Take The Quiz On This Post
Read the post, then take the quiz—test your knowledge and see what you’ve learned!
Introduction
In recent years, the Australian residential construction industry has been under intense scrutiny, and for good reason. Defective homes, shortcuts in workmanship, and poorly enforced quality standards have left many home owners feeling frustrated and out of pocket. From foundation issues to inadequate finishes, it's clear that something needs to change.
However, while there’s plenty of finger-pointing and criticism, there's a noticeable lack of viable solutions being proposed. It’s easy to sledge, but it's time we start getting proactive with administrable solutions.
One of those solutions, which has been proven to work in commercial construction for years, is the Inspection Test Plan (ITP). ITPs are not some revolutionary new idea. They are a tried and tested method used on major commercial projects to ensure every stage of construction is properly inspected and verified before moving forward.
So why aren't they standard practice in residential construction?
It's time for residential builders to put on their big boy pants and start doing things right—no more excuses (or from any of the lobby groups)
Correct paperwork and proper quality management processes should be the norm, not the exception. By implementing mandatory ITPs and backing them with real regulatory oversight, we can significantly reduce defects, improve accountability, and ultimately deliver better homes to Australian families.
In this article, we’ll explore why mandatory ITPs, paired with rigorous oversight, are the key to fixing the quality crisis in residential construction.
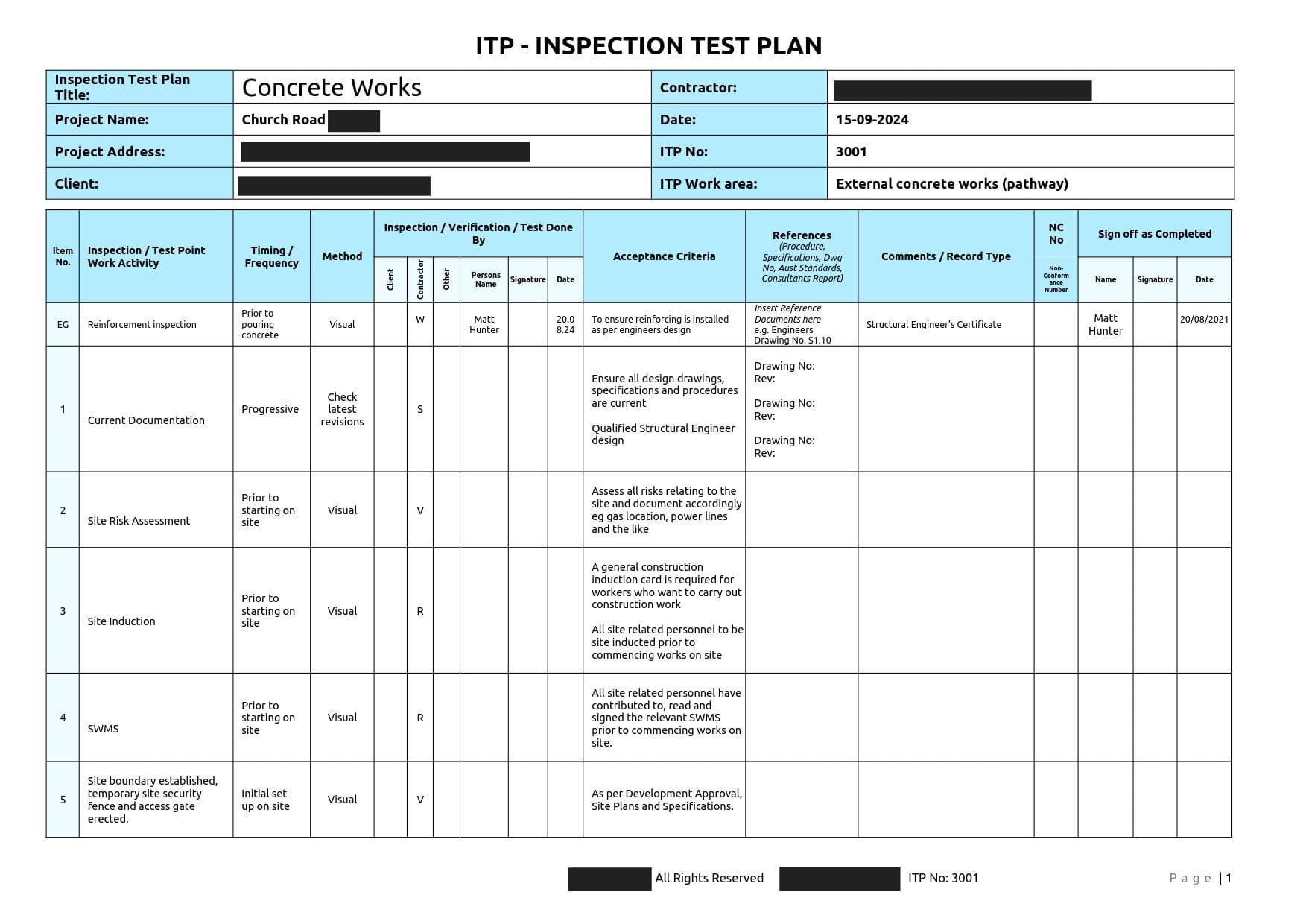
What is an ITP?
An Inspection Test Plan (ITP) is a structured document that outlines the specific inspection points throughout the construction process. It serves as a quality control tool that ensures all critical stages of work are inspected and verified before moving forward.
Think of an ITP as a checklist for construction quality—a plan that lays out exactly when and how inspections should take place to catch potential issues early on.
The key components of an ITP include:
- Inspection/Test Points: These are the stages of the project that require inspection, such as reinforcement placement before concrete is poured, as seen in the ITP for Concrete Works document (see below in the section titled: Example from the ITP for Concrete Works)
- Timing/Frequency: Specifies when the inspections should occur, whether at specific milestones or progressively throughout the project.
- Inspection/Verification Method: Details how the inspection should be performed, whether it's a visual check, a measurement, or verification against engineering drawings.
- Acceptance Criteria: Defines the standards that the work must meet, referencing relevant documents like Australian Standards or engineer specifications.
- Sign-off Requirements: Lists who is responsible for conducting and signing off the inspection, such as the contractor, client, or a third-party inspector.
An ITP ensures that the right checks are done at the right times. It creates a paper trail of accountability and offers transparency to all parties involved in the construction. By documenting each inspection, any issues that arise later can be traced back to the responsible party, providing clarity in case of disputes.
In commercial construction, ITPs are widely used, forming a backbone of a quality management system. They have proven to be effective in catching mistakes before they become costly or dangerous defects. So why is this process missing in residential construction?
By introducing mandatory ITPs in residential projects, home owners can have greater peace of mind knowing that their home is built to a high standard, with all necessary checks completed and verified.
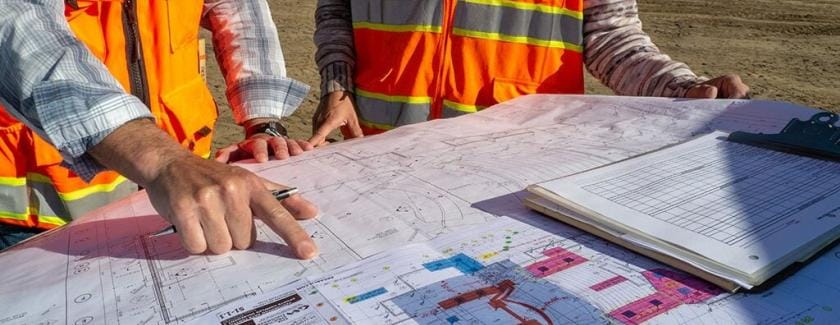
How ITPs are Administered
The administration of an ITP is an important part of the construction process. It’s not just about having a checklist—it's about ensuring that each inspection and test is carried out at the right time and to the right standard. The process begins at the very start of a project, when the contractor, engineers, and relevant stakeholders (YOU - The Client) develop the ITP to match the project’s requirements.
