In the current housing market, where demand is soaring and skilled labour is scarce, pre-made and modular construction methods are emerging as game-changers. These innovative building techniques offer a range of benefits, making them increasingly popular among first-time home builders.
In this blog post we look into how pre-made and modular construction can positively change the building industry, exploring their advantages, challenges, and the future outlook.
Understanding Pre-Made and Modular Construction
Pre-made and modular construction involves the use of factory-produced building sections, which are then transported to the construction site for assembly. Unlike traditional construction, which occurs entirely on-site, modular construction leverages controlled factory environments to produce high-quality building components. These sections, or modules, can range from entire rooms to smaller structural elements, and they are designed to fit together seamlessly.
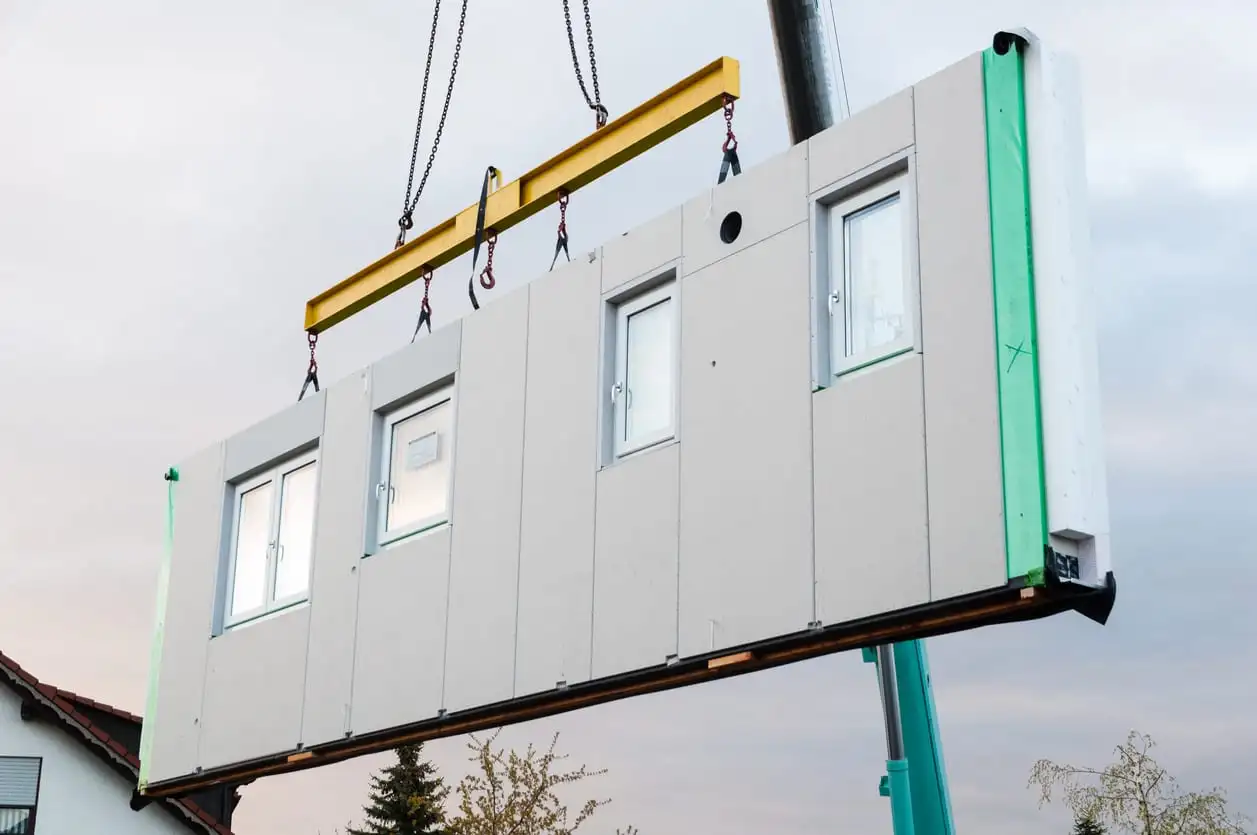
The Growing Popularity of Modular Construction
Addressing Skilled Labour Shortages
One of the most significant advantages of modular construction is its ability to mitigate the impact of skilled labour shortages. The construction industry has long faced challenges in recruiting and retaining skilled workers. As experienced tradespeople retire and fewer young people enter the field, the gap between supply and demand continues to widen.
