A Guide to Fasteners in Construction: Types & Uses
Fasteners are integral components in construction, unseen yet vital for the integrity and durability of a structure. This guide provides a thorough exploration of fasteners used in construction, detailing different types and their specific uses in various applications.
Introduction
Starting out on any construction project, whether a small backyard deck or a brand new home build, introduces you to the world of construction fasteners. These hardware devices play an essential role in ensuring the structural integrity of your build.
From the stainless steel screws that hold your kitchen cabinets in place to the carbon steel bolts anchoring the beams of your roof, selecting the right fastener is a critical decision in any building project.
Fasteners come in various types, sizes, and materials, each designed for different components and specific applications. Understanding the wide range of fasteners available can help you make informed decisions, ensuring your project's longevity and safety. This guide will explore the crucial role of fasteners in the construction industry, highlighting the importance of choosing the correct material and type for your specific needs.
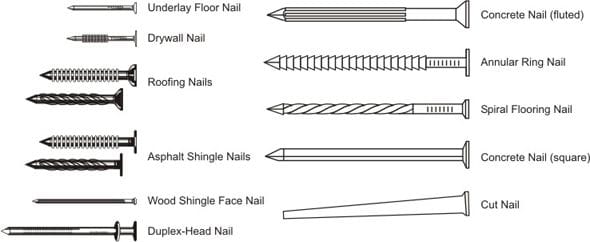
Nails: The Backbone of Construction Projects
In any toolkit for building projects, nails stand out for their simplicity and versatility. Common types of fasteners like common nails, box nails, and roofing nails are chosen based on the specific use and the pieces of wood or other materials being joined. Nails vary in various sizes and shapes, from the sharp point designed for piercing materials with minimal splitting to the flat head that provides a larger surface area to hold materials in place.
Nails are often used in a non-permanent way, allowing for easy dismantling or adjustments as needed. This feature is particularly useful in temporary fasteners or when precision and the ability to remove the fastener without significant damage are important. Despite their simplicity, nails play a crucial role in building applications, securing everything from framing structures to siding and roofing. The use of a nail gun can significantly speed up projects, driving nails evenly and quickly for a more efficient construction process.
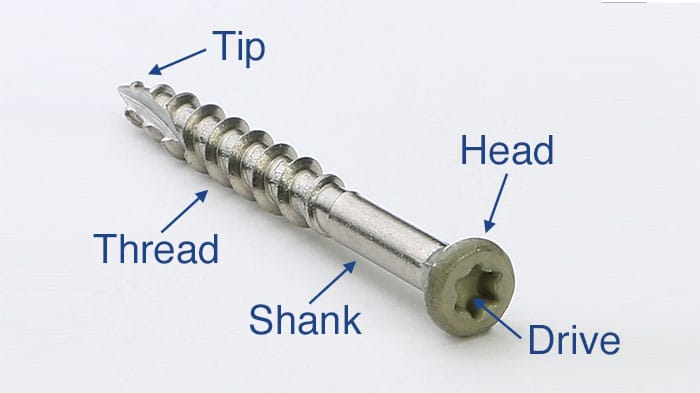
Screws: Securing with Precision
Screws take the principle of the nail and add threads, resulting in a fastener capable of providing a more secure connection through its ability to bite into the material. Wood screws, drywall screws, construction screws, and sheet metal screws are among the most commonly used types, each designed for different materials and applications. For instance, wood screws are specifically designed for joining pieces of wood, offering a sharp point for easy insertion and coarse threads to grip the wood securely.
Screws are also categorized by their head types, such as flat head or hex head, which dictate the type of tool needed for installation. Stainless steel is a popular choice for screws due to its corrosion resistance, making it ideal for outdoor use or in environments with high moisture levels. The specific applications of screws are vast, ranging from building decks with deck screws to assembling furniture with machine screws. Their versatility and strength make them one of the most versatile types of fasteners in the construction industry.
