Introduction to Tilt-Up Construction
When you think about building a house or a commercial building, what construction method comes to mind? Brick by brick or wooden frame by wooden frame, perhaps? What if I told you there's a method that involves creating entire walls in one go, then lifting them into place like giant Lego blocks? This method is called tilt-up concrete construction, and it's speeding up how buildings are erected, offering a blend of speed, efficiency, and durability that traditional methods find hard to match.
At its core, tilt-up construction is straightforward. Large concrete panels are cast on the construction site itself, lying flat. Once they cure and reach sufficient strength, these panels are "tilted up" to form the exterior walls of a building. This technique has a storied history, gaining traction in the early 1900s, but it's in the modern era that its true potential has been realised, transforming the construction of warehouses, office buildings, and even residential homes.
This method isn't just about brute strength; it's about precision and planning. From the careful planning of the job site to the meticulous design of each panel, tilt-up construction marries the raw power of concrete with the finesse of modern engineering. As we peel back the layers of this fascinating construction method, you'll see why it's become a go-to choice for projects requiring quick turnaround times without sacrificing quality or durability.
Whether you're a home owner looking to understand the construction process of your future house or a professional in the building industry, this introduction to tilt-up construction will shed light on a method that's as innovative as it is ancient. Let's explore how turning walls on their head, quite literally, is making a significant impact on construction projects across the United States and beyond.
Understanding Tilt-Up Construction
Tilt-up projects might sound like a modern marvel, but its roots trace back to the early 1900s. It's a testament to how innovative thinking can transform concrete—a material as old as construction itself—into a versatile tool for building almost any type of structure. But what exactly is tilt-up construction, and how does it work?
The Basics of Tilt-Up Construction
In essence, tilt-up construction is a method where concrete walls are formed horizontally on the ground at the construction site. Once these walls, or panels, have hardened, they are lifted (or tilted up) into their vertical position with cranes. They are then braced into place, forming the exterior walls of the building.
The Role of the Tilt-Up Concrete Association
In the Australia, The Cement & Concrete Association (CCA) plays a role in promoting the use of tilt-up construction. It sets standards, provides education, and shares resources to ensure that tilt-up remains a safe, efficient, and reliable method for building construction.
How Tilt-Up Works: A Step-by-Step Overview
- Design and Planning: Every tilt-up project starts on the drawing board. Engineers and architects design the panels, considering factors like size, weight, and how they'll fit together.
- Site Preparation: A flat, clean area is prepared on the construction site for casting the panels. This might involve pouring a concrete slab to serve as the casting surface.
- Forming Panels: Wooden forms are built to shape the panels. Reinforcements and embeds for lifting and connecting the panels are placed inside the forms.
- Pouring Concrete: Ready-mix concrete is poured into the forms. The mix's quality is crucial for achieving the necessary strength and durability.
- Curing and Lifting: The concrete panels are allowed to cure. Once they've gained sufficient strength, a crane lifts each panel into its vertical position.
- Finishing Touches: The panels are braced securely, and the construction team proceeds with the building's roof and interior.
Tilt-up construction's simplicity belies its effectiveness. It allows for the quick erection of buildings, significantly reducing construction times compared to traditional methods. Furthermore, it offers unparalleled flexibility in design, enabling architects to push the boundaries of creativity.
As we continue to explore tilt-up construction, keep in mind this method's blend of ancient material and modern technique. It's a process that respects the past while boldly moving into the future, offering practical solutions to today's construction challenges.
Key Components of Tilt-Up Construction
Tilt-up construction relies on a series of well-coordinated steps and materials to transform concrete slabs into towering walls. Understanding these components not only highlights the method's efficiency but also its versatility and reliability.
Concrete Walls and Panels
At the heart of tilt-up construction are the tilt-up concrete panels themselves. These aren't just any concrete elements; they're engineered to specific tolerances, ensuring they fit together perfectly once erected. The use of ready-mix concrete ensures consistency in quality and strength, providing the durability that buildings require to withstand time and elements.
The Construction Process
- Casting Panels on Site: Unlike traditional methods that might require transporting large, prefabricated panels from a factory, tilt-up panels are cast right where they'll be used. This approach minimises transportation costs and damage risks.
