Introduction: The Hidden Costs of Deregulation
Imagine moving into your brand-new home—the smell fresh paint (off gassing), sleek finishes, a place you've worked and saved for—only to discover leaks after the first rain, cracks appearing within weeks, or worse, the smell of mould creeping through your walls. Unfortunately, for too many Australians, this isn’t a bad dream. It’s reality.
What went wrong?
Over the past three decades, Australia’s residential construction industry has shifted from a model of independent local council inspections at key building stages to one dominated by private certifiers, many of whom are appointed—and paid—by the builders themselves. The result? Oversight has weakened, trust has eroded, and the quality of new homes has suffered.
In this article, we explain why reinstating mandatory local council inspections at four key construction stages—slab, frame, roof/flashings, and waterproofing—is a vital step toward improving building quality and protecting homebuyers.
Whether you're building your first home, comparing builders, or just trying to avoid the horror stories you've read online, this post will walk you through what’s gone wrong and how we fix it.
Construction quality has declined because key quality checks were removed. Mandatory council inspections once acted as a safeguard—builders respected them (and often feared a run-in). It’s time to bring them back.
I. The Decline of Construction Oversight in Australia
A. How Did We Get Here?
Before private certification became the norm, most residential builds in Australia were subject to mandatory inspections by local council inspectors at key construction stages. These included the footings or slab pour, the wall framing before internal linings, and a final inspection before the home could be occupied.
These inspections weren’t optional. They were conducted by independent council officers acting in the public interest, ensuring compliance with the Building Code of Australia and relevant standards.
Then came deregulation.
Starting in the 1990s and continuing into the 2000s, states and territories began to phase out council-run inspections in favour of private certifiers. The justification? Reduce red tape, cut costs, and speed up construction.
Wait a minute—hold up, hold up. Aren’t we having this exact conversation right now in the media and politics? Everyone’s saying red tape is to blame for low housing output. But didn’t we already switch to private certifiers to cut the red tape? And now we’re being told it still needs cutting?
But in doing so, governments handed responsibility for code compliance back to the very industry expected to self-regulate.
B. From Watchdogs to Lapdogs
Under the old system, inspectors worked for councils and, by extension, for the public. Their role was to independently verify that a home was being built to code—something not always in a builder’s financial interest.
Under the new system, builders choose and pay the certifiers who check their work. Certifiers, in turn, rely on builders for future jobs. And if you’re too strict—if you demand the builder fix framing issues or redo waterproofing—you might not be asked back.
This is a textbook conflict of interest. And in residential construction, it has real consequences.
C. Oversight Becomes Optional
Today, on many new home builds, no one from outside the builder’s team may ever physically check the work at crucial stages. Slab pours are signed off using photos. Frame inspections are reduced to a quick site visit—or not done at all. Waterproofing is often covered up before anyone independent sees it.
This is how corners get cut—and how defects go unnoticed until long after handover.
Without mandatory council inspections, the system now relies on builder self-certification—with homeowners left to deal with the consequences.
Mandatory Inspection Stages by State (Pre-2000)
State | Regulation | Mandatory Inspection Stages |
---|---|---|
Queensland | Standard Building Regulation 1993 | - Foundation and excavation (before footings are laid) |
- Slab stage (before concrete is poured) | ||
- Frame stage (before cladding or lining is fixed) | ||
- Final stage (after completion of all building work) | ||
New South Wales | Environmental Planning and Assessment Regulation 2000 | - After excavation and prior to placement of footings |
- Before pouring in-situ reinforced concrete building elements | ||
- Before covering framework for floor, wall, or roof | ||
- Before covering waterproofing in wet areas | ||
- Final inspection before issuing Occupation Certificate | ||
Victoria | Building Act 1993 and associated Building Regulations | - Before placing footings |
- Before pouring in-situ reinforced concrete | ||
- Upon completion of framing | ||
- Final inspection upon completion of all building work |
Mandatory council inspections once acted as a safeguard. Replacing them with builder-appointed certifiers has created a system where oversight is minimal and accountability is blurred.
