Introduction: Australia’s Housing Challenge
If you’re an Australian homeowner, prospective buyer, or simply someone who follows the news, you’ve probably seen the headlines about housing affordability.
Prices keep climbing, supply can’t keep up with demand, and rent in many cities and regions is eye-wateringly expensive. The Australian Government has set a bold goal to build 1.2 million new homes in five years, hoping to ease these pressures. But there’s a big, often overlooked stumbling block according to the Productivity Commissions new report: low construction productivity.
So, what does “construction productivity” mean, and why does it matter for you?
In short, it’s about how efficiently builders and trades use their time, labour, and resources to build each home. If that process becomes faster and more cost-effective—while still meeting quality and safety standards—homes become more affordable and can be built in higher volumes.
A recent Productivity Commission research paper, “Housing Construction Productivity: Can We Fix It?”, shines a spotlight on exactly why our residential construction productivity is lagging and what can be done to fix it.
Key Takeaway:
Rising prices and slow housing supply mean we need better construction productivity to help fix Australia’s housing affordability crisis.
Section 1: Understanding Construction Productivity
1.1 What Is Construction Productivity?
In the simplest terms, productivity means how much output you get for a certain amount of input. When we say “construction productivity,” we’re talking about how many homes (output) can be built for each hour of labour or for each dollar spent on resources (input).
If you can build more dwellings with the same labour and materials, you’ve got productivity gains—and, usually, a dip in the overall cost per dwelling.
However, the construction industry is a tricky beast. Unlike manufacturing, where identical products roll off an assembly line, each home can be unique. It’s also heavily regulated because we all want homes to be safe, energy-efficient, and built to quality standards.
The Productivity Commission’s research shows that Australia’s housing construction productivity has declined by 12% over the past 30 years, while the broader economy’s productivity rose by nearly 49%. That’s a massive gap.
1.2 Why Should Homeowners Care?
You might be wondering: Why does this matter to me? The answer: costs, timelines, and affordability.
- Costs: Lower productivity can drive up the price of new homes, as builders need more labour hours to finish the same project.
- Timelines: Delays often stem from low productivity—more time dealing with approvals, staff shortages, or repeated re-work if standards aren’t met the first time.
- Home Value & Options: In a high-cost environment, buyers and builders cut corners or skip additional features that might otherwise have been affordable in a more productive system.
1.3 Productivity Trends in Housing Construction
The Productivity Commission dug into labour and output data from the Australian Bureau of Statistics. They found:
- Dwelling construction labour productivity (a measure of how many homes are built per hour of labour, adjusted for home quality) declined by about 12% in the past three decades.
- Physical productivity—the raw number of dwellings completed per hour of work—was down by 53% (though this figure does not adjust for improvements in quality and size).
- Meanwhile, the overall economy saw productivity increase by 49% over the same period.
These numbers are particularly stark for detached houses (houses have fared worse than apartments or townhouses in productivity). The higher-density sector (apartments, units, etc.) actually improved slightly at times, though overall still lagging behind the rest of the economy.
Key Takeaway:
Australia’s new dwelling productivity has declined 12% over 30 years, while overall economic productivity rose 49%. That’s a big gap—and it spells trouble for affordability.
Section 2: Why Is Housing Construction Productivity So Low?
In this section we dive deeper into the Productivity Commission’s main findings on the roadblocks to higher productivity.
2.1 Housing Construction’s Complexity
Building a home isn’t just about laying bricks. The entire pre-construction phase (land acquisition, surveys, planning approvals, environmental checks, financing) can stretch for quite a while. There are many agencies involved—local councils, state planning commissions, environmental authorities, utilities, and more.
When the Commission talks about “cascading failures,” they’re referring to how a delay at one step (say, a permit for electricity connection) pushes everything else back. Because building is so sequential—slabs before walls, walls before wiring—a single holdup compounds the total time needed.
Why does complexity matter for productivity? The more steps there are, the more likely you’ll face mis-coordination, repeated paperwork, or rework, all of which inflate project timelines and budgets.
