Introduction
The National Construction Code (NCC) and Australian Standards exist to ensure quality, safety, and consistency in Australian residential construction. In an ideal world, these guidelines would lead to better homes, stronger buildings, and higher consumer protection. But the reality is far from this ideal.
- Builders and tradespeople often donât know or follow the standards. Many rely on what they were taught on the job rather than formal guidelines.
- Consumers pay for quality but often receive substandard work. When mistakes happen, rectifications are costly and time-consuming.
- If standards are only referenced after defects occur, are they truly serving their purpose?
The Case Study: Condensation Defects in New Homes
One of the clearest examples of this failure is condensation-related defects in modern homes. Recent NCC changes have improved energy efficiency in homes, but they have also unintentionally increased condensation risks.
Builders rarely factor in vapour barriers, ventilation, and moisture control, leading to mould growth, structural damage, and even health issues. Despite clear standards addressing condensation risks, they are widely ignored.
What Are the NCC and Australian Standards Supposed to Do?
The NCC and Australian Standards were established to create a uniform framework for construction across Australia. They aim to:
- Ensure buildings are structurally sound, safe, and durable.
- Improve livability, energy efficiency while preventing unintended defects (e.g., condensation issues).
- Protect consumers from poor workmanship and non-compliant builds.
- Standardise practices across trades and ensure accountability.
Despite these goals, compliance is inconsistent. Builders often prioritise cost-cutting over quality, and trades rarely have the time or resources to stay updated on evolving standards. As a result, construction defects persist despite regulations being in place.
Condensation Case Study
The NCC does provide clear guidelines on condensation control, but a lack of awareness and enforcement means these rules are often ignored. Builders follow the insulation requirements to the letter but forgetâor simply donât knowâto account for the ventilation needed to keep moisture levels in check.
The result? Thousands of homeowners discovering mould creeping up their walls, musty odours in their homes, and costly damage that could have been avoided.
Instead of fixing the problem before construction begins, homeowners are left trying to find solutions after the damage has already been done. Shouldnât compliance with standards mean fewer, not more, preventable building defects?
- New NCC regulations improved home insulation but failed to account for adequate ventilation, leading to a spike in condensation-related defects.
- Many builders donât understand vapour barriers, moisture management, or air movement, which are essential in preventing condensation issues.
- The NCC provides clear guidelines, but lack of awareness and enforcement means they are often ignored.
See the further reading section for our posts on ventilation and air tightness/control layers.
The Disconnect: Why Trades and Builders Ignore Standards
If Australian Standards and the NCC set clear guidelines, why do so many builders and trades fail to follow them? The reality is that tradition, cost, and accessibility play a bigger role in daily construction work than formal regulations ever have.
Learning on the Job vs. Learning the Standards
For many tradespeople, their main education comes from working under more experienced builders, not from reading the NCC or Australian Standards. The problem? Bad habits and outdated practices get passed down just as often as good ones.
Ask a veteran builder or contractor about their methods, and they might say,
"Iâve been doing it this way for 30 years, never had a problem till you came along!"
But does that mean it complies with todayâs standards? Not necessarily. Many rely on gut feel and experience rather than documented best practicesâuntil something goes wrong.
âI Donât Have Time to Read Standardsâ
Most tradespeople work long hours under tight deadlines, balancing multiple jobs at once. Sitting down to read hundreds of pages of regulatory text simply doesnât fit into their schedule. Itâs easier to stick with what they know than to research updated requirements.
The Cost of Access: When Standards Are Locked Behind a Paywall
Even if a builder wants to stay up to date, accessing Australian Standards is expensive. Unlike the NCC, which is free to access online, many Australian Standards documents come with a hefty price tag. Expecting individual trades to purchase multiple standards just to do their job properly is unrealistic.
Check out the further reading section for our post on the end of free access to Australian standards.
Regulations as a Footnote: The Missing Details in Plans
Even when standards are referenced in a project, theyâre often included as a blanket clause rather than specific instructions. A set of building plans might say âInstall in accordance with AS 4200.1â, but unless the builder has a copy of that document and reads it, adds details to drawings, they wonât know exactly what that means in practice, nor contractors understand the reference.