Modular construction addresses this issue by shifting much of the building process to a factory setting, where a smaller, more specialised workforce can produce high-quality components efficiently.
Modular construction also opens opportunities for workers who may not have traditional construction skills but can be trained to operate machinery and perform specific tasks within a controlled environment. This democratisation of the labour force helps bridge the gap caused by the shortage of skilled tradespeople, ensuring that projects can proceed without significant delays.
Speeding Up Construction Timelines
Modular construction significantly reduces the time required to complete a project. Traditional construction projects can be delayed by weather conditions, labour shortages, and other unforeseen challenges.
In contrast, modular construction allows for simultaneous site preparation and module fabrication. This parallel processing can cut project timelines by 30% to 50%, enabling home buyers to move into their new homes much faster.
For instance, while the foundation and site work are being completed on-site, the building modules can be constructed in the factory. Once the site is ready, the modules are transported and assembled quickly, often within a matter of days. This efficiency not only reduces the overall construction time but also minimises the financial burden of extended project timelines on both builders and buyers.
Enhancing Quality and Consistency
Factory-controlled environments ensure that each building module meets strict quality standards. This consistency is often harder to achieve with on-site construction, where varying conditions and labour practices can lead to discrepancies in quality. Modular construction reduces the likelihood of defects and ensures that each component is built to precise specifications, resulting in a more durable and reliable final product.
In addition to quality control, modular construction benefits from reduced exposure to environmental factors. Traditional construction sites are susceptible to weather-related issues such as rain, wind, and temperature fluctuations, which can compromise building materials and workmanship. In contrast, the controlled factory environment protects modules from these elements, ensuring that each piece is constructed under optimal conditions.
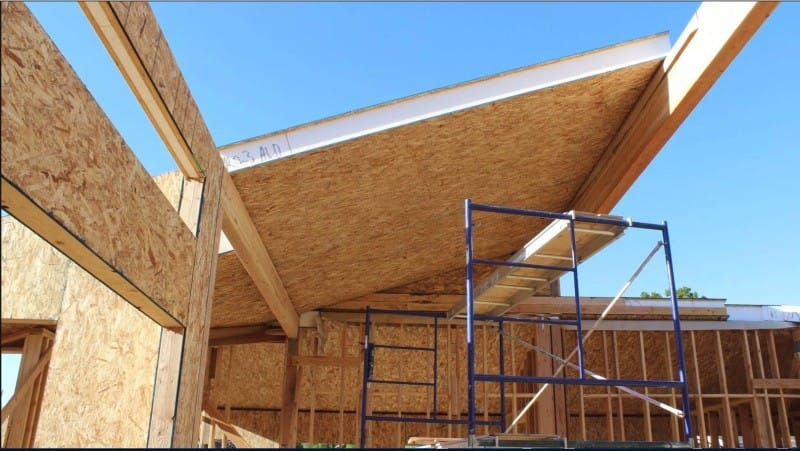
Overcoming the Challenges of Modular Construction
While the benefits of modular construction are compelling, the industry faces several challenges that have hindered its widespread adoption. Understanding these challenges is crucial for prospective home builders considering modular options.
Regulatory Hurdles
One of the primary obstacles to modular construction is navigating the complex regulatory landscape. Building codes and regulations vary widely by region, and modular construction often requires additional approvals and inspections. These regulatory hurdles can lead to delays and increased costs, making it essential for builders to work closely with local authorities to ensure compliance.
