The title feels like something straight out of a neo-noir film, like Sin City. But if we renamed it The CINS of My Builder, well… now it sounds like an adult movie mashup of Desperate Housewives and a dodgy renovation show featuring those 'buff' presenters with square jawlines.
You know the type.
What is the CINS System?
The Construction Inspection Numbering System (CINS) is a practical tool designed to improve the tracking, management, and resolution of non-conformance (NCR) items in construction projects. It provides a systematic way to physically tag and digitally document quality issues, ensuring they are identified, communicated, and resolved efficiently.
When conducting quality inspections, site supervisors or quality managers use the CINS system to label issues with unique identifiers. These tags, made from waterproof paper, are attached directly to the NCR item using various methods depending on the material and location:
- Cloth tape for sealed external elements.
- Masking tape for delicate internal elements, such as painted surfaces.
- Staples or clouts for timber or similar materials.
- Zip ties for elements where a tie can be secured, like reinforcement, around brackets etc.
The tagged issue is then logged into a digital system, along with photographs and detailed notes. This systematic approach makes it easier for contractors or tradespeople to locate, understand, and address the problem efficiently.
Key Features of the CINS System:
- Physical Tagging: Non-conformance items are marked with visible, durable tags that can be attached using cloth tape, staples, or nails, depending on the item’s nature.
- Unique Identifiers: Each tag includes a unique number that corresponds to a specific issue or checklist item, avoiding confusion and ensuring precise tracking.
- Digital Integration: Photos and notes are captured with mobile devices, linking the physical tag to a digital quality control system.
- Accountability: The system streamlines communication, ensuring the issue is brought to the attention of the appropriate person for resolution.
Benefits of Using the CINS System:
- Organised documentation of NCR items.
- Faster identification and resolution of quality issues.
- Enhanced accountability for trades and contractors.
- Improved transparency for homeowners.
The CINS system bridges the gap between physical site inspections and digital project management, making it an essential tool for ensuring quality in residential construction.
TLDR
If your like me, and often have the attention span of a gnat, then fear not. Login as a site member then click the button below to navigate to the Constructor Quality Management Checklist Page where you will find the download link to the CINS numbering along with a short version instructions on how to use them.
Introduction to Stage Quality Management Checklists
Stage quality management checklists are structured tools used during specific phases of construction to ensure that all elements meet required standards before proceeding to the next stage. These checklists are vital for maintaining construction quality, safety, and compliance, especially in residential projects.
One example is the Slab Inspection Checklist, which serves as a comprehensive guide for assessing critical elements of the slab stage. This includes ensuring proper site preparation, verifying materials, and checking compliance with engineering specifications. The checklist is designed to identify and resolve issues before irreversible work, like pouring concrete, begins.
Why Use Stage Quality Management Checklists?
- Consistency: They provide a standardised approach to inspections, reducing the likelihood of overlooked items.
- Accountability: Checklists clearly document what was inspected, who performed the check, and any issues identified.
- Prevention: They help catch errors or non-compliance early, saving time and money on rework later.
- Confidence: For homeowners, checklists provide peace of mind that their project is progressing according to plan and to a high standard.
Key Components of a Stage Checklist:
- Sections: Each checklist is divided into categories, such as housekeeping, visual inspections, services, and final notes. These focus on specific elements relevant to the construction stage.
- Status Tracking: Items are marked as "OK," "Delay," or "Issue + Follow-Up," providing clear indicators of progress and areas needing attention.
- Actionable Notes: Space for observations, notes, and follow-up actions ensures thorough documentation of findings.
By incorporating checklists at every stage, builders and quality controllers create a systematic process that ensures compliance and quality from start to finish.
How CINS and Checklists Work Together
The integration of the Construction Inspection Numbering System (CINS) with stage quality management checklists creates a seamless process for identifying, tracking, and resolving non-conformance (NCR) items on a construction site. This partnership allows for efficient documentation, clear communication, and systematic resolution of issues, ensuring that each stage of construction meets the required standards.
Step 1: Identifying NCR Items
- During a site inspection, quality controllers use the stage checklist (e.g., Slab Inspection Checklist) to systematically assess all required elements.
- Any item that does not meet the checklist criteria is classified as a non-conformance (NCR) item. Examples include improperly placed reinforcement bars or incomplete plumbing penetrations.
