements for each room or area will help you choose the right materials and installation techniques to ensure maximum comfort and efficiency.
Roof and Ceiling Insulation
The roof and ceiling are often the most significant sources of heat gain and loss, installing proper insulation in these areas essential for maintaining a comfortable indoor environment.
- Pitched Roofs with Flat Ceilings: In climates with hot summers, a combination of reflective insulation (such as sarking) and bulk insulation in the ceiling cavity can significantly reduce heat transfer. Reflective insulation helps minimize radiant heat gain, while bulk insulation (such as fiberglass batts) reduces conducted heat flow.
- Raked or Cathedral Ceilings: Ceilings that follow the slope of the roof can be challenging to insulate due to limited space. Foil-faced boards or rigid foam boards are recommended, as they provide high R-values for their thickness. It is essential to maintain air gaps between the insulation and the ceiling material to reduce condensation risks.
- Flat Roofs: Flat roofs are more prone to condensation because they lack natural ventilation. In such cases, consider using hygrothermal analysis to determine the appropriate insulation solution. Composite roof systems, which combine bulk insulation with a vapor control layer, are often effective for these roofs.
Wall Insulation
Walls are responsible for a substantial amount of heat gain and loss, depending on the construction type and the climate. Proper wall insulation can help maintain a stable indoor temperature year-round.
- Weatherboard Walls: Weatherboard walls are often insulated with bulk batts between the wall studs, along with an appropriate vapor control layer to prevent condensation. This helps increase the total R-value of the wall assembly and improve thermal resistance.
- Brick Veneer Walls: Brick veneer construction involves an exterior brick wall with an interior frame. The cavity between these layers can be filled with bulk insulation or rigid foam boards. To further improve thermal resistance, a rigid foam board can be installed within the cavity, and additional bulk batts can be added between the studs.
- Cavity Brick Walls: Cavity brick walls have an air gap between the inner and outer layers of bricks, which can be filled with cavity fill insulation (such as injected foam) to improve thermal resistance. It is important to check that the cavity fill material meets building regulations for water repellency and fire safety.
Floor Insulation
Floor insulation is essential for maintaining a comfortable indoor temperature and reducing heat loss, particularly in cooler climates. The type of insulation required will depend on the type of flooring.
- Suspended Timber Floors: The total thermal resistance of suspended timber floors should be climate-appropriate. Bulk insulation batts can be installed between the joists, supported by nylon cords or rigid foam boards to ensure coverage and reduce the risk of pests. In warmer climates, reflective foil can be used under timber floors to reduce heat gain.
- Slab-on-Ground Floors: The vertical edges of slab-on-ground floors are susceptible to heat loss. Slab edge insulation is recommended to reduce thermal bridging and maintain a consistent indoor temperature. In some climates, insulating the underside of the slab may also be beneficial, particularly in areas where groundwater is present.
Insulating Special Rooms
Some rooms in your home may require additional insulation to address specific needs, such as temperature control, soundproofing, or humidity management.
- Bathrooms and Laundries: These areas are often prone to moisture issues, so it is essential to use insulation that can handle humidity without losing performance. Water-resistant bulk insulation, such as polyester or closed-cell foam, is ideal for use in these spaces.
- Garages and Storage Rooms: Uninsulated garages and storage rooms can lead to temperature fluctuations in adjacent areas. Consider adding rigid foam boards to the walls and ceiling of garages to improve thermal performance. Insulating the garage door can also help maintain a more consistent temperature.
- Living Areas and Bedrooms: For living areas and bedrooms, insulation should focus on both thermal and acoustic performance. Bulk insulation batts provide excellent soundproofing, reducing noise transfer between rooms, while high-R-value materials help maintain comfortable indoor temperatures.
Retrofitting Insulation in Existing Homes
If your home was built without sufficient insulation, retrofitting is an effective way to improve its energy efficiency and comfort. Different approaches can be taken depending on the area of the home:
- Ceiling Retrofitting: Retrofitting ceiling insulation is often the easiest and most cost-effective way to improve thermal performance. Loose-fill insulation, such as cellulose fibre, can be blown into the ceiling cavity to fill gaps without removing existing finishes.
- Wall Retrofitting: Adding insulation to walls in existing homes can be more challenging but is still possible. Cavity fill insulation, such as loose-fill or injected foam, can be used to fill wall cavities without removing wall cladding. This approach is most effective in homes with cavity brick walls or other types of cavities.
- Floor Retrofitting: Insulating suspended timber floors from below is an effective way to reduce heat loss. Bulk batts or rigid foam boards can be installed between the floor joists to create a thermal barrier. For slab-on-ground floors, adding insulation to the edges of the slab can significantly reduce heat loss.
Avoiding Common Insulation Mistakes
Installing insulation correctly is key to achieving the intended thermal performance and maximising energy efficiency in your home. Mistakes during installation can compromise the effectiveness of even the highest-quality insulation, leading to increased energy costs, moisture issues, and uncomfortable living conditions. In this section, we will discuss common insulation mistakes and how to avoid them.
Gaps and Compression
Gaps and compression are two of the most common insulation mistakes, and they can significantly reduce the effectiveness of your insulation.
- Gaps in Insulation: Even small gaps in insulation can result in substantial heat loss or gain. Poorly fitted batts or loose-fill insulation that doesn’t cover all areas creates a path for heat to bypass the insulation. To avoid this, insulation must be cut and fitted snugly between wall studs, roof trusses, and floor joists, ensuring there are no uninsulated areas.
- Compression of Bulk Insulation: Bulk insulation, such as fibreglass or wool batts, relies on air pockets to resist heat flow. When the insulation is compressed, these air pockets are reduced, and the R-value decreases significantly. It is important to install insulation in a way that allows it to maintain its full thickness. This means avoiding placing heavy objects on top of insulation or compressing it into spaces that are too small.