Key Steps in Administering an ITP:
- Planning the ITP: The first step is to outline all the major work activities that will be performed throughout the project. For example, in the ITP for Concrete Works we reviewed, there are specific inspection points, such as reinforcement inspection prior to pouring concrete. The ITP must identify each critical inspection stage—these are often referred to as hold points (when work must stop until the inspection is completed) and witness points (when the work can proceed but must be observed).
- Assigning Responsibilities: Each inspection or test needs a responsible party to carry out the task. This could be a contractor, site supervisor, client, or an independent inspector. The roles need to be clearly defined so that there is no ambiguity over who is accountable for the quality of the work at each stage. In some cases, external parties like structural engineers are required to sign off specific tasks, particularly when dealing with critical components like reinforcement or foundations.
- Verification and Documentation: After each inspection or test, a detailed record is made to document the outcome. This includes verifying that the work meets the acceptance criteria specified in the ITP, which often refers to Australian Standards, engineer specifications, or council-approved plans. The documentation process is critical because it provides a written record that can be referred back to if any issues arise later in the project. Each stage should also have sign-off signatures from all relevant parties.
- Hold and Witness Points:
- Hold Points: These are stages where work must stop until the inspection or test has been carried out and passed. For example, before concrete is poured, the reinforcement must be checked and signed off. If it doesn't pass inspection, the work is halted until the necessary corrections are made.
- Witness Points: Unlike hold points, work can proceed without interruption, but the inspection needs to be observed by the assigned party, ensuring the work aligns with the plan.
- Progressive Checks: Some tasks, such as excavation or bulk earthworks, are checked progressively. This ensures that different stages of the same work are inspected at various points, minimising the chances of errors accumulating over time. Progressive checks can help identify issues before they compound, keeping the project on track and ensuring quality is maintained.
- Final Sign-Off: Once all stages of the work have been completed and inspected, a final sign-off is required to verify that the entire process has met the project's standards. This final step ensures that the construction work is fully compliant with the initial plans and that any deviations or issues have been properly documented and addressed.
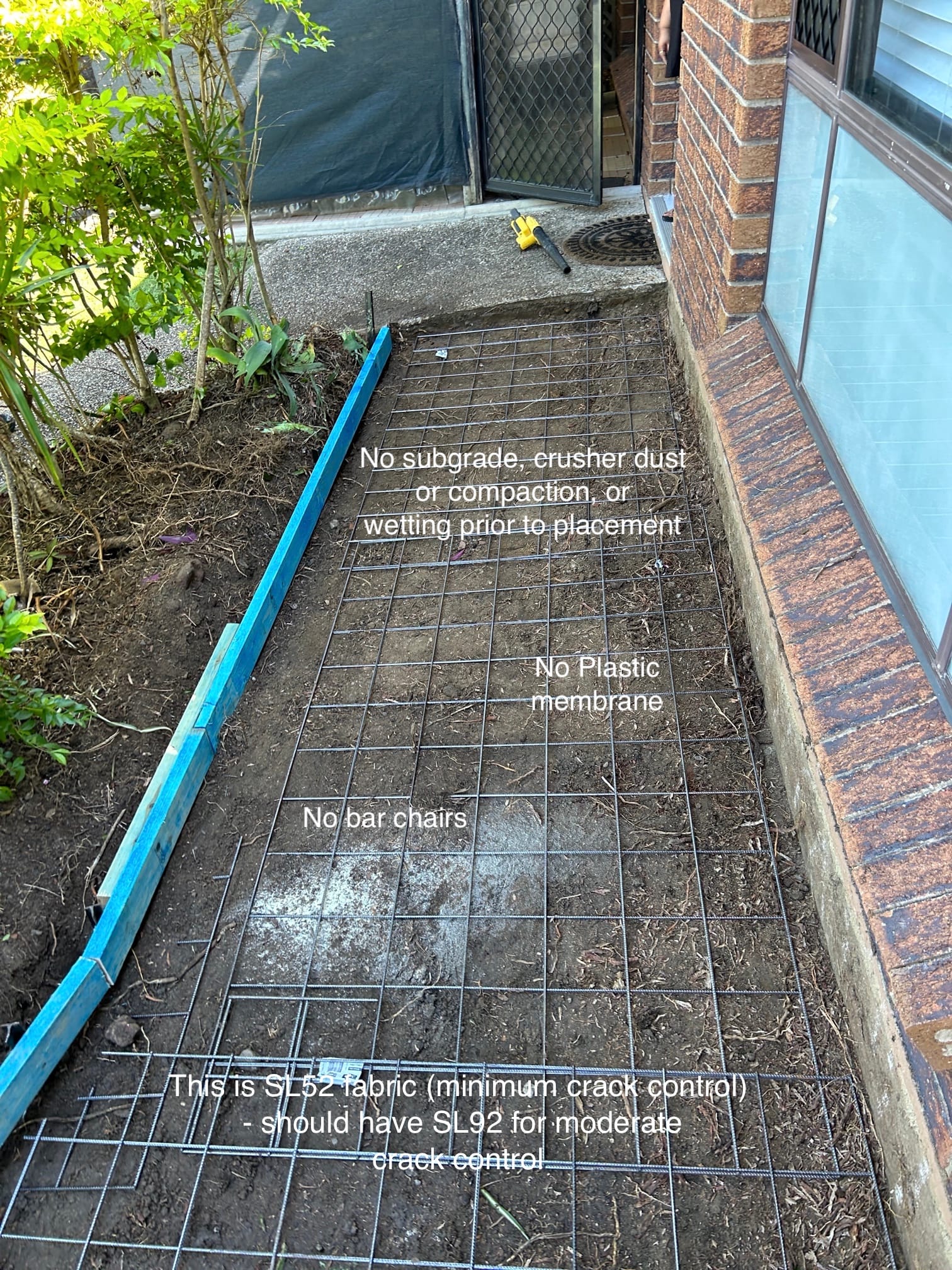
Example from the ITP for Concrete Works:
Let’s look at a specific example from the ITP for Concrete Works. One key inspection point is the reinforcement inspection, where the engineer or site supervisor/inspector must verify that the steel reinforcement is in place and meets the design specifications before concrete can be poured. This is a hold point—meaning that work cannot continue until the inspector signs off that the reinforcement is correctly placed.
The acceptance criteria for this step reference the engineer’s design and relevant Australian Standards, to ensure that the structure is built correctly and safely.
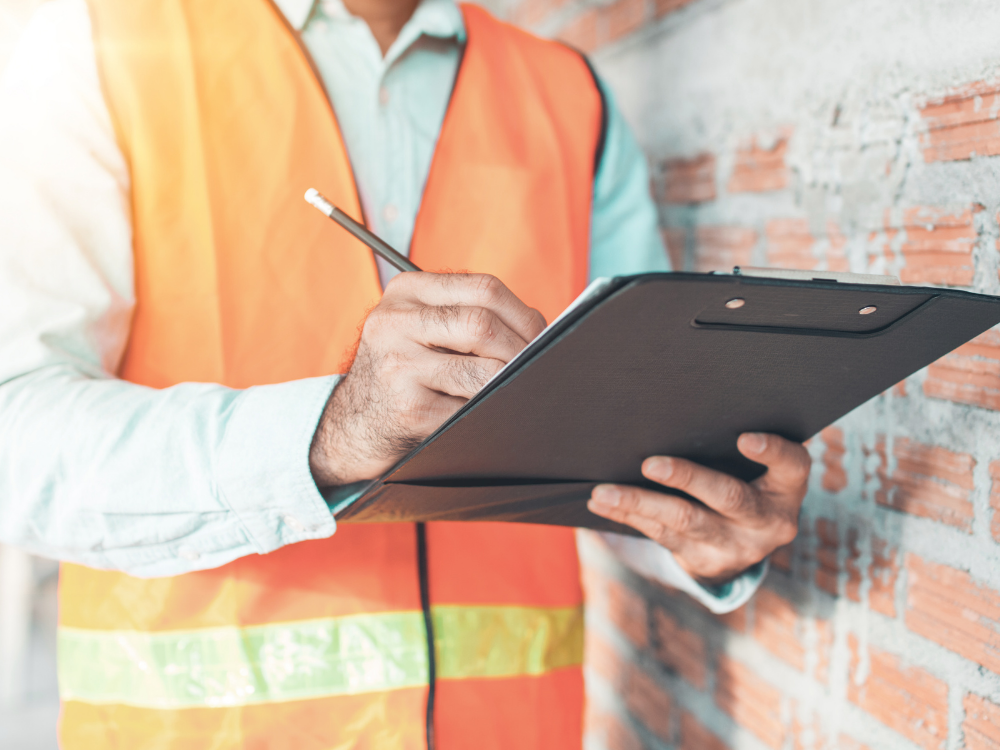
The Role of Regulatory Oversight in ITPs
The effectiveness of ITPs is heavily dependent on regulatory oversight. Without adequate supervision, there is a real risk that tradespeople and contractors may bypass inspection points or fail to carry out the proper checks and measures. This is especially true in residential construction, where the pace of work is often pushed by tight deadlines, a focus on turnover and less than stellar supervision (or quality management staff)
Why Oversight Matters
Regulatory oversight introduces an external layer of accountability. It ensures that contractors are not just going through the motions to tick off items on an ITP but are genuinely verifying that each phase of construction meets the necessary standards.