- Using the Job Site as a Casting Area: By turning the construction site into a temporary factory, tilt-up construction reduces the need for large staging areas and minimises material handling, making it an efficient process.
- Lifting Panels into Place: Once cured, the panels are lifted by cranes and tilted up to form the building's walls. This pivotal moment requires precision and is a spectacle of engineering and teamwork.
Equipment Used
- Mobile Cranes: These are crucial for lifting the heavy panels into their vertical positions. The size and capacity of the crane depend on the size and weight of the panels being lifted.
- Bracing and Supports: Once upright, the panels need to be held in place securely. This is done using braces that are anchored to the ground (fixed to deadmen) and to the panels, ensuring stability until the roof and other structural elements are added to lock everything in place.
Tilt-up construction offers a unique blend of efficiency, cost-effectiveness, and design flexibility. The ability to create and lift large concrete panels on-site revolutionises how buildings are constructed, making it possible to erect walls and structures in less time than traditional methods. Moreover, the durability of concrete means these buildings are built to last, offering energy efficiency benefits and the flexibility to accommodate various architectural designs.
The simplicity of tilt-up construction belies its innovative approach to building. By leveraging the job site itself and utilising readily available materials and equipment, it offers a streamlined, cost-effective solution for both commercial and residential construction projects.
Tilt-Up vs. Other Construction Methods
Tilt-up construction offers a compelling alternative to traditional building techniques, combining speed, efficiency, and durability. But how does it stack up against other construction methods? Let's take a look.
Comparison with Other Methods
- Precast Concrete Panels: Precast panels are similar to tilt-up panels but are manufactured off-site and transported to the construction site. While precast concrete also offers speed and quality control, the transportation of large panels can be logistically challenging and costly.
- Masonry Construction: Known for its aesthetic appeal and durability, masonry construction involves laying individual bricks or stones. This method can be labour-intensive and time-consuming, making tilt-up construction a faster alternative for large structures.
- Steel Beam Construction: Steel beams provide strong, durable frames for buildings and allow for large, open interior spaces. However, steel construction can be expensive and requires specialised labour, whereas tilt-up construction can be more cost-effective for similar applications.
Common Applications of Tilt-Up Construction
Tilt-up construction is particularly well-suited for:
- Commercial Buildings: Warehouses, distribution centres, and retail stores benefit from the large, open spaces that tilt-up panels can create, offering a quick and cost-effective construction solution.
- Office Buildings: The architectural flexibility of tilt-up construction allows for customised designs that can accommodate the unique needs of office spaces.
- Industrial Buildings: The durability and ease of maintenance of tilt-up walls make them ideal for industrial settings.
- Educational and Religious Buildings: Schools and churches often choose tilt-up construction for its cost-effectiveness and the rapid construction timeline.
Ideal Conditions for Tilt-Up Construction
Tilt-up construction thrives under certain conditions:
- Sufficient Space: The method requires ample space for laying out and curing panels on-site.
- Economies of Scale: Larger buildings benefit more from tilt-up construction, as the cost and time savings become more pronounced with scale.
- Speed of Construction: Projects with tight timelines can leverage tilt-up construction to meet deadlines more effectively than traditional methods.
Pros and Cons
While tilt-up construction offers numerous benefits, including reduced labour costs and shorter construction times, it's not without its challenges. The need for large, accessible construction sites and the initial investment (construction cost) in specialised equipment (like cranes) can be drawbacks for smaller projects or those in densely urban areas.
Benefits of Tilt-Up Construction
Tilt-up construction isn't just another way to build—it's a strategic choice for efficiency, cost savings, and sustainability. Here are the standout benefits:
Speed of Construction
One of the most compelling advantages of tilt-up construction is its ability to speed up the entire building process. Unlike traditional methods that require brick-by-brick or beam-by-beam assembly, tilt-up panels can be prepared simultaneously and erected in a matter of days. This rapid assembly (tilt-up technique) reduces overall project timelines, allowing businesses to occupy buildings sooner and investors to see a return on their investment more quickly.
Cost-Effectiveness
The financial benefits of tilt-up construction are multi-faceted:
- Labor Savings: With fewer skilled labourers needed on-site for a shorter duration, labour costs can significantly decrease.