2.2 The Burden of Regulation
Australia has three levels of government—federal, state or territory, and local—and they all have a say on what can be built, where, and how. That often means multiple development applications, environmental impact assessments, building code compliance checks, and so on.
Importantly, building codes (like the National Construction Code) change every few years. While changes often aim to improve safety or sustainability, these frequent updates:
- Create uncertainty for builders and developers.
- Make it risky to invest in new techniques because tomorrow’s code might not allow them or might force new compliance work.
- Force small firms to spend extra on compliance paperwork instead of focusing on the build.
2.3 Fragmented Industry Structure
Ever notice how many home building companies are quite small? We have an industry with lots of small builders—the average size is just 1.5–2 employees in many sub-sectors.
There’s heavy reliance on subcontractors (plumbers, electricians, plasterers, etc.). That’s partly because each building job is unique, and subcontracting trades is simpler than hiring them in-house. It’s also due to local variations in rules, which make it harder for any one builder to scale up nationwide.
What’s the productivity impact?
- Less standardisation: Hard to replicate the same efficient process from site to site.
- Weaker R&D capacity: Big firms can invest in tech (if they even do), but with so many small players, innovation efforts tend to be scattered and minimal.
2.4 Limited Innovation & Skills Shortages
Compared to other major industries, construction invests less in research and development. The Commission’s data shows that only about 35% of construction businesses report any form of innovation activity—much lower than other Australian sectors.
Prefabrication is a prime example. Building whole sections of a home off-site and shipping them in can drastically cut on-site labour. While it’s been successful in some countries, it hasn’t taken off widely here.
One big reason: financing and regulatory structures are geared toward traditional onsite builds. Another big reason: lack of large-scale players to push it forward.
Meanwhile, workforce issues abound:
- Ageing workforce? Actually, the sector is younger than the broader economy, but the supply of new apprentices is still tight.
- Occupational licensing differences across states hamper mobility for trades.
- Migration rules, until recently, weren’t friendly enough to the skilled trades we urgently need.
2.5 International Context
It’s not just Australia. Many advanced economies (like the US, UK, France, and Germany) also see construction productivity lagging behind other industries. Australia, however, is better than some peers on certain measures (like total construction cost or raw output), suggesting some universal challenges are at play—like building complexity, regulation, and workforce constraints.
Summary Point:
A fragmented market, high regulation, and limited innovation hamper construction efficiency—and in the end, everyday Australians shoulder the costs.
Section 3: How Better Productivity Can Solve Australia’s Housing Crisis
3.1 Affordability and Supply
When we talk about addressing the “housing crisis,” a big part of that means boosting supply to keep pace with population growth and demand. If the building process is more productive—meaning it takes fewer hours, fewer headaches, and less money per dwelling—more projects become economically viable. That directly impacts:
- Developers: They can take on more projects and build faster.
- Consumers: Fewer building cost blowouts, hopefully lower prices, and less risk that your off-the-plan build gets cancelled.
3.2 Boosting the Ambitious 1.2 Million Homes Goal
The Federal Government wants 1.2 million new homes built in five years. That’s 240,000 homes a year, compared to the 176,000 built in the year to June 2024. With better productivity, some of that shortfall closes as each new dwelling can be done more quickly without ballooning costs.
Imagine if the industry recaptured the productivity growth it had decades ago. The Commission estimates that if we matched the rate of growth seen in the broader economy, we’d be producing significantly more homes with the same workforce. That would go a long way toward hitting those new supply targets.
3.3 Key Productivity Drivers
So how do we get there? A few key drivers:
- Firm Scale: Encouraging the emergence of medium-to-large construction companies that can standardise processes.
- Modern Methods: Prefabrication and modular building, advanced digital tools, more project management software.
- Workforce Flexibility: Easing occupational licensing barriers across states and streamlining skilled migration for crucial trades.