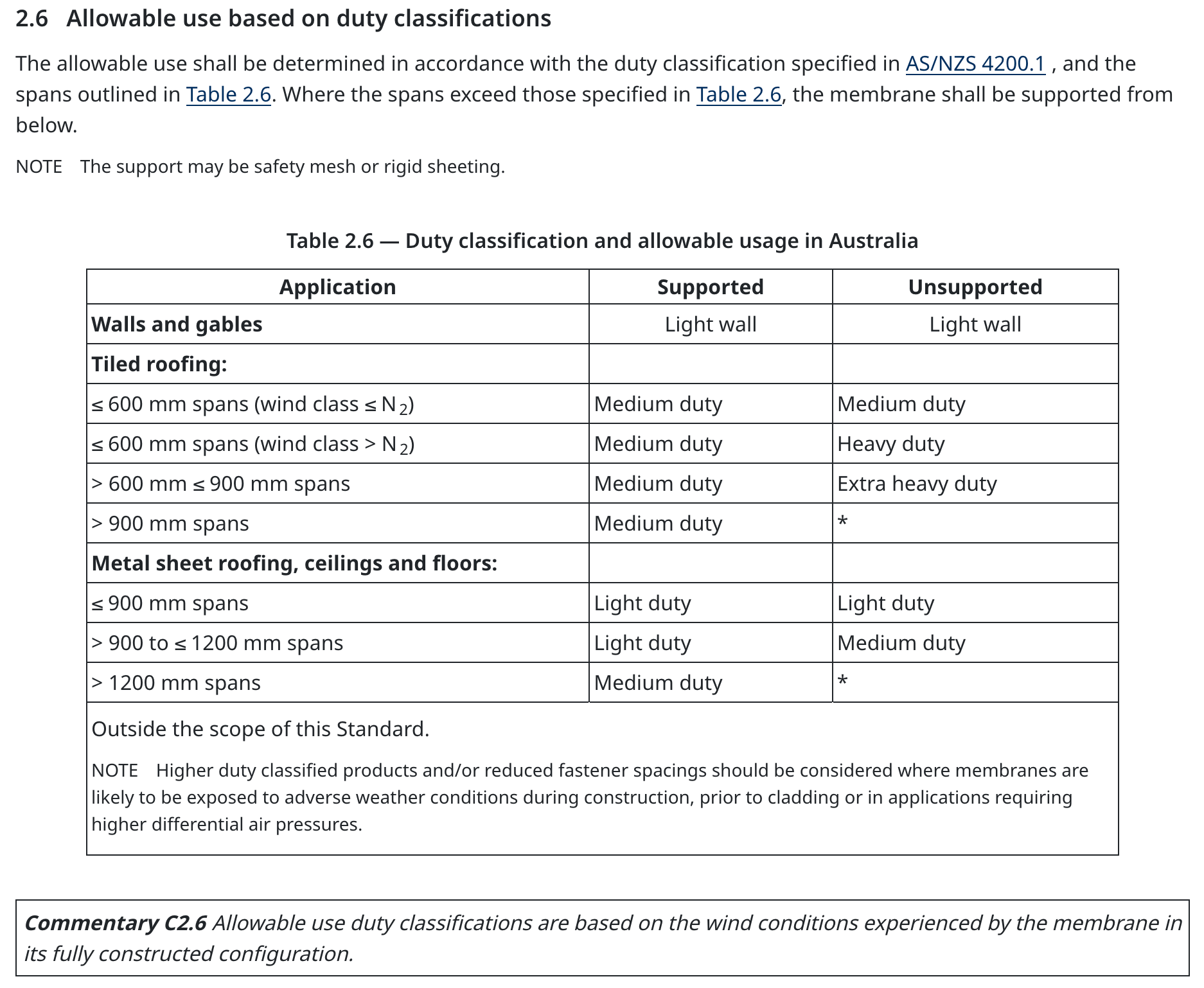
Incorrect Placement of Reflective Insulation
Reflective insulation requires careful installation to be effective. It relies on the presence of an air gap adjacent to the reflective surface to reflect radiant heat. If the air gap is not maintained or if the reflective surface becomes dusty, the insulation’s effectiveness is significantly reduced.
- Maintaining an Air Gap: Reflective insulation should always be installed with an air gap of at least 25mm next to the reflective surface. This gap allows the reflective insulation to function as intended. Installing reflective insulation without this gap will render it almost useless.
- Avoiding Dust Accumulation: Dust settling on the reflective surface can reduce its ability to reflect heat. To prevent this, install reflective surfaces facing downward or keep them vertical where possible. In areas where dust accumulation is unavoidable, consider combining reflective insulation with another type of insulation to maintain overall performance.