- Material Efficiency: Concrete, the primary material in tilt-up construction, is often more economical than steel or masonry. Moreover, the on-site casting of panels reduces transportation costs associated with precast or other materials.
- Reduced Financing Time: Faster construction means reduced construction financing costs, as projects are completed sooner.
Energy Efficiency and Sustainability
Tilt-up walls provide excellent thermal mass, reducing heating and cooling costs over the building's lifetime. Additionally, the ability to incorporate insulation during the casting process enhances this energy efficiency. The sustainability of tilt-up construction is furthered by its use of local materials and reduction in waste, making it a greener building option.
Design Flexibility
Tilt-up construction offers architects and designers vast creative freedom. The method allows for the creation of panels in various shapes, sizes, and finishes. This flexibility means that buildings can be customised to meet aesthetic goals or specific functional requirements, from sleek, modern offices to rustic, textured warehouses.
Durability and Maintenance
Concrete is known for its strength and longevity. Tilt-up buildings are resistant to fire, wind, and pests, translating into lower insurance costs and maintenance expenses over time. The durability of concrete also means these structures can withstand the test of time, maintaining their integrity and appearance with minimal upkeep.
Safety Considerations
Tilt-up construction is recognised for its excellent safety record. The controlled on-site casting of panels and reduced need for working at heights contribute to a safer construction environment. With proper planning and execution, tilt-up sites can maintain high safety standards, protecting workers and the project.
Coatings and Surface Preparations in Tilt-Up Construction
After the tilt-up panels are securely in place, the next critical steps involve applying coatings and preparing surfaces. These steps are not just about the final look but also about protecting the structure and ensuring longevity.
Common Applied Coatings
Tilt-up panels offer a canvas for a variety of finishes:
- Paints and Sealants: Provide weather protection and colour.
- Speciality Coatings: Such as anti-graffiti or reflective coatings, add functionality beyond aesthetics.
- Thin Brick and Stone Veneers: Offer the appearance of traditional masonry while maintaining the benefits of tilt-up construction.
Coating Adhesion Considerations
The success of coatings largely depends on their adhesion to the concrete surface, which can be influenced by several factors:
- Curing Compounds: While essential for proper concrete curing, these can create a barrier to coating adhesion (they are bond breakers). Proper removal of curing compounds is critical before applying coatings.
- Surface Texture and Porosity: Coatings adhere best to surfaces that are clean and slightly porous. This may require surface treatments such as sandblasting or acid etching to achieve the ideal texture.
Proper Surface Preparation
Ensuring that tilt-up panels are ready to receive coatings involves several key steps:
- Cleaning: The surface must be free of dust, dirt, and any residues that could impair coating adherence.
- Repairing Flaws: Any cracks or imperfections should be filled and smoothed out to prevent issues after coating application.
- Priming: A primer specifically designed for concrete surfaces can enhance the coating's adherence and durability.
The Importance of Expertise
Given the technical considerations and the potential impact on the building's longevity and appearance, it's essential to involve experts in coatings and surface preparations. The right professionals can advise on the best materials and techniques for a specific project, taking into account local weather conditions, the building's use, and desired aesthetic outcomes.
Choosing Tilt-Up for Your Next Project
As we've looked into the intricacies of tilt-up construction, it's clear that this method offers a compelling array of benefits for a wide range of construction projects. From commercial warehouses to office buildings, and increasingly in residential developments, tilt-up construction delivers on speed, cost efficiency, sustainability, and design flexibility.
Why Tilt-Up Stands Out
- Speed of Construction: Reducing overall project timelines allows businesses to start operations sooner, offering a quick return on investment.
- Cost-Effectiveness: Lower labour costs, reduced material waste, and decreased financing periods make tilt-up construction a financially savvy choice.
- Sustainability and Energy Efficiency: Utilising local materials and minimising waste contribute to environmental sustainability, while the thermal properties of concrete improve a building's energy efficiency.
- Design Versatility: The architectural flexibility of tilt-up construction means that buildings can be customised to meet specific aesthetic and functional requirements, making it a versatile choice for any project.
- Durability and Low Maintenance: Concrete's inherent strength ensures that tilt-up buildings are durable and resistant to natural elements, leading to lower long-term maintenance costs.