Step 2: Tagging NCR Items with CINS
- Each NCR item is tagged with a unique CINS identifier.
- Tags are attached physically to the item using non-destructive methods like cloth tape or staples, ensuring they remain visible and durable.
- The identifier corresponds to a specific checklist item for easy reference.
Step 3: Capturing and Logging NCR Items
- Using a mobile device or digital camera, inspectors take photos of the tagged NCR items, ensuring the CINS identifier is visible in the image.
- Notes detailing the issue, its location, and required corrective actions are recorded in the digital system alongside the photos.
Step 4: Communicating Issues
- The NCR report, complete with photos, checklist references, and action notes, is shared with the responsible contractor or trade.
- This communication is typically digital, ensuring prompt notification and accountability.
Step 5: Tracking Progress
- As contractors address the issues, they take compliance photos, showing the corrected item with the CINS tag still in place.
- These photos are sent back to the quality controller, who updates the checklist and digital records.
Step 6: Achieving Checklist Compliance
- Once all NCR items for a stage are resolved, the checklist is reviewed and finalised.
- Any remaining issues are followed up until the stage is fully compliant, ensuring no unresolved items are carried forward.
An Example Workflow: Slab Stage
- A quality controller finds that reinforcement mesh spacing is incorrect (checklist item S4.1).
- The issue is tagged with CINS identifier #10, and a photo is taken.
- The issue and photo are logged into the digital system and sent to the concreting contractor.
- The contractor corrects the mesh spacing, takes a compliance photo showing the #10 tag, and submits it for review.
- The quality controller verifies the correction and marks S4.1 on the checklist as compliant.
Key Benefits of Integration
- Clarity: The unique CINS tags eliminate confusion, ensuring that issues are accurately identified and tracked.
- Efficiency: Digital logging and communication speed up the resolution process.
- Accountability: All actions are documented, providing a clear audit trail for stakeholders.
- Easy: a simple numbering system is the easiest way for internal and external users to identify and track NCR items. Having the flexibility to use tape to adhere CINS numbers, or penetrate and affix CINS with staples, nails, zip ties makes CINS and extensible and malleable QC system,
By combining CINS with stage checklists, quality management becomes a streamlined process that is easy to follow, even for complex projects.
Practical Application – Slab Stage Example
To illustrate how the CINS system integrates with stage quality management checklists, let’s look at its use during the slab stage of residential construction. This phase is absolutely critical to get right, as the slab forms the foundation for the entire structure, and any errors at this stage can lead to costly rework or long-term issues.
Step 1: Conducting the Inspection
- The quality controller begins by using the Slab Inspection Checklist, systematically reviewing each section:
- Housekeeping (Section S1): Checking sediment fences, site cleanliness, and erosion control measures.
- Services and Specific Elements (Section S2): Verifying placement of plumbing and electrical conduits.
- Engineering Details (Section S4): Inspecting reinforcement mesh, trench mesh, and corner bar placements.
- Each checklist item is assessed, and non-conforming items are noted.
Step 2: Tagging Non-Conformance Items
- For example, the inspector notices that the reinforcement mesh does not meet the required spacing of 200mm (Checklist Item S4.1).
- The item is tagged with a CINS identifier, such as #201, using a cable tie to attach the label directly to the reinforcement.
Step 3: Capturing and Logging the Issue
- A photo of the non-conformance is taken with a mobile device, clearly showing the CINS tag #201.
- Notes are added, such as "Reinforcement mesh spacing exceeds 200mm; needs adjustment to meet specifications."
- The issue is logged in the digital quality management system, linking it to the corresponding checklist item (S4.1).
Step 4: Communicating the Issue
- The report, including the photo and notes, is sent to the concreting contractor responsible for the slab work.
- A deadline for resolving the issue is provided to ensure the slab pour is not delayed.
Step 5: Resolving and Verifying the Issue
- The contractor adjusts the reinforcement mesh to meet the specified spacing and takes a compliance photo, ensuring the CINS tag #201 remains visible.
- This photo is sent back to the quality controller for review.
Step 6: Finalising Checklist Compliance
- The quality controller reviews the compliance photo and verifies that the issue has been resolved.
- Checklist item S4.1 is marked as compliant, and the slab stage progresses toward approval for the concrete pour.
Additional Applications at the Slab Stage
- Tagging plumbing penetrations requiring adjustments (e.g., Checklist Item S2.7).