Without oversight, it's easy for builders to cut corners and rush through inspections, especially when there are no significant consequences for non-compliance.
In the past, council inspectors played a important role in overseeing residential construction. They were responsible for ensuring that aspects of a building were constructed according to local regulations and standards. Over time, however, the role of council inspectors in the residential construction process has diminished, leaving a gap in the enforcement of quality standards.
ITPs Alone Are Not Enough
An ITP on its own is just a document—it becomes effective only when there is an enforcement mechanism in place. Currently, many residential builders and trades operate in an environment where there is little to no “fear factor”—that is, no immediate repercussions for failing to follow proper inspection procedures. Builders and tradespeople are often under pressure to complete jobs quickly to maximise turnover, and in this environment, quality can suffer. To learn more about the tradeoff between time cost and quality, read our post below:
Without an external body to ensure inspections are properly conducted, contractors may skip critical hold points or approve work that doesn't meet required standards. The current system is largely self-regulated, placing the responsibility on construction company management to uphold strong ethics and demonstrate effective quality management and control.
This is particularly problematic in residential construction, where home owners often don’t have the technical knowledge to identify these shortcuts until it’s too late.
Reintroducing Council Inspectors
One of the most effective ways to close this gap is to reintroduce council inspectors as part of the residential construction process. These inspectors would act as independent, third-party enforcers of ITPs, ensuring that all inspection points are followed and that quality is not sacrificed for speed.
By having an external authority with the power to hold work at critical points and enforce compliance, both builders and trades would be motivated to adhere to the ITP and prioritise quality over quantity.
There would be less incentive to rush through work or bypass inspections because the risk of being caught and facing penalties would outweigh the short-term gains of cutting corners.
The Commercial Construction Comparison
In commercial construction, where ITPs are commonly used, regulatory oversight is much stricter. There are often multiple layers of checks, with independent engineers, council officers, and third-party inspectors verifying each stage of construction.
This level of scrutiny ensures that quality is better maintained (yes, I know a bold claim) throughout the project, and as a result, defects and rework are minimised. By adopting a similar approach in residential construction, we could significantly reduce the incidence of poor-quality homes.
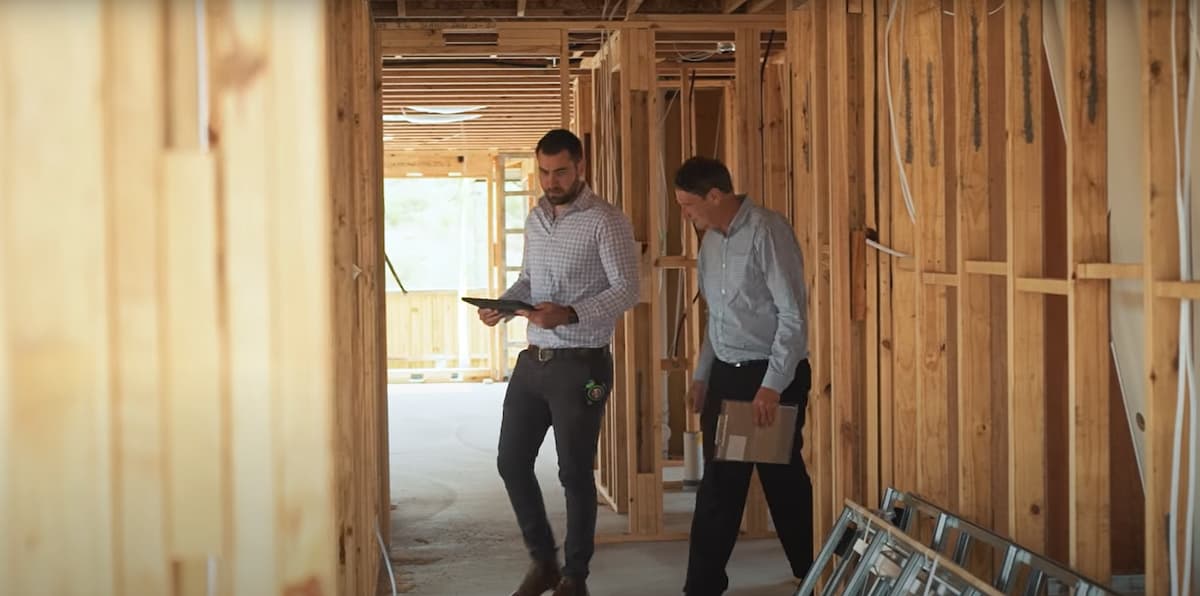
The Role of Private Certifiers vs. Council Inspectors in Quality Control
In the residential construction, there is often confusion about the role of private certifiers. Many home owners assume that certifiers are responsible for ensuring the overall quality of a build, but this is not the case.
Private certifiers play a specific and limited role focused on compliance rather than quality control.
What Private Certifiers Do
Private certifiers are responsible for assessing whether building work complies with relevant building codes and regulations, such as the National Construction Code (NCC) and local planning laws. Their role includes:
- Carrying out building assessments to ensure compliance with approved plans and building standards.
- Inspecting mandatory stages of the construction process (e.g., structural components of a Class 1a single-detached dwelling).
- Requesting designs, certificates, and documentation to determine whether the work complies with legal requirements.
- Issuing compliance certificates and enforcement notices when necessary.
- Certifying completed stages of work and issuing final certificates of occupancy or completion.
While private certifiers inspect certain aspects of the build to ensure legal compliance, their scope is limited. They do not monitor the overall quality of workmanship or materials used, nor do they supervise the job site or ensure that the builder is meeting contractual obligations. For example, certifiers will check that structural elements like framing or foundations meet engineering requirements, but they won't ensure that the finishes (like painting or tiling) are of high quality or that the builder is sticking to timelines or specifications in the contract.
What Private Certifiers Don’t Do
Certifiers are not involved in:
- Quality control or material finishes (e.g., ensuring paintwork is done correctly or timber finishes are the right color).
- Supervising the job site or ensuring that a builder follows the terms of their contract.
- Enforcing Workplace Health and Safety standards on site, which falls under the Workplace Health and Safety Act.
- Ensuring subcontractors comply with their contracts with the builder or owner.
This means that there are aspects of construction that certifiers simply do not oversee, leaving gaps in the quality control process. Home owners who expect certifiers to act as watchdogs for the entire build can be disappointed when issues like poor finishes or inadequate workmanship go unnoticed.
This is where the need for council inspectors comes in.
The Role of Council Inspectors in Quality Assurance
Council inspectors historically played a key role in maintaining quality standards in residential construction. Unlike certifiers, who focus on compliance, council inspectors would monitor overall construction quality, ensuring that builders adhered to best practices in areas like workmanship, material use, and safety. By focusing on quality beyond the strict boundaries of compliance, council inspectors provide a more comprehensive layer of oversight, much like that of a superintendent role (for which builders pay for the privilege)
Council inspections can fill the gaps left by certifiers by:
- Checking for quality issues in areas that certifiers do not review, such as material finishes, overall workmanship, and adherence to contract specifications.