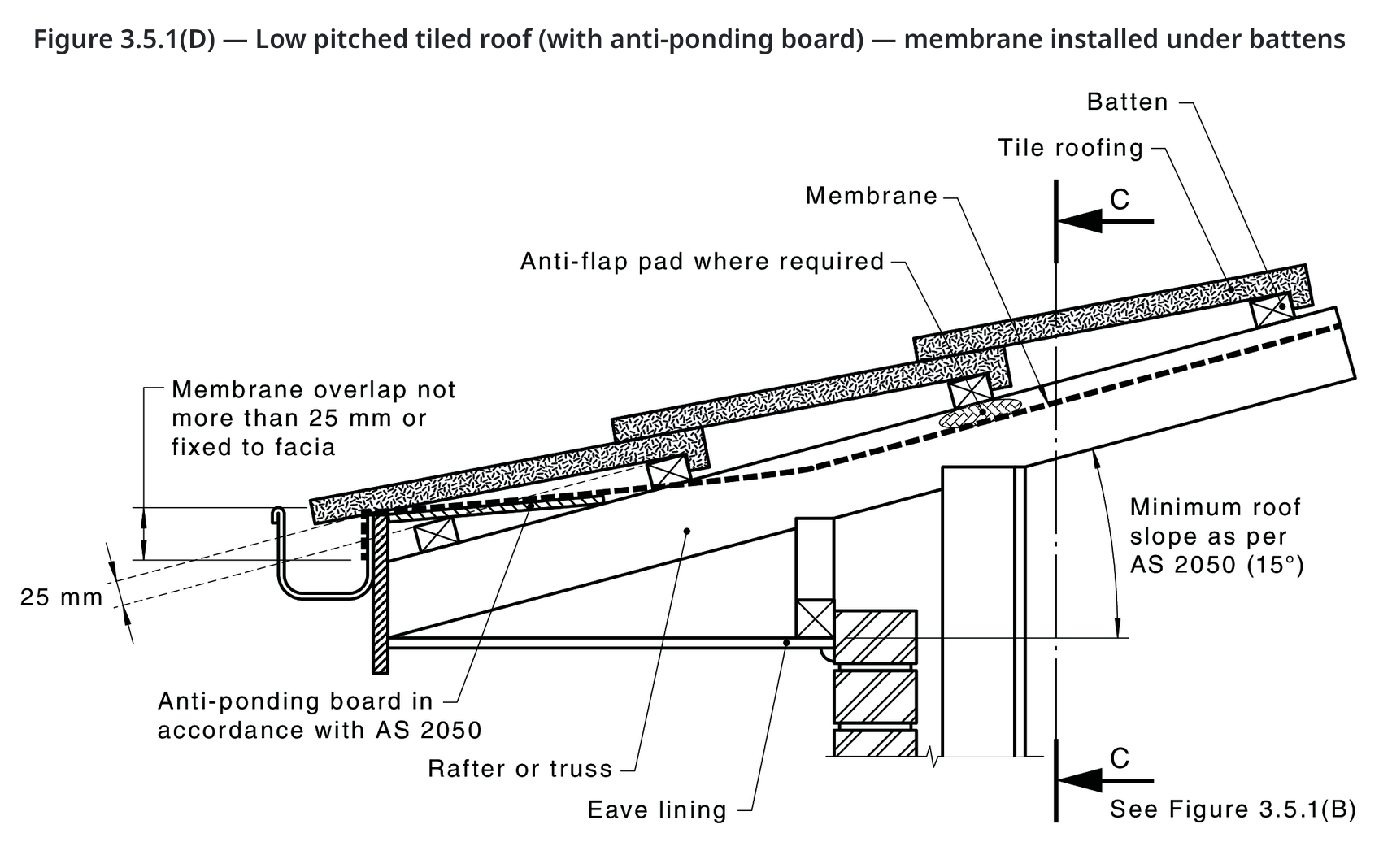
Improper Management of Thermal Bridging
Thermal bridges are a common cause of reduced insulation performance. They occur when heat bypasses the insulation through more conductive materials, such as metal frames or uninsulated parts of the building.
- Reducing Thermal Bridges: To minimise thermal bridging, consider adding thermal breaks between metal framing and cladding, or installing rigid foam boards over framing elements to improve insulation continuity. Proper detailing and planning during the design phase can help identify potential thermal bridges and allow for corrective measures before construction begins.
Insufficient Ventilation and Moisture Control
Proper ventilation is essential for maintaining the effectiveness of insulation and preventing moisture buildup. Condensation is a common issue in well-insulated homes, especially in areas like the roof and walls, and it can lead to mould growth and a reduction in insulation performance.
- Ventilation of Roof Spaces: Roof spaces should be ventilated to allow moisture to escape. Installing ridge vents, eave vents, or other types of roof vents will help maintain airflow and prevent condensation from forming on cold surfaces. In areas with high humidity, additional measures may be needed to ensure effective moisture control.
- Using Vapour-Permeable Barriers: Installing vapour-permeable moisture barriers (such as sarking) beneath roofing materials or behind wall cladding can help control moisture. These barriers allow water vapour to escape from the building while preventing water ingress, keeping insulation dry and effective.
Not Following Manufacturer’s Installation Guidelines
Each insulation product comes with specific installation guidelines from the manufacturer. Failure to follow these guidelines can lead to poor performance and may even void product warranties.
- Professional vs. DIY Installation: Some types of insulation can be installed by homeowners, while others require professional installation. It is important to understand your limitations and seek professional help if needed. For example, reflective insulation should be installed by a qualified professional, as it is conductive and poses electrical hazards if improperly handled.
- Clearances Around Electrical Fittings: Special care must be taken when installing insulation near electrical wiring, hot flues, and recessed lights. Minimum clearances must be maintained to prevent fire hazards. Older-style halogen lights, in particular, cannot be covered with insulation, whereas some LED downlights are rated to be covered. Always refer to the manufacturer’s guidelines and the Australian Standards for electrical safety.
