Have you ever looked at a house at frame stage and seen that plastic looking sheet flapping in the breeze around the outside of the frame? That's wall wrap, and chances are it was installed incorrectly.
As a home owner, you expect your house to be built to standards to ensure it's structurally sound and energy efficient.
However, many builders take shortcuts with wall wrap installation to save time and money. The truth is, installing wall wrap incorrectly can compromise the building envelope and energy efficiency of your home.
In this article, we'll walk through the proper way to install "wall wrap" according to Australian Standard AS4200.2 (Pliable Membranes Installation).
You'll learn the correct sequence to install windows, doors and wall wrap so you can make sure your builder or reno team does it right. After all, your home is a big investment, so it's worth getting the details right.
Builders nominating "reflective foil" or "reflective wall wrap" is wrong. Why this is non-compliant design to AS4200.2 and AS4859.1
First things first, many project builders are not correctly specifying wall wrap (in the specification). Reflective foil is often mentioned in specifications, and this is not a term that is referenced in AS4200.2 Pliable Membranes. One of the first things that AS4200.2 mentions is:
The design shall specify the purpose and required properties of the membrane, selected in accordance with AS4200.2
This means that when a pliable membrane is incorporated into a house it is the responsibility of the designer to specify the type of membrane being used.
There are four main types of pliable membranes. These are Air, Water, Thermal and Vapour. So when a builder says "reflective foil" which type of membrane do they mean and have they designed for? As I'm sure you can infer, there are a lot of differences between the installation of each barrier type, which also means cost implications.
Simply put, reflective foil is a term used to describe the material that a pliable membrane can be made of, but unless a type of barrier is nominated by the designer in the specification, how does anyone know what they are getting, for what reason its being used and how it should be installed properly to achieve the design outcome?
Similarly, AS4859.1 Materials for the thermal insulation of buildings says the following on this matter:
"Reflective insulation falls into one of the following product groups:
- (a) Group 1 Pliable building membranes that have at least one reflective surface. If the products within this group are installed facing an appropriate airspace, they may provide thermal insulation. If they are marketed for this property, the requirements of this Standard shall apply. NOTE: These products are often intended to have a prime function as a sarking or vapour barrier. For this application, test methods, performance classifications and installation requirements are covered by AS/NZS 4200.1 and AS/NZS 4200.2."
So, what does this mean then? I interpret this to mean that "reflective foil" when mentioned in a specification is a THERMAL BARRIER.
This means it must be installed in accordance with AS4200.2 Pliable Membranes thermal barrier installation requirements.
If you'd like to read more about this, check out our other blog post title: The Problem With “Reflective Wrap”: How Ambiguity Allows Project Builders to Avoid Responsibility.
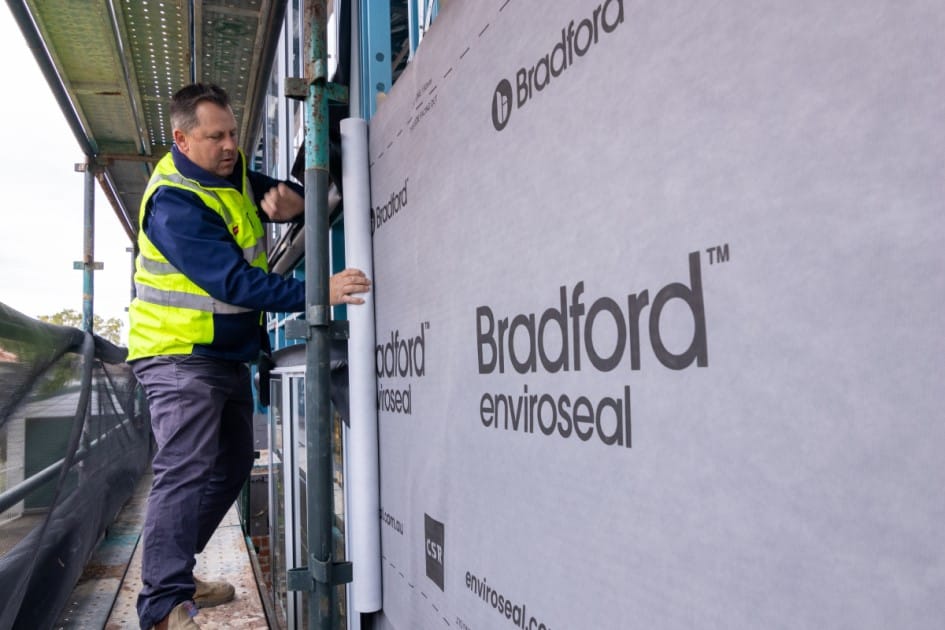
The Typical Wall Wrap, Window and Door Installation Sequence
The typical sequence for installing wall wrap, windows and doors goes like this:
- Install the windows and doors. The windows and doors are put in place inside the openings in the framing.