And letâs be honestâmost of them donât read it.
The Condensation Knowledge Gap
Condensation issues are a perfect example of how overlooked standards lead to real problems. Even though the risks are well-documented, many builders:
- Donât consider vapour permeability when installing insulation.
- Skip proper ventilation, even though the NCC requires it.
- Only recognise moisture damage once itâs too lateâleading to expensive disputes and repairs.
Builders may not ignore standards deliberately, but without training, access, or enforcement, they continue to build the way they always have, unaware of the risks.
The Consequences of Ignoring Standards
Most homeowners assume their builder will follow the rules, but when corners are cut, the damage isn't always immediate. Cracks in foundations, waterproofing failures, and weak structural elements might not appear until months or even years after move-in. By then, the costs to fix these issues are often exorbitantâand if the builder denies liability, the homeowner is left footing the bill.
When builders ignore (wilfully or ignorantly) the NCC and Australian Standards, the consequences are real and costly. Homeowners expect their new homes to be built correctly, but too often, they discover problems only after theyâve moved in.
Some defects are minor inconveniences; others lead to structural failures, legal battles, and even serious health risks. And when things go wrong, itâs mostly the homeownerânot the builderâwho pays the price.
When Poor Workmanship Becomes a Homeownerâs Nightmare
Imagine settling into your brand-new home, only to notice cracks forming along the walls. At first, they seem cosmetic, but then your doors stop closing properly, and the floors begin to slope. What seemed like a perfectly constructed home is now showing signs of foundation failure.
Some issues take even longer to emerge. Waterproofing failures might not show up until water starts seeping into floors or neighbouring rooms, causing mould and structural damage. And by the time the homeowner realises, the builder might have already moved on, leaving them to fight for repairsâif they can even get them.
The Legal Minefield of Construction Defects
Most homeowners assume their builder will fix problems under warranty, but thatâs rarely the case without a fight. The moment a defect is reported, the blame game begins.
"When did you first notice the defect, why didn;t you report it then, at 6 months defects."
Builders often rely on vague warranties, disclaimers, or contractual loopholes to avoid fixing defects. Some insist the problem is due to natural settlement, homeowner neglect, or even the weather. Meanwhile, homeowners are left navigating warranty claims, consumer tribunals, and legal disputes that can drag on for years.
Instead of preventing defects by following standards, the industry often treats them as a legal matter to resolve after the fact. And thatâs the problemâhomeowners shouldnât have to become legal experts just to get what they paid for.
Health and Safety Risks: The Hidden Dangers
Not all construction defects are visible, but that doesnât make them any less dangerous. Some of the most serious failuresâlike fire hazards, water damage, and black mould growthâcan remain hidden until they endanger the health of occupants.
Condensation issues, for example, donât make themselves known until a homeowner notices a musty smell, develops respiratory issues, or finds black mould spreading behind the walls. By then, the damage has already been done. The same goes for faulty electrical wiring, which can lead to fire hazards, or poorly installed plumbing, which can result in water damage and structural decay.
The Erosion of Trust in the Construction Industry
The biggest casualty of poor compliance? Consumer confidence. Homebuyers assume that builders follow regulations, but when defects emerge, they quickly realise the industry is more focused on marketing homes than ensuring their quality.
People spend years saving for a deposit, believing theyâre investing in a safe, durable home. Instead, they find themselves in disputes over water damage, cracking foundations, and a lack of accountability. And without better oversight, the cycle continuesâwith new home buyers unknowingly stepping into the same risks.
Condensation Case Study: When Builders Ignore Moisture Management
For many homeowners, condensation problems start small and spiral into major structural issues. They move into a new home, only to discover black mould creeping along their ceilings or a damp smell they canât get rid of. By the time the issue is recognised, the fix isnât cheap.
Instead of following NCC guidelines for ventilation and moisture control, builders often focus solely on insulationâsealing homes tighter without allowing moisture to escape. Without vapour barriers, adequate airflow, or drainage strategies, condensation builds up inside walls, creating the perfect conditions for mould growth and decay. But the reality is simple: if standards had been followed in the first place, the problem wouldnât exist.