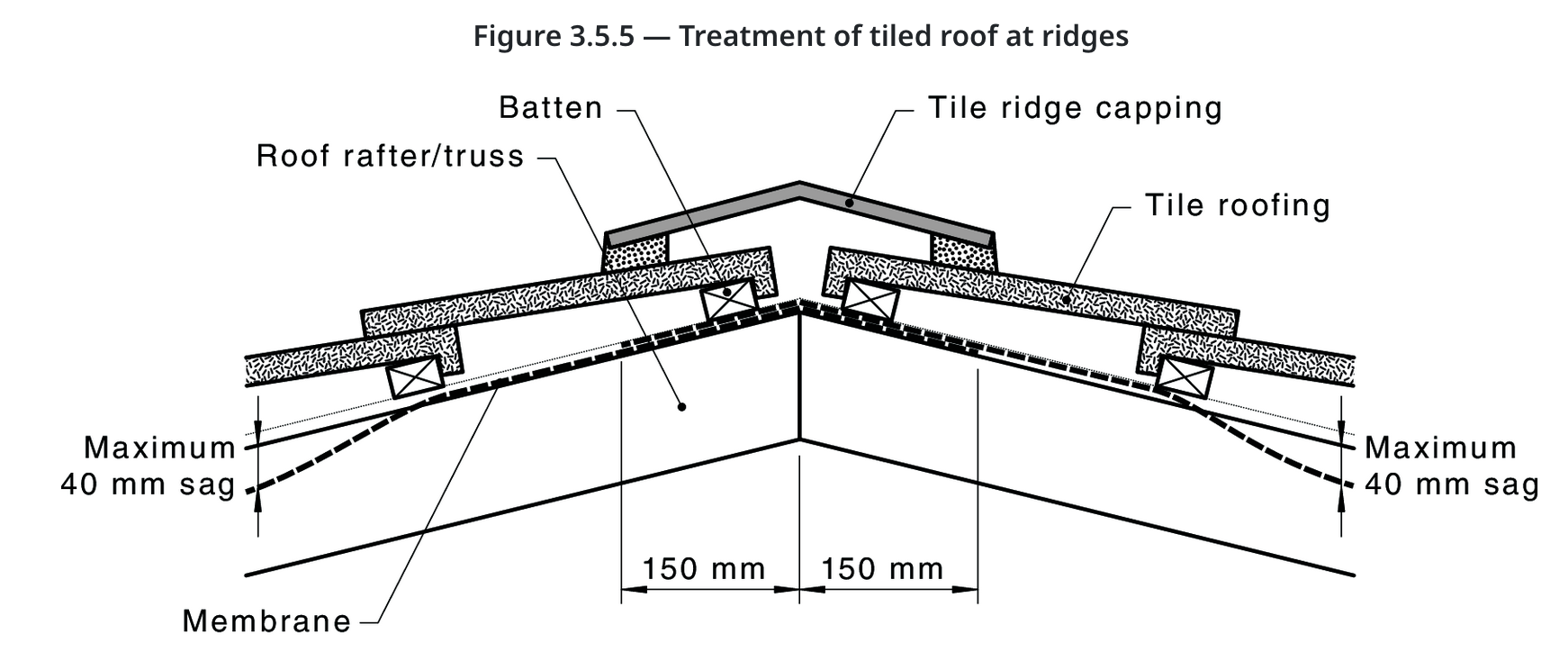
Overlooking Insulation in Key Areas
Another common mistake is overlooking important areas of the home during insulation installation. Insulating only parts of the building envelope can lead to thermal leaks, where heat can easily enter or escape.
- Corners and Junctions: Corners of walls, ceilings, and floors are often missed during insulation installation. Properly insulating these areas is essential, as they are common points for heat leaks.
- Doors and Windows: Insulation should butt tightly against door and window frames to avoid gaps. Poorly insulated windows and doors can result in significant heat loss or gain, which undermines the effectiveness of the rest of the building’s insulation.
Failing to Check Insulation Performance Post-Installation
After installation, it is important to inspect the insulation to ensure it has been installed correctly and is performing as expected. Some common steps include:
- Checking for Gaps: Conduct a visual inspection to ensure there are no visible gaps or areas where insulation is missing.
- Using Thermal Imaging: Thermal imaging cameras can be used to identify areas of heat leakage or poor insulation coverage, especially in hard-to-reach areas like roof cavities or within wall cavities.
This comprehensive resource covers everything from design and selection to installation of insulation in your home. It distills key Australian Standards into one convenient publication—well worth a read!
Health and Safety Considerations When Installing Insulation
Installing insulation is a valuable step in making your home more comfortable and energy-efficient, but it’s essential to take proper precautions to protect yourself and others during the process. Whether you choose to install insulation yourself or hire a professional, understanding the health and safety considerations is important.
Personal Protective Equipment (PPE)
When installing insulation, it is essential to wear the right personal protective equipment (PPE) to prevent injuries and minimise health risks. Here are some key PPE items to consider:
- Gloves: Wear gloves when handling insulation materials to protect your hands from irritation. Fibreglass and mineral wool insulation, in particular, can cause skin irritation.
- Dust Mask or Respirator: A dust mask or respirator is important when working with loose-fill insulation or when cutting batts. Dust particles from fibreglass, cellulose, and other insulation materials can cause respiratory issues if inhaled.
- Eye Protection: Use safety goggles to protect your eyes from fibres and particles. Reflective insulation can also cause glare, so proper eye protection is required.
- Long-Sleeved Clothing: Wearing long sleeves and pants helps protect your skin from irritation. Fibreglass and mineral wool can cause itching and rashes if they come into contact with bare skin.
AS4200.2 says "Membranes are electrically conductive - ensure they do not come in contact with electrical wiring and equipment. Conduct a risk assessment if electrical wiring is installed prior to the membrane installation.
A.2.2 electrical safety details for membrane on top of ceiling surfaces or ceiling joists and under subfloors. Obtain written statements stating that each unprotected circuit is identified and marked clearly.
Electrical and Fire Safety
Electrical and fire safety are major concerns when installing insulation, especially in areas where electrical wiring, lights, or hot flues are present.
- Clearances Around Electrical Components: It is essential to maintain minimum clearances around electrical wiring, lights, and other fixtures. Insulation installed too close to hot light fittings, such as halogen downlights, can pose a fire risk. Some LED downlights are rated to be covered with insulation, but always check the manufacturer’s specifications.