II. Evidence of Declining Construction Quality
You might think: Surely there are still checks in place. It can’t be that bad, right?
Unfortunately, it is that bad. And the data backs it up—unequivocally.
A. What the AHURI Report Tells Us
The Australian Housing and Urban Research Institute (AHURI) recently released a report in 2024: A National Roadmap for Improving the Building Quality of Australian Housing Stock. The findings are not great.
- Over 70% of homeowners surveyed reported at least one significant defect in their newly built home.
- The most common problems? Cracks in internal walls, leaks, mould, and plumbing failures—many of which relate to early-stage construction errors that would have been spotted with proper inspection.
- The defects weren’t just cosmetic. Many were serious enough to affect structural performance or occupant health.
And these numbers aren’t outliers—they reflect systemic problems across all states and territories.
B. Condensation and Mould: A National Problem
The CSIRO’s Scoping Study on Condensation in Residential Buildings added another layer of concern. It estimated that up to 40% of new homes may experience condensation-related issues.
Why is this happening?
- Modern homes are more airtight (to meet energy efficiency standards) but often lack adequate ventilation and proper moisture control.
- Without independent inspection at the frame and waterproofing stages, mistakes in vapour barrier installation, sarking, roof flashing, and exhaust venting go undetected.
- The result: black mould, musty smells, and ongoing respiratory problems for occupants—especially children and the elderly.
This is a building science failure—but it’s also a quality control failure.
C. Builders Are Often Unaccountable
What makes this even worse is that many builders are under no obligation to fix these issues unless taken to court or tribunal (like NCAT or QCAT). And even then, it’s a long, expensive and emotional road for homeowners.
A key reason these defects slip through? No one independent is checking the work when it matters.
Self regulation baby! (the red tape has been cut)
If a wall leaks and no one independent saw it go up, is it really a defect—or just a feature you didn’t pay extra for?
The statistics don’t lie—Australia’s new homes are riddled with preventable defects. Without mandatory inspections, many issues go unnoticed until they become costly or dangerous.
III. The Role of Industry Lobby Groups and Associations
You might be wondering—if all this is known, why hasn’t anything changed?
The short answer: industry resistance. The long answer? A tangled web of lobby groups, associations, and industry “self-regulation” that prioritises volume and image (awards) over substance and accountability.
A. Reform? Not on Their Watch
In a perfect world, industry associations would push for higher quality standards of members, stronger enforcement, and better outcomes for consumers. In reality, many of them oppose reforms that increase scrutiny, especially if it slows down construction or threatens profit margins (membership or insurance policy renewals).
Take the issue of reinstating independent inspections. Lobby groups argue it will add cost and slow down builds—but they rarely acknowledge the long-term cost of fixing defects, pursuing claims, or dealing with health issues caused by poor workmanship.
Why the pushback? Because more oversight exposes more problems, and that’s bad optics for developers, builders, and the associations that represent them.
B. Who Are They Really Representing?
Most builders’ associations exist to serve their members, not homebuyers. Their revenue comes from membership fees, training courses, insurance policies—not from defending consumers or enforcing quality.
- When defects spike, they minimise the issue in the media.
- When regulation tightens, they lobby to water it down.
- When awards are handed out, they often go to homes judged on aesthetic appeal, not build quality or technical performance.
C. Compliance ≠ Quality
You’ll often hear builders and industry groups say things like “We build to code” or “Our homes are fully compliant.” It sounds reassuring—but it's often meaningless without context.
Here’s the truth: compliance is the floor, not the ceiling. It’s the bare minimum required by law. And many builders use vague language that sounds impressive but avoids any measurable commitment to quality.
We’ve seen this firsthand in our ChatGPT Builder Review Series.
When ChatGPT analyses each builder specifications, we often see:
- Vague, subjective and interpretive expressions used. Terms like "Move-In-Ready inclusions", “where applicable,” “as per manufacturer’s recommendations,” “industry best practice,” and “Alternative replacement item/s where an item is unavailable or deemed unsuitable.”