- Acting as an independent authority to ensure that builders are not cutting corners in the rush to complete a project quickly.
- Offering home owners peace of mind by providing an additional layer of scrutiny over the construction process.
The Need for Cooperation Between Certifiers and Council Inspectors
To ensure that both compliance and quality are maintained throughout a construction project, there must be a clear relationship and escalation process between private certifiers and council inspectors. Without proper communication and oversight, there is a risk that builders could try to "pay off" certifiers or find loopholes in the compliance process to avoid addressing quality issues.
An effective escalation process should include:
- Cross-reporting mechanisms, where certifiers can flag concerns to council inspectors if they notice quality issues outside of their purview.
- Regular site inspections by council inspectors to check areas not covered by the certifier's scope, such as finishes and workmanship.
- An accountability system where both certifiers and council inspectors are responsible for ensuring that any issues they observe are reported and addressed.
- Transparency between certifiers and inspectors, ensuring that any failures or construction issues are properly documented and that builders are held accountable for resolving them.
Ensuring Accountability and Preventing Conflicts of Interest
One of the biggest concerns with the current system is the potential for conflicts of interest between builders and certifiers. Without proper oversight, there is a risk that builders could exert influence over certifiers, leading to corners being cut in the name of compliance. To prevent this, there must be strict accountability measures in place to ensure that certifiers are not being unduly influenced by builders and that any issues with construction quality are properly escalated.
Both private certifiers and council inspectors should be held accountable for their roles in ensuring that construction projects meet both legal and quality standards. When certifiers identify issues, there must be a process for escalating these concerns to council inspectors, who can then take further action to address problems that fall outside the certifier’s scope of work.
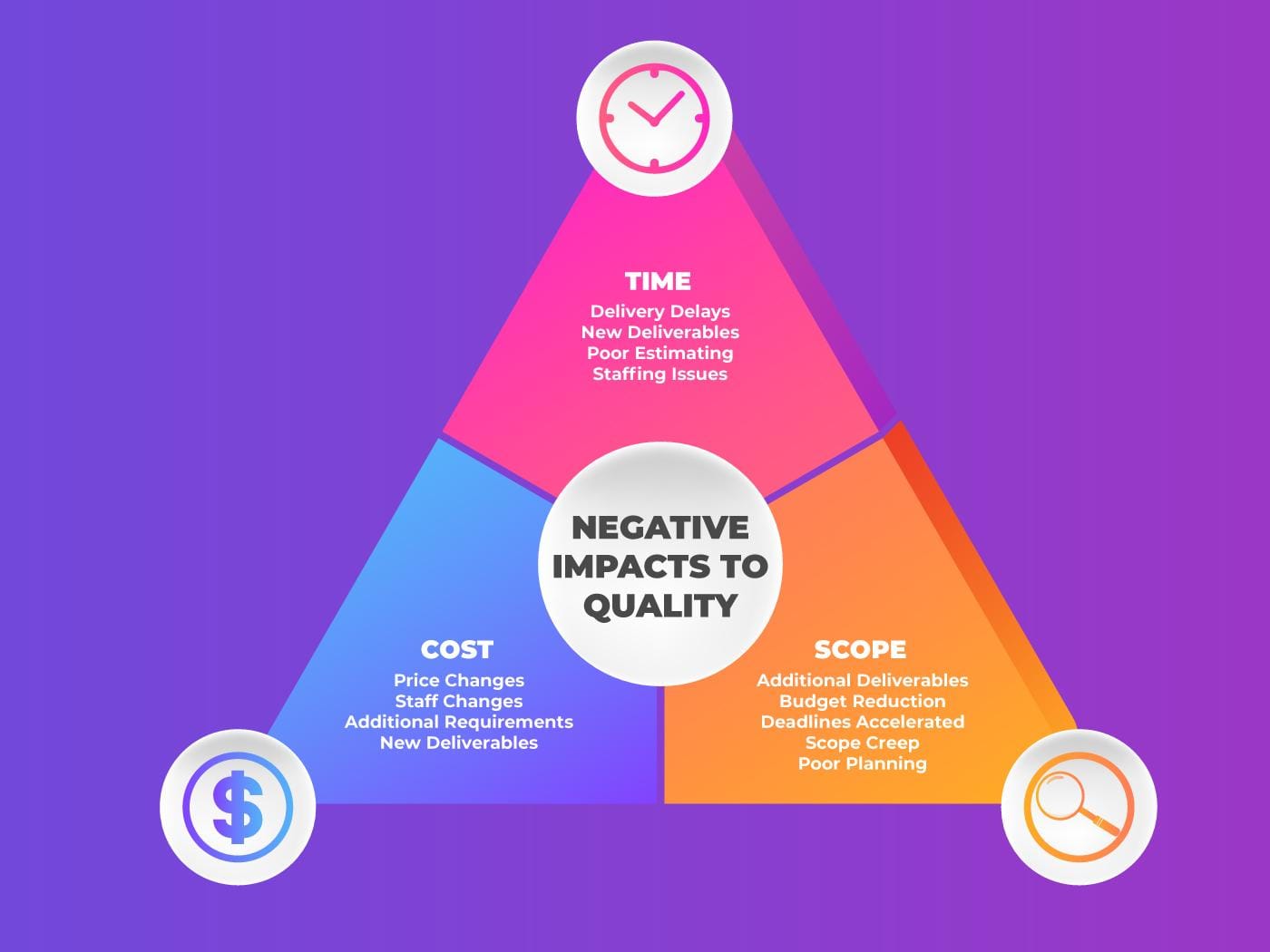
Why Builders and Trades Prefer Speed Over Quality
In the residential construction industry, the primary driving force for both builders and trades is often speed—getting the job done as quickly as possible to move on to the next project. While this focus on turnover may make sense from a financial perspective, it creates significant risks in terms of quality. When speed becomes the priority, critical inspection and verification steps are often rushed or neglected altogether.
The Pressure of Tight Timelines
Builders face pressure to complete projects within strict timelines. Whether it's to meet contractual deadlines, keep clients happy, or maintain cash flow, there is always a sense of urgency in residential construction. Tradespeople, who are usually subcontracted by builders, are also incentivised to complete their tasks quickly.
The faster they finish one job, the sooner they can move on to the next and earn more income.
This cycle of rushing from job to job often leads to compromised quality. The emphasis on speed means that hold points and inspections, which are meant to act as safeguards, are sometimes viewed as time-consuming obstacles. Without proper regulatory oversight (as we discussed earlier), these safeguards are easily bypassed in the race to finish.
Builders' Financial Incentives
For builders, time is money. The longer a project drags on, the higher the costs. Labour, materials, and overheads all add up, so builders are motivated to keep the project moving as quickly as possible.
In this context, pausing work to conduct thorough inspections, especially those required by ITPs, can be seen as a delay rather than a necessity. This attitude is further compounded by the competitive nature of the construction industry, where delays can hurt a builder’s reputation and bottom line.
As a result, the quality vs. time trade-off often tilts heavily in favour of time.
The temptation to cut corners is strong, especially when there is no immediate accountability for shoddy work. Unfortunately, home owners are usually the ones left dealing with the fallout in the form of defects, costly repairs, and long-term issues that could have been prevented with proper inspections and oversight.
Trades and the Push for Turnover
Tradespeople, too, have a vested interest in completing their work as quickly as possible. Many trades are paid on a per-project basis, meaning their income is tied directly to how quickly they can finish one job and move on to the next. This creates an environment where trades are incentivised to prioritise speed over thoroughness, leading to rushed jobs and missed inspection points.
Without proper enforcement of ITPs or third-party oversight, trades can often “sign off” on inspections without truly verifying that the work has been done to the necessary standard.
This lack of accountability results in defects being embedded into the construction process, which may not be noticed until much later—when it’s too late for simple fixes.