- Better Regulation: Focusing on balancing legitimate safety, quality, and environmental standards with simpler, more uniform compliance.
Technical/Key Point:
Lifting construction productivity directly lowers building costs, creating more affordable homes and helping meet Australia’s ambitious supply targets.
Section 4: Policy & Industry Recommendations
The Commission lays out several policy directions—not quite formal recommendations but rather strong suggestions—for government and industry to consider.
4.1 Streamlining Planning and Approvals
Planning is typically done by local councils, which also coordinate with state and national agencies. This can lead to either:
- Fast-tracked developments in some regions, or
- Nightmare wait times in others, lasting months or years before ground is even broken.
The Commission says we should:
- Coordinate the Entire Process: One-stop or “concierge” services for developments, so there’s less confusion about who signs off on what.
- Adequately Fund Regulatory Bodies: Understaffed agencies can’t keep up with approvals. More staff = faster decisions = fewer project delays.
- Set Realistic Targets: Some states do measure how long local government takes to decide on building approvals, but the Commission wants that to happen consistently, with clear benchmarks.
4.2 Reforming Building Regulations
The National Construction Code (NCC) is an important part of ensuring safe, energy-efficient homes. But frequent updates—every three years, sometimes even mid-cycle—make it hard for the industry to adapt. The Commission suggests an independent review of building regulations that looks at:
- The regularity of updates (maybe not so often).
- The code’s objectives and if they sufficiently weigh housing affordability and supply in their cost-benefit analyses.
- Consistency across states—local governments shouldn’t override the NCC with extra rules that replicate the same goals in a slightly different way.
If new code changes are found to impose net costs, the Commission suggests exploring alternative, more flexible ways to achieve the same health, safety, or environmental outcomes.
4.3 Innovating Construction Processes
To tackle low innovation:
- Government-Funded Extension Services: Similar to agriculture, where “extension officers” help farmers adopt new tech. Something like an “AusIndustry extension program” can offer direct help to small builders on best practices for modern methods of construction.
- Public R&D Funding for Construction: Evaluate whether the industry deserves more dedicated R&D funding. It’s a big employer with a big impact on the economy.
- Rating Schemes: Offering star ratings for building quality, so better builders are rewarded by customers. For example, some states already have an energy-efficiency rating upon sale or lease.
4.4 Workforce & Training
Occupational Licensing and Mutual Recognition
Right now, states have their own licensing bodies for many trades. “Automatic mutual recognition,” introduced in 2021, aimed to let trades licensed in one state easily practice in another. Progress is patchy—some states fully participate, others have special exemptions. The Commission says, let’s get it consistent, because that will let workers move quickly to meet local shortfalls.
Migration
Recent changes allow more skilled tradespeople to come in, but there’s still complexity. The Commission would like to see simpler visa processes and better alignment so an overseas-trained carpenter or electrician doesn’t have to jump through separate hoops for both immigration and licensing.
Apprenticeships & Shorter-Form Training
Some of the Commission’s earlier reports recommended rethinking apprenticeship incentives and possibly creating micro-credentials for specialised tasks. This could encourage more people to try building trades if they don’t have to commit to four-year training programs to handle certain specialized tasks on-site.
Summary Point:
Streamlined approvals, consistent codes, and better workforce support can unleash the sector’s potential to build faster and more affordably.
Section 5: The Homeowner’s Perspective—Implications & Opportunities
Now let’s bring this down to a personal level. Suppose you’re looking to build or renovate a home.
5.1 Faster Project Approvals
When local councils and utilities have the right resources to process applications quickly, you:
- Spend less time in limbo awaiting building approvals.
- Face fewer “cascading delays” that run up your loan interest costs or living expenses while you wait to move in.
A properly defined and managed (communicated) communication management plan really helps here.
5.2 Access to Innovative Building Techniques
If prefabrication and modular building become more common, you could see:
- Shorter building times (a modular building can go up in weeks rather than months).
- Potential cost savings if economies of scale are achieved.