- Identifying issues with damp-proof membrane placement (Checklist Item S2.13).
- Verifying proper alignment of formwork and boxing (Checklist Item S5.2).
By applying this method at the slab stage, builders and quality controllers can ensure that all elements are compliant, setting a strong foundation for subsequent construction stages.
Managing NCR Items with Digital Tools
Digital tools play a helpful role in enhancing the effectiveness of the Construction Inspection Numbering System (CINS) and stage quality management checklists. By integrating mobile devices and software platforms, the process of tracking, communicating, and resolving NCR items becomes streamlined, reducing delays and ensuring high-quality outcomes.
1. Capturing NCR Items on Mobile Devices
- Inspectors use smartphones or tablets to take clear, high-resolution photos of NCR items, ensuring the CINS tag is visible.
- Notes describing the issue are added directly into the digital system, linked to the corresponding checklist item.
- Apps or software platforms often allow audio recordings or voice-to-text features for on-the-go documentation.
2. Centralised Data Management
- Digital platforms act as a central hub for all NCR-related data, including photos, notes, and checklist progress.
- Cloud-based systems ensure that information is accessible in real-time to all stakeholders, including quality controllers, contractors, and project managers.
- Each tagged item is indexed under its unique CINS identifier, making it easy to search and retrieve information.
3. Real-Time Communication
- Once an issue is logged, the digital system automatically generates a report, complete with photos, notes, and a checklist reference.
- This report is sent to the responsible party (e.g., contractors or tradespeople) via email or in-app notifications.
- Real-time updates allow stakeholders to respond promptly, reducing the likelihood of delays.
4. Tracking Progress
- As contractors address NCR items, they upload compliance photos showing the corrections made, with the CINS tag still in place.
- The quality controller reviews these photos and updates the checklist to reflect the resolved status.
- Progress dashboards provide an overview of outstanding issues, resolved items, and overall compliance status for each construction stage.
5. Reporting and Documentation
- At the end of each stage, a detailed report is generated, summarising all NCR items and their resolution.
- This report serves as a record of quality control, which can be shared with homeowners, project managers, or regulatory authorities.
- Homeowners benefit from transparency, knowing their project adheres to high standards.
Recommended Tools for Digital Quality Management
- Inspection Apps: Platforms like iAuditor or PlanGrid, Fieldwire, Insite or Smartsheet offer intuitive interfaces for logging and managing NCR items.
- Photo Annotation Tools: Apps that allow text or drawing overlays on photos for added clarity.
- Cloud-Based Collaboration Tools: Software like Procore ensures real-time sharing and tracking of NCR data.
Advantages of Digital Integration
- Efficiency: Automates repetitive tasks like report generation and communication.
- Accuracy: Reduces human error by centralising and standardising data entry.
- Transparency: Provides all stakeholders with visibility into the quality management process.
- Time Savings: Speeds up the resolution process by eliminating the need for manual tracking.
By incorporating digital tools into the CINS and checklist system, construction teams can improve their workflow, minimise rework, and deliver projects that meet or exceed quality standards.
Key Advantages of the CINS System with Checklists
Integrating the Construction Inspection Numbering System (CINS) with stage quality management checklists offers a range of benefits for homeowners, contractors, and project managers. By combining physical tagging, digital tools, and structured checklists, this system addresses common challenges in quality control while enhancing overall project efficiency.
1. Enhanced Accountability
- The use of CINS tags ensures every NCR item is assigned a unique identifier, making it easy to track responsibilities.
- Contractors and tradespeople are held accountable for resolving specific issues within their scope of work.
- All actions, from tagging to resolution, are documented, creating a transparent audit trail.
2. Improved Efficiency
- The combination of physical tagging and digital integration speeds up the process of identifying and resolving issues.
- Real-time communication between quality controllers and contractors reduces delays caused by miscommunication.
- Checklists provide a systematic approach to inspections, ensuring no critical items are overlooked.
3. Reduced Costs
- Early identification and resolution of NCR items prevent costly rework later in the construction process.
- By ensuring compliance at each stage, the system minimises the risk of project delays, which can lead to increased labour and material costs.
- Digital tools reduce the need for manual paperwork, saving time and administrative expenses.
4. Increased Transparency for Homeowners
- Homeowners gain visibility into the quality management process through detailed reports and updates.