To address this, some modular construction companies are advocating for standardised regulations that recognise the unique aspects of factory-built homes. By working with policy-makers and industry organisations, they aim to streamline the approval process and reduce the bureaucratic barriers that can slow down modular projects.
Perception and Acceptance
Despite its advantages, modular construction still faces scepticism from some consumers and industry professionals. Concerns about quality, design flexibility, and resale value persist, even as evidence mounts that modular homes can match or exceed the performance of traditionally built homes. Educating the market and showcasing successful modular projects are critical steps in changing these perceptions.
Additionally, architects and designers are increasingly embracing modular construction, creating aesthetically pleasing and functional designs that dispel the myth of "cookie-cutter" modular homes.
Transportation and Logistics
Transporting large building modules from the factory to the construction site presents logistical challenges. Modules must be carefully designed to withstand transportation stresses and fit within legal size limits for road travel. Additionally, the final assembly site must be easily accessible to accommodate the delivery and installation of the modules.
Innovations in transportation and logistics are helping to mitigate these challenges. Specialised transport vehicles and equipment are being developed to handle larger and more complex modules. Moreover, strategic planning and coordination with local authorities can ensure smooth delivery and installation processes.
In some cases, modular construction companies are establishing regional factories to reduce transportation distances and costs, further enhancing the feasibility of modular projects.
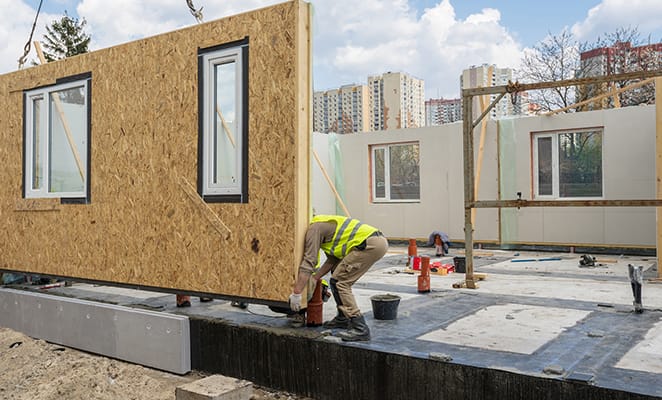
Case Studies: Successful Modular Projects
Examining successful modular construction projects provides valuable insights into the potential of this building method. Here are a few notable examples:
Project 1: Affordable Housing Initiative
By utilising factory-built modules, the project reduced construction time by 40% and costs by 20%, enabling the city to address its housing shortage more effectively. The modular approach allowed for the rapid deployment of housing units, providing much-needed relief to residents in need.
In addition to speed and cost savings, the modular housing units were designed with sustainability in mind. Energy-efficient materials and systems were incorporated, reducing the environmental impact and operational costs for residents. The success of this initiative has inspired other cities to consider modular construction as a viable solution for their housing challenges.
Project 2: Luxury Modular Homes
Contrary to the perception that modular homes are limited in design, a luxury home builder utilised modular construction to create high-end, customised homes. The factory setting allowed for precise craftsmanship and attention to detail, resulting in homes that rival traditional luxury builds in quality and aesthetic appeal.
These luxury modular homes feature high-end finishes, custom cabinetry, and state-of-the-art appliances, demonstrating that modular construction can meet the demands of discerning buyers. The ability to control construction conditions in the factory also ensures that the highest standards of quality are maintained throughout the building process. As a result, luxury modular homes are gaining acceptance among affluent buyers looking for unique and well-crafted residences.
Project 3: Sustainable Community Development
A developer focused on sustainability leveraged modular construction to build an eco-friendly community. The factory-controlled environment minimised waste and optimised material usage, while the speed of construction reduced the project's overall environmental impact. The development included energy-efficient features and sustainable materials, demonstrating modular construction's potential for green building.