- The wall wrap is then wrapped around the edge of the windows and doors and stapled in place.
The problem with this method is that it goes against Australian Standard AS4200.2 which states that “membranes shall be installed prior to the installation of windows and doors”. Installing the windows and doors first leaves gaps and tears in the wall wrap that compromise the water resistance and air barrier.
The Correct Sequence
The proper sequence for installation (for a vapour barrier) should be:
- Install the wall wrap covering the entire wall, including over the window and door openings.
- Cut 'X's in the wall wrap at each corner of the openings. Fold the flaps inside and secure in place with tape.
- Install the windows and doors. Place them in the openings over the secured wall wrap.
- Seal and tape around the edge of the windows and doors to the wall wrap to create an air and water tight seal.
- Seal around penetrations through the wall wrap and ensure there are correct wrap overlaps of at least 150mm or less (50mm), where laps are tapped.
Following this method ensures maximum protection by providing an uninterrupted layer of wall wrap under and around the windows and doors.
AS4200.2-2017 says on this subject the following:
To meet AS4200.2-2017 for installation of membranes around windows:
- Sarking before window install, membrane must be sealed to the inner face of the stud framing and noggins.
- Sarking after window install: membrane must be tucked between window frame fin and reveal box, then taped to seal over fin. There is also a requirement for the membrane to be at least 1mm thick for this method to apply.
Regarding the second point, I've never seen a builder do the wrap tuck-and-tape thing around the window frame fin. It just doesn't happen. So, the only real solution is to install the sarking properly before installing the windows and doors into the framing.
Note: this is summarised on this CSR Bradford Technical sheet below in the notes close to the page bottom:
Finally, just on this CSR Technical Bulletin, the content is incorrect in its assertion that if the windows are already installed into the frame, the membrane can be tucked between the window frame fin and reveal box, then taped sealed over. Why,
it is incorrect is because in AS4200.2 it states that this can only be done when the membrane is at least 1mm thick.
Neither the Enviroseal or Thermoseal range of products are 1mm thick!
See below the technical data sheets for each of these products and on the last page of each it clearly says the product is <1.0mm thick
Enviroseal Technical Data Sheet
Thermoseal Technical Data Sheet
What the Australian Standards Say About Proper Wall Wrap Installation
So what do the Australian Standards actually say about properly installing wall wrap? Quite a bit, as it turns out.
According to AS4200.2, wall wrap should be installed continuously around doors and windows, with the edges taped for an air-tight seal.
Unfortunately, many builders simply cut holes in the wall wrap to install doors and windows, then try to patch around them. This leaves gaps, allowing air flow and moisture to penetrate the building envelope.
Using the proper sequence and technique will ensure no moisture or air leaks into your home, keeping the temperature regulated and foundation protected.
Here's what the standards say precisely for the different types of membranes (as they are specified):
Vapour control membranes: where a pliable membrane is installed as a vapour barrier, Class 1 or Class 2, it shall be continuously sealed at all discontinuities, end laps, joints and penetrations by one of the following: heat and moisture resistant tape, mechanical fixing with adhesive sealant, adhesive bond.
Aircontrol membranes: membrane shall be taped or sealed at overlaps, end laps, discontinuities and penetrations (same way as above)
Water control membrane: upper sheets shall lap over the lower sheets to ensure water is shed to the outside of the frame
Here are a few more details on how wall membranes must be installed as per AS4200.2:
- Walls lapped no less than 150mm
- or lapped no less than 50mm jointed and taped
- butt jointed and taped where the uncompressed nominal material thickness is greater than 5mm and overlapping will compromise the cladding installation
- all end laps shall be fixed to a stud to form a continuous membrane
- where installed on timber frame is shall be fixed using mechanical fixings at 150mm centres prior to cladding
Following the standards may require a bit more time and effort, but will reward you with energy efficiency, structural integrity, and lower utility bills for years to come.
See the following attachment from CSR Bradford showing the correct installation sequence/method.
Conclusion
While it may seem like extra effort, doing it correctly the first time will save you time, money and headaches down the track. Your home is a big investment, so make sure any work done on it complies with the standards and building codes.
Next time you're overseeing construction on your place, don't be afraid to double check that proper installation procedures are being followed.