- Commitments phrased with soft verbs like “may,” “can,” or “intended to,” which mean nothing in a dispute.
- Descriptions that focus on aesthetics (“designer kitchen,” “elevated finish,” “premium inclusions”) rather than performance.
Compare that to the language of the National Construction Code (NCC) or Australian Standards, which are legal instruments:
- They use precise, enforceable terms like “shall,” “must,” and “will”—there’s no ambiguity.
- These terms define obligations, not preferences. When a clause says “shall comply with AS 1684,” it’s binding.
The problem is, most homeowners can’t tell the difference—and that’s exactly why this vague language exists.
It gives builders wiggle room to downgrade quality, substitute cheaper materials, or avoid enforcement—all while still appearing “compliant.”
Our builder reviews expose how this marketing language masks the absence of genuine commitment to performance or durability. We break down what’s actually included, what’s left vague, and what that means in real-world builds.
And when there’s no one watching during the slab, frame, or waterproofing stages—compliance is mostly theoretical.
Real quality comes from verifiable, enforceable processes. And right now, that’s missing.
Industry associations often oppose meaningful reform because it challenges their business model. Without independent oversight, builders can cut corners while maintaining a glossy image—and that leaves homeowners exposed.
IV. The Case for Reinstating Mandatory Local Council Inspections
So—if we know things are broken, what would actually fix them?
Simple. Bring back the one mechanism that used to keep builders honest: independent, mandatory inspections by local councils at key stages of the build.
🙊 This isn’t nostalgia. It’s common sense. When someone not paid by the builder checks the work before it's covered up, builders take more care, defects are caught early, and consumers are protected.
A. What Local Inspections Actually Achieve
Unlike private certifiers—who may never step foot on site—local council inspectors used to turn up when it counted:
- Slab stage – to confirm steel reinforcement, footing depth, termite protection, and proper formwork before the concrete is poured (AS2870, AS3600)
- Frame stage – to ensure structural integrity, bracing, tie-downs, and compliance with wind classifications (per AS 1684).
- Roof and flashing stage – to verify proper installation of sarking, flashings, roof battens, and ventilation pathways before roofing is completed.
- Waterproofing stage – to inspect wet areas before tiling and detect common membrane failures (AS3740 and AS4654.1).
Each of these is a choke point in the quality chain. If something goes wrong here—and no one independent sees it—you’re inheriting a problem with compounding costs.
B. Slowing Down to Speed Up
Builders argue that more inspections will “slow down housing supply.” Maybe. But here’s the thing:
Fixing bad work takes longer than doing it right.
Inspections force trades to follow standards. That means fewer reworks, fewer defect claims, and fewer legal fights later on. It’s not a delay—it’s an investment in getting it right the first time. You’re creating future value by investing in today’s process.
C. Accountability Through Presence
When someone’s watching, people lift their game. Always have, always will.
“What is the sound of one hand clapping?”
It’s the sound of a construction industry asking for fewer rules while promising better outcomes—without changing a thing.
Or more crudely, its the apprentice in the port a loo at smoko.
You can plaster marketing terms like “quality-focused” or “award-winning” all over your website, but the real test is whether you’re building to standard when no one’s looking. Much like "what we do in the shadows" but not as funny.
“Self-regulation is great—until you realise you’re the only one regulating yourself, and the building supervisor just waved from the car window.”
Mandatory council inspections create a simple equation: If you want to move forward, your work must pass an independent check. That’s how you lift standards—by verifying, not trusting.
V. Addressing Counterarguments
Whenever the topic of reinstating local council inspections comes up, defenders of the current system are quick to object. You’ll hear things like:
“It’ll cost too much!”
“It’ll slow everything down!”
“Private certifiers already do this!”
Let’s unpack those one by one—with facts, not fluff.