The community features renewable energy sources such as solar panels, rainwater harvesting systems, and green roofs, contributing to a lower carbon footprint. The use of sustainable materials, such as reclaimed wood and recycled steel, further enhances the environmental benefits of the project. Residents of this community enjoy lower utility bills and a healthier living environment, showcasing the long-term advantages of sustainable modular construction.
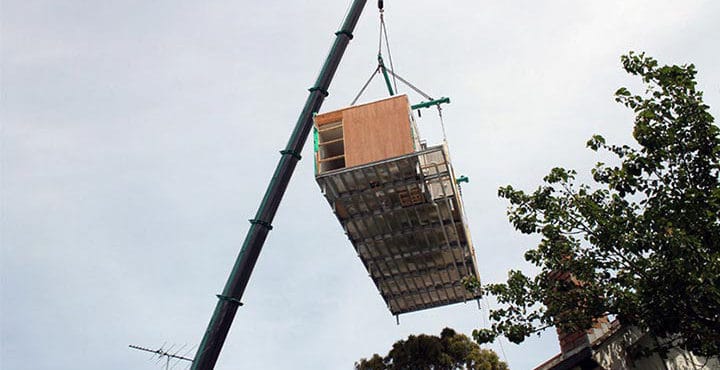
The Future of Modular Construction
The future of modular construction looks promising, with several trends indicating continued growth and innovation in the industry.
Integration with Technology
Advancements in technology are enhancing the capabilities of modular construction. Building Information Modeling (BIM) allows for precise digital representations of building components, facilitating better planning and coordination. Additionally, automation and robotics in factories can further improve efficiency and quality control.
For example, automated machinery can perform repetitive tasks with high precision, reducing the risk of human error and increasing production speed. Robotics can handle complex assembly processes, ensuring that each module is constructed to exact specifications. These technological advancements are making modular construction more competitive with traditional building methods, driving further adoption in the industry.
Customisation and Flexibility
As modular construction techniques evolve, the ability to customise and adapt designs is expanding. Home buyers can now choose from a wide range of layouts, finishes, and features, making modular homes more appealing to a broader audience. This flexibility addresses one of the main concerns about modular construction's perceived limitations in design.
Modular construction companies are partnering with architects and designers to create customisable options that cater to diverse tastes and preferences. Buyers can select from various floor plans, exterior finishes, and interior designs, ensuring that their modular home reflects their personal style. This level of customisation is helping to dispel the notion that modular homes are limited in creativity and uniqueness.
Collaboration and Partnerships
Collaboration between modular construction companies, architects, and developers is fostering innovation and expanding the market. By working together, these stakeholders can overcome regulatory challenges, streamline processes, and create compelling modular building solutions.
For instance, partnerships with local governments and housing authorities can facilitate the approval process and secure funding for modular projects. Collaboration with technology providers can enhance the integration of smart home features and energy-efficient systems. These partnerships are driving the evolution of modular construction, making it a more viable and attractive option for home buyers and builders alike.
Focus on Sustainability
Sustainability remains a key driver for the adoption of modular construction. The reduced waste, energy efficiency, and shorter construction timelines associated with modular building align with the growing demand for environmentally friendly housing. As sustainability becomes a priority for consumers and policy-makers, modular construction's eco-friendly attributes will continue to drive its popularity.
In addition to environmental benefits, modular construction offers social and economic advantages. The ability to quickly provide affordable and high-quality housing can address pressing social issues such as homelessness and housing affordability. Moreover, the economic impact of modular construction extends beyond the building site, creating jobs in manufacturing, transportation, and related industries.