Regulatory Oversight: Who Actually Checks Compliance?
The NCC and Australian Standards may exist to set the bar for construction quality, but hereâs the realityâwho actually checks that they are followed? Homeowners assume thereâs a rigorous compliance system in place, but the truth is that oversight mechanisms are fragmented, inconsistent, and often inadequate.
Many assume that building certifiers, council inspectors, or regulatory bodies closely monitor compliance, but the process isnât as thorough as people expect. In fact, many aspects of construction quality simply go unchecked.
Building Certifiers: Limited Scope, Limited Power
When most people think of building approvals, they imagine detailed inspections ensuring every aspect of a home meets regulations. But in reality, building certifiers (QLD I'm referring to here) donât check detailed workmanshipâtheir job is to ensure a project meets the broad requirements of the NCC, mainly bracing, tie down and general occupancy checks - not checking for standards compliance.
They donât get into the finer detailsâlike whether waterproofing is properly applied, insulation is installed correctly, or whether cheap, non-compliant materials are used instead of the specified products.
Builders often rely on certifiers as a stopgap for unskilled or underqualified (commodified) administration teams. Certifiers frequently receive builders applications and plans filled with errors, forcing them to spend countless hoursâoften unbilledâidentifying and reporting these issues back to the builder. The goal? To get corrected documents resubmitted, which is how the process should have worked in the first place.
This dynamic places certifiers in an awkward position, essentially acting as surrogates for building companies without reaping any of the benefits. Instead of serving as impartial arbiters ensuring compliance, theyâre bogged down in a role that stifles their ability to focus on their core service.
Council Inspections
Local councils do conduct inspections, but their role is even more limited. They check for general plumbing compliance only, but they are not responsible for verifying build quality in detail. That remains the builders obligation.
A council inspector wonât be checking whether the right fasteners were used, if waterproofing membranes were correctly applied, or if the walls have been painted corerctly.
Self-Regulation: A System Built on Trust (That Doesnât Work)
In many cases, the construction industry relies on self-regulation, meaning builders and contractors are expected to sign off on their own compliance. This is where things start to fall apart.
While some builders take compliance seriously, many others cut corners knowing that no one is actively checking their work in detail (or just to turnover more work, make more money).
Thereâs no systematic auditing process, no independent verification, and no guarantee that what was approved on paper actually made it into the final build. By the time defects appearâsometimes years laterâthe damage is done, and homeowners are left scrambling for recourse.
Take AS 4773.2 Masonry in Small Buildings, for example. Appendix A, titled "Information on Drawings and Specifications," provides a detailed checklist of what should be included in drawings and specifications (see the embedded file below). This is gold for ensuring clarity and transparency in building projects.
Yet, in residential building specifications, this information is rarely included in full. If it were, it would make a world of difference for consumers (and contractors). It would help them better understand whatâs included in the design and build, and even allow them to compare builders more effectively.
The catch? Because this appendix is labelled as âinformative,â builders arenât required to include it. And thatâs a real shame for consumers.
Add to this the lobby groups "hatred" to impose any perceived additional burden on builders, and you can see why things are the way they are. (LINK)
No Mandatory Compliance Checks for General Building Work
Unlike electrical and plumbing work, which require strict compliance certificates, general building work has no mandatory final compliance to to check details meet standards.
This means that once a home is built, thereâs no official quality control process to ensure every aspect of the construction meets the required standards. Sure, thereâs a certificate of occupancy, but this is issued based on a checklist of certificates submitted to the certifier. In this system, contractors essentially self-certify their compliance with the standards without demonstrating how they meet the standards (demonstrate a quality managements system).
From the outside, everything might look compliantâbut dig deeper, and youâll find that the scope of each certificate often may not align with the standards that actually apply. Itâs a system that leaves a lot of room for oversight, a lot of trust and hope.
Unless a defect is blatantly visible at handover, homeowners have no formal guarantee that their house has been built correctly. If residential builders and contractors used ITPs with witness hold points, and a basic quality management system, this would go along way to ensuring compliance with standards.