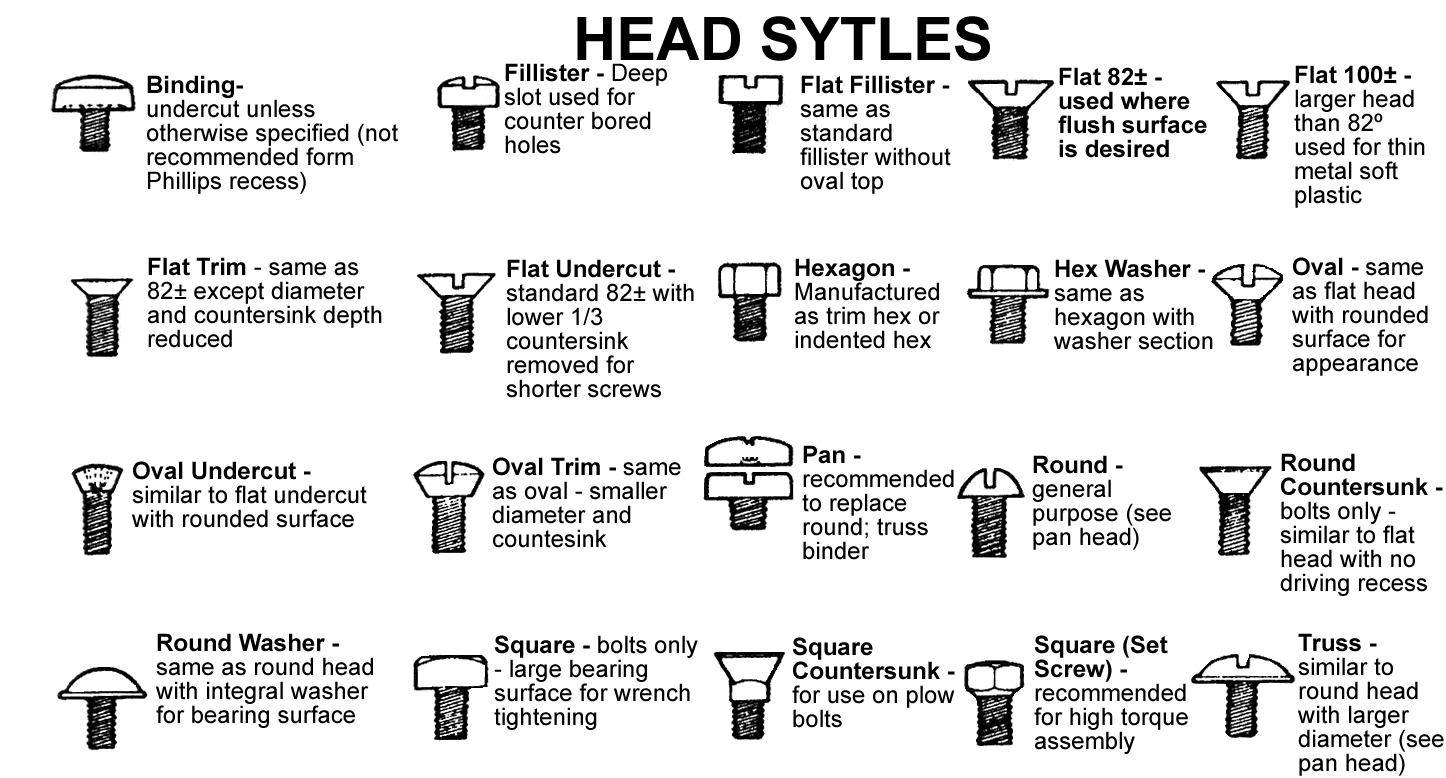
Bolts and Nuts: For Heavy-Duty Applications
Bolts, paired with nuts, form a duo that's indispensable for heavy-duty applications requiring a strong, reliable connection. Carriage bolts, hex bolts, and flange bolts are used in various construction projects, from steel construction to wooden frames. The selection of bolts is based on the load requirements, with carbon steel and silicon bronze being common materials due to their strength and durability.
Installation of bolts typically requires pre-drilled holes, ensuring a precise fit and the structural integrity of the connected materials. Bolts are especially crucial in construction projects that involve different types of materials or require a secure connection that can withstand high stress or weight. The use of a hex nut, in conjunction with the correct bolt, ensures a tight and secure fastening, crucial for maintaining the safety and longevity of a structure.