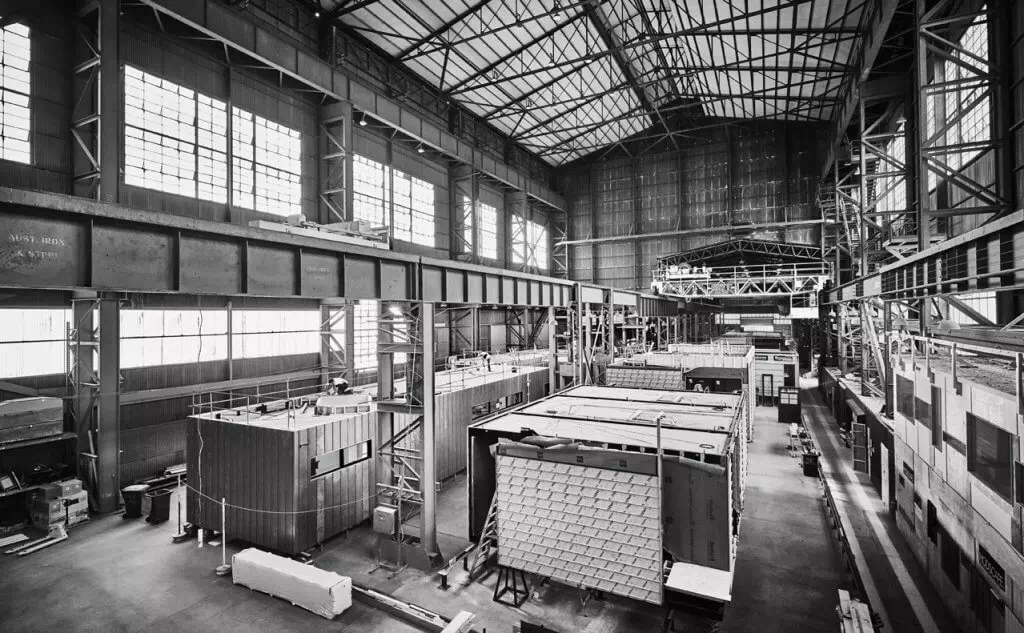
The Debate Over Labour Costs in Modular Construction
Detractors of modular construction often argue that centralising workers in a factory environment is primarily a strategy to reduce skilled labour costs, thereby increasing profit margins for construction companies. This perspective suggests that the move towards factory-based production is less about efficiency and quality control and more about minimising labour expenses by employing lower-wage workers. To fully understand this argument, it is essential to consider both sides of the debate.
The Case Against Centralising Labor
Critics claim that the primary motivation for shifting to factory environments is cost reduction, which can lead to lower wages for workers. In traditional construction, skilled tradespeople such as carpenters, electricians, and plumbers command higher wages due to their specialise skills and on-site expertise. By centralising the workforce in a factory, companies can potentially hire less experienced workers to perform more repetitive tasks, thus reducing overall labour costs.
Additionally, detractors argue that this shift can undermine the quality of craftsmanship. Skilled tradespeople bring years of experience and nuanced understanding to their work, which can be difficult to replicate in a factory setting with less experienced labour. There is also concern about the potential for job displacement among traditional tradespeople, who may find fewer opportunities as the industry moves towards modular construction.
The Case for Centralising Labour
On the other hand, proponents of modular construction highlight several benefits of centralising labour in a factory environment. Firstly, the factory setting allows for better training and supervision, ensuring that workers, regardless of their initial skill level, adhere to stringent quality standards. This controlled environment can lead to higher consistency and precision in building components, which is often harder to achieve on traditional construction sites.
Furthermore, factory-based construction can offer more stable and predictable working conditions. Unlike on-site construction, which is subject to weather delays and safety hazards, factory environments provide a safer and more controlled workplace. This stability can lead to higher job satisfaction and retention, even if wages are lower than those of traditional skilled tradespeople.
Proponents also argue that the shift towards factory labour does not necessarily mean a reduction in overall skill requirements. Instead, it involves a reallocation of skills. While fewer high-skilled tradespeople may be needed on-site, there is still a demand for skilled workers in factory settings, including those who operate sophisticated machinery and oversee quality control processes. Additionally, the growth of modular construction can create new job opportunities in manufacturing, logistics, and design, potentially offsetting any job losses in traditional construction.