A. “It Will Increase the Cost of Building Homes”
This is the go-to argument for industry groups. But here’s the truth: the cost of fixing defects far outweighs the cost of proper inspections.
Let’s say an independent inspection costs a few hundred dollars per stage. Now compare that to:
- Replacing a leaking balcony ($15,000+)
- Repairing waterproofing to bathroom ($25,000+)
- Legal fees to chase rectification in tribunal ($5,000–$30,000)
- Living in temporary accommodation during repairs (priceless, if you've got kids)
These aren't rare horror stories—they're increasingly common in today’s volume-build market. So yes, inspections cost money, but they also save homeowners from financial disasters later.
“Penny-pinching during the build only works until your roof leaks through your downlights.”
B. “It’ll Slow Down Construction”
Let’s be real: we're already seeing construction delays everywhere due to labour shortages, material availability, and centrally managed build schedules. But blaming inspections for delays is a deflection.
A well-structured inspection program doesn’t need to be a bottleneck. In fact:
- It forces better scheduling discipline.
- It reduces the need for rework.
- It sets clear, non-negotiable milestones for builders to hit (witness hold points).
That’s not inefficiency. That’s accountability.
And if you're a homeowner, wouldn’t you rather your builder takes an extra two days to do it right than saves time and costs you $20,000 in post-handover repairs, taking time off work to meet them during work hours or they wont fix it?
C. “Private Certifiers Already Inspect Everything”
Do they? Sometimes, yes. But in far too many cases, their “inspection” consists of photos, specific inspection criteria (bracing and tie down only) a subcontractor declaration, and a digital signature.
Because they work for the builder—and they want more jobs—many certifiers don’t push too hard. You don’t bite the hand that feeds you. Their incentives are aligned with the builder’s, not the buyer’s.
That’s not to say there aren’t good certifiers out there. But the model is broken. You can’t rely on enforcement from someone whose next job depends on not being a pain.
“Imagine if food safety inspectors were hired by the restaurants themselves. That’s the level of logic we’re applying to home building right now.”
The arguments against local inspections don’t hold up. Independent inspections cost less than defects, don’t delay quality builders, and provide a safeguard private certifiers simply can’t match.
D. “The System Works If Everyone Does Their Job”
That’s a big if—and it’s becoming less and less reliable as large project builders commodify their workforce.
Many of these volume builders are now staffed heavily with low-cost administrative personnel rather than trained construction professionals.
Some of the largest project home builders have aggressively offshored their administration departments—from estimating to documentation to customer service—in an effort to reduce overhead and boost margins. While this might work for processing spreadsheets or templated tasks, it often leads to a disconnect between what's happening on-site and what's being signed off in the back office.
Site supervisors are stretched across multiple jobs. Junior office staff—often without formal construction training—are tasked with preparing compliance documentation, filling out forms, or submitting inspection requests. They’re not equipped to spot technical errors or interpret standards, understand cause and effect in contracts, specifications, plan notations and they’re not expected to.
“It’s process over proficiency—and the process is full of holes.”
This shifts an enormous burden onto the private certifiers, who now act less like assessors and more like grade school teachers:
- They’re correcting poorly prepared forms.
- Requesting missing documents.
- Following up on basic oversights.
- And in many cases, having to explain to the builder’s admin team what should have been obvious to a trained construction professional.
This isn’t what certifiers are supposed to be doing. Their role is to verify compliance, not compensate for the builder’s lack of internal skill.
The irony? These same builders complain about certification delays—delays they caused by underinvesting in qualified staff. It’s a false economy. Cheaper internal staff mean more mistakes, which means more time spent by certifiers, which means longer wait times for approvals.
In short, builder cost-cutting is making certifiers do everyone’s job, and no one is left with the time or focus to do theirs properly.
“When builders hire by spreadsheet, and certifiers are left holding the red pen, you don’t get a quality home—you get a marked-up draft with no time for revision.”
As builders replace skilled professionals with low-cost admin staff, compliance becomes an afterthought—and certifiers are left cleaning up the mess. The result? More delays, more risk, and less oversight where it really counts.