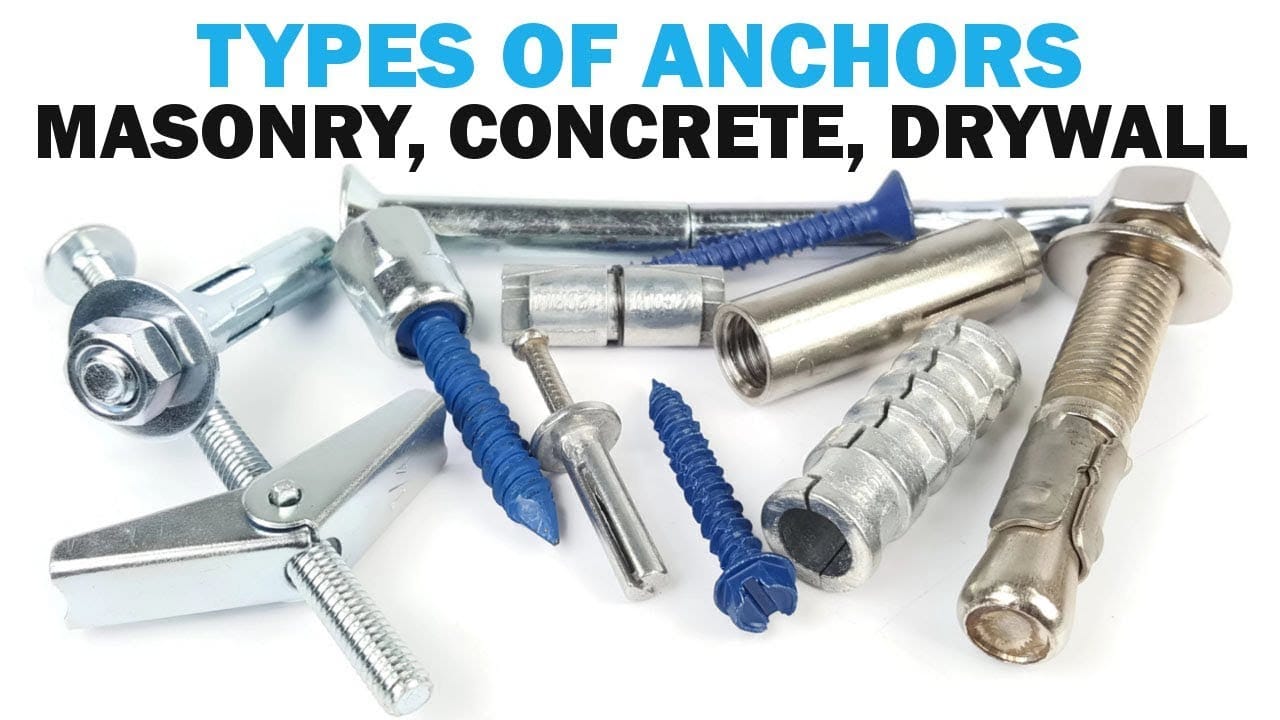
Anchors: Solid Foundations for Various Materials
When attaching objects to surfaces that might not support nails or screws effectively, anchors provide a solid foundation. Whether it's for hanging heavy shelving on drywall or securing a railing to concrete, anchors are designed to expand within the material, offering a strong hold in various materials. The specific types of anchors, such as masonry screws for concrete or drywall screws for gypsum boards, are selected based on the material's characteristics and the load it needs to bear.
Anchors are available in various shapes and sizes, ensuring there's a type suited for nearly any application. Their design allows for a secure connection in materials that are otherwise difficult to penetrate or that may crumble under the pressure of traditional fasteners. This makes anchors an essential part of the fastener family, particularly in modern construction where various materials are used.
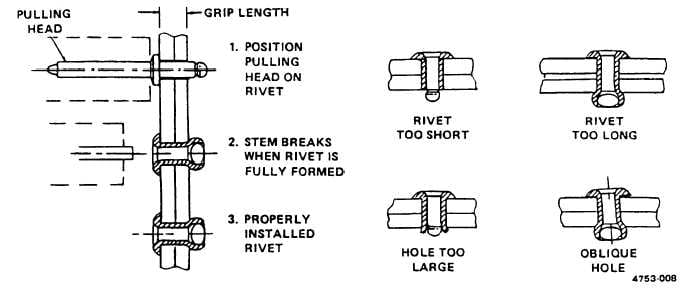
Advanced Fasteners: Rivets, Staples, and More
Moving beyond nails, screws, and bolts, the construction industry also relies on advanced fasteners like rivets and staples for specific applications. Rivets, including solid rivets, semi-tubular rivets, and blind rivets, offer a permanent joint, ideal for situations where a non-removable fastening solution is needed. Staples, on the other hand, provide a quick and efficient way to secure materials together, often used in roofing or upholstery.