- Generally: thermal control membrane without luminaries barriers (downlights) then minimum clearances apply per the table 4.6A - generally - 200mm above, 200mm side, 50mm side to bulk thermal insulation, 50mm from auxiliary equipment (battens)
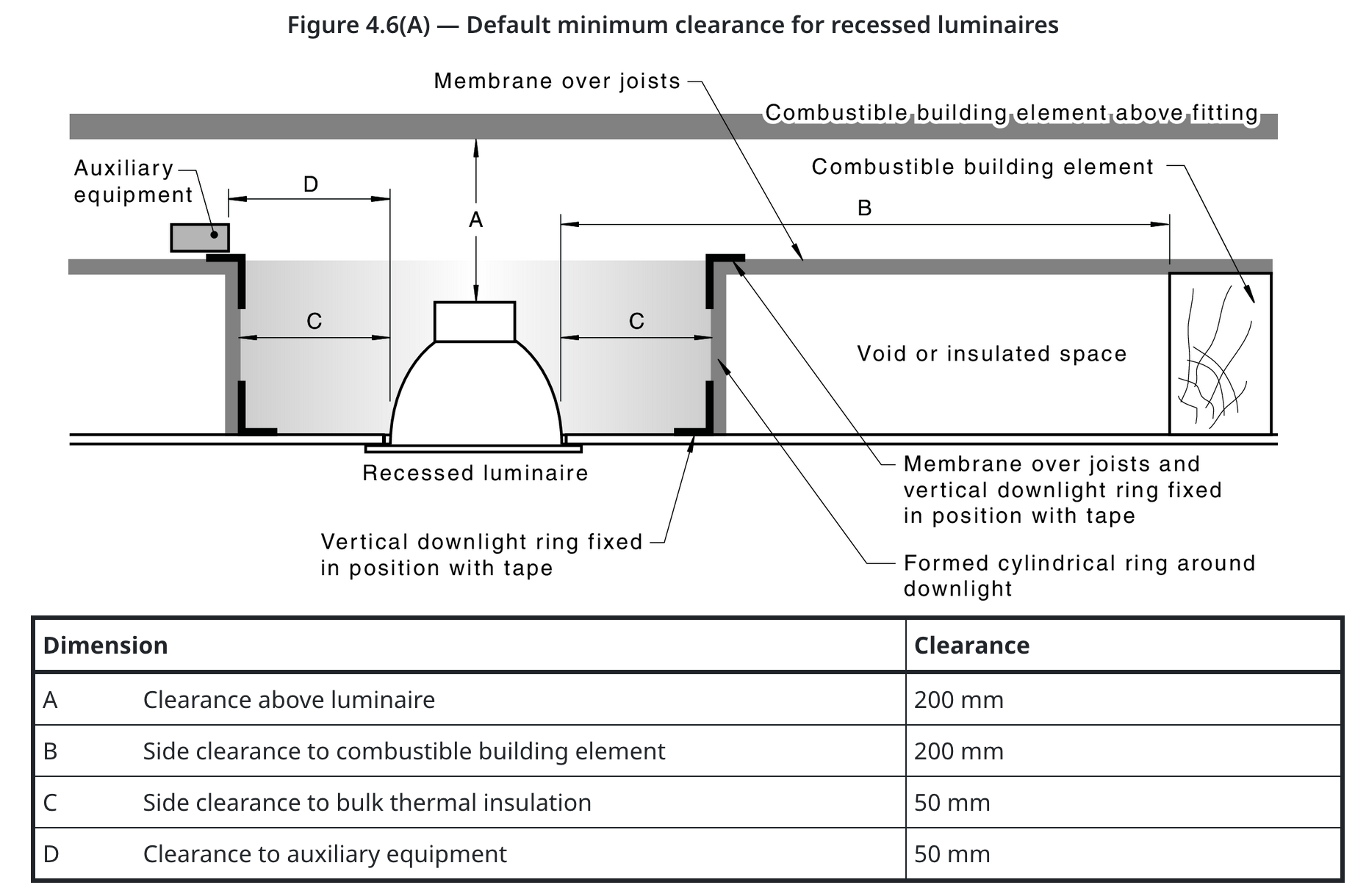
- Avoiding Electrical Hazards: Reflective foil insulation is conductive, so it is important to keep it clear of electrical cables and equipment. Reflective insulation should be installed by a qualified professional to ensure that it does not come into contact with live wires. Staples used to secure foil insulation should be non-metallic to avoid the risk of electrocution.
- Fire Safety Barriers: When installing insulation around recessed lighting, use fire safety barriers that comply with Australian Standards. Barriers help maintain the required clearances and prevent insulation from covering light fittings.
Preventing Overheating and Moisture Buildup
Proper insulation installation also requires attention to heat and moisture management to prevent potential hazards.
- Heat Buildup: Insulation should not be installed over hot flues, chimneys, or exhaust fans without ensuring proper clearances. Failing to do so can lead to excessive heat buildup and pose a fire risk.
- Moisture Control: Insulation materials, especially bulk insulation, should be kept dry to prevent reduced effectiveness and mould growth. Vapour control layers should be used where there is a risk of condensation. For example, vapour-permeable moisture barriers can be installed in wall and roof cavities to manage moisture and keep insulation dry.
Safe Handling of Insulation Materials
Different insulation materials have different handling requirements to ensure safety.
- Fibreglass and Mineral Wool: Both fibreglass and mineral wool insulation can cause skin, eye, and respiratory irritation. When handling these materials, always wear gloves, protective clothing, and a dust mask. If fibreglass comes into contact with your skin, wash the area with cold water to help remove the fibres.
- Spray Foam Insulation: Spray foam insulation should be handled only by professionals, as it involves using chemicals that can be hazardous if inhaled or if they come into contact with skin. Proper ventilation is required during installation, and installers should wear a respirator and full protective clothing.
- Reflective Foil: Reflective foil insulation can cause glare and increase the risk of sunburn when installing in bright sunlight. Always wear eye protection, sunscreen, and protective clothing when working with reflective materials outdoors.