Introducing "more" checks and balances, like a quality management system, would inevitably slow down build times. And in a system already under pressure, thatâs a tough sell. "It's crazy talk Anthony. Not practical. Your not living in "the real world" or "you know nothing" they would say to this idea.
Or the other retort would be similar to Q&A question/answer from the other night "it's more complicated than this" - a fancy way of avoiding a direct answer by assuming intellectual superiority (REFERENCE).
The Reality of Compliance: Homeowners Are Left to Find Problems Themselves
Most people assume that if a home has been approved and certified, it must have been thoroughly checked for compliance. But in reality, compliance systems are patchy at best, and outright flawed at worst.
The burden of identifying problems falls squarely on the homeowner. Unless they hire an independent engineer/building inspector, conduct extensive research, or notice defects early, they could be living in a non-compliant home without even realising it, despite forms issued by contractors "signing off" work packages as compliant.
Builders do quality checks for sure, but generally this is checking to discharge liability in the event of litigation/meet minimum compliance (fiduciary obligations). I have yet to seen a builder in Australia that has a quality management system focused on delivering the best quality product for consumers over busting out a house for turnover.
Does each contractor who signs off a work package have quality management system? How can we be assured their work is compliant if its self certified? Should we just trust them?.....
Why Marketing, Not Quality, Drives Australian Housing
Most homebuyers assume that regulations guarantee a high-quality build, but in reality, marketing does most of the heavy lifting in selling homes, not ensuring their quality. Builders donât win contracts by showcasing their superior compliance with the NCC or Australian Standards.
Instead, they sell an image, a dream, and a lifestyle, often leaving homeowners with a product that doesnât match their expectations.
The Illusion of Display Homes
Step into a display home, and youâll be sold perfectionâthe finest materials, flawless finishes, and high-end appliances. But hereâs the catch: most of what you see isnât included in the standard build. Display homes are carefully curated marketing tools designed to close the sale, not to set realistic expectations of the final product.
What isnât obvious during your walk-through is that construction quality and compliance take a backseat to aesthetics. Builders focus on selling you the visionânot on discussing structural integrity, material longevity, or compliance with building codes.
The Power of Sales-Driven Messaging
Marketing in the residential construction industry isnât about building the best possible homeâitâs about maximising appeal and minimising objections. Builders invest heavily in branding, targeted advertising, PR messaging and customer persuasion, ensuring potential buyers focus on granite benchtops, open-plan living, and âHampton-style facadesâ rather than the nuts and bolts of construction.
Have you ever seen a builder advertise their carefull and dilligent adherence to NCC guidelines, their use of compliant waterproofing methods, or their commitment to structural integrity? Probably not. Compliance is assumed, not discussed. And thatâs exactly how the industry prefers it.
Aesthetic Appeal vs. Proper Construction Methods
Homebuyers are conditioned to focus on what they can see, but the real risks lie beneath the surface.
Itâs easy to get swept up in beautiful finishes and trendy designs, but poor workmanship hides behind plasterboard, paint, and clever staging techniques. What looks like a perfectly built home on day one can start showing cracksâliterally and figurativelyâwithin months.
Builders are incentivised to complete projects quickly to move on to the next job. This often means quality control is secondary to meeting sales targets. Corners get cut. Compliance is ignored. And by the time defects emerge, itâs too late for the buyer to do much about it. See further reading below for our post on time/cost/quality - the "holy trinity" of construction.
The End Result: A Buyer Beware Market
Once construction begins, homeowners quickly realise they are navigating an industry that prioritises speed and efficiency over precision and durability. And by the time defects become apparentâwhether itâs waterproofing failures, cracking slabs, or condensation issuesâthe builder may have already moved on to the next project.
But hereâs the real kicker: builders are only held accountable for a fraction of the lifespan of the home.
- The typical statutory warranty period is 6 years and 6 months.
- The expected lifespan of a house is a minimum of 30 years.
- The average home loan is between 25 and 30 years.
So while homeowners are financially tied to their purchase for up to three decades, builders are only liable for defects for less than a quarter of that time. The rest? That risk is passed onto the homeowner and their insurance premiums.