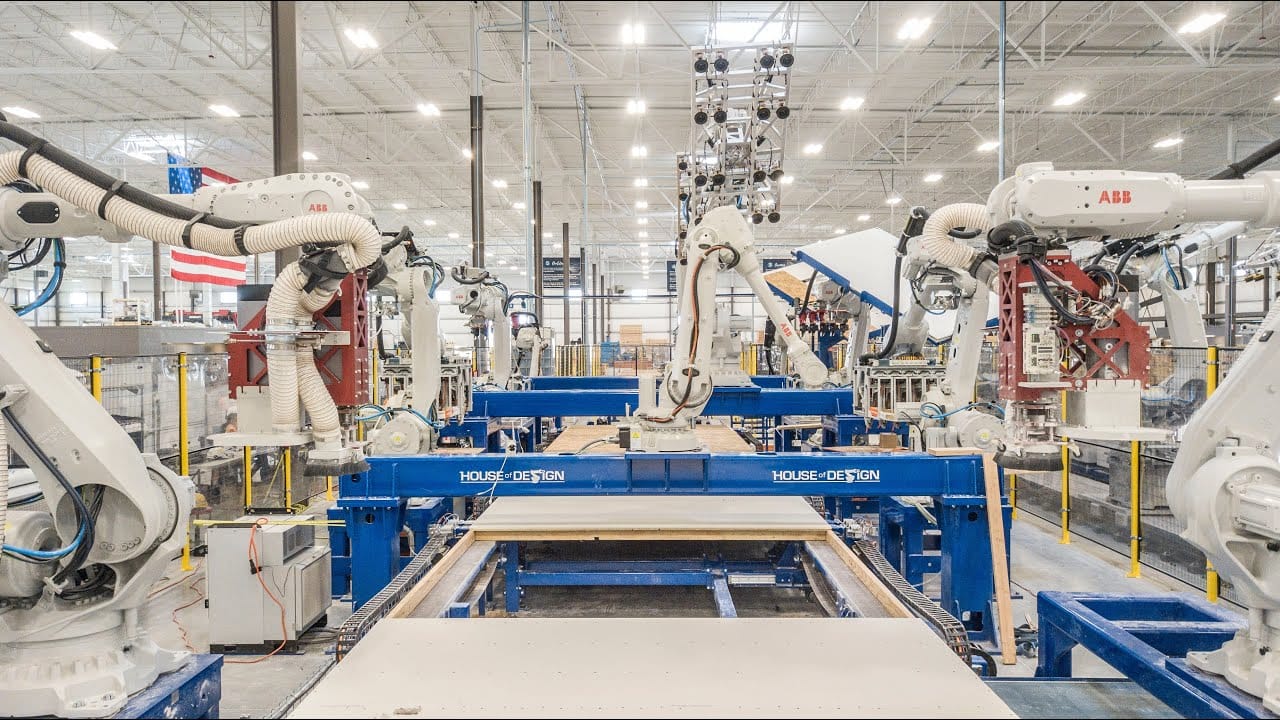
Case Study: AutoVol's Impact on Modular Construction
AutoVol, a leading innovator in the modular construction industry, exemplifies the transformative potential of this building method. Based in the United States, AutoVol specialises in automating the production of modular housing components, leveraging advanced robotics and automation technologies to enhance efficiency and quality. Their state-of-the-art facility integrates Building Information Modeling (BIM) and robotic assembly lines, enabling precise and consistent construction of modular units. By significantly reducing labour costs and construction timelines, AutoVol addresses the skilled labour shortages and high demand challenges prevalent in the housing market. The success of AutoVol demonstrates how automation and modular construction can work together to deliver high-quality, affordable housing solutions, setting a new standard for the industry.