Safe Access to Roof Spaces
When insulating roof spaces, it is important to consider safety when accessing and moving within the area.
- Avoid Stepping on Ceiling Joists: Ceiling joists are not designed to bear weight, and stepping on them can result in damage or injury. Planks or platforms should be used to create a stable walking surface when moving around in roof spaces.
- Work with a Partner: Insulating a roof space can be physically demanding and often requires working in confined areas. Working with a partner can make the task safer, particularly if lifting or positioning heavy rolls of insulation.
Professional Inspections
Once insulation is installed, it is a good idea to have the work inspected by a professional to ensure that it meets Australian Standards and has been installed correctly. A professional inspection can identify any gaps, compression, or potential fire hazards, ensuring that your insulation will provide the best possible performance.
Quality Management and Checklist for Insulation Installation
To ensure that insulation performs effectively and delivers the expected energy savings and comfort, it is important to have a quality management process in place. This includes following a checklist during installation, conducting thorough inspections, and adhering to Australian standards.
Insulation Checklist
A well-planned installation checklist can help homeowners and installers avoid mistakes and ensure that the insulation meets the required standards for thermal performance, safety, and durability. Here are some key points to include in your checklist:
- Select the Right Insulation Type: Ensure the chosen insulation type is appropriate for your climate and the area being insulated (e.g., bulk for walls, reflective for roofs).
- Verify R-Values: Confirm that the insulation meets or exceeds the recommended R-value for your climate zone, as specified by the National Construction Code (NCC).
- Inspect Insulation Materials: Check that insulation materials are free from defects and stored in a dry area before installation. Wet or damaged insulation can reduce performance.
- Avoid Gaps and Compression: Install insulation so that it fits snugly, with no gaps or areas of compression. Gaps or compressed insulation will reduce the overall R-value.
- Maintain Air Gaps for Reflective Insulation: Ensure an air gap of at least 25mm is maintained adjacent to the reflective surface, as required for effective radiant heat reflection.
- Follow Manufacturer's Guidelines: Adhere to all manufacturer installation instructions, including spacing, layering, and handling requirements.
- Check Electrical and Fire Clearances: Maintain proper clearances around recessed lights, hot flues, and other fixtures to prevent fire hazards. Use fire-rated barriers where necessary.
- Use Vapour-Permeable Barriers: Install vapour-permeable moisture barriers where condensation is a risk, such as beneath roof cladding or behind wall insulation.
- Verify Installation Locations: Confirm that all key areas, including walls, ceilings, floors, and other thermal bridges, have been properly insulated.
- Secure Insulation: Use appropriate fasteners, such as non-metallic staples, to secure insulation materials in place, particularly for reflective foil insulation.
Quality Control Tips
Quality control is essential for ensuring that the insulation in your home meets Australian standards and performs effectively over time. Here are some additional quality control tips to follow after installation:
- Inspect All Insulation Areas: Conduct a visual inspection of all insulated areas, including hard-to-reach spots like corners and junctions, to verify that insulation is installed without gaps.
- Thermal Imaging: Consider using thermal imaging to identify any areas of heat leakage or improperly insulated spaces. Thermal imaging cameras are especially useful for detecting missing insulation within wall cavities and roof spaces.
- Check for Consistent Coverage: Ensure that loose-fill insulation, such as cellulose, is evenly distributed and that batts are positioned flush against each other with no spaces or overlaps.
- Address Any Issues Immediately: If any issues are identified, such as missing insulation or incorrect installation, address them immediately. Fixing problems early on can prevent long-term energy loss and performance issues.
Ensuring Compliance with Australian Standards
All insulation products and installation methods must comply with Australian standards to guarantee performance, safety, and energy efficiency.
- AS/NZS 4859: This standard sets out requirements for materials used for thermal insulation in buildings, including bulk and reflective insulation. Ensure that the insulation product you choose is certified to comply with AS/NZS 4859.
- AS/NZS 3999-2015: This standard covers the installation of bulk thermal insulation. It outlines best practices for handling and installing insulation materials, including safety requirements.
- Electrical Safety Standards: Refer to AS/NZS 3000 (the Australian/New Zealand wiring rules) for specific guidelines on maintaining proper clearances around electrical fixtures when installing insulation.
Conclusion
Insulation is one of the most important elements in ensuring your home remains comfortable, energy-efficient, and cost-effective throughout the year. By understanding the different types of insulation materials, selecting the right R-values, and ensuring correct installation, you can significantly improve the thermal performance of your home.
Quality installation is as important as the insulation product itself. By following best practices, you can maximise the benefits of your insulation. Whether you're building a new home or retrofitting an existing one, taking the time to plan and manage insulation properly will provide long-term comfort, lower energy bills, and greater peace of mind.
FAQ Section
1. What is the best type of insulation for my climate?
The best type of insulation depends on your climate. In hot and humid climates, reflective insulation is ideal for minimising heat gain, while in cooler climates, bulk insulation like fibreglass or wool batts helps retain heat. In mixed climates, a combination of bulk and reflective insulation provides the best results.
2. How does insulation affect my energy bills?
Proper insulation can significantly reduce your heating and cooling costs by preventing heat from escaping in winter and keeping it out in summer. This reduces the need for air conditioning and heating, leading to lower energy bills.
3. What is the difference between R-value and total R-value?
The R-value measures the thermal resistance of an individual insulation product, while the total R-value takes into account all components of a building element (e.g., wall, roof, or floor) to determine the combined insulating effect. Total R-values are more accurate in assessing the overall performance of insulation within the building envelope.
4. Can I install insulation myself, or should I hire a professional?
Some insulation types, like fibreglass batts and polyester batts, can be installed by homeowners, provided that they follow safety guidelines. However, for materials like spray foam or reflective foil, professional installation is recommended due to safety concerns and complexity.