The Culture of Speed in Residential Construction
Unlike commercial construction, where ITPs are enforced and there are multiple levels of checks and balances, residential construction operates in a far more relaxed regulatory environment. The culture in residential construction prioritises completion over compliance, and the current system allows for this to continue unchecked.
While builders and trades may feel that they are doing what's necessary to meet tight deadlines, the long-term costs of rushing through the construction process are significant. Poor-quality homes lead to increased defects, home owner dissatisfaction, and a tarnished reputation for the builder in the long run.
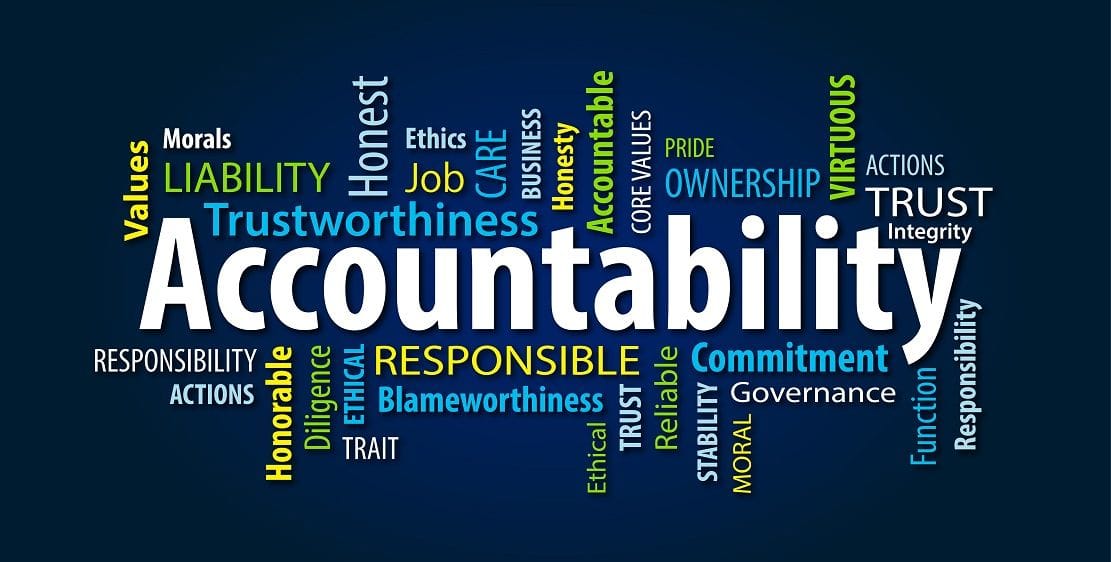
The Importance of Accountability
In any industry, accountability is key to maintaining high standards, and residential construction is no exception.
Unfortunately, the current system allows for a significant lack of accountability, especially when it comes to following proper inspection procedures and ensuring quality.
Without clear accountability, trades and builders can easily cut corners, skip inspections, or rush through work without thoroughly checking for errors. As a builder, I don’t trust any trade or builder to do what they say they'll do. The only way to ensure compliance in construction is to verify it yourself using a standardised assessment, quality control checklist.
Why Accountability Matters
Accountability ensures that everyone involved in a construction project, from the builder to individual tradespeople, is responsible for their actions. When there’s a clear system of checks and balances, it becomes much harder for poor-quality work to slip through unnoticed. This is where mandatory ITPs can play a pivotal role.
By requiring ITPs on all residential construction projects and enforcing them through proper regulatory oversight, you create a paper trail of responsibility. Each inspection is documented, and each stage of the work must be signed off by the relevant parties. This means that if defects or issues arise later on, there’s a clear record of who was responsible at each stage of the process.
Hold Points: A Tool for Accountability
One of the most important elements of an ITP is the hold point—a stage in the construction process where work must stop until the inspection has been completed and approved. Hold points are designed to act as a safety net, ensuring that no further work is carried out until the current phase has been verified as meeting the necessary standards.
Hold points create accountability because they require someone, whether it's a contractor, inspector, or site supervisor, to physically inspect the work and sign off that it meets the required criteria. Without this sign-off, the work cannot proceed. This creates a forced pause in the project, ensuring that all critical steps are properly checked.
However, in many residential construction projects, these hold points are either ignored or signed off without a proper inspection. This is often due to the pressure to finish work quickly or the lack of oversight to enforce them. Mandatory ITPs, combined with strong regulatory oversight, would make it much harder for contractors to skip hold points or falsify inspection records.
The Role of Regulatory Bodies in Enforcing Accountability
Currently, the residential construction industry operates with minimal oversight compared to its commercial counterpart. As discussed earlier, the decline in council inspector involvement has created a significant gap in accountability. Builders and trades are left to self-regulate, which often leads to quality being sacrificed for the sake of speed and cost-saving.
By reintroducing council inspectors into the process and enforcing mandatory ITPs, accountability can be restored. Regulatory bodies would ensure that all inspection points are adhered to and that tradespeople are held responsible for the quality of their work. Without this oversight, the temptation to rush through projects and skip inspections will continue to undermine construction quality.
Long-Term Benefits of Increased Accountability
When accountability is enforced, everyone involved in the construction process must take their responsibilities seriously. Trades are less likely to rush through work if they know it will be properly inspected, and builders are more likely to prioritise quality over speed when they know that their work will be scrutinised.
For home owners, increased accountability means fewer defects, better-quality homes, and long-term savings. It also reduces the likelihood of costly legal disputes between home owners and builders over construction defects, as the root cause of the problem—poor-quality work and skipped inspections—will have been addressed during the construction process.
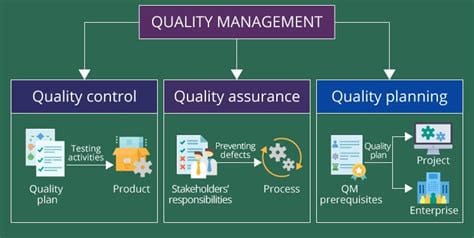
How Mandatory ITPs Improve Construction Quality
Mandatory Inspection Test Plans (ITPs) serve as a structured approach to ensuring quality at every stage of the construction process. When properly implemented and enforced, ITPs help catch potential issues early on, preventing defects and ensuring that each component of the build meets the required standards. By making ITPs a mandatory part of the residential construction process, the industry can shift from a reactive approach—where defects are addressed only after they arise—to a proactive one, where quality is assured from the start.
Preventing Defects Early
The main benefit of mandatory ITPs is their ability to catch defects before they become major problems. Every construction project has critical stages where certain elements, such as foundations, framing, and roofing/flashings, waterproofing, must be inspected before moving on to the next phase. These stages represent points where mistakes, if unnoticed, can compound into larger issues later on. For example, incorrect reinforcement placement or size used before pouring concrete could result in structural weaknesses that aren’t detected until the building has settled, requiring costly repairs.
With mandatory ITPs in place, these critical stages are treated as hold points—meaning that the work cannot progress until it has been inspected and approved. This ensures that any errors or omissions are addressed immediately, saving time and money in the long run. By preventing defects at these early stages, home owners are less likely to experience issues such as cracks, leaks, or structural failures, which can be both expensive and stressful to fix.
Ensuring Consistent Quality Across All Projects
Another advantage of mandatory ITPs is that they create a consistent framework for quality across all construction projects. By establishing clear inspection points and acceptance criteria, builders are required to meet the same high standards regardless of the project. This helps eliminate variations in quality that can arise from different trades or contractors working on the same site.
ITPs also provide transparency to home owners.
With a detailed record of all inspections, home owners can see exactly what was checked and when. This gives them confidence that the work on their home was performed to the highest standard and that any potential issues were addressed during construction, rather than after the fact.
Reducing the Need for Rework
One of the most significant costs in construction is rework—having to go back and fix mistakes after the fact. Rework not only delays the project but also increases costs, as additional labour and materials are required to correct the issue. Mandatory ITPs help reduce the likelihood of rework by ensuring that work is done correctly the first time. By requiring inspections at critical stages, errors are caught before they become embedded into the structure.