At the end of the day, the system doesnât incentivise long-term qualityâit incentivises builders to meet minimum compliance for as short a time as possible. And when homes start failing long before the mortgage is paid off, itâs the buyerânot the builderâwho pays the price.
Fixing the System: How to Improve Compliance and Quality
"It costs nothing to do the job right the first time. It costs a fortune to fix it later."
If the standards exist, why arenât they being followed? And more importantly, how do we fix the system so that compliance actually happens? The solution isnât just about enforcementâitâs about accessibility, education, accountability, and real consequences for cutting corners.
Make Standards Freely Accessible
How can we expect builders and trades to follow standards when they donât have easy access to them? Unlike the NCC, which is freely available online, Australian Standards are locked behind paywalls. Expecting every builder, contractor, and apprentice to purchase multiple expensive documents just to understand compliance is unrealistic.
Standards should be open to all professionals and consumers. If compliance is the goal, then knowledge should be accessible, not hidden behind a subscription fee (see further reading for our post on this). Making these resources free would be the simplest and most effective way to improve industry-wide understanding and adoption.
Increase Training and CPD Requirements
Most builders and tradespeople learn on the job, which means that new regulations and evolving best practices rarely make their way into real-world construction sites. Without ongoing education and structured training, compliance becomes an afterthought rather than a core part of the trade.
A strong Continuing Professional Development (CPD) program should be mandatory.
Training should include condensation risk assessments, moisture control techniques, building science, waterproofing and best practices in structural complianceâall areas where poor execution leads to costly defects. Learning from mistakes after the fact isnât good enough; we need to build knowledge before problems occur.
Proactive Inspections: Catching Problems Before They Start
Currently, much of the construction industry operates on a âwait until something goes wrongâ model. Defects are only addressed after homeowners complain, take legal action, or report issues. By then, the damage is done, the costs are high, and the builder may have already moved on to the next project.
Instead of relying on consumer complaints, regular, proactive inspections should be standard practice. Third-party auditors should conduct random site inspections during construction, rather than only verifying compliance after handover. If a mistake is caught early, it can be fixed before it turns into a major defect.
Require Compliance Documentation
Imagine buying a car without a logbook, service history, or any verification that itâs roadworthy.
Now consider that this is exactly what happens with newly built homes.
Builders should be required to provide documented proof that their work complies with relevant standards before final approvals are granted. Compliance shouldnât be an assumptionâit should be verifiable, transparent, and provided to homeowners before they take possession of the property.
Mandatory quality assurance documentation would ensure that compliance isnât just a tick-box exercise but a real accountability measure (see further reading section below for our post on "stress free home building..with a quality management plan."
Strengthen Penalties for Non-Compliance
Currently, many builders operate under the assumption that cutting corners comes with little risk. If they get caught, the worst they face is having to fix the issue after a complaint is made. But what about the cases where homeowners donât notice defects until years later?
Without financial and licensing consequences, builders have little incentive to prioritise compliance over profit. The solution? Real penalties for non-compliance. Builders who repeatedly fail to meet standards should face fines, mandatory rectification work, and even restrictions on their license.
If poor workmanship costs builders more than doing the job right the first time, compliance will no longer be an afterthoughtâit will be the only way to stay in business (see further reading post title "Demand better..why accountability in Australian home building."
Fixing the System Requires Commitment
The path to better compliance isnât a mysteryâwe already know what needs to be done. The real question is whether there is the political and industry will to enforce these changes.
The reality is this: homeowners deserve homes that meet the standards they were promised. Until compliance is made easier, mandatory, and enforceable, we will continue to see costly defects, frustrated homeowners, and a construction industry that fails to live up to its potential.
Conclusion
The NCC and Australian Standards exist to provide a framework for high-quality, safe, and durable homes. Yet, their effectiveness is undermined by a lack of awareness, enforcement, and accountability within the construction industry.
Key Takeaways:
- Most builders and trades do not actively engage with the standards, relying instead on outdated training or industry norms.
- Consumers suffer the consequences, facing costly repairs, legal disputes, and potential health risks due to defects.