- Better quality control, because these homes can be built in factory-like conditions.
5.3 Better Market Information
With expanded or improved rating systems (like energy efficiency, builder reliability scores, or quality metrics):
- You can differentiate between a developer with a strong track record and one with a spotty compliance history.
- Over time, that fosters competition, pushing subpar players to lift their game or exit the field.
Key Point:
Productivity gains can trickle down to homeowners through faster approvals, better-quality builds, and more efficient designs.
Conclusion & Final Takeaways
Australia’s housing challenge isn’t just about high demand or interest rates. Low construction productivity is one factor keeping supply tight and prices high.
The Productivity Commission’s research paper reveals that dwelling construction productivity has actually fallen in the past few decades—while the rest of the economy moved forward.
Yet it’s not all doom and gloom. We can absolutely turn the tide if:
- Governments streamline planning, reduce regulatory roadblocks, and fund approval agencies adequately.
- The National Construction Code places greater emphasis on net benefits, consistency, and truly weighs new changes against affordability goals.
- Builders and developers adopt innovative approaches, be it digital project management, modular homes, or advanced R&D.
- We fix workforce constraints by standardising occupational licensing across states and welcoming skilled migrants more readily.
For homeowners, this means the potential for shorter building timelines, improved home quality, and hopefully more stable or lower home prices. As the old saying goes, you shouldn’t have to sacrifice speed for quality—and with the right reforms in place, you won’t have to.
Thank you for reading, and keep an eye on how these proposed reforms progress. Even small changes in regulatory systems or workforce structures can make a big difference to the home-building landscape—and ultimately to your bottom line.
FAQS
- What exactly is productivity in housing construction, and why should I care?
Answer: It’s the amount of output (like completed homes) for each unit of input (labor hours, capital, materials). High productivity generally leads to faster builds, cheaper costs, and more housing supply, which matters if you want more affordable homes or less building hassle. - How do regulations affect how quickly and cheaply my home can be built?
Answer: Regulations are crucial for safety and quality, but multiple layers or overly frequent changes can slow approvals, raise compliance costs, and discourage builders from trying new cost-saving methods. - Is innovation in building (like prefabrication) reliable, and will it reduce my costs?
Answer: Yes, off-site or modular construction can save both time and money, though it’s still not as widespread in Australia. As it scales up and regulations become friendlier to these methods, more affordable prefab options should enter the market. - What do the new changes to the National Construction Code mean for me?
Answer: They can affect things like energy-efficiency standards, accessibility, or building materials. While these often improve safety or sustainability, frequent updates can add cost or delay if you’re in the middle of a build. - How do planning and zoning rules affect property values and availability?
Answer: Strict zoning can limit where homes can be built or how many dwellings can fit on a lot, curtailing supply. If fewer homes are built, prices can climb. Reforms to relax certain constraints can help encourage more projects. - Why are there so many small construction firms? Should I worry?
Answer: The industry is naturally fragmented—builders often subcontract trades. It’s not necessarily a problem, but it does limit scaling and slow the uptake of new technologies. Larger builders often have more capacity to innovate. - How can I check a builder’s or contractor’s quality rating?
Answer: Some states (e.g., NSW) have introduced ratings for builders under iCIRT. Check whether your state has a similar system, or look for references, online reviews, and official building industry registers. - What incentives exist for energy-efficient or sustainable homes?
Answer: Both federal and state governments sometimes offer rebates or discounts for solar, insulation, or green building designs. Programs change frequently, so always ask your builder or check government websites for the latest. - Do policy recommendations actually trickle down to cost savings for me?
Answer: They can. Better planning coordination, clearer codes, and less duplication typically reduce overhead for builders, which can lower prices and speed up delivery. - How do I navigate potential delays or cost blowouts when building or renovating?
Answer: Ensure your contract is clear about timelines, progress payments, and variations. Stay involved in the approvals process—understand each milestone. If something goes awry, talk to your builder quickly; if needed, escalate to local council or a relevant building authority.