For builders, reducing rework means improved profitability and efficiency. For home owners, it means fewer disruptions and a smoother construction process, with fewer unexpected costs or delays. The added scrutiny provided by ITPs ensures that everyone involved is working toward the same goal: delivering a high-quality home on time and within budget.
Creating a Culture of Accountability and Quality
Making ITPs mandatory also fosters a culture of accountability within the construction industry. When builders and tradespeople know that their work will be thoroughly inspected and documented, they are more likely to take their responsibilities seriously. This shift in mindset encourages trades to focus on doing the job right the first time, rather than cutting corners to meet tight deadlines.
Additionally, by requiring proper documentation and sign-offs at each inspection point, ITPs create a clear chain of accountability. If an issue arises, it’s easy to trace back to the point in the construction process where the problem occurred and identify who was responsible. This level of transparency makes it much harder for trades to rush through inspections or overlook important steps, as there is a record of every action taken.
Assessing Builders Based on Their Quality Management System (QMS)
For home owners, choosing the right builder is one of the most important decisions in the construction process. Unfortunately, many people rely on a builder's marketing and PR efforts to make this choice, but as anyone in the industry knows, a glossy brochure or a well-designed website doesn't necessarily reflect the true quality of a builder's work. Instead,
home owners should assess builders based on their Quality Management System (QMS) as this is the clearest indicator of how committed a builder is to delivering a defect-free, high-quality home.
What is a Quality Management System (QMS)?
A QMS is a structured system of processes and procedures that a builder follows to ensure that every aspect of their work meets the required standards of quality. A builder with a strong QMS has detailed plans for inspections, testing, documentation, and accountability and review at every stage of the build and after handover. This system ensures that quality is not left to chance or individual discretion but is instead an integral part of the construction process.
A well-designed QMS will:
- Include regular inspections and sign-offs at key stages (ITPs) ensuring that defects are caught early.
- Ensure documentation is maintained for each stage, providing a record of compliance and quality assurance.
- Incorporate processes for corrective actions, so that any issues identified are addressed promptly and properly.
- Be aligned with industry best practices and relevant standards, such as the National Construction Code (NCC) and Australian Standards.
Let Actions Speak Louder Than Words
When evaluating builders, home owners should focus on demonstrable actions, not just promises. Builders often use marketing and PR to paint a picture of their reliability and quality, but the truth lies in the processes they follow. This is where a strong QMS comes into play. By asking builders to show evidence of their QMS in action, potential clients can get a real sense of how committed a builder is to quality.
Instead of relying on a builder’s marketing claims, home owners should ask for:
- Examples of their QMS in previous projects.
- Details about their inspection processes and how they document compliance.
- A walk-through of their quality control procedures, including how they handle defects and issues when they arise.
By focusing on a builder’s actual processes and track record, clients can better assess whether the builder is truly committed to delivering a high-quality home.
You can download our 102 point checklist to help you assess your builder before getting into bed with them, click on the button below to view and download (opens Docsend a Dropbox Company):
Competition Based on Quality Management
Builders should be encouraged to compete based on their QMS rather than relying on marketing campaigns or flashy showrooms (ahem M e t r i c o n - or whomever Japanese Company now owns you since you fumble fucked yourself due to your high overheads/operational costs - they vastness of middle and upper management - just what fixes grass roots quality onsite - talkers, not doers!).
When builders are transparent about their quality management processes, it gives home owners a real opportunity to compare substance over style. The question home owners should ask isn’t just, “Can this builder construct my home?” but rather,
“Does this builder have a system in place to guarantee that the home will be built to a high standard?”
Builders who are serious about quality will welcome this competition, as it allows their actions and processes to speak louder than any marketing claim. Those with a strong QMS should actively promote it as a key differentiator, showing potential clients why their system is more robust and reliable than their competitors.
Marketing vs. Reality: Trusting Demonstrable Facts
In an industry plagued by defects and unfinished homes, it’s becoming increasingly difficult for home owners to trust marketing and PR alone. Many builders make grand promises in their brochures or online, but these promises often fall short when the actual work begins. The best way to build trust with potential clients is through transparency and proof.
Home owners should be encouraged to ask tough questions, such as:
- "How does your QMS prevent defects?"
- "Can you provide evidence of your inspection and quality control processes?"
- "How do you handle defects or rework when they occur?"
- What lessons have you learnt from the past and how have you incorporated this into design, material or process changes?
By focusing on demonstrable facts—such as a builder’s QMS, past projects, and the transparency of their processes—home owners can make more informed decisions. Builders who rely on marketing alone should not be trusted blindly. Instead, clients should demand proof of the builder's commitment to quality, letting actions speak louder than words.
The Case for Reintroducing Council Inspectors
One of the key elements missing in today’s residential construction industry is effective third-party oversight. While ITPs create a framework for ensuring quality, their success hinges on the ability to enforce them. This is where the reintroduction of council inspectors into the residential construction process could make a significant impact.
The Role of Council Inspectors in the Past
Historically, council inspectors played a crucial role in residential construction by acting as independent enforcers of building standards. These inspectors were responsible for ensuring that every aspect of a construction project, from the foundation to the final finishes, met local building codes and regulations. They provided an additional layer of oversight, catching issues that builders or tradespeople might have missed or intentionally overlooked.
However, over time, the role of council inspectors in residential construction has diminished. Various factors, such as budget cuts, deregulation, and a shift towards self-regulation in the industry, have led to a decline in the frequency and effectiveness of inspections. This has resulted in a gap in oversight, allowing some contractors to bypass critical inspections and take shortcuts that compromise quality.
The Need for Independent Oversight
Reintroducing council inspectors would help bridge this gap by providing an independent third-party check on the work being done. Unlike builders or tradespeople, who may be tempted to rush through inspections to meet deadlines or reduce costs, council inspectors have no vested interest in the outcome of the project. Their sole responsibility is to ensure that the construction work complies with the required standards.
Council inspectors would act as the enforcement arm of mandatory ITPs, ensuring that every hold point is properly adhered to and that no stage of the project proceeds without the necessary inspections. This independent oversight would make it much harder for builders to cut corners or rush through inspections, as the presence of a council inspector would add an extra layer of accountability.
Addressing the Housing Crisis with Improved Quality
The benefits of reintroducing council inspectors extend beyond individual projects. The current housing crisis in Australia, as highlighted in recent news articles, is driven in part by a focus on increasing the quantity of homes being built while neglecting quality. This approach has led to a growing number of homes with defects, which in turn increases costs for home owners and delays the delivery of safe, liveable housing.
By bringing back council inspectors and enforcing mandatory ITPs, we can address this crisis by ensuring that new homes are built to a higher standard. Fewer defects mean fewer costly repairs, which not only benefits homeowners but also helps reduce the long-term costs associated with housing. Improved construction quality would lead to more reliable, long-lasting homes that meet the needs of Australian families, helping to alleviate the pressure on the housing market.
Reinstating Trust in the Construction Process
For many home owners, the construction process can feel opaque and intimidating. Without technical knowledge, it’s difficult for the average home owner to know whether their builder is following the correct procedures or cutting corners. The reintroduction of council inspectors would provide home owners with greater peace of mind, knowing that an independent authority is overseeing the construction of their home.
This would also help to restore trust in the construction industry as a whole. Home owners would have confidence that their home is being built to the highest standards, while builders and trades would be held accountable for the quality of their work. The end result would be a stronger relationship between builders and clients, with fewer disputes and a more transparent construction process.
Overcoming the Challenges of Implementing Mandatory ITPs
While mandatory ITPs present a clear solution to improving construction quality, their implementation does come with challenges. These challenges range from resistance within the industry to the perceived increase in costs and time. However, when weighed against the long-term benefits of fewer defects and improved home owner satisfaction, these obstacles can be overcome with thoughtful planning and execution.
Industry Resistance
The most significant challenge to implementing mandatory ITPs is likely to come from within the construction industry itself.
Builders and tradespeople, already under pressure to complete projects quickly and within budget, may see ITPs as an additional layer of bureaucracy that slows down the process and increases costs.