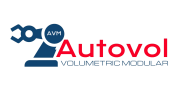
Leading the way in modular construction and building technology
Balancing Perspectives
The debate over labour costs and centralisation in modular construction is complex, with valid points on both sides. While cost reduction is undoubtedly a factor, it is not the sole driver of the shift towards modular construction. The benefits of increased efficiency, quality control, and safety cannot be overlooked. However, it is crucial for the industry to address concerns about fair wages and job displacement, ensuring that the transition to modular construction is balanced and equitable.
By fostering transparent communication between stakeholders—builders, workers, and policy-makers—the industry can work towards solutions that benefit all parties. This might include investment in training programs to upskill workers, ensuring fair labour practices in factory settings, and promoting the advantages of modular construction to both consumers and the workforce.
Ultimately, the success of modular construction depends on its ability to deliver high-quality, cost-effective housing while also supporting a skilled and fairly compensated workforce. By addressing these challenges head-on, modular construction can continue to change the building industry for the better.
Comparing Modular and Traditional Project Builder Homes in Australia
When comparing modular construction to traditional project builder homes in Australia, several key differences emerge in terms of process, time, cost, and quality. Modular construction involves manufacturing building components in a factory setting, which are then transported to the site for assembly. This controlled environment allows for simultaneous site preparation and module fabrication, significantly reducing construction time—often by 30% to 50%. In contrast, traditional project builder homes rely on sequential on-site construction, which can be delayed by weather conditions and labour shortages, resulting in longer build times.
Cost-wise, modular homes can offer savings due to the efficiency of factory production and reduced labour requirements. However, initial setup and transportation costs must be considered. Traditional project builder homes may have higher labour costs due to the need for skilled tradespeople on-site and potential delays, but they benefit from established supply chains and economies of scale that can also keep costs competitive.
Quality is another crucial differentiator. Modular homes benefit from the precision and consistency of factory conditions, minimising defects and ensuring that each module meets strict quality standards. Traditional project builder homes, while capable of high-quality outcomes, are more susceptible to variability due to on-site conditions and differing levels of craftsmanship. Both methods strive for excellence, but modular construction’s inherent control over the building environment often results in higher consistency and reliability.
Conclusion
Pre-made and modular construction are transforming the way we build homes, offering significant advantages in a high-demand, skilled labour-shortage market. By addressing challenges related to labour shortages, construction timelines, and quality control, modular construction provides a viable and attractive alternative to traditional building methods. As the industry continues to innovate and adapt, modular construction is poised to play a crucial role in meeting the housing needs of the future.
For first-time home builders, understanding the benefits and challenges of modular construction is essential in making informed decisions. By considering modular options, prospective home owners can take advantage of faster build times, consistent quality, and potentially lower costs, making their dream of owning a home more achievable.
However, it is also important to acknowledge the debate over labour costs in modular construction. Critics argue that centralising workers in a factory environment is a strategy to reduce skilled labour costs, potentially leading to lower wages and diminished craftsmanship. On the other hand, proponents highlight the benefits of better training, supervision, and safer working conditions in factory settings. Balancing these perspectives is crucial for the industry's growth and sustainability.
As the market evolves, staying informed about the latest trends and developments in modular construction will be key to navigating this dynamic and promising sector. Whether driven by necessity, innovation, or sustainability, modular construction is undoubtedly changing the way we build for the better. By addressing concerns about labour practices and ensuring fair compensation and opportunities for all workers, the industry can foster a more inclusive and equitable future.
With the growing popularity of modular construction, it is important to keep an eye on emerging technologies and industry trends that will shape the future of home building. As more builders and buyers embrace this innovative approach, modular construction will continue to evolve, offering even greater benefits and opportunities for those looking to enter the housing market.
By staying informed and exploring the possibilities of modular construction, first-time home owners can make well-informed decisions that align with their goals and values.
Whether your seeking affordability, sustainability, or speed, modular construction offers a promising path forward in the ever-changing landscape of residential construction.