VI. Steps Toward Implementation
It’s one thing to say the system needs fixing—it’s another to map out how we get there.
Reinstating mandatory local council inspections isn’t just a nostalgic throwback. It’s a practical, measurable reform with a track record of improving quality. But to make it work in today’s building environment, we need more than good intentions—we need structure, funding, and political will.
Here’s how we do it.
A. Create a National Framework for Mandatory Inspections
Right now, oversight is a patchwork. Some councils still perform limited inspections. Others do none. Builders in one postcode face a completely different level of scrutiny than builders a few kilometres away.
We need:
- A nationally consistent policy requiring independent inspections at key construction stages (slab, frame, roof/flashings, waterproofing).
- Uniform rules and standards that apply across all states and territories—so a builder in Brisbane, Ballarat, or Broken Hill is held to the same expectations.
- A system that removes builder choice from the equation—you don’t get to choose who checks your work.
This could be written into the National Construction Code (NCC) or tied to state-based legislation with federal support. The goal? Make it impossible for a home to be completed and sold without having passed independent checks at each critical stage.
B. Fund and Resource Local Councils
If we want councils to resume this role, we need to give them the tools and funding to do it properly.
That means:
- Hiring and training more qualified building inspectors.
- Providing digital infrastructure to manage inspection reports, scheduling, and defect tracking.
- Ensuring inspectors are paid fairly and insulated from industry pressure.
This isn’t a cost—it’s an investment in public protection. And it would create skilled jobs while rebuilding public trust in the system.
C. Tie Approvals and Stimulus to Quality Assurance
We’re constantly hearing about the need to increase housing supply. And yes, we do need more homes—but not at the expense of quality.
Governments should:
- Tie planning fast-tracks and housing stimulus funding to builder participation in independent inspection schemes.
- Make developer and builder eligibility for state and federal housing programs contingent on demonstrated quality assurance processes.
In short: if you want the benefits, you have to prove you’re building to a higher standard—not just ticking boxes and moving volume.
D. Empower Homeowners with Transparency
Let’s be clear: most homeowners don’t want to micromanage their build—but they do want transparency and assurance that their home has been built right.
We need:
- Inspection reports shared directly with homeowners—not just buried in builder records.
- Easy digital access to compliance certificates, photos, and approvals.
- A central, government-backed system for reporting non-compliance or concerns before handover.
Because the best time to fix a mistake is before it’s covered up.
Reinstating council inspections is doable—with the right funding, legislation, and leadership. And it’s not just about builders—it’s about restoring trust, transparency, and accountability for every new homeowner.
🧱 Conclusion: You Deserve a Home, Not a Headache
We’ve built ourselves into a corner.
In the pursuit of faster approvals, cheaper builds, and “cutting red tape,” we’ve stripped away one of the few safety nets homeowners had—independent, mandatory inspections at key build stages. And now we’re paying the price.
The stats don’t lie. The horror stories aren’t outliers. Poor workmanship, mould, structural cracking, and waterproofing failures have become features—not bugs—in Australia’s residential construction industry. Why? Because no one’s watching when it counts.
We’re not asking to hear the sound of one hand clapping—we’re asking for every trade and builder to be held to verifiable quality standards, not just superficial outputs and self-certified milestones. Builders self-certify, private certifiers juggle compliance and loyalty, and homeowners are left holding the hammer—and the repair bill.
But here’s the good news: we’re standing at a crossroads.
Right now, in the midst of global uncertainty and economic restructuring, Australia has an opportunity to re-imagine construction as a primary manufacturing output—one that builds wealth, resilience, and equity.
If we want homes to be a store of long-term value, then we need to treat home building as more than an economic statistic. It’s infrastructure. It’s shelter. It’s national productivity. That means:
- Investing in local jobs, training, and a skilled workforce
- Holding builders accountable to consistent, enforceable quality standards
- Building more homes, yes—but not just any homes. Well-built, efficient, and durable homes
- Delivering social and affordable housing that isn’t second-rate, but proudly constructed to last
This isn’t about going backward—it’s about choosing a better path than the last 30 years. The opportunity is right in front of us. We can either keep papering over the cracks or finally fix the foundations. And we all know which one will last—and add real value to our society.