These advanced fasteners are chosen for their specific strengths, such as the ability to distribute load across a wider area or to fasten materials without access to both sides. Their application in construction varies, from securing insulation and roofing materials with staples to assembling metal structures with rivets. Each type of fastener has its own set of tools for installation, from staple guns to rivet guns, highlighting the diverse toolkit required in the construction industry.
Nails vs. Screws: Understanding the Benefits and Strengths
One of the key decisions involves before starting construction involves choosing between nails and screws. This choice significantly impacts the project's efficiency, cost, and durability. While screws are often praised for their holding power and ease of removal, there are specific scenarios where nails are not only beneficial but preferred due to their unique properties and advantages.
Benefits of Using Nails
- Speed of Installation: Nails can be installed much quicker than screws, especially when using a nail gun. This makes them ideal for projects where speed is crucial, such as framing or sheathing.
- Cost-Effectiveness: Generally, nails are less expensive than screws, making them a cost-effective choice for large projects where a high volume of fasteners is required.
- Tensile Strength: Nails have a higher tensile strength compared to screws. This means they are better at withstanding forces that try to pull them straight out. This characteristic is particularly important in framing and structural applications where the integrity of the construction must resist dynamic loads, such as wind or seismic activities.
- Shear Strength: While screws have excellent tensile strength due to their threads, nails are superior in shear strength. Shear strength is the ability of a fastener to resist forces that try to cut it in half or slide the joined materials past each other. In many structural applications, such as framing, the shear strength of nails makes them the preferable choice to ensure the structural integrity of the building.
When to Use Nails Over Screws
- Framing and Structural Work: Due to their shear strength and the ability to absorb sudden loads without snapping, nails are predominantly used in framing and other structural work in residential and commercial construction.
- Decking: For the base structure of decks, nails are often preferred for their ability to withstand the forces that may cause the deck to shift or move.
- Roofing: Nails are typically used for attaching shingles. Their ability to be rapidly installed and their high shear strength make them ideal for withstanding high winds and other harsh weather conditions.
- Siding and Sheathing: Nails are also preferred in siding and sheathing for their quick installation and the fact that they allow materials a bit of movement due to temperature changes without compromising the structural integrity.
Tensile vs. Shear Strength: A Closer Look
The discussion about tensile and shear strength is central to understanding why nails might be chosen over screws for specific applications. Screws, with their threaded design, provide excellent tensile strength, making them ideal for applications where the primary concern is the force pulling directly away from the fastened material. However, in many construction scenarios, the forces applied to the structure are complex, involving not just tensile but also shear stress.
Nails, with their smooth shank, can bend slightly under load, distributing the stress along the length of the nail, which often makes them more resilient to shear forces than screws. This bending flexibility under load helps prevent the sudden failure of the fastened joint, a crucial factor in the overall safety and durability of structures.
In summary, while screws are indispensable for their holding power and versatility, nails hold a distinct advantage in applications requiring rapid installation, cost efficiency, superior shear strength, and resilience under dynamic loads. Understanding the strengths and applications of each type of fastener ensures that construction projects are not only built efficiently but are also safe and durable.
Fastener Corrosion Resistance: Levels and Considerations
Corrosion resistance is an essential attribute for fasteners used in construction, especially in environments exposed to moisture, chemicals, or saline conditions. The longevity and reliability of a fastener—and by extension, the entire construction project—can be significantly affected by its ability to resist corrosion. Furthermore, the interaction between dissimilar metals can lead to accelerated corrosion, making the selection process even more critical.
Levels of Corrosion Resistance
Fastener materials can be ranked based on their corrosion resistance, from least resistant to most resistant:
- Low Corrosion Resistance:
- Carbon Steel: The most basic fastener material, offering minimal corrosion resistance. Carbon steel fasteners are usually coated with zinc (galvanized) to improve their resistance to rust. Suitable for indoor applications where exposure to moisture is minimal.