- They can see exactly what issues have been identified and how they have been resolved, fostering trust in the construction team.
- Clear documentation of quality control provides reassurance that the project meets high standards.
5. Better Quality Assurance
- By linking CINS tags to specific checklist items, the system ensures that all identified issues are directly addressed and verified.
- Compliance photos taken during and after resolution add an extra layer of quality assurance.
- Finalised checklists confirm that each stage of construction meets industry standards before progressing.
6. Simplified Workflow for Complex Projects
- For larger or more complex residential builds, the CINS system helps streamline the inspection and resolution process.
- Centralised digital records allow project managers to monitor progress across multiple stages or sites, ensuring consistency and quality.
Real-Life Benefits in Action
- Example 1: A homeowner is concerned about potential defects in their slab stage. With the CINS system, they receive a report showing tagged NCR items, photos of corrections, and a checklist confirming compliance before the slab pour.
- Example 2: A contractor needs to address several plumbing penetration issues. The tagged items and associated checklist provide clear instructions, allowing them to resolve the issues efficiently and meet deadlines.
Why It Matters The integration of CINS and checklists goes beyond meeting compliance requirements—it ensures that every element of the construction process is approached with precision, care, and accountability. For homeowners, this means peace of mind; for contractors, it means delivering a superior product.
Why You Should Care
As a homeowner, you may feel disconnected from the technical aspects of your construction project, leaving you unsure whether the work being done meets the required standards. This is where tools like the Construction Inspection Numbering System (CINS) and our stage quality management checklists become invaluable.
These systems ensure that every phase of construction is inspected, documented, and compliant before proceeding, providing you with transparency and confidence in your investment.
1. Protecting Your Investment
- Poor construction quality can lead to costly repairs, reduced property value, or even safety hazards.
- By ensuring compliance at every stage, CINS and checklists protect your investment and minimise the risk of future issues.
2. Gaining Transparency
- You have the right to know what’s happening on your site.
- With CINS and checklists, you can review reports, photos, and progress updates, giving you a clear picture of how your project is unfolding.
3. Ensuring Accountability
- These systems create a detailed record of inspections and resolutions.
- If disputes arise about quality or compliance, this documentation provides undeniable evidence of what was done and when.
4. Avoiding Delays
- Catching and resolving issues early helps avoid costly delays later in the project.
- The CINS system streamlines communication between your builder, contractors, and quality controllers, ensuring that work progresses efficiently.
5. Peace of Mind
- Knowing that a structured quality management system is in place can significantly reduce stress during the construction process.
- You’ll have confidence that your home is being built to the highest standards.
How to Ensure Your Builder Uses These Systems
- Ask Questions: Inquire whether your builder uses a quality management process like CINS and checklists.
- Request Updates: Ask for regular reports and photos showing tagged NCR items and resolved issues.
- Monitor Compliance: If possible, visit the site during inspections or ask your builder to explain how quality is managed.
A Homeowner’s Perspective Imagine receiving a report from your builder detailing all quality checks completed during the slab stage. You see tagged items, photos of corrections, and notes confirming compliance. Not only does this assure you that everything is on track, but it also allows you to understand the work being done on your future home.
Empowering You Understanding and supporting these systems isn’t about micromanaging your builder—it’s about empowering yourself as a homeowner to stay informed and involved in your project. With tools like CINS and checklists in place, you can feel confident that your dream home is being built with care and precision.
Conclusion
Building a home is one of the most significant investments you’ll ever make, and ensuring that your project meets the highest standards of quality is essential. The Construction Inspection Numbering System (CINS) and stage quality management checklists are invaluable tools that make this possible.
By combining physical tagging, digital documentation, and systematic checklists, these systems streamline the identification and resolution of quality issues at every stage of construction. Whether you’re a homeowner, builder, or contractor, the benefits are clear—improved efficiency, greater transparency, and enhanced accountability.
For homeowners, understanding how these systems work provides peace of mind. You’ll know that each stage of your project is being inspected and that any non-conformance items are resolved before moving forward. For builders, adopting CINS and checklists demonstrates a commitment to delivering quality outcomes, fostering trust and satisfaction among clients.
Take an active role in your project by asking about the quality management process, reviewing reports, and staying informed. Your dream home deserves nothing less than excellence.