If we want homes to be a store of national wealth, we need to stop building them like fast fashion. Mandatory inspections, skilled jobs, and a national commitment to quality can make housing not just more affordable—but more worthwhile.
❓ Frequently Asked Questions (FAQ)
1. Why were mandatory local council inspections removed in the first place?
They were phased out in the 1990s–2000s to reduce red tape and encourage housing supply. But in removing them, we also removed independent oversight—leading to a decline in construction quality.
2. How do private certifiers differ from council inspectors?
Private certifiers are hired (and paid) by the builder. Council inspectors were independent public officers. This change introduced a conflict of interest and eroded accountability.
3. What construction stages should be inspected?
The key stages are:
- Slab (including reinforcement, termite protection)
- Frame (tie-downs, bracing, structural integrity)
- Roof and flashings
- Waterproofing (in wet areas, balconies)
4. Don’t builders already follow the code?
Not always—and without independent verification, there’s little to stop shortcuts. Compliance on paper is easy. Compliance on-site is what matters.
5. Won’t more inspections increase build costs?
Slightly, yes. But fixing defects later is far more expensive. Independent inspections are a smart investment that prevent costly repairs.
6. Doesn’t this slow down construction?
Only if the builder’s admin and scheduling are poor. In fact, early intervention and defect detection can reduce costly delays and rework.
7. Are all private certifiers bad?
Not at all. But the model they work within is flawed. Even the best certifiers are constrained when their next job depends on keeping a builder happy.
8. How can I know if my build had independent inspections?
You usually can’t—unless you organise them yourself. That’s why reinstating mandatory council inspections matters: so every homeowner has this protection by default.
9. What role do industry groups play in this issue?
Many industry associations resist reform. They focus on defending their members’ business models—not necessarily on raising construction standards.
10. What can I do if I’m building soon?
You can engage your own independent inspector, ask your builder detailed questions about supervision and QA, and pressure your local MP to support legislative change.
Further Reading
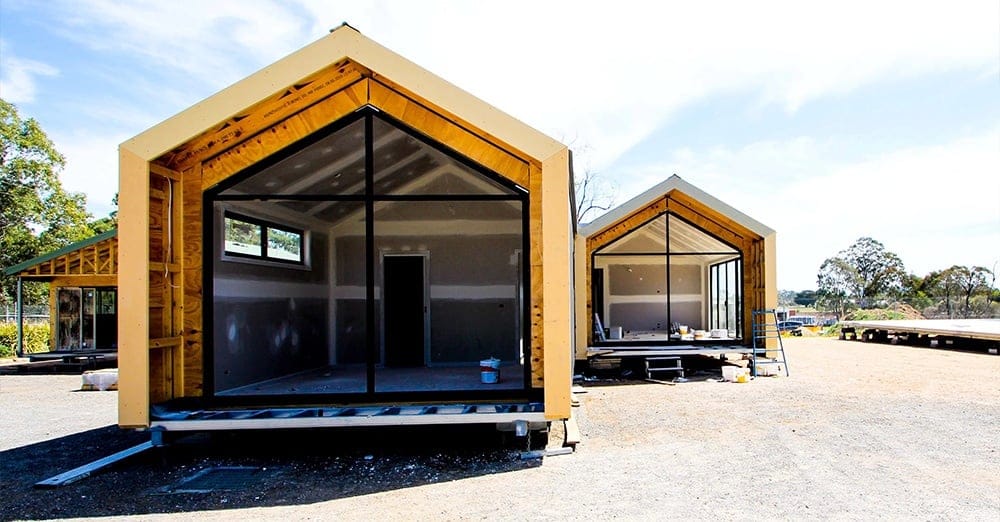