- Moderate Corrosion Resistance:
- Galvanized Steel: Carbon steel coated with a layer of zinc for added protection against corrosion. While galvanization extends the fastener's lifespan, these are not recommended for highly corrosive environments like coastal areas.
- Coated Fasteners (Phosphate, Black Oxide): These have a protective coating that offers moderate resistance to corrosion and is mainly used for aesthetic purposes or minimal exposure environments.
- High Corrosion Resistance:
- Stainless Steel: Known for its high corrosion resistance, stainless steel fasteners are ideal for outdoor applications and environments with moderate to high exposure to corrosive elements. They are a popular choice for decking, siding, and marine applications.
- Silicon Bronze and Brass: Offer good corrosion resistance in marine environments. They are less strong than stainless steel but are suitable for decorative applications or in situations where the fastener is in direct contact with water.
- Very High Corrosion Resistance:
- Titanium and Special Alloys (Inconel, Monel): These materials offer the highest level of corrosion resistance and are used in highly corrosive environments, such as chemical plants or areas with constant exposure to saltwater. Their use is typically reserved for specialized applications due to their higher cost.
The Impact of Dissimilar Metals
When selecting fasteners, it's crucial to consider the metals involved in the construction project. The use of dissimilar metals can lead to galvanic corrosion, a process where one metal corrodes preferentially to another when both metals are in electrical contact and exposed to an electrolyte, such as water. For example, using carbon steel screws in aluminum framing can accelerate corrosion due to their dissimilarity.
To prevent galvanic corrosion, it's important to:
- Use fasteners made of materials compatible with the materials they will contact.
- Employ barrier coatings or isolating washers to separate dissimilar metals physically.
- Choose fasteners with a corrosion resistance level appropriate for the environment and in line with the most corrosion-resistant metal in the assembly.
Conclusion
Choosing the right fasteners isn't just important for construction; it affects everything about a structure's strength, how long it lasts, and how safe it is. Our exploration of fasteners, from basic nails and screws to rust-resistant metals and preventing corrosion, shows how vital these small parts are.
Understanding the different roles, strengths, and best uses of various fasteners helps make smart decisions for construction projects. It ensures they're durable and can handle environmental challenges. Knowing about corrosion resistance and the effects of using different metals adds another layer to this process, stressing the importance of choosing fasteners that match both the project's needs and its surroundings.
So before you start your next construction project rest assured your now equipped with the knowledge to navigate the different types of construction fasteners, considering not just the immediate structural needs but also the long-term environmental interactions.
Selecting high-quality fasteners with the appropriate corrosion resistance for the specific environment ensures that projects stand the test of time, maintaining their strength and aesthetic appeal even in the face of corrosive elements.
As we conclude, it’s clear that the role of fasteners in construction goes beyond mere utility. They are important in ensuring that every piece of wood, every panel, and every beam comes together into a structure that is not only structurally sound but also durable against the elements. Whether it’s choosing a stainless steel screw for its corrosion resistance or a carbon steel bolt for its sheer strength, the right fastener makes all the difference. Armed with this understanding, builders, contractors, and DIY enthusiasts can now select fasteners that will hold their projects together, ensuring safety, durability, and integrity for years to come. The right fixing for the intended application!
FAQs
- What are the most versatile types of fasteners for residential construction?
- Screws, particularly wood screws and construction screws, are among the most versatile due to their strength, ease of use, and suitability for a wide range of materials and applications.
- How do I choose the right fastener for outdoor use?
- Consider materials like stainless steel or silicon bronze for their corrosion resistance and durability in varying environmental conditions.
- What's the difference between wood screws and drywall screws?
- Wood screws are designed specifically for joining wood pieces and typically have a sharp point and coarse threads, while drywall screws have a fine thread and are used for attaching drywall to studs.
- Can the same type of bolt be used for different materials?
- It depends on the application and load requirements; however, selecting a bolt material and type appropriate for both materials is crucial for a secure connection.
- Why is stainless steel a popular choice for fasteners?
- Its corrosion resistance, durability, and strength make stainless steel ideal for a wide range of applications, including those exposed to harsh environmental conditions.