For many, the idea of introducing more paperwork and inspections may seem counter productive in an industry where speed is often prioritised.
Addressing Industry Concerns
To overcome this resistance, it’s important to communicate the long-term benefits of ITPs. While there may be some initial push back, builders and trades need to understand that implementing ITPs can actually lead to fewer costly mistakes, less rework, and improved client relationships. When work is done right the first time, it reduces the risk of disputes and ensures smoother project completion. In the long run, this can enhance a builder’s reputation and lead to more referrals and repeat business.
Additionally, with proper training and education, builders and trades can learn to incorporate ITPs into their workflow without causing significant delays. By making ITPs a standard part of the project planning process, they can be integrated seamlessly into the construction schedule, minimising disruptions.
Perceived Increase in Costs
Another common concern is the potential for increased costs. Builders may worry that the added inspections and documentation required by ITPs will raise their expenses, which could be passed on to the homeowner. However, the reality is that the cost of not implementing ITPs—such as rework, defect rectification, and potential legal disputes—often outweighs the upfront costs of proper inspections.
While there may be some initial expenses associated with training and hiring additional personnel to manage ITPs, these costs should be seen as an investment in quality. The reduction in defects, rework, and client dissatisfaction will ultimately save money in the long run. Moreover, by making ITPs mandatory across the industry, it levels the playing field, ensuring that all builders and trades are held to the same standards.
When weighing the cost of implementing ITPs and a quality management system against the long-term expenses of maintenance, cheap materials, and poor-quality control, the choice becomes clear.
The upfront costs of a well-structured quality management process may seem high, but they pale in comparison to the cumulative expenses of fixing defects, redoing substandard work, and replacing low-quality materials.
In contrast, builders who invest in ITPs save on costly rework, minimize disputes, and enhance their reputation for delivering reliable homes. While some may argue that the immediate cost of ITPs could tighten margins, the long-term benefits—fewer defects, satisfied clients, and reduced liabilities—far outweigh these concerns, making ITPs a smart, future-focused investment.
Government and Regulatory Support
One way to mitigate the cost concerns is to ensure that the government and regulatory bodies provide adequate support for the implementation of ITPs.
This could take the form of subsidies for training, financial incentives for builders who adopt ITPs, or even funding to reintroduce council inspectors as part of the oversight process.
By working with the industry rather than imposing regulations from above, governments can help ensure a smooth transition to mandatory ITPs. Lets use a honey not stick approach to luring builders away from the dark side and towards the light (yes, a star wars analogy).
Learning from Other Industries
The construction industry is not the only one to face challenges when implementing stricter quality control processes. Other industries, such as manufacturing and engineering, have long relied on inspection plans and quality management systems to ensure the integrity of their products. By looking to these industries for examples of how to successfully implement mandatory ITPs, the construction sector can learn valuable lessons.
For example, in manufacturing, Quality Management Systems (QMS) are used to ensure that every stage of production meets strict quality criteria. These systems are supported by rigorous inspections, detailed documentation, and independent third-party audits. By adopting a similar approach in residential construction, builders can ensure that their projects are delivered to the highest standards without compromising on time or cost.
It makes no sense that you can track your pizza through every stage of production, yet construction offers nothing even remotely comparable. Yes, tools like Builder Trend exist, but in terms of investment in technology, R&D, and process improvement, the construction industry lags far behind.
The Long-Term Benefits of Implementing ITPs
Ultimately, the challenges of implementing mandatory ITPs are outweighed by the long-term benefits they provide. Fewer defects, less rework, happier home owners, and a stronger reputation for quality—all of these are achievable outcomes with the right quality management processes in place. While it may take time for the industry to adjust to these changes, the end result will be a more reliable, transparent, and trustworthy construction process for all involved.
Why Slower Build Times Aren’t Necessarily a Bad Thing
One of the biggest concerns about introducing stricter quality management processes, like mandatory Inspection Test Plans (ITPs), is the potential for increased build times. While it’s true that adding more layers of inspection and oversight will likely extend construction timelines, this isn’t necessarily a bad thing—especially in a market where fast construction has led to a noticeable decline in quality.
The Reality of Current Build Times
Right now, residential construction projects are facing delays regardless of whether ITPs are in place. Labour shortages are a significant issue, with not enough tradespeople available to meet the current demand for new homes. As a result, build times are already longer than expected, and the quality of work being done during these rushed projects has reached an all-time low.
This begs the question: if build times are blowing out anyway, wouldn’t it make more sense to focus on quality rather than rushing through to meet unrealistic deadlines?
Homeowners are increasingly being forced to choose between fast and flawed construction or slow and solid builds. When considering the long-term benefits, slower but quality-assured construction is a much better option.
Fast Construction Leads to Long-Term Problems
Rushed construction often leads to defects, rework, and costly repairs down the line. As noted in your article, "Time, Cost, and Quality: Why This is the Holy Trinity and Most Important Consideration for Your New Home", the relationship between these three elements is a delicate balance. When speed is prioritised over quality, cost savings in the short term often turn into expensive fixes later. The result is a home that may look good on the surface but is prone to hidden issues like structural defects, leaks, or electrical failures that could have been avoided with proper inspections.
A fast build may seem appealing, especially when facing long wait times for housing, but the reality is that "fast" often means "flawed." Without sufficient checks, trades are more likely to cut corners, and critical steps in the construction process may be rushed or ignored altogether. The result? A house that requires constant maintenance and repair, costing home owners time, money, and stress for years to come.
Slower Build Times, Better Results
Now consider the alternative: slower, quality-assured builds. When ITPs are implemented, each stage of construction is thoroughly inspected, and potential defects are addressed early on. This leads to a better-built home that stands the test of time, with fewer repairs and less maintenance required in the future. In a market where home owners are already waiting longer than expected for their homes to be completed, it’s worth asking: would you prefer a home that’s delivered quickly but riddled with problems, or one that takes a bit longer but is built to last?
The long-term benefits of prioritising quality over speed far outweigh the short-term inconvenience of a slower build. Home owners can enjoy peace of mind, knowing that their home was constructed with care and that any potential issues were caught and resolved during the build, rather than after they’ve moved in.
The Case for Quality Over Speed
While it’s easy to understand why builders and trades are pushing for faster turnover, the current state of the construction industry shows that this approach is unsustainable. The emphasis on speed has driven quality standards to rock bottom, leaving many home owners facing repair bills and headaches long after they’ve taken possession of their new homes.
The implementation of ITPs, while extending build times, offers a much-needed shift toward quality management. It creates a system of checks and balances that forces trades to slow down, take their time, and ensure that every aspect of the build meets the necessary standards. This might seem like a disadvantage in the short term, but it’s a crucial step toward improving the long-term durability and safety of residential construction.
A Question of Choice
At the end of the day, it comes down to a simple question: if you had to choose between fast and ready or slower but quality-assured, which would you prefer?
Given the rising number of defects in homes built under tight deadlines, it’s clear that speed is not always an advantage. The peace of mind that comes with knowing your home was built right—using proper quality management processes, verified by ITPs—is worth the wait.
Conclusion
The conversation around residential construction quality in Australia has been dominated by criticism, but it's time to shift from finger-pointing to providing real solutions. Inspection Test Plans (ITPs), paired with proper regulatory oversight, offer a practical and proven approach to ensuring higher standards and reducing defects in new homes. These processes are not new; they’ve been used successfully in commercial construction for years, and now it's time for residential builders to adopt them too.
By implementing mandatory ITPs, the construction industry can shift its focus from speed to quality, addressing the root causes of many of the defects and rework currently plaguing home owners. Yes, build times may increase, but this is a necessary step to ensure that homes are built right the first time, with fewer long-term maintenance issues and better overall performance.
In an industry where time, cost, and quality are often in conflict, the introduction of ITPs helps to realign priorities. Quality management processes, like those enforced through ITPs, will ensure that each stage of construction is thoroughly inspected and verified, preventing defects before they occur. The reintroduction of council inspectors could further strengthen this process, ensuring that builders and tradespeople are held accountable for their work.