- There is no robust enforcement mechanism ensuring compliance, meaning many issues only come to light after a home is completed.
- Marketing overshadows quality, misleading homeowners into thinking they are buying a well-built house when, in reality, no one is verifying compliance before handover.
What Needs to Change?
- Make the NCC and Australian Standards freely accessibleâbuilders and trades cannot follow rules they cannot afford to read.
- Increase mandatory training and continuing educationâcompliance should not be optional.
- Introduce proactive inspections and compliance documentationâbuilders must prove they followed the standards before completion. ITP, ITC and ITR goes a long way to demonstrating this.
- Strengthen enforcement with real penaltiesâbuilders and trades must be held accountable when they ignore compliance requirements.
- Ensure consumer awarenessâhome buyers should have access to compliance reports and quality assurance documentation before purchase.
Final Thought:
The tools to build better homes already exist, yet they are ignored. If homeowners, regulators, and the construction industry demand change, we can shift the focus from marketing hype to real quality in residential construction.
FAQS
- What is the National Construction Code (NCC) and why does it matter?
The NCC sets out the minimum requirements for the safety, health, amenity, and sustainability of buildings in Australia. - Are Australian Standards legally enforceable in residential construction?
Some standards are referenced in legislation, making them mandatory, but many are only guidelines unless explicitly required by contract or local regulations. - Why donât builders follow the standards if they exist?
Many claim they are too expensive, difficult to access, or time-consuming to apply in real-world building scenarios. - Who checks if my home is built to the right standard?