- How do environmental conditions affect the choice of fasteners?
- Conditions such as moisture, temperature changes, and chemical exposure can dictate the need for fasteners with specific properties like corrosion resistance or thermal stability.
- What are non-permanent fasteners, and when should they be used?
- Non-permanent fasteners, like certain types of screws and nails, allow for easier disassembly or adjustments and are suitable for applications where changes or maintenance are anticipated.
- How important is the material of the fastener in construction projects?
- The material can significantly impact the fastener's performance, durability, and suitability for specific applications, making it a critical consideration in the selection process.
- Are there specific fasteners for heavy-duty applications?
- Yes, there are fasteners specifically designed for heavy-duty applications in the construction industry. Bolts, particularly carriage bolts, hex bolts, and structural bolts, are commonly used for their strength and ability to securely join heavy components. These bolts are often made from high-strength materials like carbon steel or alloy steel to withstand high loads and stress. Additionally, anchors designed for concrete and masonry, such as sleeve anchors and wedge anchors, provide reliable solutions for attaching heavy items to these materials.
- What are the key differences between using nails and screws in construction projects?
- The main differences lie in their method of load bearing and installation. Nails offer superior shear strength and faster installation, making them ideal for structural framing and sheathing. Screws provide excellent tensile strength and are preferred for precise applications where materials need to be securely fastened with the option for easy removal, such as cabinetry and decking.
- When should I consider corrosion resistance in selecting fasteners for my project?
- Corrosion resistance should be a key consideration for any project exposed to moisture, chemicals, saline environments, or varying weather conditions. This includes outdoor structures, projects in coastal areas, and any construction involving metal that could be prone to rust.
- What materials offer the highest level of corrosion resistance for fasteners?
- Titanium and special alloys like Inconel and Monel provide the highest corrosion resistance, making them suitable for highly corrosive environments such as chemical exposure or saltwater contact. Stainless steel also offers high corrosion resistance for more general outdoor applications.
- How do I prevent galvanic corrosion when using fasteners with dissimilar metals?
- To prevent galvanic corrosion, choose fasteners made from a compatible material with the metals being fastened, use barrier coatings or isolating washers to physically separate the metals, or select fasteners with a protective coating that prevents electrolytic action.
- Why might I choose nails over screws for a project?
- Nails might be chosen over screws for their quick installation, cost-effectiveness, superior shear strength, and the ability to absorb sudden loads without failure, making them especially useful in framing and structural applications.
- What is the least corrosion-resistant material for fasteners, and where might it be appropriately used?
- Uncoated carbon steel offers the least corrosion resistance and is typically used in interior applications where exposure to moisture or corrosive elements is minimal. For added protection, carbon steel can be galvanized or coated.
- Can stainless steel fasteners be used with all types of materials?
- While stainless steel fasteners are versatile and corrosion-resistant, careful consideration is needed when using them with certain materials, such as aluminum, to avoid galvanic corrosion. Barrier methods or specific stainless steel grades designed to minimize corrosion should be used in such cases.
- What factors should I consider when selecting fasteners for heavy-duty applications?
- Consider the load requirements, environmental exposure, and potential for corrosive interaction. Materials like high-strength steel or corrosion-resistant alloys may be required, along with fasteners that provide both tensile and shear strength.
- Are there specific coatings that can improve a fastener's corrosion resistance?
- Yes, coatings such as zinc (galvanization), phosphate, and black oxide can improve a fastener's resistance to corrosion. The choice of coating depends on the application's environmental conditions and the required aesthetics.
- How can I ensure the fasteners I choose are appropriate for the environmental conditions of my project?
- Evaluate the potential exposure to corrosive elements and select fasteners with suitable materials and coatings. Consider stainless steel, silicon bronze, or specially coated fasteners for high corrosion resistance in outdoor or harsh environments.
Further Reading
Don't get screwed! Why Class 4 Corrosion Resistance Won’t Cut It READ HERE
Metal Coatings 101: A Quick Primer for Home Construction READ HERE
A buyers guide to external cladding READ HERE
An Introduction Into the Different types of Steel Surface Preparation Methods READ HERE
Timber or Steel? Choosing a Lightweight Frame for Your Home READ HERE
Discussion