Home owners deserve more than rushed, poorly constructed homes that come with years of costly repairs. By choosing quality over speed, the construction industry can restore trust, deliver better homes, and ultimately provide long-term value to Australian families.
The question remains:
Would you prefer a fast build that leaves you facing long-term maintenance headaches, or a slower, quality-assured build that gives you peace of mind for years to come?
The answer should be clear.
FAQs
- What is an Inspection Test Plan (ITP)?
An ITP is a structured document that outlines key inspection and testing points during the construction process. It ensures that each stage of the project is inspected and verified before moving forward, preventing defects and ensuring quality. - Why should ITPs be mandatory in residential construction?
ITPs help catch mistakes early in the construction process, reducing the chances of defects and ensuring that homes are built to a high standard. Making them mandatory would ensure consistent quality across all residential projects. - How do ITPs affect build times?
Implementing ITPs may increase build times slightly, but this ensures that each stage of construction is thoroughly inspected. The trade-off is fewer long-term issues and less maintenance, offering a better-quality home. - What is a 'hold point' in an ITP?
A hold point is a critical stage in the construction process where work must stop until an inspection is carried out and approved. This ensures that mistakes are caught and corrected before the project moves forward. - Why are council inspectors important for enforcing ITPs?
Council inspectors provide independent oversight, ensuring that builders and tradespeople follow the ITPs correctly. Their role is essential for holding contractors accountable and maintaining construction quality. - How do ITPs help reduce defects in construction?
ITPs provide a clear process for inspections, making sure that each phase of construction meets the required standards. By catching errors early, they prevent defects from becoming larger issues later in the project. - Will mandatory ITPs increase the cost of building a home?
While ITPs may add some upfront costs, they reduce the likelihood of defects, rework, and maintenance, saving money in the long run. It’s an investment in long-term quality and durability. - What happens if a builder or trades person skips an inspection point in the ITP?
If an inspection point is skipped, there is no guarantee that the work meets quality standards. This can lead to defects, safety concerns, and costly repairs. Proper enforcement of ITPs, through oversight like council inspectors, ensures these inspection points are not missed. - How can home owners ensure their builders are using ITPs?
Home owners can ask builders to include ITPs as part of the construction contract and request regular updates on inspections. This creates transparency and ensures the builder is held accountable for quality. - What are the long-term benefits of building with mandatory ITPs?
Homes built with ITPs undergo more rigorous inspections, resulting in fewer defects and less maintenance over time. This ensures a more durable, higher-quality home that provides long-term value.
Further Reading
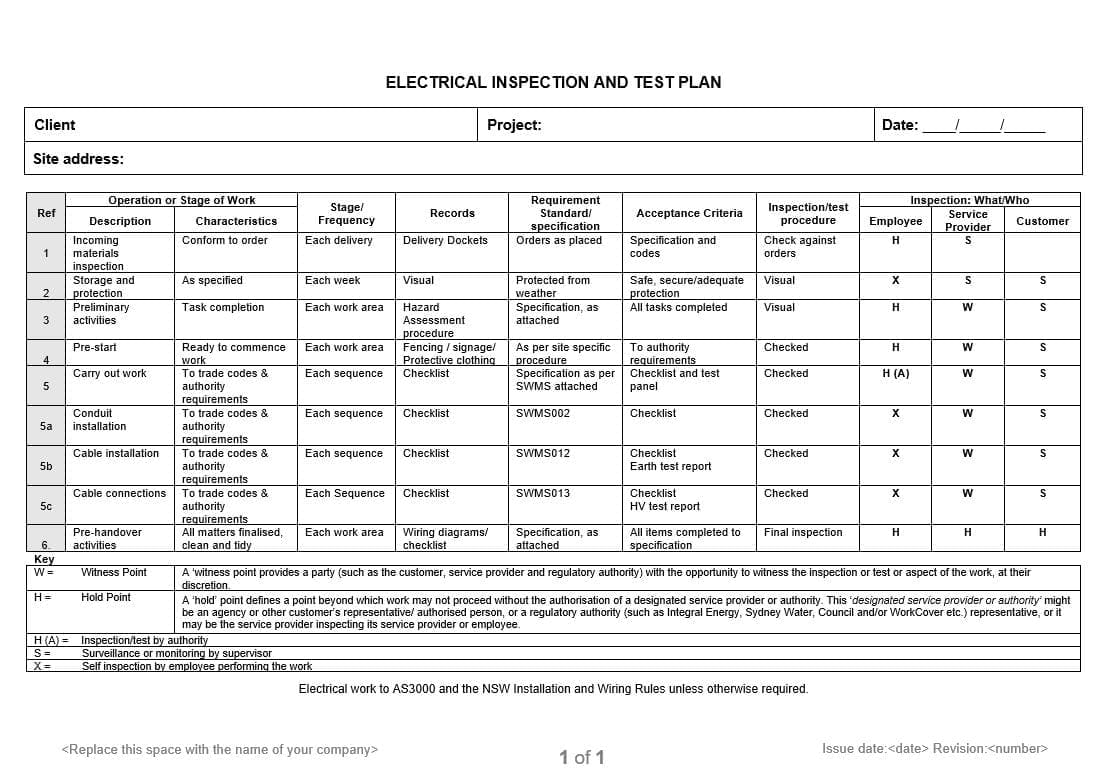
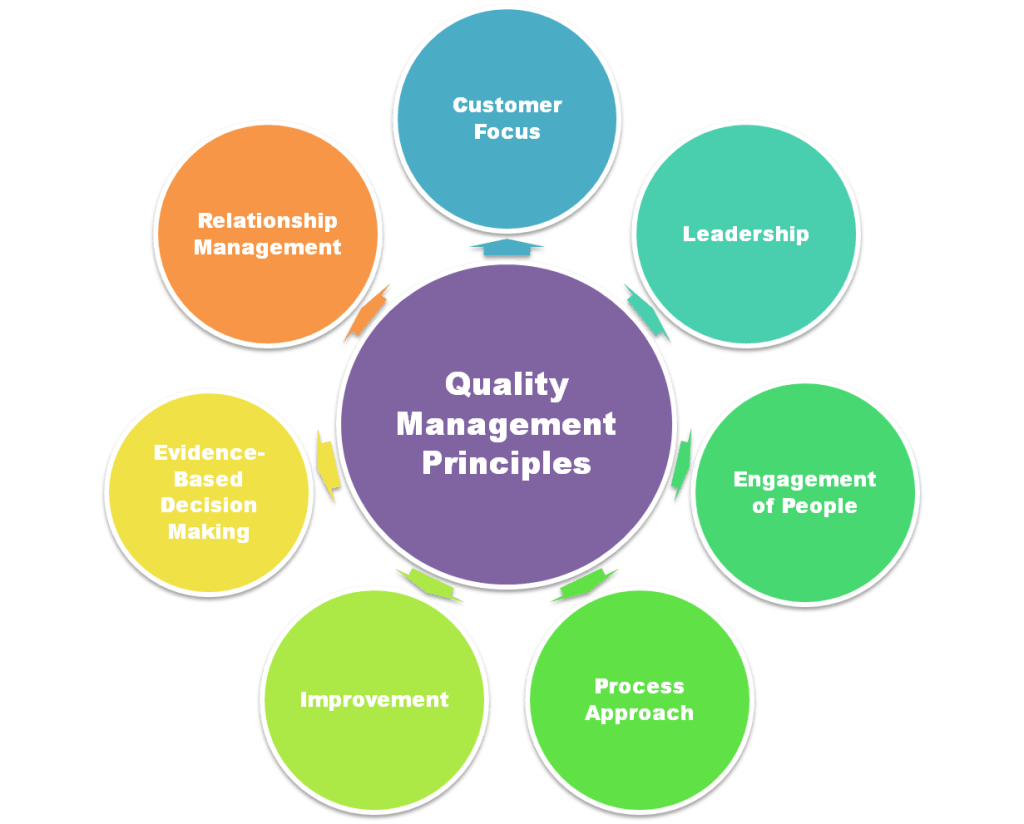