Making the Decision
Choosing tilt-up construction for your next project involves careful consideration of your specific needs, including the size and scope of the project, timeline, budget, and aesthetic goals. Working with experienced contractors and designers familiar with tilt-up methods can help ensure that your project leverages all the advantages this construction method has to offer.
Frequently Asked Questions
Q: Is tilt-up construction only suitable for commercial projects? A: While tilt-up is popular for commercial and industrial buildings due to its efficiency and cost-effectiveness, it's also becoming increasingly used in residential construction, especially for developments where speed and durability are priorities.
Q: How does weather affect tilt-up construction projects? A: Weather conditions can impact the curing time of concrete and the feasibility of lifting panels. However, proper planning and scheduling can mitigate these effects, making tilt-up construction adaptable to various climates.
Q: What are the safety considerations with tilt-up construction? A: Safety is paramount in tilt-up construction, particularly during the lifting and placement of panels. Strict adherence to safety protocols and the use of experienced crews can ensure a safe construction site.
Q: How do tilt-up panels contribute to a building's energy efficiency? A: The thermal mass of concrete panels helps regulate indoor temperatures, reducing the need for heating and cooling. Additionally, insulation can be incorporated into the panels to enhance energy efficiency further.
Q: What is the average cost per square foot for a tilt-up construction project? A: Costs can vary widely depending on the project's location, size, and complexity. However, tilt-up construction is generally competitive with or less expensive than traditional construction methods, especially when considering long-term savings from energy efficiency and low maintenance.
Q: Can tilt-up construction be used for buildings in colder climates? A: Yes, tilt-up construction can be adapted for use in colder climates. Special considerations, such as insulation techniques and winter construction methods, can address the challenges presented by cold weather.
Q: What are the advantages of precast concrete construction compared to tilt-up? A: Precast concrete allows for controlled factory conditions and can be beneficial for projects where site constraints make on-site casting impractical. However, it generally involves higher transportation and lifting costs compared to tilt-up panels cast on site.
Further Reading on the topic of Concrete
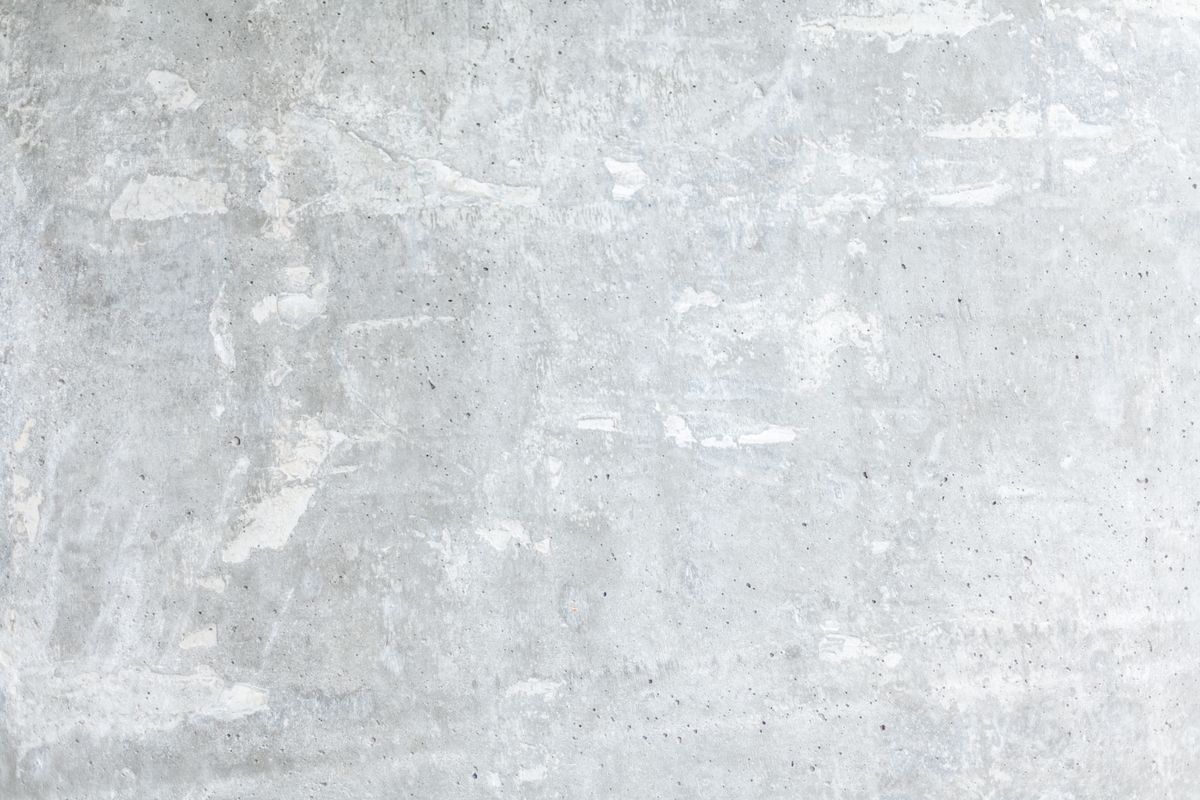
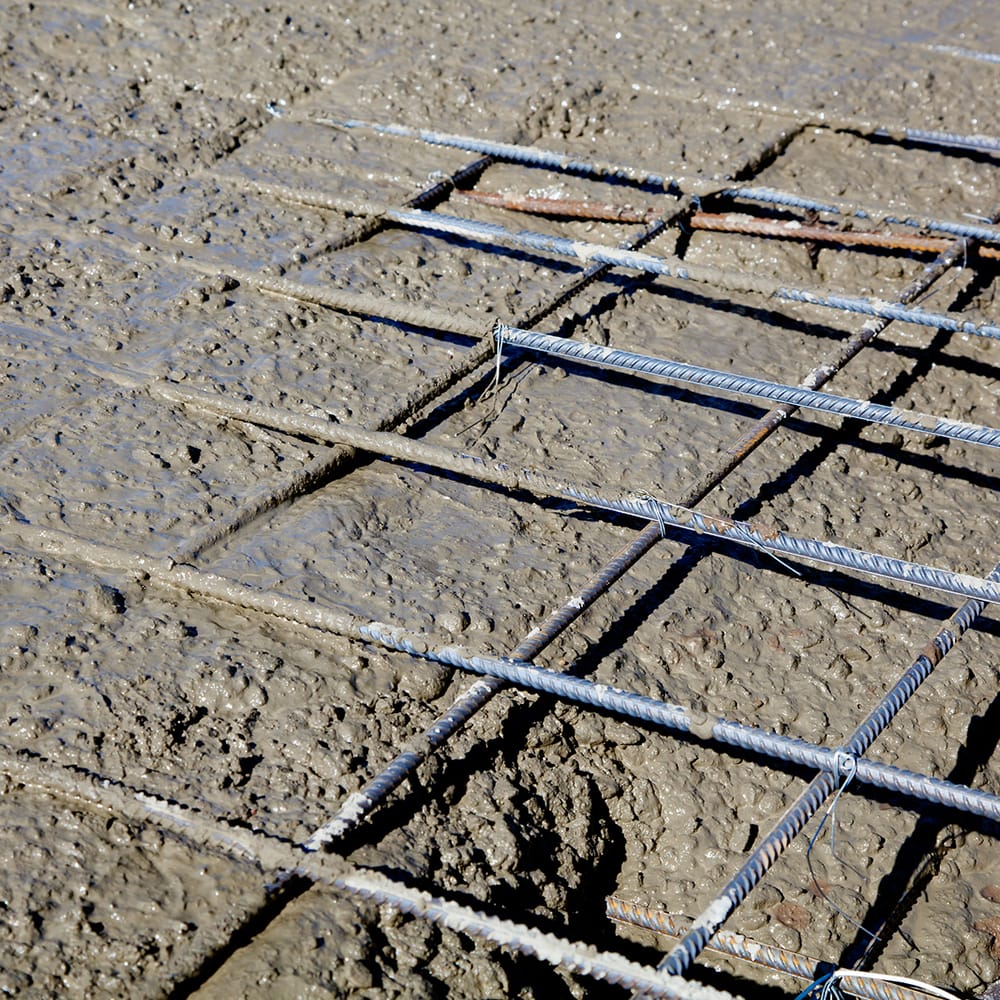