Further Reading
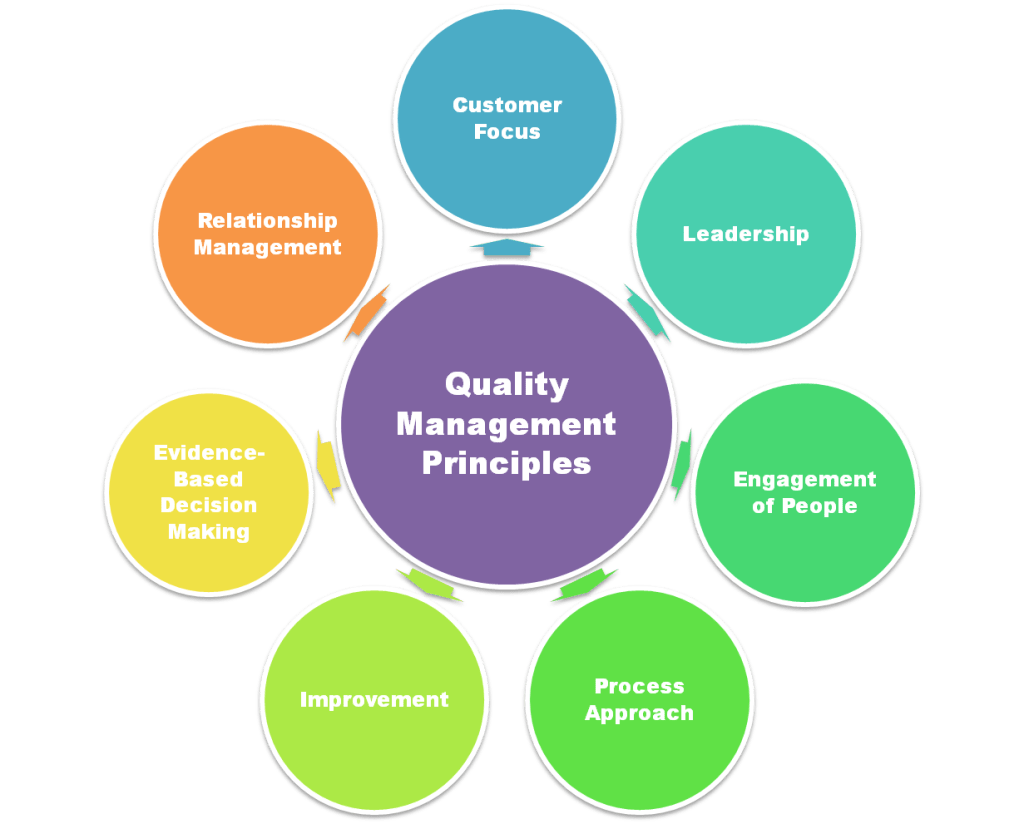
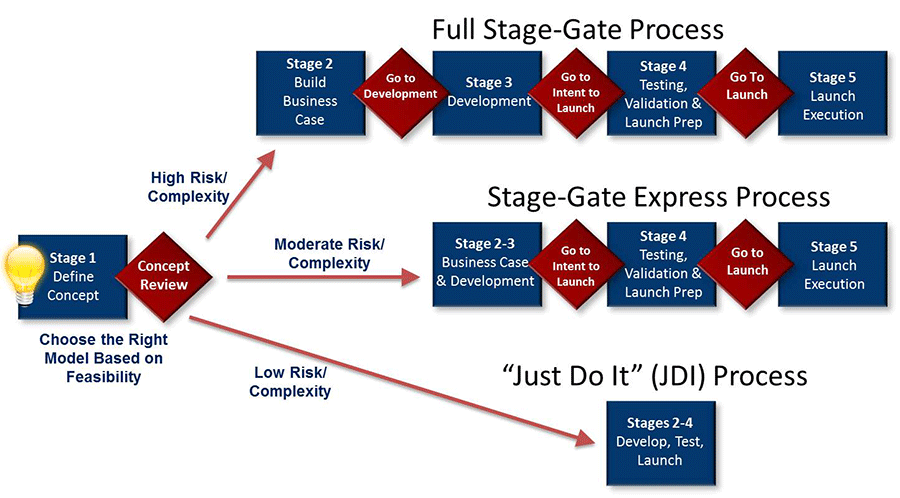