Building certifiers and council inspectors conduct basic compliance checks, but they do not inspect everything. There is no comprehensive oversight ensuring all standards are followed. - How can homeowners verify compliance before itâs too late?
Request documentation, engage an independent building inspector, and educate yourself on key compliance requirements. - What are the biggest risks of non-compliance in home construction?
Structural failures, condensation issues, waterproofing failures, energy inefficiencies, legal battles, and major financial losses. - Why is condensation becoming such a big problem in new homes?
Improved insulation and airtight construction have reduced ventilation, leading to trapped moisture and mould growth. - What can be done to prevent condensation-related defects in housing?
Proper vapour barriers, ventilation strategies, and moisture control measures must be incorporated during construction.
Further Reading
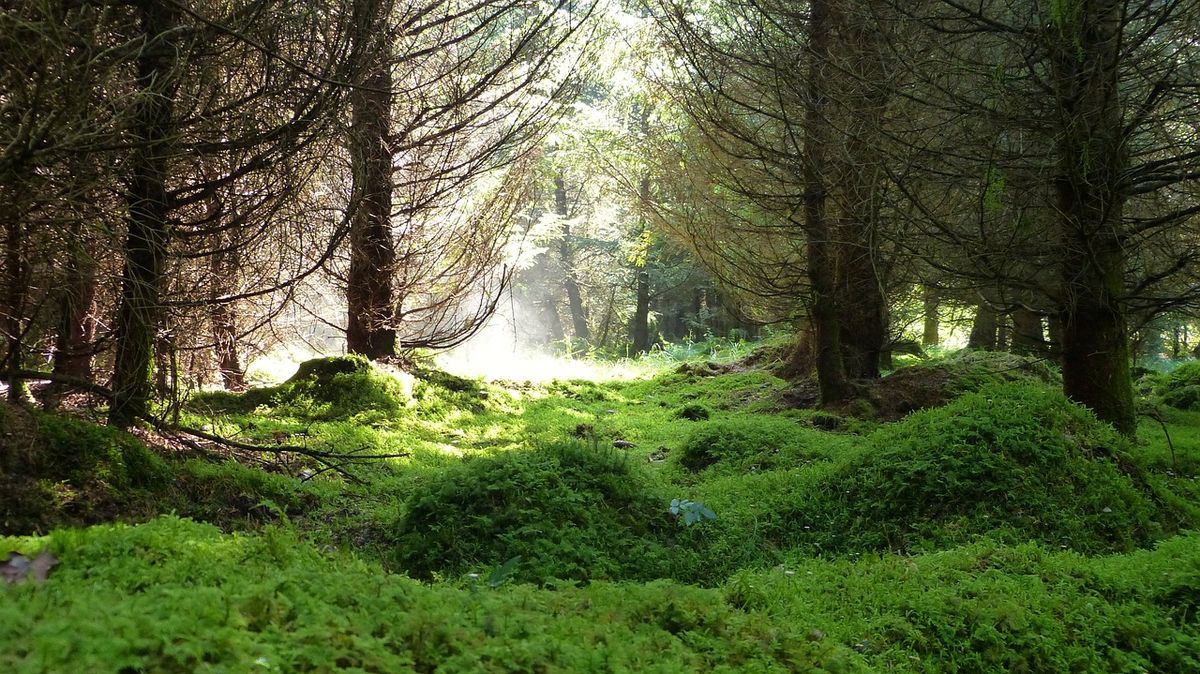
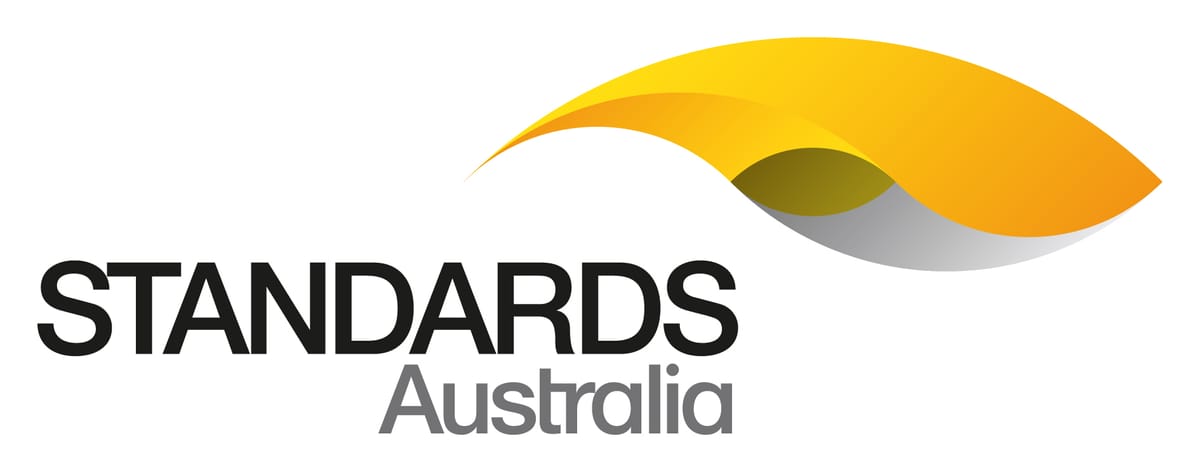
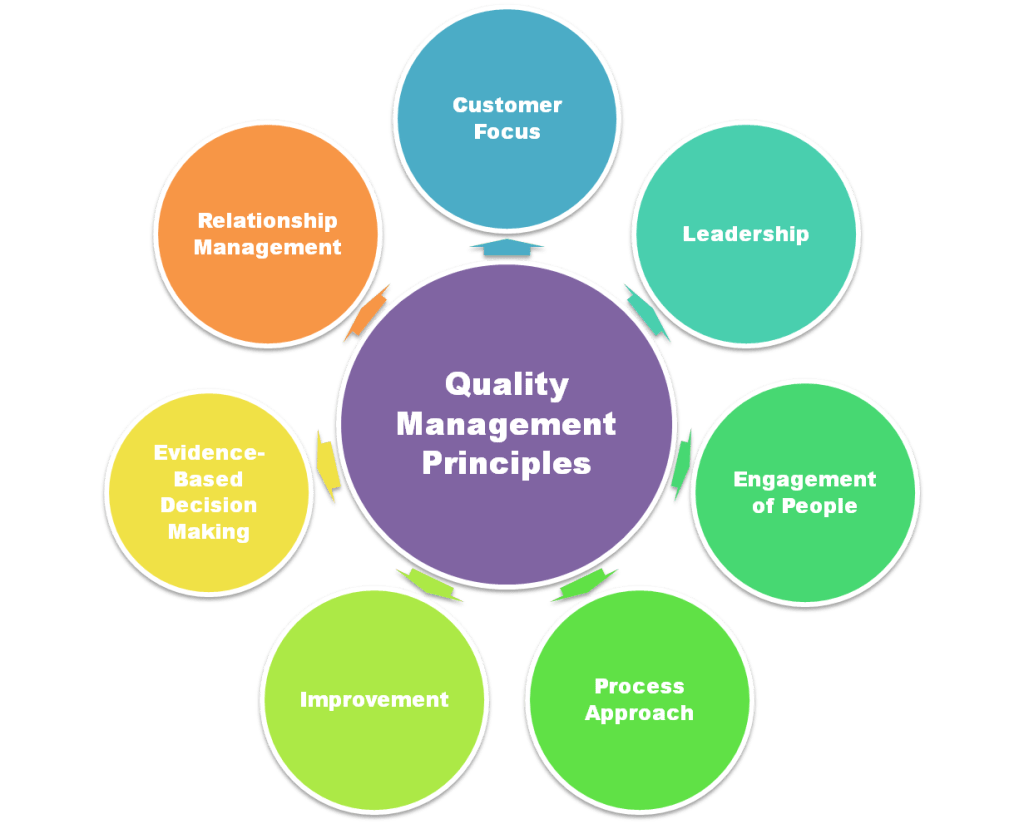
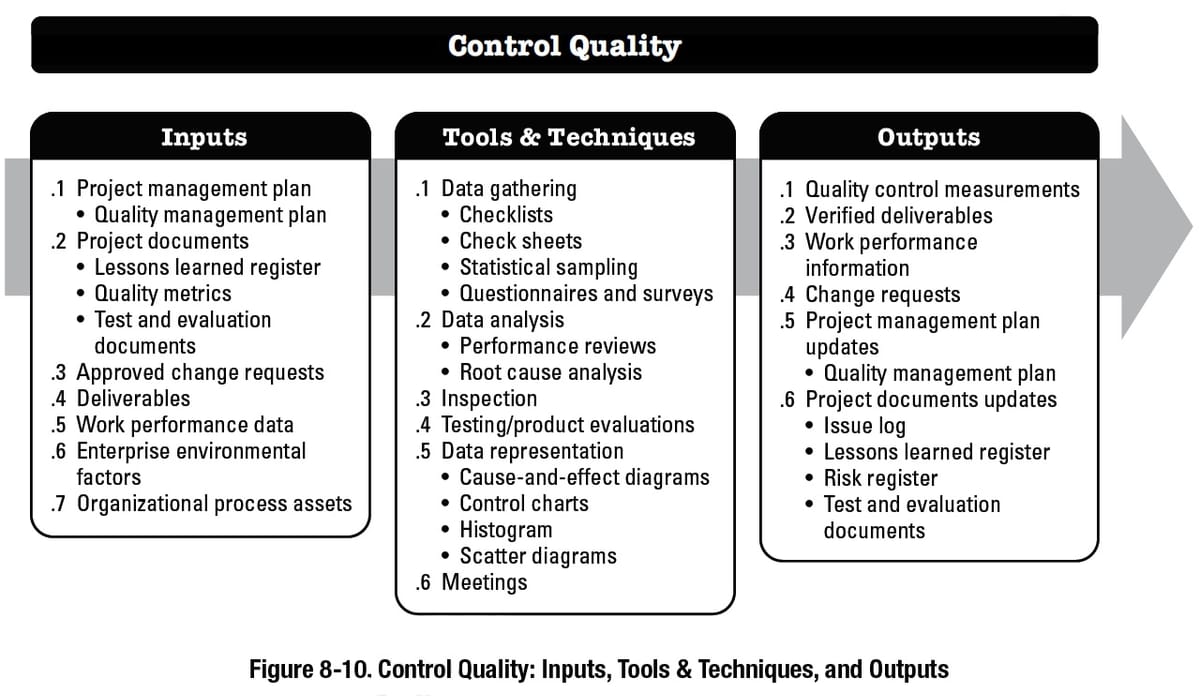