5. What are thermal bridges, and why are they a concern?
Thermal bridges are areas where heat can bypass the insulation, usually through more conductive materials like metal framing. They reduce the overall effectiveness of insulation and can lead to condensation issues. Minimising thermal bridges helps improve energy efficiency and prevent moisture problems.
6. Is reflective insulation suitable for all parts of my home?
Reflective insulation works best in areas with significant exposure to radiant heat, such as roofs and walls facing direct sunlight. It is not ideal for use in areas without an air gap or where dust can accumulate, as this reduces its effectiveness. Reflective insulation should be installed with proper air gaps for optimal performance.
7. How do I prevent condensation issues with insulation?
To prevent condensation, ensure proper ventilation in roof spaces, use vapour-permeable moisture barriers, and avoid compressing insulation materials. Condensation is more likely to occur in areas with poor airflow, so proper design and installation are required.
8. What environmental considerations should I take into account when choosing insulation?
Consider insulation products that contain recycled content, such as fibreglass or polyester, and are recyclable at the end of their life. Look for ecolabel certifications like Ecospecifier Global or GreenTag, which indicate the product's environmental impact.
9. How do I ensure my insulation meets Australian Standards?
To ensure compliance, choose insulation products certified to AS/NZS 4859 and follow installation guidelines according to AS/NZS 3999-2015. For electrical safety, follow AS/NZS 3000 guidelines for maintaining clearances around electrical components.
10. Can insulation be retrofitted in existing homes?
Yes, insulation can be retrofitted in ceilings, walls, and floors of existing homes. Loose-fill insulation is often used for ceiling cavities, while cavity fill insulation (e.g., injected foam) can be used for wall cavities. Floor insulation can be added to suspended floors to reduce heat loss.
Further Reading
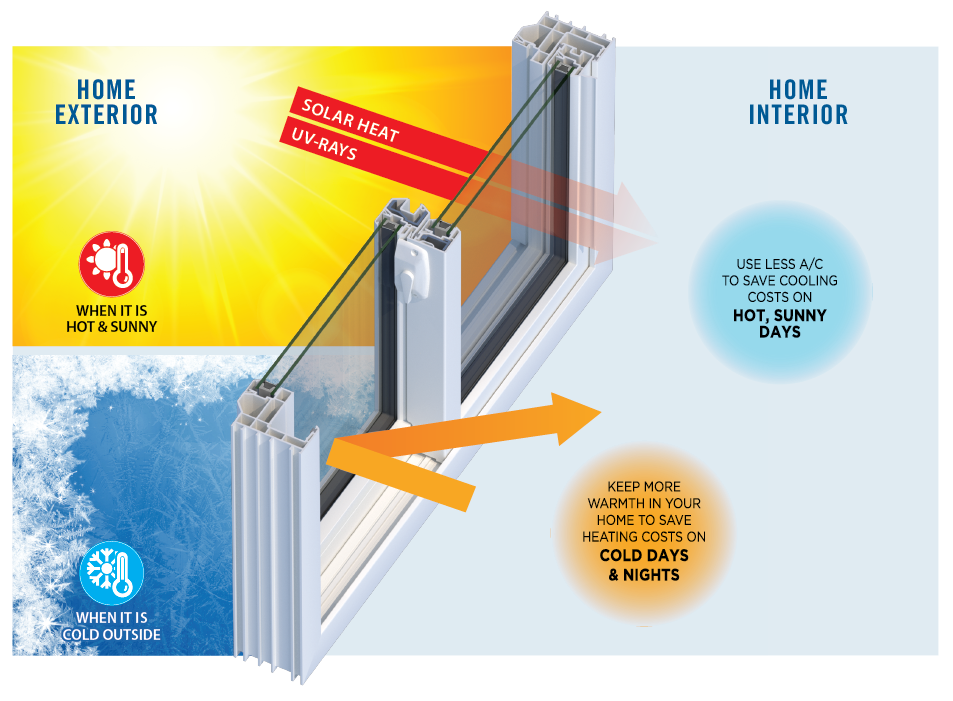
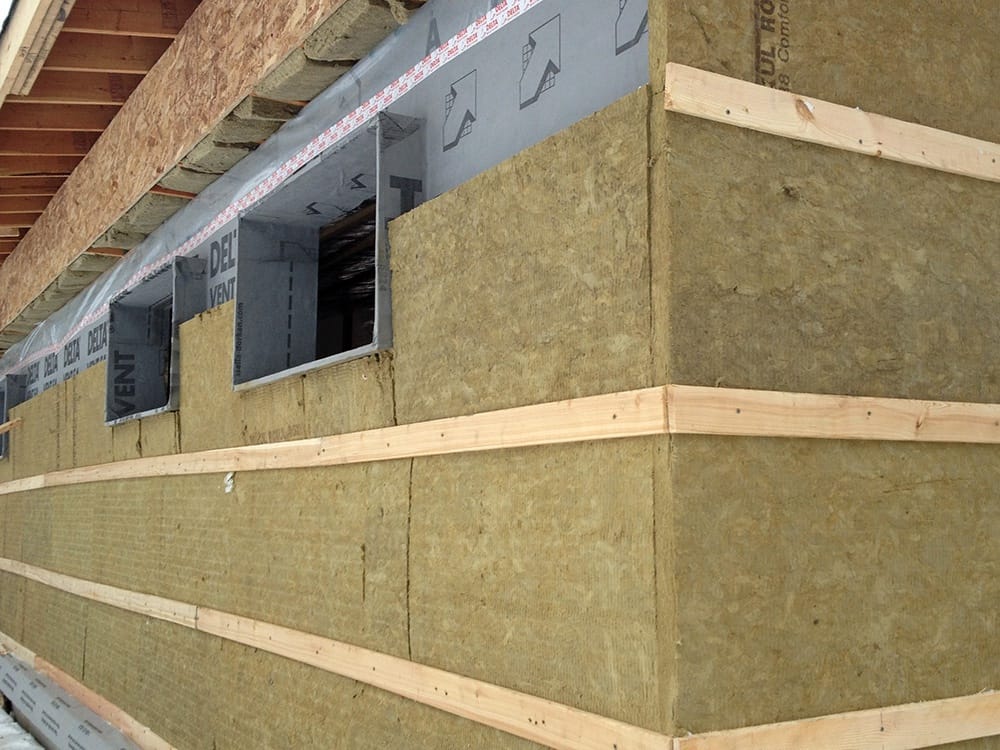
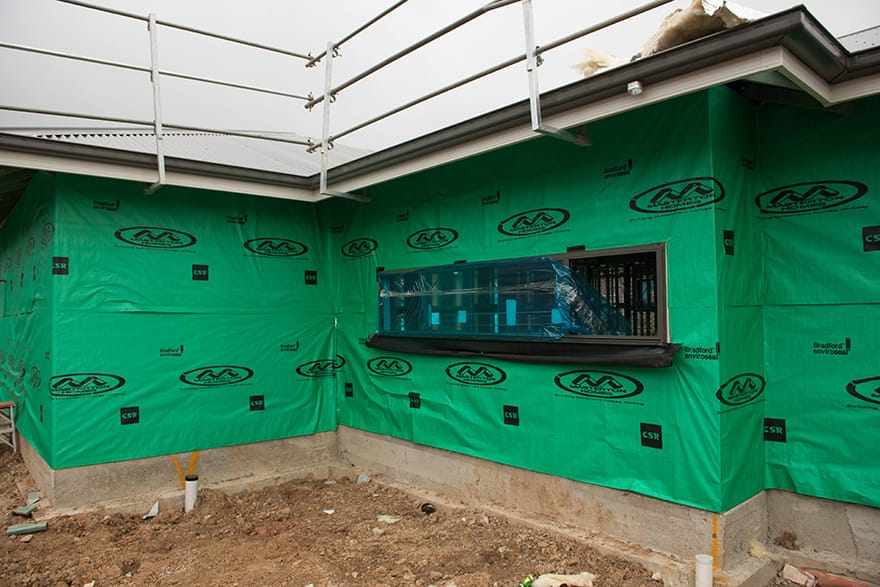
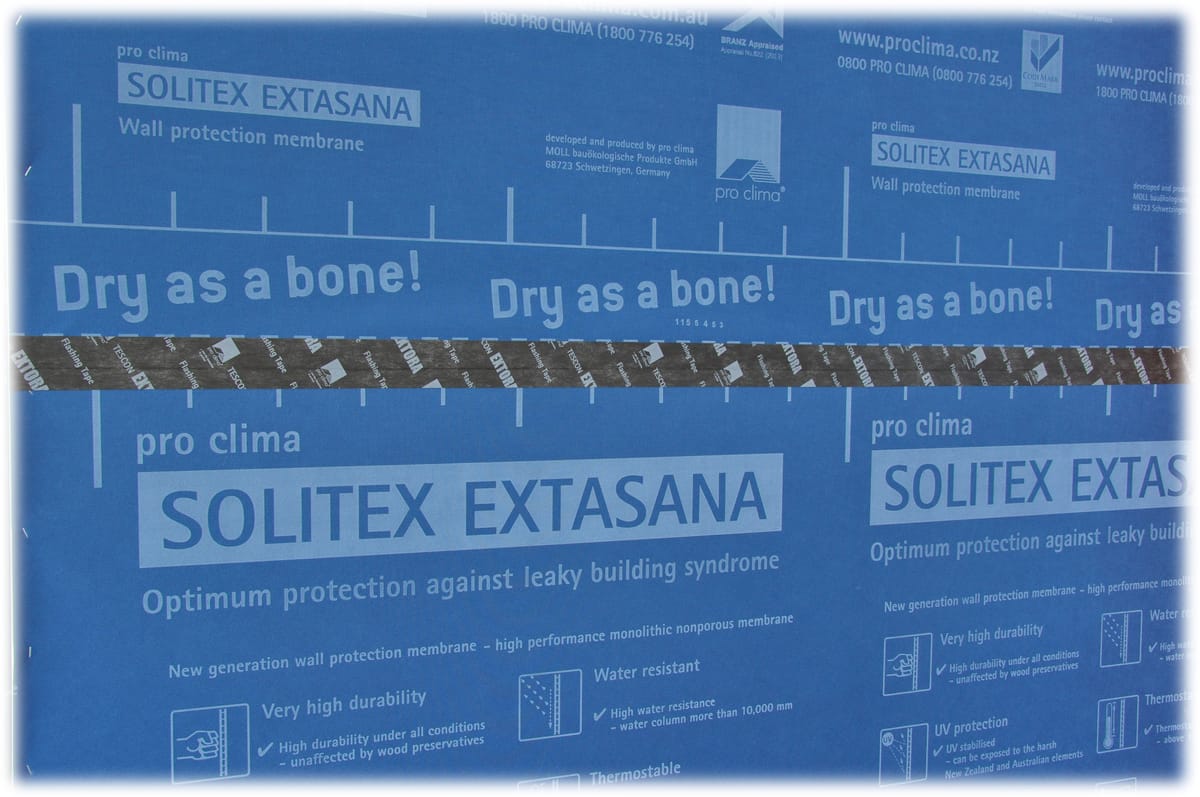
Not sponsored: We prefer the Proclima System because its a complete system
Helpful Software
Note: not sponsored. Just some helpful and intuitive takeoff software
Conx is affordable and easy to use software to do quick estimates and quotes. Pay per job or a reasonable monthly fee. The Xero integration is handy too.