Further Reading
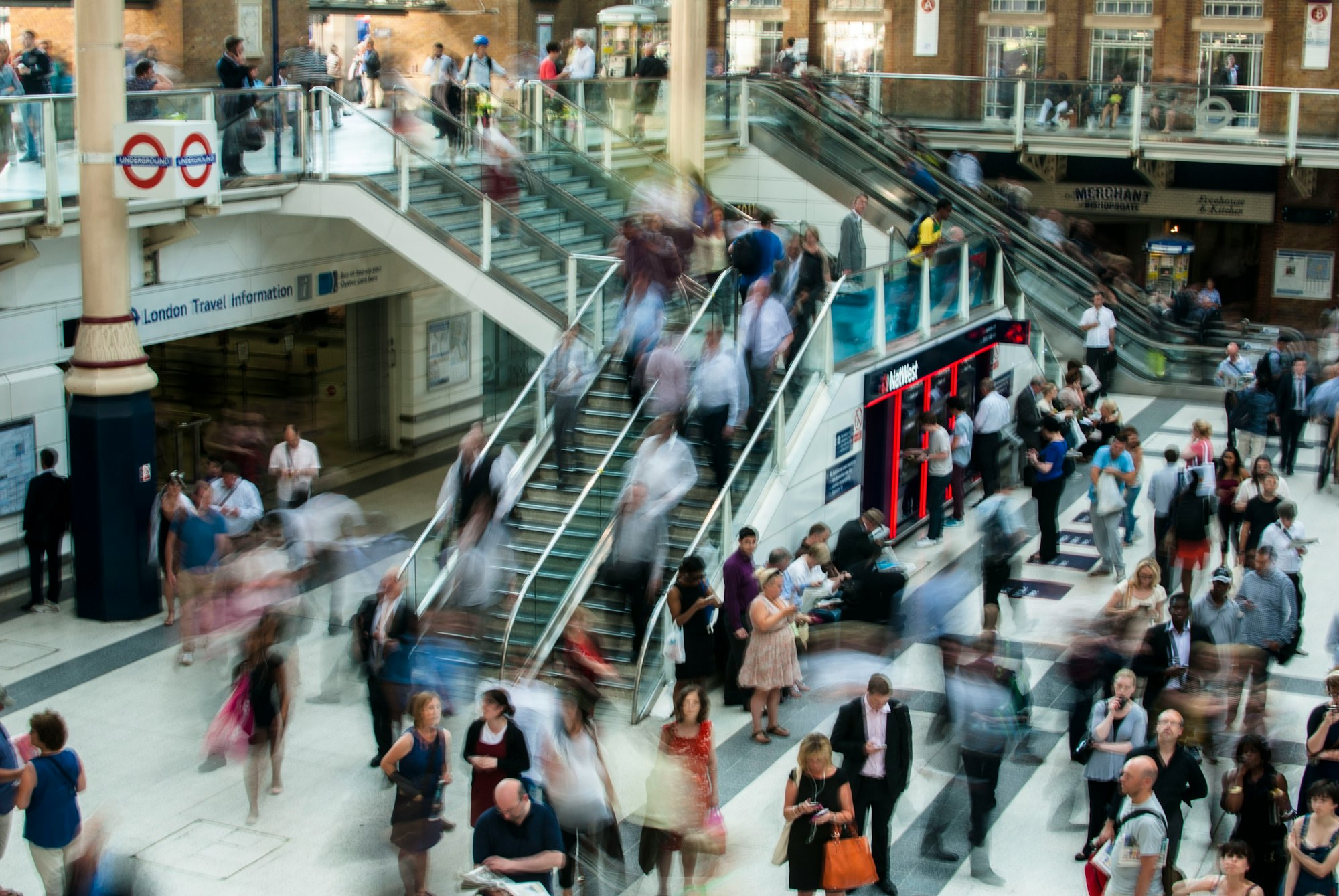